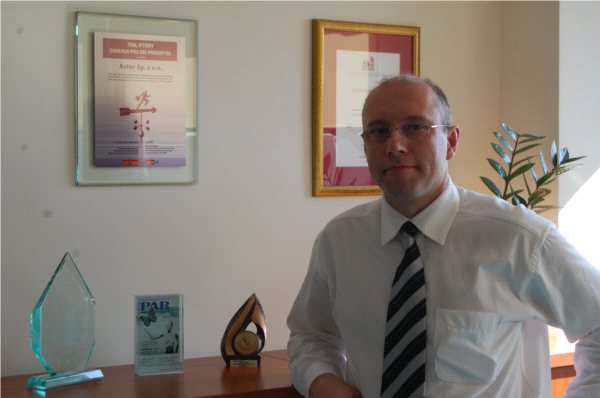
Polskie fabryki przyszłości
Z Stefanem Życzkowskim, prezesem Astor Sp. z o.o., rozmawia Przemysław Ozga.Jak wygląda kondycja polskich zakładów produkcyjnych jeśli chodzi o automatykę i robotykę?
Polska jest bardzo słabo zrobotyzowana, jesteśmy w przysłowiowym „ogonie”. W Polsce,...
Jak wygląda kondycja polskich zakładów produkcyjnych jeśli chodzi o automatykę i robotykę?
Polska jest bardzo słabo zrobotyzowana, jesteśmy w przysłowiowym „ogonie”. W Polsce, która ma aspiracje stania się tygrysem Europy, montuje się 300-400 robotów na wolnym rynku, czyli poza rynkiem Automotive, podczas gdy w czterdziestomilionowej Korei Płd., która jest tygrysem azjatyckim, montowanych jest 2 500 robotów, czyli rocznie prawie 10 razy więcej. Ta sytuacja sprawia, że koreańskie produkty są tańsze, nie tracąc jednocześnie na jakości.
Efektywność produkcji w polskich fabrykach jest dużo niższa niż ma to miejsce w podobnych zakładach zlokalizowanych w państwach zachodnich czy wschodniej Azji. Stąd misja, jaką postawiła sobie firma Astor – zwiększania efektywności wytwórczych polskich przedsiębiorstw. Robimy wiele, aby fabryki funkcjonujące w Polsce, nierzadko dzięki zagranicznemu kapitałowi, zostały w naszym kraju na dłużej. Firma Astor podejmuje starania, aby Polska nie stała się chwilowym miejscem funkcjonowania fabryk na drodze do Ukrainy czy Rosji.
Firmy dostarczające roboty oraz systemy wsparcia produkcji mają w Polsce wiele do zrobienia, zwłaszcza jeśli chodzi o świadomość osób zarządzających fabrykami i procesami w nich zachodzącymi. Menadżerowie z państw zachodnich oraz Azji wykazują znaczną otwartość na zmiany i uwagi co do funkcjonowania ich zakładów produkcyjnych i całych firm. Natomiast w polskich firmach dominuje przeświadczenie, że fabryka funkcjonuje perfekcyjnie i już nic nie da się w niej udoskonalić. Taka postawa blokuje rozwój, który jest niezbędnym składnikiem konkurencyjności. Poza potrzebą większej otwartości, istnieją również takie wskaźniki jak PKB, które jasno pokazują, że Polska ma jeszcze wiele do zrobienia, przed polską produkcją nadal dużo pracy, aby próbować zmniejszyć dystans dzielący nas do Niemiec czy Europy Zachodniej, a przynajmniej nie dać mu dalej rosnąć.
Jak bardzo realne są plany zrobienia z Polski tygrysa Europy przy takiej ilości wdrożeń?
Istnieje tzw. „japoński dylemat” wywodzący się z rywalizacji na linii Japonia-Chiny, gdzie panują warunki bardzo ostrej konkurencji, zresztą charakterystycznej dla kultur azjatyckich. Japończycy, mając do dyspozycji mało surowców oraz ograniczone tereny pod eksploatację, muszą konkurować z większymi i liczniejszymi Chinami. Firmy japońskie, które są dla mnie pewnym wzorcem, postawiły w tej konkurencji na automatyzację procesów produkcyjnych i technologie. Dzięki temu są w stanie konkurować z chińskimi firmami, mimo dużo wyższych kosztów pracy. Ponieważ sprowadzamy technologie głównie z trzech państw: Japonii, USA oraz Finlandii – mamy stały kontakt z japońskimi firmami, dzięki czemu obserwujemy wzorce, które mają nam pomóc w naszej misji – zagwarantowania dla polskiego przemysłu topowych rozwiązań technologicznych, aby polskie fabryki były konkurencyjne na skalę Europy a nawet świata. Nie chcemy bowiem, aby fabryki działające w Polsce zostały w przyszłości przeniesione na Wschód.
