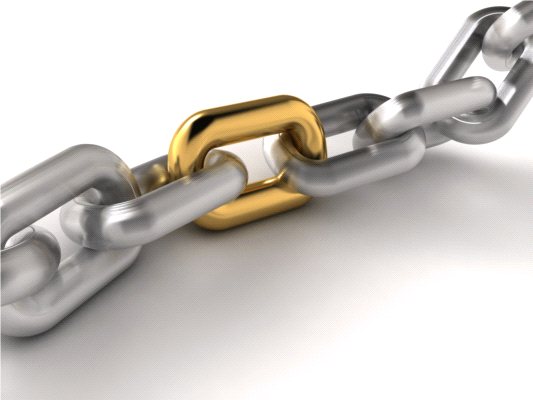
Łańcuch dostaw w masowej kastomizacji
Skuteczność i efektywność masowej kastomizacji w określonym przedsiębiorstwie jest uwarunkowana i umożliwiana przez modularność procesu i produktu, odpowiednie systemy operacyjne, zastosowanie koncepcji punktu rozdziału zamówienia oraz odraczania, a także przez dostosowanie...
Dla powodzenia masowej kastomizacji nieodzowna jest modularność procesów oraz modularność produktu. Modularność procesu polega na dekompozycji procesu na niezależne moduły, tak aby mogły one być traktowane jako logiczne jednostki, które są konfigurowane i łączone dla zbudowania odpowiedniego wariantu procesu.
Niezbędną dla kastomizacji elastyczność procesów produkcyjnych osiąga się poprzez małe, zbudowane na zasadzie modułów jednostki procesu (zespoły, komórki, gniazda), z krótkimi cyklami produkcyjnymi, posiadające zdolność do łatwego dostosowania się i samodzielnego decydowania o podziale pracy. W skład modułów wchodzą wysoce wykwalifikowani i autonomiczni pracownicy. Każdy moduł ciągle dąży do podniesienia swoich zdolności. Sukces modułu zależy od tego, jak skutecznie, szybko i efektywnie wykonuje swoje zadania i jak dobry jest w rozszerzaniu swoich zdolności. Projektowanie procesu wiąże się z ustaleniem rodzaju modułów i ich konfiguracji dla skutecznego, szybkiego i efektywnego wykonania skastomizowanego produktu.
System masowej kastomizacji łączący różne moduły musi posiadać następujące atrybuty: szybkość – moduły i procesy muszą być łączone razem bardzo szybko. Pozwala to na szybką reakcję na różne potrzeby klienta; taniość – łączenie nie powinno zwiększać znacząco kosztów procesów; gładkość – połączenia i indywidualne moduły nie powinny być odczuwalne przez klienta, aby obsługa klienta na tym nie ucierpiała. Wszystkie moduły powinny działać jak jeden ciągły proces; łatwość.
Sieci lub grupy modułów powinny być formowane przy małych nakładach. Komunikacja musi po połączeniu funkcjonować natychmiast, bez straty czasu na integrowanie zespołów.
Podział procesu na niezależne moduły pozwala w pewnych przypadkach zmieniać kolejność operacji w procesie w celu przesunięcia operacji różnicujących produkt w dół łańcucha dostaw i w ten sposób umożliwić zastosowanie opóźnionego kastomizowania produktów, określanego jako odraczanie.
Rodzaje modularności
Modularność produktowa jest osiągana poprzez takie projektowanie produktu, aby składał się z niezależnych modułów dostępnych w kilku standardowych wariantach. Kastomizacja produktu następuje poprzez kombinację lub modyfikację tych modułów odpowiednio do indywidualnych potrzeb klienta. Ponieważ określony typ modularności jest charakterystyczny dla jednostki kastomizującej, istnieje wiele jej odmian. Według sposobu, w jaki produkt jest montowany z modułów, wyróżnia się różne typy modularności.
Modularność komponentu wspólnego – jeden komponent rdzeniowy (moduł) jest wykorzystywany do budowania skastomizowanych produktów. Przykładem są windy, gdzie jeden system napędowy jest wspólny, podczas gdy kabina windy i inne elementy są dostosowywane do indywidualnych cech budynku.
