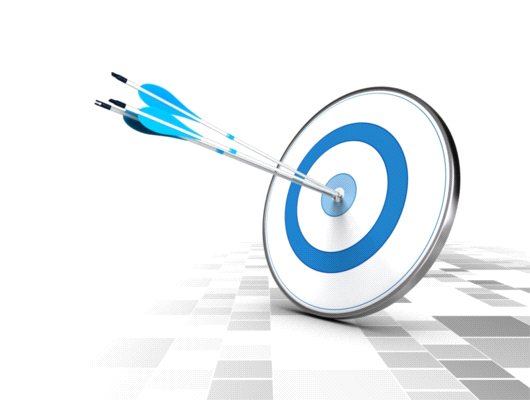
Przewaga dzięki APS
Rozmowa z panem Sebastianem Zbierskim, kierownikiem wydziału systemów ERP w firmie TRAX S.A., na temat metod usprawnienia planowania produkcji.Z jakimi problemami podczas swojej pracy najczęściej spotykają się planiści?
Największym problemem pracowników...
Z jakimi problemami podczas swojej pracy najczęściej spotykają się planiści?
Największym problemem pracowników zajmujących się planowaniem produkcji jest brak informacji, a także to, że informacje, którymi dysponują, są niepełne. Planiści nie są w stanie optymalnie zaplanować procesów produkcyjnych, gdy nie mają dostępu do aktualnych danych na temat wykorzystywanych w produkcji zasobów i materiałów. Na jakość planu produkcyjnego wpływa również brak informacji z produkcji w toku np. ile sztuk i w jakim czasie zostało wyprodukowanych, czy są jakieś braki, czy nie ma przestoju danej maszyny. Brak informacji jest głównym powodem utrudniającym realizację najważniejszego celu każdego zakładu produkcyjnego: terminowego wyprodukowania wyrobu gotowego.
Konsekwencją braku informacji jest również to, że firmy nie wywiązują się z terminowości zleceń. Jakie są inne przyczyny tego, że firmy nie nadążają z produkcją?
Powodem takiego stanu rzeczy jest to, że firmy produkcyjne nie znają lub po prostu ignorują swoje zdolności produkcyjne i biorą na siebie więcej zleceń, niż faktycznie mogą wykonać. Powodem może być również źle zoptymalizowana produkcja, a także brak narzędzi, które wspomagałyby realizację procesu produkcyjnego.
Co zrobić, aby poprawić przepływ kluczowych informacji w przedsiębiorstwie?
Na pewno rozwiązaniem byłoby wprowadzenie odpowiedniego narzędzia, które wsparłoby realizację procesu produkcyjnego i umożliwiłoby sprawny przepływ informacji pomiędzy pracownikami pionu produkcyjnego a pozostałymi pracownikami. Takim narzędziem bez wątpienia jest system klasy APS. System takiej klasy daje obraz zdolności produkcyjnych przedsiębiorstwa i pomaga tak zaplanować produkcję, aby kolejne zlecenia produkcyjne nie kolidowały ze sobą i jednocześnie umożliwiły maksymalne wykorzystanie wszystkich dostępnych zasobów. Pozwala również wprowadzać zamówienia o wysokim priorytecie w przypadku nagłych zamówień.
Jeżeli firma stosuje już system klasy ERP, to po co jej dodatkowe planowanie? Jaka jest w takim razie różnica pomiędzy ERP a APS?
Różnicę tę najłatwiej opisać przyglądając się konkretnym rozwiązaniom. Weźmy na przykład system Infor CloudSuite APS. Jego rozbudowane funkcje umożliwiają zaawansowane planowanie oraz harmonogramowanie, co objawia się realnym określeniem planowanej daty dostawy produktu, skalkulowanej przez system z uwzględnieniem rzeczywistego stanu z hali produkcyjnej. Infor CloudSuite APS, w jednym kroku, tworzy zintegrowany plan produkcji i zakupów w oparciu o marszrutę technologiczną, listę materiałową i inne krytyczne ograniczenia zakładu produkcyjnego, takie jak materiały, maszyny (remonty, awarie i przestoje), operatorzy, itd. Ponadto system, wykorzystując algorytm APS, wspomaga planistę w planowaniu i realizacji nagłych zamówień (ad hoc). Już w chwili rejestracji nagłego zamówienia jesteśmy w stanie sprawdzić możliwość realizacji pod datę żądaną przez klienta. System w przypadku braku możliwość realizacji takiego zamówienia wskazuje przyczyny (braki materiałów, braki mocy produkcyjnych, itd.).
System Infor CloudSuite APS wspiera różne typy produkcji, m.in. produkcję pod zamówienie, produkcję konfigurowalną, produkcję pod projekt, produkcję na magazyn, a także wspiera metody KANBAN/JIT. System ponadto pozwala na łączenie powyższych typów produkcji (tzw. produkcja hybrydowa), tak aby maksymalnie dopasować się do specyfiki zakładu produkcyjnego. Kluczowym elementem systemu Infor CloudSuite APS jest możliwość tworzenia scenariuszy „co jeśli”, które m.in. pozwalają planistom na sprawne wypracowanie wyjścia z trudnych sytuacji, sprawdzenie konsekwencji przyjęcia nagłego zamówienia lub sprawdzenie konsekwencji wyłączenia maszyny (np. w celu konserwacji bądź kalibracji).
