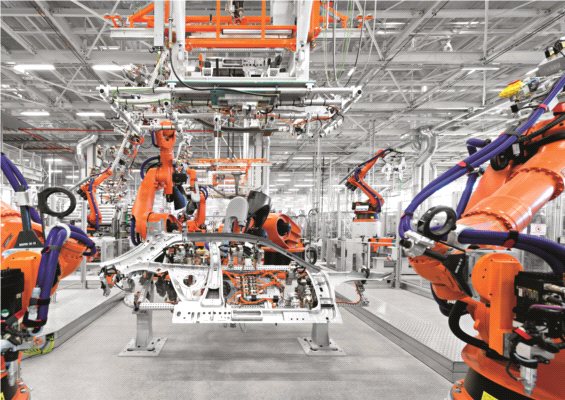
Produkcja na zielono
W największej w Europie hali produkcyjnej N60 w ciągu 460 minut z 288 części powstaje nadwozie Audi A3. Najnowocześniejsza technologia i innowacyjne metody nie tylko przekładają się na wysoki poziom jakości, ale i przyczyniają się w znacznym stopniu do zrównoważonej produkcji...
W fabryce w Ingolstadt wytwarza się modele Audi A3, A4, A5 i Q5 oraz wykonuje końcowy montaż Audi TT. Wymienione auta przechodzą pełny cykl produkcyjny, od surowego materiału do gotowego pojazdu. W początkowym etapie produkcji elementy ze stali i aluminium formuje się w prasowni. Ukształtowane gotowe blachy są wykorzystywane do montażu karoserii (w hali N60 w przypadku Audi A3), zanim zostanie ona przetransportowana do lakierni. Zanim nadwozie powędruje do dalszej obróbki w lakierni, roboty przemysłowe wykonują w nim 4,8 tys. zgrzein punktowych. Polakierowana karoseria wędruje następnie do hali montażowej, gdzie umieszcza się w niej dalsze komponenty, takie jak silnik, reflektory, siedzenia itp. Ostatnim elementem jest szczegółowa kontrola jakości. Dzięki precyzyjnym robotom nowej generacji oraz szeroko zakrojonej kontroli jakości z wykorzystaniem techniki laserowej już na wstępnym etapie produkcji redukuje się do minimum błędy i koryguje wymiary szczelin.
Ergonomiczna infrastruktura
Efektywność procesu produkcji jest konsekwencją nie tylko samego wyposażenia hali N60, ale i lokalizacji sąsiadujących z nią budynków. W północnej części jest to licząca 4,3 tys. mkw. sekcja logistyki. Stamtąd elementy konstrukcji auta elektrycznymi meleksami są dostarczane do gmachu głównego. Również dwa dalsze budynki, w których znajdują się biura, pomieszczenia socjalne i przebieralnie, zostały dogodnie usytuowane pomiędzy bramą fabryki a halą montażową. Wewnątrz tej ostatniej ruch odbywa się na rowerach. „Zaplanowaliśmy obiekty tak, aby odcinki do pokonania były jak najkrótsze zarówno dla ludzi, jak i dla części. W ten sposób pracownicy oszczędzają czas i energię” – wyjaśnia Rainer Weiß, kierownik odpowiedzialny za projekty nadwozia w Audi.
Oszczędność energii
W hali produkcyjnej N60 Audi na powierzchni 50 tys. mkw. podłogę codziennie czyści bez użycia środków drażniących i substancji chemicznych nowoczesny system wyposażony w szczotki z włosiem kokosowym. Jak widać nawet sprzątanie zasługuje tu na opinię: „w wysokim stopniu ekologiczne”. To tylko jeden szczegół w kompleksowym procesie produkcyjnym nadwozia modelu A3. „Na etapie planowania budowy, tworzenia koncepcji procesów i ustalania przebiegu dnia roboczego problem zrównoważonej produkcji zyskał wysoki priorytet” – wyjaśnia Sabine Mayer, która oprowadza grupy zwiedzających po hali, gdzie 800 ludzi i taka sama liczba robotów spawa, skręca, nituje i skleja w jedną karoserię 288 pojedynczych elementów ze stali i aluminium.
Zanim nadwozie powędruje do dalszej obróbki w lakierni, roboty przemysłowe wykonują w nim 4,8 tys. zgrzein punktowych
Montaż nadwozia pochłania 14 proc. całkowitej energii procesu produkcyjnego i jest po lakierowaniu drugim w kolejności pożeraczem energii. Ma jednak duży potencjał oszczędności. „Już samo zastosowanie robotów nowej generacji odgrywa w tej materii znaczącą rolę. Pracują one precyzyjnie, a w stanie bezczynności przechodzą w tryb energooszczędny (stand-by). Każde podwyższenie poziomu zużycia i każda nieszczelność w przewodach ciśnieniowych są natychmiast automatycznie sygnalizowane przez wskaźnik poboru energii. Wskutek takich usterek wcześniej odnotowywano duże straty” – wyjaśnia Mayer.
