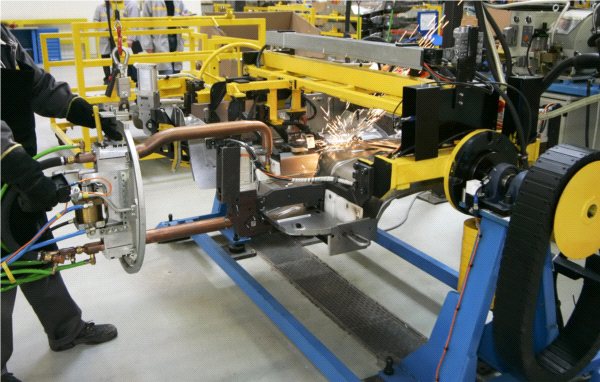
Efektywność utrzymania ruchu
Niemalże na każdym szczeblu zarządczym i operacyjnym, niezależnie czy dotyczy to produkcji, utrzymania ruchu, logistyki czy systemów IT, spotykamy się z terminem efektywności lub jego zbliżonymi obliczami – wydajnością, jakością, rentownością, niezawodnością.Menedżerowie...
Menedżerowie przywiązują coraz większą uwagą do narzędzi mierzenia efektywności, zgodnie z zasadą, że nie można zarządzać czymś, czego nie mierzymy. Istnieje duże zapotrzebowanie na systemy mierzenia efektywności szczególnie w firmach o charakterze produkcyjnym, wydobywczym, transportowym, które posiadają znaczącą ilość zasobów technicznych. Wiele firm z rodzimego rynku zgłosiło się do BalticBerg z zamówieniem opracowania i wdrożenia takiego systemu lub chęcią rozwiązania problemów w systemach już istniejących.
Klarowność informacji
Efektywność, w języku angielskim określana dla obszarów operacyjnych jako „performance”, rozumiana jest często w różny sposób (w zależności od dziedziny i warunków, których dotyczy). Dla systemów utrzymania ruchu jest to właściwość ludzi lub obiektów technicznych spełniania przez nich wymagań w różnym kontekście: niezawodnościowym, ekonomicznym, jakościowym, wydajnościowym, energetycznym itd. Istotą oceny efektywności jest określenie prawdopodobieństwa zachowania przez system nominalnych (lub pożądanych) osiągów w trakcie realizacji zadań. Efektywność w systemach UR określa się zatem w kategoriach rezultatów osiągniętych (dane historyczne) lub oczekiwanych (dane prognozowane), łącząc użyteczne grupy informacji z wybranych obszarów dotyczących użytkowania i utrzymania maszyn oraz instalacji.
Organizacje chcące doskonalić swoje UR zwracają szczególną uwagę na realizowane strategie eksploatacyjne
Na podstawie identyfikowalnych i interpretowalnych informacji z systemu UR możliwe jest podejmowanie uzasadnionych decyzji zarządczych, inwestycyjnych i eksploatacyjnych. Między innymi mogą one dotyczyć wyboru określonych metod utrzymania systemów technicznych. Wiąże się to z m. in. z wyborem i wdrożeniem strategii utrzymania w poszczególnych obszarach (strategia „do uszkodzenia” ang. Run-To-Failure, strategia planowo-zapobiegawcza ang. Planned Maintenance czy strategia według stanu technicznego ang. Condition Based Maintenance), podjęciem działań modyfikacyjnych i/lub modernizacyjnych lub działań naprawczych w odpowiednim czasie.
Działania mogą być podejmowane w sposób odosobniony lub zintegrowany, a ich celem jest oczywiście podniesienie efektywności według wybranych kryteriów. Selekcja i dostosowanie działań jest jednak możliwe tylko pod warunkiem posiadania odpowiedniej wiedzy o eksploatowanych systemach, które mają charakter wielocechowy. Informacje dotyczące UR mogą zawierać dane z wielu obszarów: techniczny – np. informacje dotyczące niezawodności, wydajności, jakości, sprawności itd.; organizacyjny – np. struktura pracowników, przyjęta strategia eksploatacji w poszczególnych podsystemach eksploatacji, struktura maszyn i urządzeń itd.; ekonomiczny – np. koszty utrzymania w skali roku dotyczące pracowników własnych i podwykonawców, koszty części zamiennych, koszty środków utrzymania (czyściwa, narzędzia) itd.
