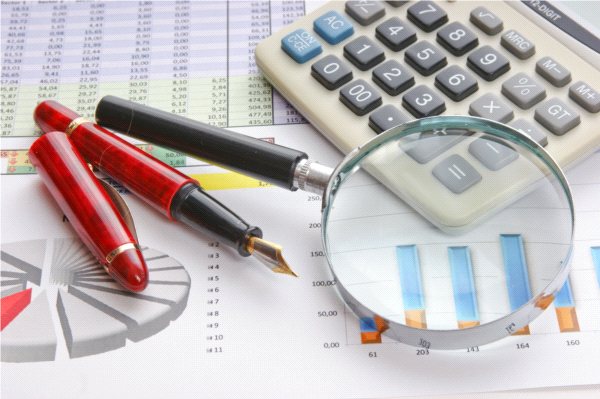
Koncepcja poziomowania produkcji
Heijunka to japoński termin oznaczający poziomowanie i wygładzanie. W kontekście Lean Manufacturing i Toyota Production System (TPS), Heijunka oznacza koncepcję poziomowania produkcji (production leveling) lub wygładzania produkcji (production smoothing) stosowaną w...
Jeffrey K. Liker w swojej świetnej książce „Droga Toyoty” (polskie wyd. przez MT Biznes w 2005) zaliczył Heijunka do 14 podstawowych zasad zarządzania przedsiębiorstwem Lean. Heijunka jest także obok standaryzacji pracy i wizualnego zarządzania fundamentem tzw. „Domu Toyoty”, na którym oparte są jego filary: JIT, Jidoka i Kaizen na których z kolei wspiera się dach domu Toyoty, czyli najwyższa jakość, najniższe koszty, najkrótszy czas realizacji, największe bezpieczeństwo, najwyższe morale dzięki skracaniu strumienia wartości poprzez eliminację strat. Bez Heijunka nie może skutecznie i efektywnie funkcjonować system Kanban, ciągłe doskonalenie – Kaizen, standaryzacja pracy i inne elementy TPS.
Eliminacja 3xM
Implementacja Heijunki umożliwia osiągnięcie stabilności w procesach produkcyjnych poprzez usuniecie Mura (nierównomierność obciążenia ludzi i maszyn) oraz Muri (przeciążenia zasobów produkcyjnych takich, jak ludzie czy maszyny), a także eliminację Muda (straty w procesie produkcyjnym, wykonywanie działań nie związanych z dodawaniem wartości). Działania prowadzące do Muda traktuje się jako straty, gdyż wydłużają czas realizacji, powodują zbędne przemieszczanie materiału, narzędzi i ludzi, wytwarzają nadmierne zapasy i prowadzą do bezproduktywnego oczekiwania ludzi oraz materiału. Eliminacja Muda jest zasadniczym elementem programów wdrażania Lean Manufacturing w przedsiębiorstwach, natomiast stosunkowo mniejszą wagę przywiązuje się do likwidacji Muri oraz Mura. Dzieje się tak ze względu na łatwość, z jaką można zwykle identyfikować straty w procesach i eliminować je. W przedsiębiorstwach tych pojawiają się jednak, prędzej czy później, problemy wynikające z braku stabilności i wypoziomowania produkcji. W zakładach Toyoty, Muda, Muri i Mura mają równorzędne znaczenie, a ich skuteczna i efektywna eliminacja jest traktowana jako wzajemnie zależna. Koncentracja wyłącznie na eliminacji ośmiu rodzajów strat typu Muda, bez angażowania się w likwidację Mura i Muri, może niekiedy prowadzić do obniżenia produktywności ludzi i systemu produkcyjnego. Dlatego eksperci od wdrażania TPS i Lean Manufacturing zalecają skupienie się w pierwszej kolejności na poziomowaniu produkcji, gdyż brak stabilności w procesach prowadzi do na przemian nadmiernego i niedostatecznego obciążania ludzi i maszyn, co z kolei nie sprzyja jakości, standaryzacji pracy, produktywności i ciągłej poprawie.
