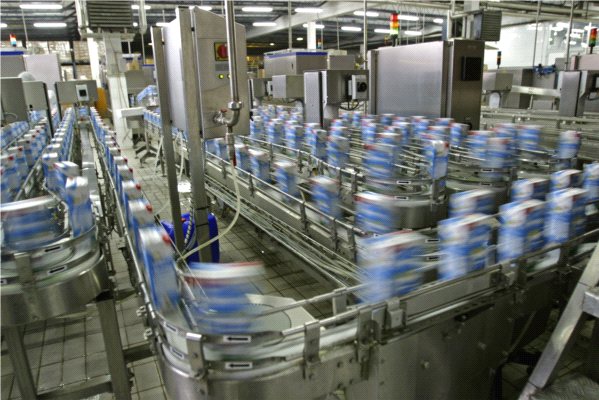
W gąszczu danych utrzymania ruchu
Niezależnie od tego, w jakiej branży realizujemy swoją działalność operacyjną, jeżeli wykorzystujemy przy tym znaczące zasoby techniczne, należy postawić pytanie: ile muszę wiedzieć o swoim systemie eksploatacji? Właściwa odpowiedź jest uwarunkowana wieloma czynnikami, takimi...
Obserwując to, co dzieje się we współczesnych standardach dotyczących zarządzania majątkiem technicznym, można ulec wrażeniu, że bezpowrotnie mijają czasy, w których wiedza na temat tego, co dzieje się w technicznym aspekcie naszych systemów produkcyjnych (transportowych, wydobywczych), spoczywa tylko i wyłącznie w głowie głównego inżyniera, kilku mechaników oraz w papierowej dokumentacji technicznej. W realizowaniu działań utrzymania ruchu i zarządzaniu zasobami technicznymi mamy do czynienia z różnymi rodzajami informacji. Zastanówmy się, jak są one ważne w podnoszeniu efektywności przedsiębiorstw i czego używa się w dzisiejszych czasach, by lepiej nimi zarządzać.
Narzędzia i metodologie w UR
Nowoczesne utrzymanie ruchu to nie tylko „gaszenie pożarów”, czyli reagowanie na zdarzenia awaryjne. Jest to przede wszystkim świadome utrzymanie techniczne. Wiąże się to nie tylko z coraz lepszą gotowością do realizacji zadań awaryjnych, ale przede wszystkim coraz lepszą organizacją działań prewencyjnych (zapobiegawczych) mających zapewnić bezawaryjną pracę.
Cele utrzymania ruchu balansują gdzieś pomiędzy kosztami a pożądaną niezawodnością. Znalezienie złotego środka nie jest wcale łatwe. W ramach utrzymania ruchu na przestrzeni lat powstało wiele metodologii wspierających zintegrowane doskonalenie w tym obszarze. Często mówi się o Total Productive Maintenance, Reliability Centered Maintenance czy Lean Maintenance. Wszystkie te metodologie bazują na dobrej organizacji informacji i danych eksploatacyjnych. Potrzebne są zatem narzędzia do zarządzania tymi informacjami.
Wśród przeważającej większości firm wykorzystywanych jest zaledwie od kilku do kilkunastu procent funkcjonalności oferowanej przez system
Zapewnienie pożądanej niezawodności obiektów technicznych w akceptowalnych kosztach wiąże się z wieloma specjalistycznymi obszarami. Są to między innymi: diagnostyka techniczna, planowanie i harmonogramowanie pracy, zarządzanie częściami zamiennymi i środkami eksploatacyjnymi, budżetowanie, zarządzanie cyklem życia obiektów itd. Niezwykle trudno jest spiąć wszystkie te obszary w ujęciu informacyjnym i koordynacji prac. Z tego względu zainteresowaniem cieszą się systemy IT, które są dedykowane zarządzaniu utrzymaniem ruchu i tzw. majątkiem technicznym.
CMMS, czyli Computerized Maintenance Management System to nic innego jak system informatyczny poświęcony gromadzeniu informacji na temat eksploatacji oraz wspomagający zarządzanie pracą. Integruje w sobie zazwyczaj wiele modułów związanych z posiadanymi zasobami osobowymi i technicznymi oraz organizacją ich pracy.