Podejmowane decyzje zarządcze muszą być właściwie umotywowane. Niezbędne jest zatem uwzględnianie informacji z więcej niż jednego z wymienionych powyżej obszarów. Generuje to potrzebę wielokierunkowego analizowania danych eksploatacyjnych i operacyjnych. I teraz kluczowe pytanie – jak to zrobić?
Traktat PMS
Odpowiedzią są systemy mierzenia i analizy efektywności (w tym wypadku efektywności działów UR). Czym jest system mierzenia i analizy efektywności (ang. Performance Measurement System – PMS)? PMS zawiera w sobie definicję narzędzi mierzenia efektywności w konkretnym środowisku operacyjnym oraz informacje uzupełniające takie jak: opis środowiska, propozycje interpretacji, wskazania do analizy wyników, wskazania do walidacji danych i samego systemu itd. Zawierają w sobie szereg informacji i stanowią swego rodzaju „umowę” czy „traktat” pomiędzy produkcją, utrzymaniem ruchu i zarządem firmy.
PMS może zawierać mierzalne cele, które wyznaczają kierunek rozwoju systemu UR
Systemy takie odnoszą się przede wszystkim do wyboru sposobu definiowania interesujących grup informacji, procedury gromadzenia danych, ich obliczania, walidacji i interpretacji. Ostatnim elementem jest zazwyczaj definicja dystrybucji odpowiedzialności i struktury informacyjno-raportowej. Czy łatwo to stworzyć i wdrożyć?
Pułapki KPI
Jak jednak definiuje się istotne grupy informacji? Zazwyczaj menedżerowie i inżynierowie, wyznaczając istotne grupy informacji, kierują swoją uwagę na kluczowe efekty działalności systemu UR: rezultaty operacyjne, niezawodność, jakość, wydajność, opłacalność realizowanych działań eksploatacyjnych. Kluczowe wskaźniki efektywności KPI są narzędziami, dzięki którym przedstawia się te informacje. Stanowią zestawienie wybranych wartości i mogą być prezentowane w ujęciu wartościowym oraz jako trendy w wybranych zakresach czasowych. Ich zastosowanie znacznie ułatwia osiągnięcie szeregu celów zarządczych i eksploatacyjnych.
Kiedy pomagam organizacjom wdrażać rozwiązania z zakresu efektywności, zawsze uprzedzam, że KPIs, choć są używane na całym świecie i można znaleźć wiele definicji pomagających w ich zrozumieniu i wdrożeniu (literatura, normy, standardy), to mają w sobie wiele pułapek, które mogą zmylić niejednego menedżera. Dokonanie wyboru wskaźników oraz ich właściwe zdefiniowanie to tylko pierwszy etap, a niestety już na tym etapie pojawią się zazwyczaj problemy. Będą one dotyczyć konkretnych źródeł informacji i interpretowania pewnych nazw, które w normach (celowo) nie są do końca wyjaśnione. Wynika to z tego, że twórcy norm oraz autorzy literatury dokładnie zdają sobie sprawę, że nie ma firm jednakowych i definicja np. czasu przestoju awaryjnego będzie u jednych obejmowała czas rozruchu, a u innych nie.