W typowych systemach produkcyjnych zdarzają się okresy i miejsca, gdy pracy jest więcej niż wynoszą możliwości maszyn i ludzi (Mura); a kiedy indziej pracy brakuje. Nierównomierność pracy wynika z niewypoziomowanych harmonogramów produkcji lub fluktuacji wolumenów produkcji spowodowanych problemami w rodzaju: przestoje maszyn, brak części czy defekty. Fluktuacje produkcji powodują, że zawsze trzeba mieć do dyspozycji tyle wyposażenia, materiałów i ludzi, aby sprostać potrzebom najwyższego możliwego wolumenu produkcji, nawet jeśli przeciętne zapotrzebowanie na nie jest znacznie niższe, a to z kolei prowadzi do strat muda.
Programy redukcji czasu przestawiania się z jednego typu wyrobu muszą poprzedzać implementację poziomowania produkcji
Poziomowanie wolumenu i asortymentu produkcji
Heijunka oznacza poziomowanie produkcji zarówno pod względem wolumenu, jak i mieszanego asortymentu wyrobów. Zakłada się przy tym, że wyrobów nie należy wytwarzać zgodnie z faktycznym napływem zamówień klientów, który może nieprzewidywalnie fluktuować w górę lub w dół, lecz łączny wolumen zamówień w pewnym horyzoncie czasu powinno się równomiernie rozłożyć, tak aby każdego dnia wytwarzać te same wielkości i produkty w jak najmniejszych partiach. Stanowi to częściowe odejście od podstawowej zasady TPS, która mówi, że należy wytwarzać dokładnie to, co i ile potrzebują klienci (zarówno wewnętrzni jak i zewnętrzni). Jednak produkcja zgodnie z rzeczywistą sekwencją zamówień klientów prowadzi do nierównomierności w wytwarzaniu. Jeżeli w poniedziałek zamówień jest więcej niż we wtorek, to w poniedziałek trzeba będzie zapłacić robotnikom za pracę w godzinach nadliczbowych, a we wtorek posłać ich wcześniej do domu. Aby tego uniknąć, ustala się na podstawie rzeczywistych zamówień, wolumen oraz sekwencję typów produktu i tworzy się wypoziomowany harmonogram produkcji.
„Bat na byka”
Fluktuacje w liniach montażu finalnego wyrobu powodują powiększenie strat, czyli muda. Dzieje się tak, ponieważ wyposażenie, pracownicy, zapasy i inne elementy potrzebne w łańcuchu dostaw muszą być ciągle przygotowane na szczytową produkcję. Taka jest cena elastyczności. Jeżeli w finalnym procesie wyrobu zmienia się zapotrzebowanie na zasysane części w zakresie czasu i ilości z procesów w górze strumienia wartości, to zakres tych fluktuacji wzrasta, gdy przesuwają się one w górę łańcucha dostaw. Zjawisko to jest znane jako amplifikacja popytu lub efekt „bata na byka”. Aby zapobiec fluktuacjom w produkcji, także w procesach dostawców zewnętrznych, ważnym jest aby zminimalizować fluktuacje w linii montażu finalnego wyrobu. Linie montażu finalnego w zakładach Toyoty nigdy nie montuje tego samego modelu wyrobu w dużej partii. Zamiast tego poziomują produkcję, poprzez montowanie zestawu kilku modeli w jak najmniejszych partiach.
Kroki w poziomowaniu produkcji na linii montażu finalnego
- Ustalenie popytu i wolumenu produkcji miesięcznej.
- Ustalenie wolumenu produkcji dziennej.
- Obliczenie taktu.
- Wyrównanie produkcji w oparciu o mieszany model produkcji.
- Określenie sekwencji produkcji na kolejny dzień dla linii montażu finalnego.
Model mieszanej produkcji
Zakład Toyoty (przykład zaczerpnięty z materiałów szkoleniowych Toyoty) produkuje trzy modele produktu finalnego (A – samochód pięciodrzwiowy, B – samochód czterodrzwiowy, C – samochód trzydrzwiowy), a miesięczny prognozowany zagregowany popyt kształtuje się na poziomie 10000 szt., w tym udział w sprzedaży modelu A wynosi 50 proc., a modelu B i C po 25 proc., co daje odpowiednio: 5000szt. A, 2500szt. B, 2500szt. C.
