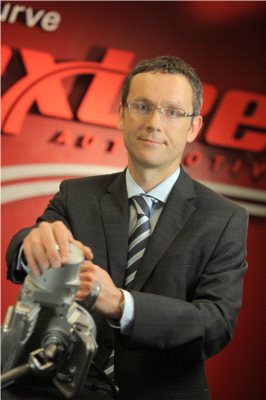
Ogromne wyzwanie
Z Rafałem Wyszomirskim, prezesem zarządu Nexteer Automotive Poland i dyrektorem tyskiej fabryki rozmawia Przemysław OzgaW 2009 roku w tyskim zakładzie wdrożono RFID. Jakie funkcje spełnia system radiowej identyfikacji w fabryce w Tychach?
System RFID pozwala na automatyczne...
W 2009 roku w tyskim zakładzie wdrożono RFID. Jakie funkcje spełnia system radiowej identyfikacji w fabryce w Tychach?
System RFID pozwala na automatyczne śledzenie każdego elementu w procesie montażu. Podczas każdej kolejnej operacji maszyna weryfikuje, czy dana sztuka wyrobu poprawnie przeszła poprzednie operacje. Element, który nie przeszedł prawidłowo poprzedniego etapu montażu, jest zatem odrzucany przez kolejną maszynę podającą operatorowi stosowny komunikat. Dodatkowo system RFID pomaga zbierać ustalone parametry procesowe wszystkich wyrobów z danej linii, które są zapisywane w bazie danych. Dzięki temu w dowolnej chwili możemy odtworzyć historię każdego systemu EPS oraz przeprowadzać badania statystyczne o zadanym profilu.
W zeszłym roku uruchomiliście państwo Centra Analiz? Jakie są kompetencje pracujących w nich zespołów? Jak wygląda ich współpraca z innym działami w zakładzie w Tychach?
Centra Analiz pozwalają diagnozować problemy w czasie rzeczywistym w miarę ich pojawiania się na liniach produkcyjnych. Szybka diagnoza umożliwia nam oszacowanie ryzyka i natychmiastowe podjęcie stosownych działań korygujących.
W ostatnim roku uruchomiliście dwie dodatkowe linie produkcyjne…
W kwietniu tego roku uruchomiliśmy produkcję kolumn kierowniczych wspomaganych elektrycznie do najnowszego modelu Lancii Ypsilon. W tym celu zainstalowano i uruchomiono dwie dodatkowe linie produkcyjne oraz kilka nowych maszyn na liniach już istniejących. Konstrukcja kolumny bazuje na tej montowanej w modelach Fiata 500 i Fordzie KA. Zmiany dotyczą układu regulacji położenia kolumny i układu kontrolera. Całość produkcji wysyłana jest do zakładu Fiat Auto Poland w Tychach, a docelowy plan to około 650 systemów dziennie. W poprzednich latach natomiast uruchomione zostały linie dla modeli Fiata 500 oraz najnowszych modeli Citroena: C3 i DS3.
Firma stawia sobie za cel zmniejszanie kosztów i czasu wytwarzania, przy jednoczesnym zachowaniu najwyższej jakości wytwarzanych systemów. W jaki sposób go osiągniecie?
Osiąganie szeroko pojętych celów kosztowych nie może być skuteczne bez utrzymania najwyższego poziomu jakości. De facto ciągła poprawa wskaźników First Time Quality (FTQ) prowadzi do zmniejszania kosztów złomu oraz zwrotów gwarancyjnych przy jednoczesnym zwiększeniu produktywności wskutek lepszego wykorzystania dostępności maszyn. Kluczem do sukcesu jest jasne zdefiniowanie obszarów oraz celów jakościowych. Nad realizacją stosownych projektów pracuje specjalnie powołana grupa Innovation and Continuous Improvement Methodologies (ICIM), która składa się z inżynierów ekspertów stosujących zaawansowane metody analityczno-statystyczne w ramach 6 Sigma oraz techniki FastX.
Czy firma prowadzi specjalne szkolenia dla swoich pracowników uświadamiające im związek pomiędzy jakością montażu układów kierowniczych a komfortem i bezpieczeństwem prowadzenia gotowych samochodów?
Owszem, w Nexteer prowadzimy takie szkolenia począwszy od szkoleń wstępnych, poprzez specjalny proces certyfikacji pracowników produkcyjnych, a skończywszy na kampaniach jakościowych mających na celu podwyższenie wiedzy na temat wpływu jakości na komfort i bezpieczeństwo. Dla przykładu, nasze centrum informacyjne wyposażone jest w system symulacyjny (Wheel to Wheel), który uświadamia naszym pracownikom wpływ jakości systemów sterowniczych na kontrolę pojazdów. Prowadzimy również jazdy próbne w samochodach pilotażowych wyposażonych w systemy symulujące potencjalne wady wspomagania, co pozwala doświadczyć ewentualnych skutków niskiej jakości. Metody te zdecydowanie podnoszą świadomość oraz czujność naszych pracowników pod kątem jakości produktów Nexteer.
Czy Nexteer wdraża zasady Lean Management, szczupłego zarządzania?
