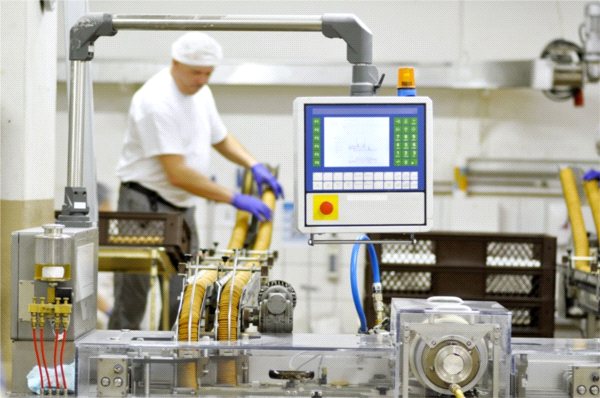
Dążenie do decentralizacji
Coraz mniej wątpliwości budzi fakt, że dążenie do maksymalnej elastyczności procesów realizowanych w firmie produkcyjnej musi łączyć się z ich decentralizacją. W przeciwnym wypadku poziom złożoności centralnego systemu kontrolnego stałby się niewyobrażalny.Tym samym nowe światło...
Tym samym nowe światło pada na jeden z elementów koncepcji Przemysł 4.0, czyli rozproszone struktury. Kluczową rolę grają elastyczne procesy i możliwość dokonywania wyborów niezależnie od centralnej struktury. Warto przyjrzeć się istniejącym powiązaniom oraz adekwatnym przykładom.
Decentralizacja zaczyna się od małej skali
W przeciwieństwie do szeroko rozpowszechnionej praktyki mocno hierarchicznej kontroli produkcji, w nowoczesnych halach produkcyjnych używane jest coraz więcej samoregulujących się systemów oraz inteligentnych mechanizmów kontrolnych. Nie mówimy już tylko o inteligentnych maszynach, ale również inteligentnych procesach, które dają pracownikom większą swobodę wyboru. Jednym z podstawowych fundamentów tej koncepcji jest dostęp do informacji poza centralnymi strukturami. Lokalne komórki, dysponując informacjami oraz dodatkowo wzbogacając je o zebrane przez siebie dane, będą w stanie podejmować autonomiczne decyzje. Co więcej, do tego typu decentralizacji na małą skalę wdrażanie takich technologii jak chmury obliczeniowe czy CPS nie będzie niezbędne.
Przykłady z intralogistyki
Prostym przykładem zdecentralizowanego i samoregulującego się systemu jest Kanban. Przypomnijmy: Kanban zakłada produkcję odpowiednich elementów tylko w sytuacji, gdy zgłoszono na nie zapotrzebowanie, w określonej ilości, aby uniknąć powstawania nadmiernych zapasów. Zasada ta znana jest również jako system ssący i łączy się ze stosowaniem supermarketów. W klasycznym rozwiązaniu Kanban jest tak zdecentralizowany, że interwencja ze strony centralnego nadzoru w znaczącym stopniu zaburzyłaby przebieg procesów.
Uzupełniając system Kanban o elektroniczne elementy kontrolne, zapewniamy przejrzystość procedury i tym samym możemy zsynchronizować ją z innymi prowadzonymi procesami. Tego typu rozwiązanie znane jest jako eKanban. Zdecentralizowany charakter, kiedy to sygnał do rozpoczęcia produkcji danego wyrobu przychodzi z hali, a nie nadrzędnego systemu planowania, pozostaje cechą charakterystyczną eKanban i gwarantuje wydajność tej metody.
Zarządzanie transportem wewnętrznym w nowoczesnym stylu również może być zorganizowane lokalnie. Tym samym możliwa jest sytuacja, w której pracownik, wykonując operacje na swoim stanowisku pracy, generuje zlecenia transportowe – na przykład po wykonaniu odpowiedniej ilości wyrobów syganlizuje konieczność odebrania palety. Gdy zlecenie transportowe zostaje wygenerowane (z takimi danymi jak miejsce odbioru, miejsce docelowe i lista wyrobów do przewiezienia), najbliższy wolny kierowca wózka widłowego może zarezerwować dla siebie a następnie wykonać to zadanie.