Jeżeli zakład kierowałby się jedynie korzyściami skali produkcji oraz minimalizacją kosztów przestawiania produkcji, to plan produkcji byłby następujący: przez dwa tygodnie produkcja modelu A w partii o wolumenie 5000szt., a w kolejnych tygodniach produkcja modeli B i C w partiach po 2500 szt.
Wady niewypoziomowanego harmonogramu produkcji
- Klienci przez cały tydzień kupują różne modele. Jeżeli zamówią na początku miesiąca modele B i C, to oznacza, że muszą czekać dłużej czekać na realizację zamówienia lub firma musi utrzymywać duże zapasy wyrobów gotowych różnych modeli, co prowadzi do zwiększenia kosztów utrzymania zapasów.
- Ryzyko, że nie wszystkie modele zostaną sprzedane. Jeżeli firma nie sprzeda wszystkich modeli A wyprodukowanych w pierwszej połowie miesiąca, to musi składować je w postaci zapasów.
- Niezrównoważone wykorzystanie zasobów. Produkcja różnych modeli wymaga zwykle różnego zapotrzebowania na siłę roboczą w poszczególnych tygodniach. Oznacza to ryzyko zwiększenia Mura i Muda.
- Nierównomierne zapotrzebowanie na półprodukty i części z wcześniejszych procesów. Fluktuacje w produkcji wyrobów finalnych przenoszą się w górę łańcucha dostaw z narastającą amplifikacją i pojawia się efektu „bata na byka”.
Zakład, dążąc do uniknięcia powyższych wad oraz uzyskania korzyści z wygładzania produkcji, stosuje w harmonogramowaniu produkcji linii montażu finalnego tzw. model mieszanej produkcji. Model mieszanej produkcji polega na tym, żeby w każdym okresie czasu, w każdym tygodniu, a następnie w każdym dniu, zmianie roboczej oraz godzinie produkować wszystkie modele produktów, w wolumenie i proporcjach odpowiadających przewidywanemu zapotrzebowaniu. W rozpatrywanym zakładzie każdego dnia będzie produkowane 500szt. (przy założeniu 20 dni roboczych w miesiącu) w tym: 250 szt. A, 125 szt. B i 125 szt. C. Wtedy czas taktu wyniesie 8×60/500 = 0,94 min (przy założeniu pracy na jedną zmianę), czyli co jedną minutę powinien spływać jeden samochód z linii. Harmonogram montażu finalnego ułożony poprzedniego dnia przez planistę będzie prezentował się następująco: AABCAABCAABCAABCAABC…
W ten sposób osiągnięto wyrównanie produkcji zarówno ze względu na wolumen, jak i asortyment. W takiej właśnie sekwencji planista każdego dnia układa karty Kanban w skrzynce Heijunka na dzień następny.
Planowanie produkcji w oparciu o model mieszanej produkcji pozwala na szybkie przestawianie się na inne wielkości (z dnia na dzień), gdy zmienia się popyt na poszczególne modele. Załóżmy, że popyt na model A zmalał dwukrotnie, a na model B wzrósł dwukrotnie, wtedy sekwencja wyrobów na następny dzień, będzie wyglądała następująco: ABBCABBCABBCABBC…
Korzyści z zastosowania poziomowania produkcji w oparciu o model mieszanej produkcji
- Elastyczność w wytwarzaniu tego, co potrzebuje klient w wymaganym przez niego czasie. Oznacza to zmniejszenie zapasów w zakładzie i związanych z nimi problemów.
- Zmniejszenie ryzyka, że nie wszystkie produkty zostaną sprzedane. Gdy zakład produkuje tylko to co zamawiają klienci nie trzeba się martwić o koszty utrzymywania i magazynowania zapasów wyrobów.
- Zrównoważenie wykorzystania pracowników i maszyn. W zakładzie można opracowywać standardowe zadania i wyrównywać produkcję z uwzględnieniem faktu, że niektóre modele wymagają więcej, a inne mniej pracy. Uwzględnienie tych różnic zapewnia zrównoważone i łatwe do zarządzania obciążenie w ciągu całego dnia pracy.