Modularność komponentów zamiennych – moduły mogą być dobierane dla zapewnienia produktowi odpowiednich cech. Przykładem może być wybór procesora z kilku możliwych podczas konfiguracji skastomizowanego komputera.
Modularność mieszana – podobna do modularności komponentów zamiennych, z tą różnicą, że połączenie modułów powoduje utratę ich unikatowej tożsamości. Przykładem może być kastomizacja farby ze składników o standardowych kolorach.
Modularność segmentowa – ten typ modularności skupia się na możliwości aranżacji standardowych modułów w unikatowy produkt. Przykładem mogą być segmenty meblowe lub systemy klocków Lego.
Modularność komponentów ciętych – w tym przypadku następuje zmiana wymiarów modułów. Przykładem modułów ciętych są soczewki w okularach oraz profile okienne.
Modularność busowa – ten typ modularności umożliwia dodawanie modułów do istniejącej bazy (korpusu). Modularność busowa umożliwia kastomizację poprzez dostarczanie konstrukcji, która może zawierać różne zestawy komponentów przy zachowaniu kontroli nad produktem finalnym, np. system świateł w pojeździe.
Połączenie modularności z zaangażowaniem klienta w konfigurowanie produktu przyczynia się do poprawy efektywności i skuteczności realizacji masowej kastomizacji. Z jednej strony modularność ogranicza stopień kastomizacji, ale z drugiej strony przyczynia się do zwiększenia powtarzalności produkcji i w ten sposób do poprawy jej efektywności. Produkcja modułów odbywa się wyprzedzająco w stosunku do zamówień klientów, ale jej planowanie bazuje na prognozie zagregowanego popytu, która charakteryzuje się mniejszym ryzykiem: niezgodności z rzeczywistym popytem. W konsekwencji występują mniejsze zapasy w łańcuchu dostaw, zmniejsza się ryzyko nadmiaru lub niedoboru komponentów i wzrasta poziom obsługi.
Systemy operacyjne
Systemy operacyjne masowej kastomizacji powinny łączyć efektywność procesów masowej produkcji z elastycznością procesów indywidualnej kastomizacji. Systemy te muszą być zdolne do przyjmowania zamówień od klientów na skastomizowane produkty i ich szybkiej transformacji w instrukcje sterujące realizacją tych zamówień . Wymaga to zapewnienia współdziałania z klientem w konfigurowaniu produktu i uzyskiwania konkretnych oraz akuratnych informacji. Procedura przyjmowania zamówień powinna w prosty i przyjazny sposób prowadzić klienta przez proces dokładnego specyfikowania jego indywidualnych wymagań odnośnie do produktu. Dla zapewnienia bezpośredniego przepływu informacji od klienta do produkcji i dostawy musi powstać sieć, która umożliwi integrację klienta bądź sprzedawcy z procesami operacyjnymi.
Koncepcja łańcucha dostaw dla masowej kastomizacji w dużym zakresie odpowiada koncepcji łańcucha dostaw Lean-Agile
Systemy masowej kastomizacji muszą także zapewniać odpowiednią elastyczność procesów. W pewnych jednostkach kastomizujących indywidualizacja będzie następować w fazie montażu (kastomizacja standaryzowana), w innych będzie to faza fabrykacji komponentów (kastomizacja na miarę). Systemy CAD/CAM, elastyczne systemy produkcyjne (FMS), maszyny sterowane numerycznie (CNC), uelastyczniły do tego stopnia systemy masowej produkcji, że stała się możliwa zautomatyzowana produkcja skastomizowana realizowana potokowo.
Proces kastomizacji rozpoczyna się od dialogu z klientem. Wykorzystuje się odpowiedni konfiguracyjny software, który może być wdrożony w laptopie sprzedawcy lub na Web stronach firmy. Kiedy konfiguracja zostanie ukończona i klient złoży zamówienie, informacje o zamówieniu zostają przesłane przez modem wejściowy do zakładu produkcyjnego, gdzie wchodzą do bazy danych zamówień. Tam zostają zamienione na pakiety danych, które przepływają odpowiednio do monitorów wyświetlających on-line instrukcje dla montażu.