Inteligentne oświetlenie
W hali N60 oszczędza się aktywnie. I jak w każdym gospodarstwie domowym, proces ten zaczyna się od oświetlenia. Przez przeszkloną powierzchnię 2 tys. mkw. od strony północnej przenika do wnętrza światło dzienne, jednak aby linia produkcyjna była w równym stopniu widoczna, na suficie zamontowano 3 tys. ultraoszczędnych żarówek. Przy dużym nasłonecznieniu czujniki automatycznie zmniejszają natężenie promieniowania. Z kolei w pochmurne zimowe dni lampy kompensują niedobór światła dziennego. Jednak – inaczej niż w domu – nie trzeba tu biegać za wszystkimi, przypominając o gaszeniu żarówek. Czujniki ruchu wyłączają oświetlenie w miejscach, w których w danej chwili nie wykonuje się żadnej pracy, „pracy człowieka – doprecyzowuje Sabine Mayer – bo roboty nie potrzebują światła”.
800 ludzi i taka sama liczba robotów spawa, skręca, nituje i skleja w jedną karoserię 288 pojedynczych elementów ze stali i aluminium
Kontrola dopływu prądu
Odcięcie źródła elektryczności jest najprostszą i najbardziej skuteczną formą oszczędzania energii. Również tu nasuwa się paralela z gospodarstwem domowym – wiele urządzeń w trybie stand-by to prawdziwi pożeracze prądu. Urządzenia do produkcji nadwozi wykazują jednak nieporównywalnie wyższe zużycie energii niż telewizor czy odtwarzacz DVD. Do tej pory tylko podczas weekendów pobierały one w trybie stand-by 1300 MWh rocznie, czyli 325 razy więcej, niż zużywa w takim samym okresie czteroosobowa rodzina. W hali N60 dzięki nowoczesnej koncepcji wyłączania źródła energii, wszystkie urządzenia – poza kilkoma strategicznymi komputerami sterującymi – można całkowicie odciąć od prądu, co pozwala na oszczędność rzędu 80 proc.
Energia solarna
Jeszcze bardziej ekologicznym rozwiązaniem jest własna produkcja elektryczności. Zainstalowane na mającym 7,5 tys. mkw. powierzchni dachu hali kolektory słoneczne wytwarzają rocznie 460 Mwh energii. „Możemy ją praktycznie bez strat wykorzystać w procesie produkcyjnym” – mówi Roland Fürholzer, odpowiedzialny w Audi za technikę energetyczną budynków. Prąd ten wystarczyłby do zasilenia 140 domów jednorodzinnych przez okrągły rok. Kolektory pozwalają uniknąć emisji do atmosfery 250 t CO2, które pochodziłyby z pracy elektrowni.
Hamujesz – produkujesz
Oprócz wymienionych metod oszczędzania energii, które w mniejszym stopniu, choć w podobnej formie, znalazłyby zastosowanie w każdym domu jednorodzinnym, ogromny potencjał wydajności mają specjalne technologie montażu nadwozia. Podczas transportu nadwozi odzyskuje się energię hamowania przenośników taśmowych. Zjawisko to kierowcy Audi dobrze znają pod nazwą rekuperacji. Odzyskane zasoby są zwracane do systemów transportujących. W ten sposób można zaoszczędzić 86 MWh prądu, co odpowiada rocznemu zapotrzebowaniu na energię elektryczną 25 domów jednorodzinnych.
Dzięki precyzyjnym robotom nowej generacji oraz szeroko zakrojonej kontroli jakości z wykorzystaniem techniki laserowej już na wstępnym etapie produkcji redukuje się do minimum błędy i koryguje wymiary szczelin
Nowatorskie technologie
Do kluczowych rozwiązań koncernu należy również zastosowanie lekkich materiałów, np. kompozytów z włókna węglowego, znanych pod nazwą Audi ultra. Redukcja masy robotów produkcyjnych to kolejny krok na drodze do zwiększenia efektywności. „Przeprowadziliśmy zakrojone na szeroką skalę badania, aby bliżej poznać wpływ obciążenia granicznego, rozmiarów, masy i prędkości na zużycie prądu przez robota” – wyjaśnia Rainer Weiß. Wyniki badań pozwoliły zredukować masę wysięgnika naprowadzającego i łączącego dach z karoserią o 76 proc. ( 345 kg zamiast 1450 kg). Dach można teraz montować znacznie szybciej i przy mniejszym zużyciu energii niż w przypadku wariantu z konstrukcja stalową.
Można by jeszcze długo wyliczać przykłady zastosowania nowatorskich technologii w hali produkcyjnej N60, bardziej efektywne lasery tarczowe i diodowe w miejsce powszechnie stosowanych laserów krystalicznych, szybsze i niewymagające zbytniej konserwacji elektromotoryczne pistolety do zgrzewania zamiast modeli pneumatycznych chłodzone wodą z miejskich wodociągów to tylko niektóre nowe ekologiczne rozwiązania. „Już sam pomysł wykorzystania wody przemysłowej pozwala na wyeliminowanie emisji 760 t CO2 rocznie. Aby wyemitować taką ilość gazu, Audi A4 2.0 TDI musiałoby pokonać dystans ponad 5,6 mln km” – wylicza Roland Fürholzer.