Coraz częściej w rodzimym środowisku eksploatacyjnym pojawia się też szeroko znany na świecie termin EAM. Podczas gdy CMMS jest podstawowym narzędziem wspomagającym zarządzanie utrzymaniem ruchu, istnieją jeszcze systemy z punktu widzenia funkcjonalności bardziej rozbudowane. Skrót wywodzi się od angielskiego „Enterprise Asset Management”, co w dosłownym przetłumaczeniu oznacza zarządzanie majątkiem przedsiębiorstwa. EAM to nic innego jak narzędzie zarządzania cyklem życia wyposażenia obejmujące oprócz funkcjonalności CMMS (wspomagającego zarządzanie UR, planowanie pracy itp.) również szczegóły dotyczące rejestru wyposażenia, inwestycji, bezpieczeństwa, dokumentacji technicznej, gospodarki magazynowej i zakupów, zarządzania podwykonawcami itd.
Zarówno CMMS, jak i EAM stają się codziennością wielu przedsiębiorstw. Mogą one funkcjonować jako odrębne systemy niezwiązane z firmowymi zasobami np. ERP lub jako ich integralne lub interfejsowane elementy.
Czy UR generuje informacje?
Działy techniczne czy utrzymania ruchu są istną fabryką informacji. Dlaczego? Liczebność obiektów technicznych, pracowników, duży udział niestandardowych działań i wiele innych czynników powodują, że obszar techniczny wymaga szczególnego podejścia do gromadzenia analizy płynących z niego informacji.
CMMS integruje w sobie zazwyczaj wiele modułów związanych z posiadanymi zasobami osobowymi i technicznymi oraz organizacją ich pracy
Generowane dane przez wielu mogą być niedostrzegane i niedoceniane, jednak warto jest wykonać „rachunek sumienia” i sprawdzić w swoim dziale technicznym, jakie dane są gromadzone i w jaki sposób są później wykorzystywane. Co się okazuje, w większości organizacji, nawet jeżeli są zaimplementowane CMMS/EAM, dane tam gromadzone mają bardzo mały współczynnik wykorzystania. Dlaczego tak się dzieje?
Generowane w systemie utrzymania ruchu informacje mają różny charakter i aby móc je efektywnie wykorzystywać, niezbędne są trzy „czynniki”: wykształcona i doświadczona kadra inżynierska znająca dobre praktyki nowoczesnego zarządzania technicznego; standard akwizycji i przetwarzania informacji; narzędzia ułatwiające gromadzenie i analizę danych oraz łączenie informacji z wielu źródeł.
Bez powyższych krytycznych elementów, niezależnie czy będą one miały bardziej lub mniej sformalizowaną postać, bardzo trudno jest właściwie wykorzystywać informacje płynące szerokimi strumieniami z systemu eksploatacji.
Hierarchia danych?
Logicznym następstwem rozważań dotyczących mnogości i różnorodności danych pochodzących z UR jest próba określenia, czy – i jeżeli tak to dlaczego – pewne informacje są ważniejsze od innych. W pierwszej kolejności należy postawić pytanie: jakie informacje powinienem gromadzić? W większości sytuacji niezbędne jest skupienie się w na pewnych obszarach swojego systemu eksploatacji. Próba odpowiedzi na to pytanie mogłaby wyglądać następująco: priorytetem w zakresie gromadzenia danych w naszym systemie eksploatacji są informacje o maszynach i ich strukturze, wykonywanych działaniach (zlecenia pracy), wykorzystaniu części zamiennych, bezpieczeństwie, kosztach (np. personelu, serwisów zewnętrznych, części zamiennych), efektywności pracowników i maszyn, wykorzystaniu serwisów zewnętrznych.