Nagłe zamówienie i co dalej? W jaki sposób można szybko zmodyfikować plan produkcji?
W przypadku nagłego zamówienia system klasy APS umożliwia po wprowadzeniu zamówienia do systemu sprawdzenie, na kiedy można je zrealizować. Planując datę wykonania zamówienia uwzględnia wszystkie inne zamówienia, zlecenia produkcyjne, materiały znajdujące się na magazynie, a także dostępność maszyn i pracowników. System klasy APS umieszcza wprowadzone zlecenie w miejscu, w którym będą dostępne zasoby. Wykorzystuje materiały potrzebne do realizacji danego zamówienia, a w przypadku ich braku generuje propozycję zamówienia potrzebnego materiału – wystarczy ją potwierdzić, aby w systemie zostało założone właściwe zamówienie zakupu. Gdy zamówienie jest niespodziewane i „na wczoraj”, system klasy APS umożliwia nadanie mu priorytetu i wykonania go szybciej niż pozostałe zamówienia o niższym priorytecie. Po wprowadzaniu takiego priorytetowego zamówienia system pozwala uzyskać wgląd na wpływ lub zmianę zamówień w całym harmonogramie, aby zachować potrzebne informacje.
Dlaczego podczas wykorzystywania systemu klasy APS tak ważna jest technologia?
Klienci, którzy decydują się na wdrożenie systemu APS, muszą być świadomi, iż bez kompletnych danych dotyczących technologii wykonywania produktów (operacji, materiałów, wykorzystanych zasobów, czasów technologicznych i innych elementów) stworzony plan produkcji, planowane daty wykonania produktów czy daty dostaw będą przekłamane. Może się okazać, że system na podstawie niedokładnie zdefiniowanych technologii nieprawidłowo wyliczy czas wykonania zlecenia, co może skutkować niezadowoleniem klienta.
Jakie są realne korzyści z planowania produkcji?
Korzyści z planowania, poza oczywistą – realizacją zamówień klienta na czas – jest wiele. Przede wszystkim maksymalizacja wykorzystania zasobów, minimalizacja zapasów tj. obniżenie stanów magazynowych do bezpiecznego poziomu, minimalizacja czasów przezbrojeń, optymalizacja produkcji, a przede wszystkim redukcja kosztów i maksymalizacja zysków.
Podsumujmy zatem korzyści ze stosowania systemu APS.
Wdrożenie systemu APS pozwala firmie produkcyjnej na generowanie przejrzystego, jednolitego planu z uwzględnieniem szczegółowych informacji o zapasach magazynowych, produkcji w toku, zamówieniach zakupu w drodze oraz zasobach produkcyjnych (maszynach, operatorach, itp.). Planiści mają możliwość szybkiego sprawdzenia możliwości realizacji zamówień klienta, zleceń produkcyjnych, prognoz z uwzględnieniem zdefiniowanych ograniczeń materiałowych i zasobów produkcyjnych (z ang. ATP – Available To Promise oraz CTP – Capable To Promise). Istotną zaletą jest również możliwość niezależnego nadawania priorytetów dla zamówień klienta oraz zleceń produkcyjnych, uwzględnienie wyjątków dla zasobów (awarie, nadgodziny) i dni wolnych od pracy, a także możliwość uwzględniania alternatywnych materiałów, półproduktów i zasobów w procesie planowania. Planiści docenią także łatwą identyfikację opóźnień w realizacji zamówień klienta, prognoz, zleceń produkcyjnych i projektów. Podczas procesu optymalizacji produkcji uzyskamy możliwość szybkiej identyfikacji wąskich gardeł (materiały, półprodukty, grupy zasobów, zasoby). Po wygenerowaniu Wykresu Gantta otrzymujemy przejrzystą, graficzną interpretację planów. Nie sposób nie wspomnieć o opcji tworzenia alternatywnych planów, tzw. analiz „co jeśli”, z kopii planu głównego, bez zakłócania jego realizacji.
Czy zaawansowane możliwości systemów APS oznaczają zarazem skomplikowaną obsługę? Na ile udaje się wykorzystać ich potencjał?
O tym, czy możliwości systemu są w odpowiedni sposób wykorzystywane, w przeważającym stopniu decyduje proces wyboru rozwiązania oraz jego wdrożenia. Współpracując z firmą, która posiada duże doświadczenie i ma na koncie współpracę z wieloma przedsiębiorstwami produkcyjnymi, zyskuje się pewność, że będzie ona w stanie szybko zidentyfikować rzeczywiste potrzeby klienta. Firma TRAX podczas wdrażania systemu Infor CloudSuite APS poświęca czas na poznanie specyfiki realizowanych w fabryce zadań produkcyjnych stosując certyfikowaną metodę wdrożeniową Infor OPIM. W ramach tej metody większość zadań wykona firma TRAX, przejmując odpowiedzialność za wdrożony system, dając możliwość objęcia opieki nad rozwiązaniem oraz gwarancję rozwoju systemu w przyszłości.