Tego typu podejście może też być wykorzystane przy transporcie surowców na początek linii produkcyjnej czy też dostarczeniu narzędzi niezbędnych do dokonania przezbrojenia. Dzięki inteligentnym procesom dystrybucji oraz swobodzie w dokonaniu wyboru przez osobę odpowiedzialną za zadania transportowe mamy pewność, że nie będzie potrzeby przeprowadzenia centralnej interwencji. Ale jednocześnie system zarządzający produkcją wie, które zadanie transportowe zostały już wykonane, a które wciąż oczekują na realizację.
Kombinacja zdecentralizowanych systemów
Zarówno eKanban, jak i zdecentralizowane zarządzanie transportem przynoszą korzyści w postaci zmniejszenia nakładów na planowanie I koordynację, gdyż w przypadku obu systemów te działania wykonywane są automatycznie. Zaś połączenie eKanbanu i zarządzania transportem może multiplikować te korzyści: zadanie transportowe zostaje wygenerowane automatycznie, gdy należy zabrać właśnie opróżniony – lub napełniony – pojemnik. Mamy wówczas pewność, że każdy pojemnik Kanban znajduje się na odpowiednim etapie cyklu. Jednocześnie panel eKanban prezentuje status wszystkich pojemników używanych w cyklu. Dodatkowo możemy wykorzystywać tagi RFID wielokrotnego zapisu, aby lokalnie zapisywać dane dotyczące cyklu Kanban. Alternatywą dla takiego rozwiązania jest oznaczenie pojemników kodem kreskowym – wszystkie informacje są wówczas zapisane w centralnym systemie.
Jeśli chcielibyśmy pójść z tym scenariuszem o krok dalej, system zarządzania transportem wewnętrznym może zostać powiązany przez interfejs z systemem pojazdów pozbawionych kierowcy . Wówczas zlecenia transportowe byłyby realizowane według zasady maksymalnej wydajności, zaś przed ich rozpoczęciem automatycznie zostałaby przeprowadzona optymalizacja trasy.
Inną alternatywę stanowi wsparcie aplikacji mobilnych, aby zapewnić płynne działanie i zwiększyć elastyczność generowania zadań transportowych. Przy wykorzystaniu aplikacji mobilnej nowe zlecenie transportowe może zostać wygenerowane na przykład natychmiast po awarii jednego z pojazdów, gdy zaplanowane dla niego zadania muszą być obsłużone przez inną jednostkę.
Centralna synchronizacja z MES
Niezależnie od zastosowanego rozwiązania oraz stopnia jego zautomatyzowania, ciągła synchronizacja z centralnym systemem jest nieunikniona. Z jednej strony wynika to z potrzeby zachowania przejrzystości, a z drugiej ma na celu szybką identyfikację krytycznych sytuacji i w miarę możliwości złagodzenie ich skutków. System, który musi synchronizować realizację wielu zdecentralizowanych procesów, musi być zasilany szerokim spektrum informacji, a także działać w czasie rzeczywistym, aby wykorzystać zebrane dane.
Wymagania te spełnia system klasy MES (Manufacturing Execution System), który może pełnić rolę huba gromadzącego wszystkie dane z procesu produkcji. Informacje na temat maszyn i narzędzi, materiałów, zleceń produkcyjnych oraz pracowników kwalifikują MES do roli narzędzia, które dokonuje centralnej synchronizacji zadań. Jednakże taki system ma także możliwość monitorowania i koordynowania zdecentralizowanych scenariuszy planowania. Przecież procedura zebrania wszystkich danych z produkcji i przekazania ich do nadrzędnego procesu ERP, pozostaje taka sama. Generalnie można stwierdzić, że zdecentralizowana organizacja procesów daje korzyści, choć niezbędne jest zachowanie pewnego stopnia nadzoru ze strony jednostki centralnej.
Wnioski
Podsumowując te wywody, możemy stwierdzić, że:
- inteligentne działanie na poziomie lokalnym i zapewnienie swobody wyboru mogą znacząco ograniczyć pracę związaną z planowaniem, jak też uprościć funkcjonowanie centralnej jednostki,
- synchronizacja działań przez element centralny (np. system MES) jest jednak bardzo ważna,
- wykorzystywana technologia często gra drugorzędną rolę i tylko wspiera zdecentralizowane procesy.