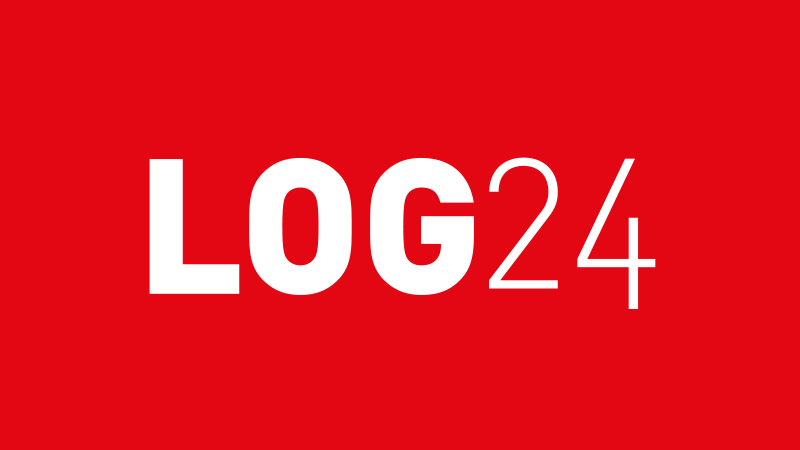
Trendy w produkcji
Obserwując zmiany w podejściu fabryk do realizowanych operacji postanowiliśmy pochylić się nad kwestią trendów, które aktualnie dominują w działalności firm produkcyjnych. W naszym subiektywnym zestawieniu spoglądamy na nie z perspektywy producentów działających w Polsce...
Perspektywa ta z pewnością nieco inna, niż w przypadku najbardziej rozwiniętych światowych gospodarek. Co prawda większość z omawianych trendów przybyła do nas od światowych liderów, lecz przyjmując je na nasz grunt musi pamiętać o ograniczeniach z którymi borykają się firmy w Polsce.
Lean i spółka
Toyota Production System, stanowiąca podwaliny Lean Manufacturing i całej chmary mutacji tej metody zarządzania, ma już po 50 lat. Czy sięganie po Lean i pochodne jest już zatem niemodne? Ależ skąd – to trend wciąż aktualny, a w Polsce szczególnie popularny.
To, która metoda – czy to Lean, czy Teoria Organiczeń, czy Six Sigma, czy Quick Response Manufacturing – jest wybierana, nie jest istotne. Uwagę chcemy zwrócić bowiem na to, że firmy dostrzegają potencjał do poprawy we własnej organizacji, jak też możliwości, jakie daje ciągłe doskonalenie.
Lean, stanowiący początkowo metodę typową dla branży motoryzacyjnej, rozprzestrzenia się na inne sektory. Ostatnie miesiące to także przenoszenie narzędzi ciągłego doskonalenia poza hale produkcyjne. Po metodykę leanowską sięgają obszary administracji, coraz więcej wdrożeń dotyczy też sektora usług.
Warto zwrócić uwagę, że upowszechnianie się nowoczesnych metod zarządzania to przede wszystkim zasługa zagranicznych inwestycji. Polskie firmy podpatrują standardy stosowane u kontrahentów i konkurentów, przenosząc je na swój grunt. Jak więc widać, korzyści płynące z inwestycji zagranicznych nie są jednowymiarowe.
Rosnąca popularność systemów IT
Oczywiście, nie można powiedzieć, że rozwiązania informatyczne nie są już teraz obecne w działających w Polsce firmach produkcyjnych. Sęk tym, że producenci nader często ograniczają się do Excela, któremu nie można odmówić elastyczności, ale w wyspecjalizowanych zadaniach szybko docieramy do granic możliwości arkusza kalkulacyjnego.
Po ERP, czyli często narzędzie wciąż stosunkowo uniwersalne, sięga tylko ¼ działających w Polsce producentów. Tymczasem możliwości zaawansowanych systemów tworzonych z myślą o producentach – przede wszystkim MES i APS, ale też CMMS czy EAM – są imponujące. Możliwość śledzenia produkcji w toku, wsparcie planowania czy bieżąca ocena stanu parku maszynowego owocuje w wielu przypadkach wręcz rewolucyjną poprawę produktywności.
Oprogramowanie nie zrobi za nas wszystkiego, ale wspieranie się zaawansowanym IT to nieodwracalna tendencja, o czym świadczą jednoznacznie pozytywne komentarze jego użytkowników. Systemy IT nieustannie ewoluują i w tej chwil powszechne w fabrykach stają się technologie mobilne. Prawdziwa przyszłość to jednak rozwój komunikacji między maszynami, wpisująca się z założenia Przemysłu 4.0. Nie ma też wątpliwości, że nieustannie rósł będzie problem cyberbezpieczeństwa w firmach produkcyjnych.
Automatyzacja i robotyzacja
Automatyzacja i robotyzacja jest w naszych warunkach szczególnym przypadkiem. Nie pierwszy już raz wspominamy, że trend ten spotyka w Polsce szczególnie duży opór, wynikający z kilku czynników.