W naszym zakładzie wdrażamy takie elementy kultury Lean, jak standaryzacja pracy, minimalizacja buforów międzyoperacyjnych, kontrole wizualne, ciągłe doskonalenie pracowników czy tak zwane 5S, czyli pochodzącą z Japonii zasadę porządkowania miejsc pracy. Przy projektowaniu procesów produkcyjnych staramy się zapewnić jak najlepszą ergonomię, instalując maszyny w sposób optymalny dla obsługujących je pracowników. W naszym zakładzie bardzo dobrze funkcjonuje również tak zwany Program Sugestii, który zachęca do składania wniosków skierowanych na poprawę procesu, podnoszenie jakości oraz bezpieczeństwa pracy. Co miesiąc nagradzamy na forum wewnątrzzakładowym autorów najwyżej ocenionych sugestii.
W jaki sposób dostarczane są komponenty na linie montażowe (produkcyjne) w fabryce w Tychach? Czy nowe linie produkcyjne wymagały zmiany koncepcji przepływu materiałów potrzebnych do produkcji?
Branża motoryzacyjna szczyci się najlepszymi i najbardziej zaawansowanymi rozwiązaniami logistycznymi. Takie techniki są również stosowane i codziennie doskonalone w tyskim zakładzie Nexteer. Komponenty są dostarczane dokładnie wtedy, kiedy są potrzebne do miejsc ściśle przyporządkowanych operatorowi montującemu wyrób w sposób najbardziej dla niego ergonomiczny. Samo pojęcie magazynu od dawna przestało mieć autonomiczne znaczenie i traktowane jest jako integralna część procesu przepływu wartości. Komponenty, po uprzedniej weryfikacji jakościowej oraz nadaniu adnotacji identyfikacyjnej, dostarczane są w ściśle określonych ilościach na specjalnie w tym celu skonstruowanych urządzeniach transportowych. Zapotrzebowaniem zarządza system Kanban, który, tak jak i inne elementy składowe systemu dostarczania materiałów na linie montażowe, jest optymalizowany w przypadku jakichkolwiek zmian w procesie produkcyjnym.
W trakcie roku zakłady Nexteer w Polsce produkują około trzech milionów układów i kolumn kierowniczych. Jak sobie radzicie z dystrybucją tak dużego wolumenu produktów? Czy współpracujecie z którymś z operatorów logistycznych? Posiadacie własne magazyny dystrybucji?
W roku 2010 wyprodukowaliśmy około czterech milionów wyrobów gotowych w zakładach w Tychach i Gliwicach. Zarządzanie logistyczne w firmie z tak dużym obrotem materiałowym jest ogromnym wyzwaniem. Każdego dnia jesteśmy w kontakcie z naszymi klientami i dostawcami rozmieszczonymi na terenie całej Europy, jak i w krajach zamorskich. Dlatego też współpracujemy od lat ze ściśle określonymi firmami spedycyjnymi, które wykorzystując swoje doświadczenie, pozwalają nam na realizację zamierzonych, wysoko postawionych celów. Z racji dużych wolumenów produkcyjnych proces magazynowania realizowany jest obecnie u naszego poddostawcy logistycznego, lecz pracujemy nad ciągłą optymalizacją systemu celem maksymalnego dostosowywania procesu dystrybucji do naszych specyficznych rosnących wymagań.
W najbliższym czasie Nexteer Automotive zainwestuje ponad 200 milionów złotych w zakłady w Tychach i Gliwicach. Finansowy zastrzyk ma wesprzeć uruchomienie trzech nowych projektów. Proszę powiedzieć coś więcej na ich temat. O ile wzrośnie szacowana wydajność?
Nexteer Automotve Polska planuje inwestycje kapitałowe na poziomie 200 milionów złotych w okresie od 2012 do 2014 roku. Będą one związane z pięcioma uruchomieniami w zakładzie tyskim oraz gliwickim. Część nowych kontraktów zastąpi wygasające projekty. Planujemy utrzymać produkcję na obecnym poziomie z możliwą lekką tendencją wzrostową, jednocześnie zastępując około 40 procent bieżących wolumenów nowymi kontraktami opartymi o najnowsze technologie w ramach systemów Single Pinion EPS (SPEPS) oraz Column EPS (CEPS). Projekty te pozwolą nam rozszerzyć kompetencje w produkcji elektrycznych systemów sterowniczych na zakład w Gliwicach, który obecnie specjalizuje się w systemach hydraulicznych. Wyżej wspomniane projekty odnoszą się do siedmiu konkretnych modeli w ramach pięciu marek samochodowych sprzedawanych przede wszystkim na rynku europejskim. Więcej szczegółów na temat nowych uruchomień będziemy przekazywać po uzyskaniu stosowanych akceptacji ze strony naszych klientów.
Według analiz inżynierów Nexteer Automotive, do 2020 roku co drugi samochód na świecie będzie wyposażony w elektryczny układ kierowniczy. Czy tak duży popyt na układy EPS w przyszłości będzie wymagał od was uruchomienia dodatkowych zakładów produkcyjnych?
Nexteer rozważa lokalizację oraz zdolności produkcyjne zakładów przy okazji zdobycia każdego nowego projektu. Jesteśmy dumni z tego, że wartość nowych projektów wygranych na światowych rynkach w roku 2010 trzykrotnie przekroczyła roczne obroty firmy. Świadczy to o zaufaniu naszych klientów w umiejętności firmy, a szczególnie o przeświadczeniu co do konkurencyjności oraz innowacyjności naszych produktów. Rosnące zapotrzebowanie na systemy EPS oraz ewidentny wzrost nowych uruchomień Nexteer w Europe stanowią solidną podstawę analiz potrzeb oraz ewentualnych lokalizacji nowych fabryk.