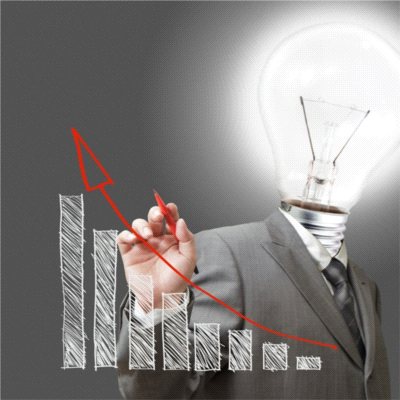
Bliżej doskonałości
Wysoki wzrost efektywności linii produkcyjnych oraz usprawnienie współpracy zespołu uzyskała spółka Jantoń, dzięki wprowadzeniu systemu zarządzania Lean Management. Firma wprowadza kolejne procesy, które mają na celu wzrost efektywności produkcji oraz jakości pracy w...
– Lean Management to sposób zarządzania polegający na ciągłym doskonaleniu procesów po-przez m.in. ograniczenie zbędnych operacji w procesie produkcji oraz dbałość o najwyższą jakość produktów przy zachowaniu niskich kosztów wytwarzania. Zdecydowaliśmy się na wprowadzenie procesu Lean ponieważ chcieliśmy zoptymalizować przede wszystkim procesy produkcji – mówi Jacek Jantoń, prezes Jantoń S.A. Sp.k. – Do procesu podeszliśmy w sposób systemowy: ustaliliśmy priorytety, a następnie wybraliśmy te narzędzia i metody, dzięki którym usprawniliśmy najistotniejsze obszary działania firmy. W pierwszych latach realizacji procesu Lean zastosowaliśmy m.in. metodę SMED (Single Minute Exchange of Die), filozofię TPM (Total Productive Maintenance), Program Sugestii Pracowniczych Kaizen oraz wdrożyliśmy system informatyczny klasy MES.
SMED wśród priorytetów
Jednym z priorytetów firmy było skrócenie czasu przezbrajania maszyn, który wpływa na wydajność i większą elastyczność produkcji. W związku z tym jednym z pierwszych narzędzi Lean, które wykorzystał Jantoń, był SMED (Single Minute Exchange of Die). Istota techniki SMED przewiduje zastosowanie szeregu sposobów redukowania i doskonalenia czynności wykonywanych podczas przezbrojenia.
Kolejną istotną kwestią w procesie zmian była współpraca z zespołem. Zmiany rozpoczęto od projektu szkoleniowo-wdrożeniowego, który miał na celu poprawę efektywności, koncentrując się na poszerzeniu kompetencji i kwalifikacji personelu. Znajomość całego procesu wytwarzania napojów alkoholowych, pozwala na usprawnienie pracy na liniach produkcyjnych. Wykorzystano także potencjał i doświadczenie pracowników firmy. Wdrożono też Program Sugestii Pracowniczych.
Kaizen i TPM
Proste, wydawać by się mogło, zmiany, takie jak m.in. przeniesienie panelu sterowania na inną stronę, czy zmiana sposobu wystawiania dokumentów magazynowych, znacząco wpłynęły na produktywność i czas pracy. Mówiąc o roli personelu, należy wspomnieć o wykorzystaniu narzędzia Lean, jakim jest japońska filozofia biznesu Kaizen. Kaizen to doskonalenie stylu życia, doskonalenie siebie jako sprawnego pracownika. Postępowanie zgodnie z zasadami filozofii przekłada się na podnoszenie jakości firmy i produktu, poprzez świadomą ocenę wykonywanych przez ludzi czynności. Kaizen pozwoliło na wyeliminowanie zbędnych działań i przestojów w pracy oraz usprawnienie systemu organizacji pracy.
W firmie Jantoń wdrożono również podstawy filozofii TPM (Total Productive Maintenance). TPM jest całokształtem działań przedsiębiorstwa, zmierzających do zapewnienia sprawności technicznej maszyn, urządzeń i oprzyrządowania w celu maksymalnego ich wykorzystywania. TPM wiąże się z przekazaniem pewnych obowiązków związanych z obsługa maszyn i urządzeń bezpośrednim ich użytkownikom. Dlatego w Jantoń do zadań operatorów dodano przede wszystkim: smarowanie, czyszczenie, konserwacje, a także dbałość o prawidłowy stan (np. dokręcanie śrub) wszystkich maszyn i urządzeń. Sporządzone zostały specjalne karty przeglądowe, gdzie operatorzy mają wypisane w punktach co należy wykonać podczas przeglądu.
Kolejnym krokiem była standaryzacja pracy na produkcji. Dla wszystkich maszyn w zakładzie zostały ustalone standardowe ustawienia parametrów dla każdego programu na maszynie. Parametry zostały spisane na specjalnych arkuszach, do których wszyscy operatorzy mają dostęp. Dzięki standaryzacji, udało się uzyskać większą płynność pracy linii i wyeliminowane zostały przestoje powodowane błędnym ustawieniem parametrów na maszynie.
MES pomaga eliminować przestoje
Problemy, z jakimi borykają się zakłady produkcyjne, to mikroprzestoje, spadki wydajności i awarie. Aby wyjść naprzeciw oczekiwaniom firma Jantoń zdecydowała się wdrożyć system realizacji produkcji MES. System klasy MES pozwala na pełną kontrolę nad wydajnością parku maszynowego i procesem produkcyjnym oraz umożliwia optymalizację operacji procesu produkcyjnego w obszarze biznesowym. Dzięki systemowi MES można śledzić przebieg produkcji w czasie rzeczywistym, co wspiera zarządzanie produkcją i podejmowanie decyzji. Obszerne raporty dostarczane przez system dotyczące wszystkich przestojów, awarii i wydajności maszyn pozwalają szczegółowo przeanalizować przyczyny strat i wyciągnąć wnioski w celu doskonalenia procesu.
– Osiągnięcie znaczącego wzrostu wydajności linii produkcyjnej to duży sukces. Mamy jednak świadomość, iż Lean to proces ciągły. Obecnie rozpoczynamy kolejny projekt z zakresu logistyki. – mówi prezes Jantoń. – Jesteśmy już po wstępnych analizach, które wskazują obszary przyszłych zmian.
Jantoń S.A. Sp.K. powstała w 1976 roku. Obecnie jest jednym z największych producentów, importerów i dystrybutorów branży winiarskiej w Polsce. Szeroka i różnorodna oferta produktowa firmy zawiera m.in.: wina gronowe, wina musujące, wermuty, wina grzane, ekologiczne, deserowe, owocowe, cydry, napoje niskoalkoholowe oraz drinki RTD.