Czy któreś z tych informacji są ważniejsze od innych? Wszystko zależy od osoby, która będzie chciała je wykorzystać. Warto jednak zwrócić uwagę, że ogólnie nakreślone obszary zainteresowania stanowią w wielu firmach tak olbrzymi zakres danych, że nie sposób rozpocząć gromadzenie tych informacji w odniesieniu do wszystkich zasobów technicznych równocześnie. W takiej sytuacji proponuję zadać pytanie dotyczące istotności informacji inaczej: czy niektóre z obszarów mojego przedsiębiorstwa są ważniejsze niż inne? Takiego uszeregowania dokonuje się wykorzystując zagadnienie tzw. „krytyczności”. Otóż niektóre obszary firm są z punktu widzenia utrzymania ruchu bardziej krytyczne, a niektóre mniej. Wynikać to może z kilku względów. Po pierwsze, niektóre linie czy poszczególne maszyny produkcyjne mogą być niezbędne do realizowania kluczowych zamówień. Jest to czynnik biznesowy, który przekłada się bezpośrednio na rentowność firmy, i tym samym przykład krytyczności ekonomicznej. Możemy rozróżniać również inne kryteria obejmujące zarówno ocenę ilościową jak i jakościową (np. niezawodność, bezpieczeństwo, wpływ na środowisko naturalne). Efektem analizy krytyczności powinna być odpowiedź na pytanie, które zasoby techniczne są krytyczne, a które nie? Wydzielenie maszyn, systemów krytycznych umożliwia rozgraniczenie zakresów gromadzenia informacji i również wyznaczenie priorytetowych obszarów, gdzie CMMS lub EAM powinny być wykorzystywane.
Cele utrzymania ruchu balansują gdzieś pomiędzy kosztami a pożądaną niezawodnością
Kryteria do hierarchizacji zasobów dobierane są zazwyczaj przez zespół projektowy złożony z przedstawicieli różnych szczebli operacyjnych i zarządczych. Całokształt działań związanych z określeniem ważności poszczególnych systemów oraz istotności informacji generowanych przez te systemy powinien odbywać się w zgodzie ze strategią operacyjną przedsiębiorstwa. Jeżeli taka nie istnieje, w czasie prac nad „systemem wartości” w obszarach technicznych warto zastanowić się nad istotą podejścia naszej firmy do zasobów technicznych oraz określić, jakie cele są przed nami stawiane i z czego one wynikają. Ponieważ utrzymanie ruchu to ciągłe poszukiwanie balansu między kosztami i niezawodnością maszyn, próba definiowania istotności informacji powinna być związana z naszymi długofalowymi planami w tym zakresie.
Wdrażanie systemów
Systemy CMMS oraz EAM są narzędziami oferującymi bogatą funkcjonalność w zakresie akwizycji, katalogowania oraz analizy danych dotyczących systemów technicznych. Systemy te można nazwać młodszymi i bardziej wyspecjalizowanymi braćmi rozwiązań ERP (ang. Enterprise Resource Planning).
Rozwiązania CMMS/EAM zyskały szerokie uznanie w wielu systemach eksploatacji, gdzie inżynierowie i menedżerowie muszą radzić sobie z ogromną ilością danych oraz podejmować uzasadnione decyzje zarządcze i operacyjne.
Wdrożenie systemu typu CMMS / EAM nie jest działaniem bezbolesnym. Jak każda zmiana w organizacji, również projekt tego typu napotka zawsze na pewien opór. Znakomicie zatem sprawdzają się tu tzw. dobre praktyki związane z projektowaniem procesów biznesowych i zarządzaniem zmianą (ang. Change Management). Pozwalają one nie tylko lepiej „sprzedać” rozwiązanie w organizacji, ale również uzbroić pracowników w dostateczną wiedzę na poszczególnych etapach.
Okazuje się, że wśród przeważającej większości firm, które mają działające systemy CMMS/EAM, wykorzystywanych jest zaledwie od kilku do kilkunastu procent funkcjonalności oferowanej przez system. Wynika z tego, że nawet najlepszy system CMMS czy EAM nadal pozostaje tylko narzędziem, które wspomaga zarządzanie i operacje. W ramach każdego z systemów oferowane jest pewne podejście do akwizycji i zarządzania informacjami. Kluczem do sukcesu jest jednak właściwe określenie potrzeb swojej organizacji, dostosowanie do nich narzędzia i przystosowanie firmy do nowych standardów pracy. Wdrożenie rozwiązań informatycznych jest również okazją do wprowadzenia korzystnych zmian w organizacji, ustanowienia nowych zasad pracy i wprowadzenia pracowników na wyższy poziom świadomości i wiedzy o utrzymywanych systemach technicznych.