Wskaźniki
Spośród najczęściej stosowanych wskaźników ekonomicznych warto wymienić stosunek całkowitych kosztów UR (ang. TMC – Total Maintenance Cost) do tzw. wartości odtworzeniowej obiektu/przedsiębiorstwa (ang. ARV- Asset Replacement Value). Wskaźnik ten wywodzi się z obliczeń, jakie menedżerowie często dokonują przy zakupie elementów majątku trwałego, rozważając, ile kosztuje utrzymanie obiektu w stosunku do ceny jego zakupu. Wskaźnik ten jest używany przez wiele organizacji nie tylko na poziomie maszyny lub grupy maszyn, ale przede wszystkim na poziomie całego zakładu produkcyjnego. W jego adaptacji i wdrażaniu kryje się jednak wiele pułapek. Obliczenie ARV jest już dla wielu organizacji nie lada problemem, gdyż spośród wielu sposobów muszą wybrać jeden i być konsekwentnymi w jego stosowaniu, aby wskaźnik pozostał użyteczny. W zależności od branży, wielkości przedsiębiorstwa, rodzaju wyposażenia i realizowanej działalności wskaźnik ten zazwyczaj zawiera się w przedziale od 1 do 5,5 proc. Jednak trudno mówić tu o ogólnych wartościach tzw. najlepszej praktyki – każdą organizację należy rozpatrywać indywidualnie.
Innym wskaźnikiem bardzo często wykorzystywanym w systemach mierzenia i analizy efektywności utrzymania ruchu jest średni czas między awariami (ang. MTBF – Mean Time Between Failures). Jest to stosunek czasu operacyjnego do liczby uszkodzeń, które wystąpiły w rozpatrywanym przedziale czasu. Warto zaznaczyć, że wskaźnik ten może być wykorzystywany tylko dla obiektów odnawialnych. Dla obiektów nieodnawialnych (nienaprawialnych) stosuje się jego odpowiednik – średni czas do uszkodzenia MTTF (ang. Mean Time To Failure). MTBF kryje w sobie wbrew pozorom wiele dowolności (pułapek). Organizacje chcące mierzyć za pomocą tego wskaźnika muszą dokładnie zdefiniować, co mierzą. Czas operacyjny może przez każdą organizację być rozumiany w inny sposób. Najczęstszą różnicą jest uwzględnianie albo nieuwzględnianie w tym parametrze tzw. czasu gotowości bez zamówienia – NONA (ang. No Order No Activity). Niektóre organizacje wliczają ten stan do czasu operacyjnego, a inne nie. Są oczywiście ku temu konkretne powody. Definicja uszkodzeń też nie jest tak oczywista, jak by się wydawało. Zgodnie z polskimi normami jest to stan, w którym obiekt techniczny utracił zdatność techniczną. W praktycznym zarządzaniu utrzymaniem ruchu definicja ta może być rozumiana na wiele różnych sposobów. Niektóre organizacje definiują uszkodzenia bardzo dokładnie i tym sposobem określają, co jest stanem uszkodzenia, a co np. mikroprzestojem lub regulacją.
Organizacje chcące doskonalić swoje UR zwracają szczególną uwagę na realizowane strategie eksploatacyjne. Innymi słowy mierzą efektywność między innymi w zakresie realizowania utrzymania prewencyjnego. Jednym ze wskaźników stosowanych w tym zakresie jest procent wykonania planów prewencyjnych.
Niejednolite wsparcie
Projekty, które ukierunkowane są na zbudowanie w organizacjach użytecznego systemu mierzenia i analizy efektywności, mają różny horyzont czasowy, na który wpływają liczne czynniki kształtujące organizację klienta. Niektóre firmy są przez naszych konsultantów wspierane kompleksowo w trakcie całego projektu, inne natomiast potrzebują jedynie skutecznego rozpoczęcia i ukierunkowania projektu, a następnie okresowego wsparcia doradczego.
Podczas rozmów z menadżerami technicznymi na temat systemów mierzenia efektywności jednym z najczęstszych pytań, jakie słyszę, jest: „za ile będziemy mogli z tego korzystać?” Oczywiście zawsze staram się odpowiedzieć możliwie dokładnie szacując czas, jaki potrzebny jest w danej organizacji na stworzenie takiego systemu. Zawsze proponuję jednak, abyśmy najpierw dokładnie omówili, co klient chciałby mierzyć lub aby odniósł się do naszych propozycji, gdyż wdrożenie może zająć zarówno miesiąc, jak i dziewięć miesięcy. W BalticBerg Consulting bardzo często stajemy przed wyzwaniem stworzenia dla klienta dedykowanych rozwiązań. Dlatego trudno mówić o pewnych sztywnych zasadach dotyczących czasu wdrożenia.