- Wyrównanie zapotrzebowania na wyroby z wcześniejszych procesów i na te wytwarzane przez dostawców. Jeżeli zakład obciąża wcześniejsze procesy produkcyjne zgodnie z zasadą dostaw just in time, a dostawcy wielokrotnie w ciągu dnia przywożą swoje produkty, to również mogą wytwarzać je według stabilnych i wyrównanych zamówień. Pozwala to im zmniejszyć stan zapasów w łańcuchu dostaw i w ten sposób obniżyć koszty– tak więc wyrównywanie produkcji jest korzystne dla wszystkich uczestników łańcucha dostaw.
Poziomowanie produkcji zarówno ze względu na wolumen, jak i asortyment produkcji, staje się możliwe dopiero wtedy, gdy nastąpi drastyczne zredukowanie czasu przestawiania produkcji. To właśnie programy redukcji czasu przestawiania się z jednego typu wyrobu muszą poprzedzać implementację poziomowania produkcji.
Pożądane niewielkie zapasy
Wyrównywanie harmonogramów montażu wyrobów finalnych ma korzystny wpływ na cały łańcuch wartości; stwarza możliwość dokładnego planowania każdego szczegółu produkcji oraz standaryzowania pracy. Dostawcy producenta wyrobów finalnych klasy Lean oczekują, że składane zamówienia na części również będą wygładzone i nie utrzymują zapasów swoich wyrobów gotowych. Wiąże się to z pewnym ryzykiem, bo bez zapasów wyrobów gotowych, każde odchylenie wielkości czy kompozycji zamówień może prowadzić do takich konsekwencji, jak nadgodziny, czy kosztowne ekspresowe dostawy. Dostawcy wiarygodnych producentów Lean jednak rzadko doświadczają takich problemów, ponieważ ci konsekwentnie wyrównują swoje harmonogramy produkcji i produkują to, co zapowiadają dostawcom. Gdy dostawcy obsługują odbiorców, których popyt ulega znacznym wahaniom, eksperci od wdrażania Lean zalecają wprowadzenie przynajmniej niewielkich zapasów wyrobów gotowych. Teoretycznie firma ściśle przestrzegająca zasad Lean powinna wytwarzać i wysyłać zgodnie z potrzebami klienta, bez utrzymywania zapasów wyrobów gotowych. Jednak aby uzyskać korzyści poziomowania produkcji, niewielki zapas wyrobów gotowych jest często niezbędny dla ochrony harmonogramu produkcji przed nieoczekiwanymi skokami popytu i utrzymania wygładzonej produkcji i uniknięcia Mura, Muri i Muda w całym procesie i łańcuchu dostaw. Przykładowo, jeżeli zagregowany popyt dla rodziny produktów zmienia się w okresie tygodnia od 900 do 1100, to dla utrzymania wyrównanego harmonogramu produkcji uzasadnionym będzie utworzenie na początku tygodnia zapasu o wielkości 100 szt., żeby na koniec tygodnia posiadać zapas wysyłkowy na poziomie 1100, który znowu w kolejnym tygodniu będzie wynosił 100 szt. (Przy założeniu stabilnej produkcji na poziomie 1000 i wysyłce tej wielkości w końcu tygodnia). Utrzymywanie tego stosunkowo niewielkiego zapasu umożliwia jednoczesne zachowanie wygładzonej produkcji i zaspokojenie potrzeb klientów w warunkach fluktuacji popytu.
Droga do sukcesu
Wdrażanie systemu produkcji Toyoty (TPS) i Lean Manufacuring należy rozpocząć od wygładzania produkcji Heijunka, gdyż warunkuje ono osiąganie korzyści Lean Manufacturing. Eliminacja Muda to tylko jedna trzecia przedsięwzięć, które trzeba zrealizować aby osiągnąć te korzyści. Równie ważne jest usuwanie Mura i Muri, a to właśnie zapewnia wyrównywanie wolumenu i asortymentu produkcji oraz ujednolicone obciążenia nakładane na pracowników, wyposażenie i dostawców. Wprowadzając zasadę wyrównywania produkcji Heijunka, tworzy się nowe środowisko dla pracowników, którzy nie są przeciążani, dla klientów, którzy dostają lepsze produkty w przyrzeczonych terminach, a także dla producentów, którzy oszczędzają pieniądze, kiedy Muda, Mura i Muri są usuwane z procesów.