W przypadku kastomizacji „na miarę” informacja o zamówieniu dociera do parametryzującego stanowiska CAD/CAM, które zamienia dane o zamówieniu w parametryczne rysunki CAD części i zespołów, a następnie tłumaczy te rysunki na programy dla maszyn CNC.
Zasilanie linii
Masowa kastomizacja wymaga także szybkiego uzupełniania komponentów standardowych przez dostawców wewnętrznych i zewnętrznych. Komponenty muszą oczekiwać przy stanowiskach (w fazie montażu lub wytwarzania) na zamówienie klienta i powinny być uzupełniane w tzw. „spontanicznych” łańcuchach dostaw. Stosowane są takie techniki automatycznego uzupełniania komponentów, jak kanban, min-max oraz technika wolnych zapasów (free stock). Kanban może bazować na systemie dwupojemnikowym, gdzie dostawca uzupełnia pusty pojemnik w okresie zużywania komponentów z drugiego pojemnika. W technice min-max po osiągnięciu poziomu minimalnego dostawca uzupełnia zapas do poziomu maksymalnego. Technika wolnych zapasów polega na częstym napełnianiu pojemników przez dostawcę i okresowym rozliczaniu należności.
Odraczanie
Odraczanie (postponement) jest koncepcją polegającą na wstrzymywaniu wykonywania działań związanych z indywidualizacją i finalizacją produktu w łańcuchu dostaw aż do nadejścia zamówień klientów. Punkt w łańcuchu dostaw, do którego dociera zamówienie klienta, nosi nazwę punktu rozdziału zamówienia klienta (CODP – Customer Order Decoupling Point). Punkt rozdziału zamówienia klienta jest także punktem przypisania produktu do określonego klienta i punktem kastomizacji. Odraczanie dąży do przesuwania punktu przypisania produktu określonemu klientowi do końcowych faz łańcucha dostaw. Koncepcja ta jest stosowana dla zredukowania wpływu niepewności popytu klienta i poprawy efektywności przy zachowaniu reaktywności łańcucha dostaw. Efektywność w górnej części łańcucha dostaw jest osiągana dzięki produkcji planowanej w oparciu o prognozy zagregowanego popytu, który wykazuje mniejszą niepewność w porównaniu z popytem zindywidualizowanym. Realizacja tych planów powinna opierać się na ssących systemach sterowania typu Kanban. W efekcie następuje redukcja zapasów oraz kosztów ich utrzymania, redukcja kosztów nadprodukcji, kosztów starzenia ekonomicznego składników przy wysokiej niezawodności dostaw.
Głównym powodem odraczania finalizacji lub kastomizacji produktu jest brak dysponowania informacją o aktualnym zamówieniu klienta w określonej fazie łańcucha dostaw. Efektywne zastosowanie odraczania w wielu przypadkach będzie wymagało zmiany kolejności faz i operacji wytwarzania produktu. Operacje, które wymagają informacji o zamówieniu klienta, powinny zostać przesunięte w dół łańcucha dostaw, a z kolei operacje, które nie wymagają takich informacji lub mogą być wykonane wyprzedzająco, powinny zostać przesunięte w górę łańcucha dostaw.
Połączenie modularności z zaangażowaniem klienta w konfigurowanie produktu przyczynia się do poprawy efektywności i skuteczności realizacji masowej kastomizacji
Przykładem praktycznego zastosowania odraczania jest firma odzieżowa Benetton. W firmie tej dokonano zmiany kolejności operacji w procesie produkcyjnym swetrów. W tradycyjnym systemie najpierw farbowano przędzę, z której tkano swetry o różnych kolorach, co utrudniało szybkie dostosowywanie asortymentu do zmieniającego się popytu. Po zmianie kolejności operacji, która polegała na przesunięciu farbowania do końcowych faz procesu, udało się opóźnić punkt różnicowania produktów i dzięki temu zmniejszono ryzyko wykonania produktów w kolorach, na które nie ma zapotrzebowania.
