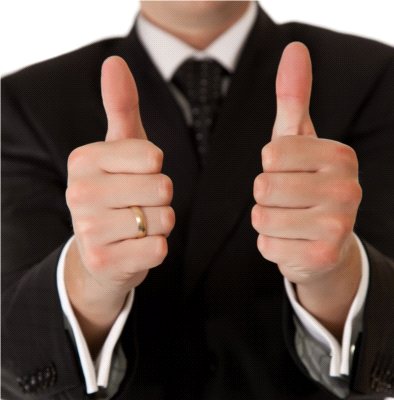
Ujarzmić kluczowe decyzje
Umiejętność podejmowania szybkich i trafnych decyzji jest kluczem do sukcesu w zarządzaniu zmianami na produkcji. Przeniesienie co-produkcji przez FM Polska do innej lokalizacji jest przykładem praktycznego podejścia do procesu decyzyjnego, co może stać się dobrą praktyką...
Praktyczne podejście do procesu decyzyjnego wymaga odpowiedniego uproszczenia i dyscypliny. Firma FM Polska zrealizowała projekt przeniesienia istniejącej co-produkcji modemów kablowych marki Thomson Telecom z jednej lokalizacji do innej w rekordowo krótkim czasie i przy osiągnięciu wymaganych korzyści ekonomicznych.
Trwająca współpraca
Partnerstwo biznesowe pomiędzy FM Polska a Technicolorem rozpoczęło się w Mszczonowie w roku 2004 pod marką – Thomson Telecom. Główną operacją należącą do co-produkcji FM Polska było składanie urządzeń – zestawów do multimedialnych serwisów internetowych (głównie modemów kablowych). Są to dość skomplikowane produkty pod względem technicznym w zakresie co-produkcji.
Szybkość i trafność decyzji zgodnie z modelem TRACE zależy głównie od jakości opisu celu i przyjętych kryteriów oraz wiedzy i doświadczenia zespołu podejmującego decyzję
FM stworzyła proces polegający na całkowitym zarządzaniu łańcuchem dostaw. Firma samodzielnie zamawia komponenty do produkcji, materiały pomocnicze i opakowania. Następnie wykonuje produkcję, a finalny produkt wysyła do wielu odbiorców na całym świecie. Produkcja jest skomplikowana technicznie, gdyż wykracza poza proces składania i pakowania modemów. Do obowiązków operatora FM należy bowiem również wgranie oprogramowania, wykonanie testów itd. Aby produkcja mogła przebiegać bez zakłóceń, Technicolor wynajął przestrzeń magazynową FM Polska. Ze względu na intensywność produkcji (trzy zmiany) w magazynie FM składowane są również komponenty do modemów.
Nowe cele
o kilku latach współpracy Technicolor postawił przed FM Polska nowe wymagania. Co-produkcja modemów charakteryzuje się sezonowością. Wcześniej istniała trudność nawiązania trwałej współpracy z firmami, które zajmowały się kontraktowaniem ludzi na linię produkcyjną. Technicolor poszukiwał sposobów optymalizacji wykorzystania struktury magazynowej tak, aby spadły koszty oraz by wykorzystać wielozmianowość mocy produkcyjnych. Jednym z głównych celów, jaki sobie postawiono, było ograniczenie powierzchni produkcyjnej o 30 procent. Dzięki podjętym krokom chciano uzyskać wymierne efekty w postaci: obniżenia kosztów stałych, obniżenia ceny modemu oraz ograniczenia kosztów logistyki.
W zamian za pozytywną odpowiedź na nowe wyzwania, Technicolor przedłużył kontrakt na kolejny okres gwarantujący partnerstwo przyszłej współpracy. Zaopatrzeniem w surowce i materiały do produkcji miała zajmować się, tak jak poprzednio firma SECROM.
Obaj partnerzy mieli usiąść do negocjacji i uzgodnienia nowych taryf i cen miesiąc po wprowadzeniu zmian przez FM. Aby sprostać wymaganiom Technicoloru, FM rozpatrzył wiele opcji i możliwości. Jedyną trafną i skuteczną decyzją okazała się ta o przeniesieniu co-produkcji do nowej lokalizacji.
TRACE
Decyzja to świadomy, nielosowy wybór jednego z rozpoznawalnych i możliwych wariantów przyszłego działania. Decyzję podejmuje się wówczas, kiedy występuje wybór co najmniej pomiędzy dwoma wariantami. Każda decyzja podejmowana jest fazowo w następującym schemacie: problem – faza przygotowawcza – ustalenie kryterium decyzyjnego – uporządkowanie wariantów decyzyjnych według kryterium – faza podjęcia decyzji – faza realizacji – kontrola.
Kamienie milowe projektu
- Zdefiniowanie przeniesienia linii produkcyjnej do Błonia
- Określenie layotu w nowej przestrzeni
- Zdefiniowanie rozwiązania dla biur i pomieszczeń socjalnych
- Plan przeniesienia zasobów ludzkich
- Przygotowanie nowej struktur IT (hardware)
- Instalacja nowej struktury IT
- IT testy
- Okablowanie i instalacje struktur linii produkcyjnych
- Przeniesienie linii produkcyjnych
- Transfer zapasów magazynowych
- Przygotowanie planu możliwości produkcyjnych
- Audyt gotowości prowadzony prze klienta
- Start produkcji w nowej lokalizacji
Na każdą podjętą decyzję decydujący wpływ mają następujące czynniki: cele, które chcemy zrealizować za pomocą tej decyzji; osobowość osób ponoszących konsekwencje tej decyzji; wielostronność i różnorodność przesłanek (zdobyte do tej pory doświadczenie); stopień przewidywalności sytuacji decyzyjnej (ryzykowność decyzji, jak uda nam się ją zrealizować), zasadność konsultacji z osobami kompetentnymi (budowanie zespołu i wiedzy, która ludziom towarzyszy).