Niskie koszty pracy nie skłaniają zarządów firm do zastępowania pracy ludzkiej robotami. Nie brakuje też pewnego oporu dla wprowadzania nowych technologii, wynikającego ze swego rodzaju przywiązania do tradycyjnych rozwiązań. Nie bez znaczenia pozostają tez duże jednorazowe koszty inwestycji, związanej z robotyzacją fabryki.
Swoje robią też protesty pracowników, obawiających się utraty stanowisk. Tymczasem doświadczenia z krajów, w których roboty są już upowszechnione, pokazują, że automatyzacja nie wywołuje fali zwolnień, zaś uwolnienie pracowników od konieczności wykonywania nużących czynności, często w trudnych warunkach, wyraźnie poprawia morale. Wreszcie wysoka jakość operacji prowadzonych przez roboty sprawia to wymóg, jaki coraz częściej stawiają przed producentami klienci.
Druk 3D
Technologia druku 3D straciła już status absolutnej nowości, ale w działających w Polsce firmach produkcyjnych nie jest jeszcze zbyt często spotykana. Bez wątpienia będzie się ona upowszechniać, lecz najprawdopodobniej w nieco innym kierunku, niż oczekiwano.
Druk 3D zwrócił na siebie uwagę możliwościami, jakie daje ta technologia. Jednak gdy przestaniemy zwracać uwagę tylko na efektowne pokazy, dostrzeżemy ograniczenia wiążące z wykorzystaniem go w masowej produkcji. Druk 3D pozostaje zbyt drogi, aby mógł zastąpić inne techniki seryjnego wytwarzania, zaś sam proces pochłania sporo czasu.
Jednak technologia ta jest tak młoda, że można liczyć na szybkie postępy w jej udoskonalaniu. A już teraz można z powodzeniem wykorzystywać ją w procesach prototypowania, jak na przykład czyni to Sapa Aluminium. General Motors drukuje z kolei nietypowe narzędzia wykorzystywane następnie przy produkcji samochodów. Wielki potencjał druku 3D widać także w procesach kastomizacji produkcji.
Masowa kastomizacja
A skoro już o niej mowa, masowa kastomizacja to kolejny trend waty uwagi. Mówi się o nim już od lat, ale pozostaje aktualny i odegrał znaczącą rolę w tworzeniu założeń Przemysłu 4.0. Fabryki przyszłości mają cechować się maksymalną elastycznością, aby być w stanie dopasować się do szybko zmieniających się potrzeb klientów.
Pojęcia masowej kastomizacji pojawiło się już w latach 80-tych XX w – Stanley Davis w książce „Future Perfect” opisywał fenomen „szycia na miarę” koszul w produkcji masowej i do tego bez znaczącego wzrostu kosztów. Rozwój nowych technologii sprawił, że kastomizacja zagościła także w innych branżach – elektronicznej, meblarskiej czy motoryzacyjnej.
Trend kastomizacji z pewnością nie wygaśnie, bowiem napędza go rewolucja wywołania przez e-commerce i Internet. Regularnie spada też różnica w cenie między seryjnymi a skastomizowanymi produktami. Firmy produkcyjne muszą liczyć się w tym, że wkrótce powszechna będzie komunikacja z klientem już na etapie projektowania wyrobu.
Planowanie i strategie
Zwiększanie nacisku na zintegrowane planowanie produkcji wynika z chęci definitywnego pożegnania się z systemem pracy, który opierał się na gaszeniu pożarów na produkcji. Plany produkcyjne były nieustannie odsuwane na bok i pomimo istnienia takich narzędzi jak MRPII, rzadko był czas aby postępować zgodnie z ich zasadami.
Gaszenie pożarów wielokrotnie było efektem niespodziewanych zamówień. Firmy produkcyjne zaczynają znajdować na to radę, sięgając z planowaniem poza obszar hali produkcyjnej. Sales&Operational Planing przekonuje do siebie producentów dzięki możliwości przygotowania się na zmiany popytu.
Wdrożenia S&OP wiążą się z dodatkową korzyścią. Sprawdzają się one bowiem tylko wówczas, gdy angażują się w nie wszystkie działy. W efekcie produkcja i sprzedaż przestają być dwiema działającymi w oderwaniu od siebie działami firmy. Zintegrowane planowanie wymusza nawiązanie współpracy i powoduje efekt synergii, dzięki któremu firmy produkcyjne zyskują dojrzałość organizacyjną.
Udana współpraca wewnątrz organizacji to także pierwszy krok do dojrzałej współpracy z innymi firmami. Tym samym zyskujemy możliwość nawiązania relacji win-win z kontrahentami i klientami, oraz zaangażować się w takie działania jak tworzenie klastrów.