Nie sposób wspomnieć również o podejściu wielu firm, które chcąc uniknąć „nietrafionej” implementacji rozwiązań wspomagających UR, korzystają z ogólnodostępnych baz danych i arkuszy kalkulacyjnych w celu gromadzenia informacji i ich późniejszych analiz. Nie można nazwać tego podejścia błędnym, jednak warto zastanowić się, jaką strukturę danych przyjąć w takim okresie przejściowym, aby zgromadzone informacje można w przyszłości zaimportować i wykorzystać w nowych systemach.
Przydatność danych w UR
Oczywiście intuicyjna odpowiedź na to pytanie jest obecna w świadomości większości osób zajmujących się utrzymaniem ruchu lub wykorzystujących takie usługi. Używając danych z utrzymania ruchu chcemy przede wszystkim dobrze kontrolować naszą efektywność oraz doskonalić eksploatację.
Wśród klientów BalticBerg Consulting najczęściej określanym celem jest podniesienie niezawodności ich systemów produkcyjnych, transportowych i wydobywczych. W tym zakresie dane pochodzące z systemu eksploatacji stanowią podstawowe źródło wiedzy na temat występujących uszkodzeń, czasu przestojów oraz zasobów wykorzystywanych w działaniach naprawczych. Podejście „proniezawodnościowe” związane z realizacją różnych analiz wymaga od eksploatatorów gromadzenia właściwych informacji. Między innymi kluczowe stają się informacje o uszkodzeniach (ich przyczynach oraz charakterystyce występowania), zasobach (personel techniczny, części zamienne), realizowanych obsługach (realizacja zleceń pracy) oraz innych informacjach związanych z poszczególnymi zdarzeniami eksploatacyjnymi.
Celem wymienianym stosunkowo często przez klientów BalticBerg jest również lepsza kontrola kosztów. Mimo wszechobecnej opinii o wprowadzanych oszczędnościach, w wielu firmach menedżerowie zdają sobie sprawę, że drastyczne cięcia wydatków w obszarze UR mogą doprowadzić do dezorganizacji technicznej przedsiębiorstwa. Z tego względu istotnym staje się nie tylko suma kosztów UR, ale dokładniejsza kontrola tego, jak wydatkowany jest budżet i czy pieniądze idą na pewno na właściwe zadania. Ciężko dokonać takiej analizy bez reprezentatywnych danych pochodzących z systemu eksploatacji.
Innym istotnym celem jest ograniczenie ryzyka związanego z ewentualną rotacją zasobów ludzkich. W przypadku niesformalizowanego systemu informacji, gdzie większość wiedzy na temat eksploatowanych maszyn znajduje się w głowie kilku mechaników, istnieje duże zagrożenie, że w przypadku odejścia któregokolwiek z nich firma bezpowrotnie straci dużą część historii. Jej odbudowanie może się okazać bardzo kosztowne, a w niektórych przypadkach nawet niemożliwe. Posiadanie dobrze zaprojektowanego systemu gromadzenia danych UR pozwala w dużej części zabezpieczyć się przed takim zdarzeniem.
Istnieje oczywiście dużo więcej powodów przemawiających za przemyślanym gromadzeniem danych UR i wykorzystaniem rozwiązań typu CMMS / EAM, które bezpośrednio przekładają się na możliwość zwiększenia niezawodności systemów technicznych oraz racjonalizację kosztów UR. Zachęcam do dokładniejszego przyjrzenia się gromadzonym w firmach informacjom pochodzących z systemów technicznych. Przede wszystkim należy zadać sobie pytanie: czy gromadzimy informacje pochodzące z UR, a jeżeli tak, to jak wykorzystujemy dane z UR, jakie mamy informacje na temat awarii, jak przechowywane są zgromadzone dane? Jeżeli odpowiedzi nie będą satysfakcjonujące i przekonujące, można być pewnym, że z każdą godziną tracimy istotne dane, a tym samym tracimy również realne pieniądze.