Dedykowane rozwiązania
Przykłady wskazujące na potrzebę indywidualnego dostosowania systemów mierzenia efektywności można mnożyć, a najwięcej z nich będzie dotyczyć oczywiście interpretacji, wyznaczania celów i dystrybucji odpowiedzialności. W tym zakresie już nawet w małym procencie kopia rozwiązań z innych systemów byłaby sukcesem. Jest to jednak prawie niemożliwe. Z tego względu warto wesprzeć się radą tych, którzy już to robili w swoich firmach lub w ramach działalności eksperckiej i osiągnęli zamierzone rezultaty w całej strukturze firmy.
Kiedy pracujemy przy projektach związanych z mierzeniem efektywności, najczęściej rozpatrujemy cykl, który opracowaliśmy w BalticBerg na nasze potrzeby. Obrazuje on poszczególne kroki w ciągłym doskonaleniu efektywności operacyjnej. Każdy z przedstawionych elementów (mierzenie, diagnozowanie, doskonalenie i utrwalanie) to powiązane ze sobą grupy zadań. W każdym z nich można wyróżnić trzy etapy: przygotowanie, realizacja, kontrola rezultatów (załącznik 1).
Jest to autorskie rozwiązanie ekspertów BalticBerg znacznie ułatwiające planowanie projektów w zgodzie z tzw. najlepszymi praktykami. Systemy mierzenia efektywności przede wszystkim dają nam informację o tym, czy dobrze zarządzamy i jak realizujemy nasze działania. PMS może zawierać mierzalne cele, które wyznaczają kierunek rozwoju systemu UR. Poprzez analizę efektywności możemy znaleźć obiektywną odpowiedź na temat realizowanych działań.
Korzyścią jest również możliwość rozliczania personelu oraz menedżerów z realizacji ich działań. Mając dobrze dostosowane narzędzia, można polegać na otrzymywanych rezultatach i na tej podstawie definiować zespołowe i personalne cele, których realizacja może podlegać weryfikacji.
Droga do benchmarkingu
Mierzenie i analiza efektywności są również punktem wyjściowym do benchmarkingu. Oznacza to, że chcąc porównywać wewnątrz mojej organizacji (np. dwie fabryki lub dwie linie produkcyjne) lub na zewnątrz (z innymi firmami) muszę zacząć od mierzenia siebie. Benchmarking pozwala nie tylko na uzyskanie odpowiedzi, czy robimy coś lepiej lub gorzej, ale przede wszystkim co robimy inaczej. Jest to narzędzie, które pozwala na doskonalenie organizacji poprzez korzystanie z lepszych praktyk naszych partnerów i wybranych obszarów naszej własnej organizacji.
Prawdziwy zysk przychodzi jednak, gdy umiemy dokładnie powiedzieć, jaki jest nasz punkt odniesienia i gdzie powinniśmy skierować naszą uwagę (w które obszary firmy, na które maszyny, na jakie funkcje pracownicze). Wtedy jest czas na opracowanie strategii przejścia z punku A do punktu B. Jak tego dokonać? Oczywiście możliwości jest przed nami wiele. Na przestrzeni lat menedżerowie techniczni i operacyjni oraz grupy konsultantów na całym świecie wypracowały wiele metod związanych z doskonaleniem działań UR. Moim zdaniem nie warto wyważać otwartych drzwi i powinno się rozważyć skorzystanie z już sprawdzonych rozwiązań. W ogólnym rachunku na pewno będzie to znacznie tańsze i skuteczniejsze niż wynalezienie koła od nowa.