Należy pamiętać, że każdemu czynnikowi oraz etapowi podjęcia decyzji towarzyszy stres. Krzywa oddziaływania stresu pokazuje, że w sytuacjach, gdy potrzebne jest podjęcie kluczowych decyzji, umiarkowany stres jest wskazany. Gorszy wpływ na podejmowanie decyzji ma zbyt duże napięcie i czynniki wysoko stresogenne.
Elementy, które wpływają na decyzje można zamknąć w terminie TRACE (ślad), czyli: Time, Risk, Aim, Committee, Expertise. Czynniki te działają jak naczynia połączone. Idealna sytuacja to krótki czas decyzji i niskie ryzyko. Im proces decyzyjny ma krótszy czas, decydent potrzebuje więcej wiedzy, jaśniej określonego celu oraz lepszej kontroli i analizy, aby ryzyko nie wzrosło do niebotycznych rozmiarów. Mamy wtedy do czynienia z decyzją bardziej oczekiwaną. Niezwykle ważna jest aktualna, szeroka wiedza w przedmiocie, w którym dany zespół będzie podejmował decyzje. Właściwi ludzie, bazując na swoim doświadczeniu i kompetencjach, mogą podejmować trafne decyzje przy słabo opisanych kryteriach celu. Podsumowując: szybkość i trafność decyzji zgodnie z modelem TRACE zależy głównie od jakości opisu celu i przyjętych kryteriów oraz wiedzy i doświadczenia zespołu podejmującego decyzję.
Pięć kluczowych decyzji
Oczekiwane decyzje umożliwiają świadomy wybór i niosą za sobą niskie ryzyko. Zanim FM przeniósł co-produkcję do nowej lokalizacji, musiał stanąć przed podjęciem kluczowych decyzji, które w znaczny sposób wpływały na koszty projektu. Pierwsza decyzja dotyczyła serwera IT. Wybór był następujący: można było zakupić nowy serwer, przenieść stary z poprzedniego obiektu lub pozostawić stary serwer tam, gdzie jest i pracować poprzez łącze. Ryzyko związane z pozostawieniem serwera było zbyt duże, gdyż przerwa w dostawie informacji, brak komunikacji dotyczącej potoku produkcyjnego wywołałby chaos w procesie wytwarzania. Specjaliści FM zostali wysłani do Francji na konsultacje. Kryterium ryzyka przeważyło, zdecydowano się zakupić nowy serwer.
Kolejna kwestia dotyczyła infrastruktury, czyli instalacji elektrycznej, IT itd. Firma FM wzięła pod uwagę czas, jaki byłby potrzebny na przejście wszystkich procedur (plany, odbiory techniczne) i montaż nowej infrastruktury oraz zmieniające się przepisy i standardy. Zdecydowano się zamontować nową infrastrukturę.
Następnie zapadła decyzja dotycząca biur i szatni dla personelu, których wcześniej nie było. Warianty były cztery: zbudować nowy budynek biurowy, zastosować kontenery lub inne rozwiązania (np. namioty), zakupić ewentualne kontenery, czy wydzierżawić. Ostatecznie firma wydzierżawiła kontenery, aby pracownicy mieli gdzie się przebierać do pracy.
Kolejnym krokiem było rozmieszczenie aktywności (layout) w nowym środowisku. W tym przypadku na decyzję było więcej czasu, gdyż maszyny wjeżdżały do obiektu dopiero w momencie uruchomienia produkcji. W tym celu FM mogła skopiować przepływy i organizację powierzchni, jaką dotychczas stosowano lub zaproponować nowy układ, zapewniając w ten sposób spełnienie wymagań. Zadecydowano się na przeniesienie i udoskonalenie layotu, co, dzięki odpowiedniej fazie przygotowawczej, nastąpiło w ciągu 48 godzin.
FM – Błonie
FM dokonała transferu aktywności co-produkcji z Mszczonowa do Błonia. Podczas przeniesienia co-produkcji do nowej lokalizacji firma zastosowała retroplaning, który realizowano poprzez wzrost kompetencji zespołu podejmującego decyzje, intensywne wykorzystanie wiedzy eksperckiej w danych dziedzinach i precyzyjny opis celu. Dzięki zmianie lokalizacji firma zoptymalizowała nową powierzchnię, udoskonaliła layout co-produkcji, a także zapewniła ciągłość i utrzymała właściwy wolumen produkcji. W nowym magazynie zredukowano poziom rezerwacji miejsc paletowych o 20 procent, przy tych samych stawkach składowania i handlingu.
FM zaproponowała Technicolor partycypację w kosztach „technicznych”, ustalono budżet związany z partnerskimi relacjami obu firm. Przedsiębiorstwa zoptymalizowały wykorzystanie zasobów ludzkich oraz określiły wysokość współudziału w kosztach transportu i organizacji nowej przestrzeni produkcyjnej.
W nowej platformie technicznej liczącej 37 000 mkw. powierzchni, oprócz produkcji modemów kablowych składowane są również leki, kosmetyki, środki chemiczne itd. Obiekt dedykowany jest całkowicie dla produktów „non food”.
Nowa lokalizacja w Błoniu zapewniła pracownikom równy dystans dojazdu do pracy, dzięki czemu wzrosła szansa na utrzymanie dawnego zespołu. Obiekt posiada sześć hal magazynowych, 42 doki załadunkowo- rozładunkowe oraz 70 pracowników. Co-produkcja Technicolor zorganizowana została w centrum platformy FM. Pozyskanie każdego nowego klienta w platformie FM obniża koszty utrzymania pozostałych hal.