Współpraca w klastrach
Tradycyjne podejście do innych z firm z branży było jasne – konkurent, czyli wróg. Z przyjemnością obserwujemy zatem zmianę ten filozofii i coraz częstsze tworzenie się klastrów i grup, gromadzących producentów świadomych tego, że współpracować warto z każdym.
Dolnośląski Klaster Motoryzacyjny czy Dolina Lotnicza – to przykłady największych organizacji tego typu działających w Polsce. Firmy dzięki tworzeniu większych struktur są w stanie współpracować w szeroko pojętym interesie klastra oraz jednym głosem reprezentować swoje interesy. Istnienie klastrów zapewnia rozwój danej branży jak też pozytywnie przekłada się na działalność wszystkich członków.
Otwartość członków na wymianę doświadczeń to podstawowy warunek skutecznej działalności klastra. Łączenie się w klastry, oprócz wymiany wiedzy, niesie za sobą szereg udogodnień m.in. generowanie i wdrażanie nowych rozwiązań technologicznych czy organizacyjnych. Jednocześnie członkowie klastrów często tworzą grupy zakupowe i mogą negocjować ceny prądu oraz innych mediów.
Walka o talenty
Hasła dotyczące troski o pracowników od lat były jedną z podstaw PR wszystkich firm produkcyjnych. Jednak dziś, ze względu na wysychający rynek pracy, przestaje to być czcza deklaracja.
Niedobory talentów szczególnie odczuwane są na terenach silnie uprzemysłowionych. Z powodów logistycznych i podatkowych (istnienie specjalnych stref ekonomicznych) nadal są to najpopularniejsze lokalizacje dla nowych inwestycji. Rynek pracy nie jest jednak z gumy i firmy produkcyjne podnoszą pensje oraz kuszą pracowników dodatkowymi benefitami. Dopieszczanie pracowników ma też drugie dno. Zmotywowana i dobrze dobrana załoga jest w stanie znacząco przyczynić się do poprawy działalności firmy, angażując się w programy ciągłego doskonalenia.
Kolejnym trendem związanym z niedoborami na rynku pracy w Polsce jest otwieranie klas patronackich oraz kierunków na studiach przez firmy produkcyjne. Udało się przekonać rząd, aby ponownie zainwestować w technika i szkoły zawodowe, zaś producenci szybko zaoferowali swoje wsparcie. Volkswagen, BASF, Delphi, GM – to tylko przykłady z największych koncernów, które otworzyły w Polsce klasy patronackie i szukają cennych pracowników już na etapie edukacji. Wraz z rozwojem działalności badawczo-rozwojowej w Polsce rośnie też współpraca producentów z uczelniami wyższymi, czego przykładem może być Wielton.
Ekologia i energooszczędność
Ekologia i energooszczędność to aktualnie chyba najważniejszy trend w całej światowej gospodarce. W sektorze produkcji wiąże się on jednak nie tylko z dobrym wizerunkiem, ale także z realnymi korzyściami. Nic więc dziwnego, że działania proekologiczne szybko przybierają na sile także w polskich fabrykach.
Praktycznie wszystkie nowe inwestycje tworzone są wykorzystaniem energooszczędnych technologii – począwszy od oświetlenia LED a skończywszy na systemach wentylacji i ogrzewania. W istniejących już zakładach coraz częściej pojawiają się instalacje odzyskiwania ciepła powstające w ramach procesów produkcyjnych. Elektrownie i huty inwestują z kolei w układy odsiarczania spalin.
Fabryki szczycą się tym, że udaje im się wyeliminować nawet 100 proc. odpadów produkcyjnych, dzięki ekoprojektowaniu i recyklingowi. Popularność zyskuje tez możliwość pozyskiwania energii z odnawialnych źródeł.
Energooszczędność dla polskich przedsiębiorców jest szczególnie ważna, bowiem ceny prądu dla odbiorców przemysłowych są u nas bardzo wysokim poziomie. O ile roboty budzą obawy, a nowoczesne systemy IT nie zawsze wydają się przydatne, to do inwestycji w ograniczenie zużycia energii łatwo jest przekonać zarządy firm.
CSR i jego znaczenie
CSR czyli odpowiedzialność społeczna biznesu to kolejny trend, który ostatnio jest na topie także w firmach produkcyjnych. Wszystko wskazuje na to, że będziemy obserwować wzrost znaczenia CSR także poza dużymi korporacjami.
CSR staje się bowiem coraz istotniejszym czynnikiem podczas negocjacji handlowych. Coraz częściej jakość produktu ma wyższe znaczenie niż jego cena, zaś teraz ważne staje się również, czy producent w ramach swoich działań szanuje środowisko naturalne oraz interesy społeczne. Zwolennicy CSR podkreślają, że firmy prowadzące zaawansowaną politykę społeczną łatwiej przywiązują do siebie pracowników i przyciągają młode talenty. Należy jednak pamiętać, że należy znaleźć właściwy kompromis między znaczeniem CSR a realizacją celu biznesowego.