Jak duży wpływ na inwestycje w robotykę i automatyzację ma niski koszt pracy w Polsce?
Był to jeden z głównych powodów, dla którego w Polsce pojawiło się i funkcjonuje wiele fabryk opartych na zagranicznym kapitale. Gdy zaczynałem pracę na początku lat 90-ych średnia płaca krajowa oscylowała na poziomie 20 dolarów, teraz jest to tysiąc dolarów – w ciągu dwóch dekad wolnego rynku w Polsce nastąpił pięćdziesięciokrotny wzrost płac. Obecnie dynamika przyrostu jest naturalnie wolniejsza niż 20 lat temu, a koszt pracowniczy w niektórych regionach kraju jest nadal niewysoki dla inwestora. Mimo niskich koszów pracy i zmniejszonej dynamiki wzrostu, obecnie jest nam znacznie łatwiej wprowadzać systemy automatyki i rozmawiać o redukcji kosztów, niż było to w przeszłości.
Polskie firmy produkcyjne wychodzą nierzadko z założenia, że robot wiąże się z redukcją personelu…
To prawda. Pierwszą najczęstszą reakcją menedżerów lub samych pracowników jest obawa, że robot to konkurent człowieka, czyli narzędzie, które go zastąpi. Robot jednak nie jest konkurentem dobrego pracownika. Co więcej konkretne przykłady naszych klientów, którzy zainwestowali w robotyzację, pozwalają patrzeć na roboty jako na „kolegów” z pracy. Roboty w połączeniu z efektywnymi i świadomymi pracownikami pozwalają firmom na znaczące zwiększenie swojej elastyczności i konkurencyjności na rynku. A za większą konkurencyjnością idzie ich rozwój.
Czyli roboty są formą wsparcia a nie wyłącznie alternatywą dla dobrego, ale też drogiego pracownika?
Skuteczne zarządzanie firmą oraz inwestycje w robotyzację, automatykę, często idą w parze. Współpracujemy w tej chwili z firmą produkcyjną, która przed zainstalowaniem ośmiu robotów zatrudniała 3000 pracowników. Praca robotów na najważniejszych węzłach przyniosła wzrost efektywności poprzez zrytmizowanie pracy, obniżenie kosztów, poprawę pozycji ekonomicznej przedsiębiorstwa, czego efektem jest to, że firma zatrudnia w tej chwili 3 300 osób, czyli 10 procent więcej, niż przed instalacją robotów.
Jakie branże będą w najbliższym czasie inwestować w robotykę?
Zdecydowanie dominującą w tej sferze pozostaje branża Automotive, gdzie w przybliżeniu sprzedaje się 90 proc. robotów i systemów automatyki. Mówiąc o innych branżach, rozmawiamy o pozostałych 10-u procentach rynku. Ta dysproporcja wynika głównie z pieniędzy jakimi dysponuje branża motoryzacyjna. Mnożąc cenę samochodu przez ilość wyprodukowanych sztuk, łatwo sobie wyobrazić potencjał inwestycyjny jaki drzemie w branży Automotive. Stąd fabryka samochodowa dysponuje o wiele większymi możliwościami finansowymi niż np. fabryka pralek. Kolejną sprawą jest duża ilość procesów na linii produkcyjnej do zrobotyzowania, ponieważ samochód jest bardzo skomplikowanym produktem z dużą ilością ciężkich części.
Obecnie w automatykę mocno inwestuje branża budowlana, gdzie roboty wykorzystywane są do paletyzacji ciężkich produktów, takich jak kostka brukowa czy worki z cementem lub klejami, itd. Moda na instalacje robotów trwa również w branży mleczarskiej, co wcześniej było trudne do przewidzenia.
Czy automatyka jest warunkiem przetrwania firmy na rynku? Jak będą wyglądały fabryki przyszłości?