W strategiach łańcucha dostaw wyróżnia się odraczanie czasowe oraz odraczanie formy. Odraczanie czasowe polega na wstrzymywaniu dostarczania produktów do momentu nadejścia zamówienia klienta. Odraczanie formy polega na przesuwaniu różnicowania i kastomizacji produktów aż do końcowych faz w łańcuchu dostaw.
Łańcuch dostaw a kastomizacja
Koncepcja łańcucha dostaw dla masowej kastomizacji w dużym zakresie odpowiada koncepcji łańcucha dostaw Lean-Agile. Koncepcja ta opiera się na podziale łańcucha dostaw na część Lean i Agile i takim pozycjonowaniu punktu rozdziału, aby łańcuch dostaw zachował zdolność szybkiego i zwinnego reagowania na potrzeby klienta w dole strumienia przy zachowaniu dużej efektywności przepływu na stałym poziomie w górnej części strumienia. W koncepcji Lean-Agile zakłada się, że określony proces w łańcuchu dostaw nie może być jednocześnie efektywny i reaktywny, czyli jednocześnie Lean i Agile. Stąd podział łańcucha dostaw na część o procesach Lean i Agile, przy czym procesy Lean w łańcuchu dostaw muszą poprzedzać zarówno geograficznie, jak i historycznie procesy Agile. Dla stworzenia warunków do zastosowania masowej kastomizacji nieodzowne jest wcześniejsze przekształcenie procesów masowej produkcji w procesy Lean.
Procesy Lean są osiągane poprzez rozwijanie strategii eliminacji strat i ciągłego doskonalenia, zorientowanej na zwiększanie efektywności. Łańcuch dostaw Lean-Agile powstaje na drodze transformacji procesów Lean w dolnej części łańcucha dostaw w reaktywne procesy Agile. Transformacja ta następuje poprzez rozwijanie strategii zorientowanej na zwiększanie reaktywności na skastomizowane zamówienia. Dlatego budowanie łańcucha dostaw masowej kastomizacji będzie wiązało się z pozycjonowaniem punktu CODP, który wyznacza optymalny zakres procesów zorientowanych efektywnościowo i procesów reaktywnych oraz odraczaniem kastomizacji.
Komponenty muszą oczekiwać przy stanowiskach (w fazie montażu lub wytwarzania) na zamówienie klienta i powinny być uzupełniane w tzw. „spontanicznych” łańcuchach dostaw
CODP jest punktem w łańcuchu dostaw, który rozdziela procesy realizowane wyprzedzająco, bez uwzględniania zamówienia klienta finalnego, od procesów przebiegających w reakcji na zamówienia klientów. Punkt ten wyznacza także obszary w łańcuchu dostaw, w których powinny być rozwijane strategie Lean i Agile.
Pozycjonowanie CODP
W warunkach masowej kastomizacji pozycjonowanie CODP będzie się wiązać ze znajdowaniem zrównoważenia między efektywnością (produktywnością) i pożądanym stopniem kastomizacji oraz możliwościami zastosowania masowej kastomizacji. Gdy wymagany jest wysoki stopień kastomizacji, punkt rozdziału będzie przesuwany górę łańcucha dostaw, a ograniczeniem będzie efektywność masowej kastomizacji. Dla zwiększenia efektywności masowej kastomizacji i możliwości konkurowania ceną punkt rozdziału będzie przesuwany w stronę klienta. W implementacji masowej kastomizacji konieczne jest balansowanie korzyści zmian efektywności i stopnia kastomizacji.
Koncepcja odraczania przesuwa punkt rozdziału w dół strumienia, bliżej klienta finalnego. Poprzez odraczanie większa część łańcucha dostaw reprezentuje procesy Lean, co pozwala na utrzymanie wysokiej efektywności (produktywności) w warunkach kastomizacji. Z drugiej strony, dzięki przesunięciu punktu kastomizacji w stronę klienta, czas realizacji zamówienia ulega skróceniu i następuje wzrost reaktywności. Dlatego można stwierdzić, że koncepcja odraczania w połączeniu z modularnością warunkuje masową kastomizację, gdyż zwiększa efektywność i reaktywność w łańcuchu dostaw.