Bez automatyki konkurencja jest utrudniona. Podam przykład. Klawiatura do komputera (102 klawisze) może kosztować 19 złotych za sztukę – w tym jest cena materiałów, cło, VAT, transport, itd. Taka sytuacja jest możliwa dzięki całkowitej automatyzacji procesów wytwarzania, gdzie gotowa klawiatura produkowana jest zapewne co sekundę. Produkcja ręczna podniosłaby cenę do 100-u złotych, więc produkt automatycznie przestałby być konkurencyjny. Dlatego firmom, które nie są zautomatyzowane chociażby w minimalnym stopniu, niezwykle trudno jest przetrwać na rynku, wiele mikro-firm ma w związku z tym ogromne kłopoty. Nad tymi firmami z ręczną produkcją plasują się przedsiębiorstwa z częściowo zautomatyzowanymi procesami. Następnie działają organizacje w pełni zautomatyzowane, dodatkowo połączone z softwarem MES (ang. Manufacturing Execution System), aby monitorować jakość produkcji. Na samym szczycie są przedsiębiorstwa z fabrykami niezwykle rzadko spotykanymi w Polsce, gdzie MES ma przełożenie na działania Human Resources i programy motywacyjne dla załogi. Polska fabryka wyposażona w systemy zautomatyzowane, MES, w której liczy się efektywność, procesy są opomiarowane, a na końcu korzystne wyniki dzieli się z załogą, jest dla mnie wizją zakładu przyszłości w Polsce. Fabryki odnoszące na Zachodzie największe sukcesy, mają te systemy bardzo dojrzałe – to ich przewaga i powód istniejącej między nami przepaści.
Jaką rolę odgrywają systemy IT, np. MES, jeśli chodzi o negocjację pomiędzy potencjalnym dostawcą a producentem? Jak przekonać firmę do wdrożenia MES?
W wielu fabrykach, które mamy okazję oglądać systemy softwareowe wyglądają za każdym razem inaczej, ale nazywane są wspólną nazwą MES. Ale MES to system, który pozwala wyliczać przestoje, mikroprzestoje, nieefektywności, braki, zarządzać efektywnością produktu, całe OEE (przyp. red. Overall Equipment Effectiveness). Firmy bardziej zaawansowane mają oczywiście te systemy, ale w niejednym zakładzie masa danych pozostaje na kartkach papieru. W efekcie raporty generowane a następnie przedstawiane osobom decyzyjnym niemal zawsze pozwalają osiągnąć zakładany przez „górę” OEE, czy inne wskaźniki, tak, żeby wszyscy byli zadowoleni – jest to częsta praktyka, ponieważ przysłowiowy papier przyjmie wszystko.
Jak ważny w negocjacjach nad wdrożeniami rozwiązań automatycznych jest czynnik ceny?
W Polsce trwa kryzys rynkowy wynikający z pewnej mentalności polskich producentów. Niewielka liczba producentów inwestuje w robotykę, dodatkowo istnieje nadpodaż nie tylko samych robotów, ale również integratorów. Bardzo wielu tych ostatnich staje do przetargów o projekty, podczas gdy, niestety, niejednemu brakuje kompetencji, gdyż nie posiadają doświadczenia realnych wdrożeń. W związku z tym bardzo wiele aplikacji finalnie nie spełnia oczekiwań klienta. To wszystko wynika z tego mentalnego przekonania, o którym wspomniałem na początku, że w przetargach liczy się tylko cena. Z drugiej strony pokusa dla integratora by wygrać dzięki tańszej ofercie, jest naprawdę duża. Niestety, przeważnie kończy się to nieudanymi wdrożeniami i co gorsze, skutkuje tym, że wiele firm zniechęca się do jakichkolwiek inwestycji w automatykę. Na rynku robotyki, ciągle jest za mało sukcesów, które dobrze by świadczyły o robotyzacji i korzyściach z niej płynących. Nie mniej jednak jestem optymistą, wcześniej czy później to się zmieni. Nieustannie nad tym pracujemy. Efekty można zobaczyć na naszej stronie internetowej, na której klienci chwalą się swoimi sukcesami związanymi z robotyzacją, np.: Fabryka Farb i Lakierów Śnieżka lub Okręgowa Spółdzielnia Mleczarska Mońki.