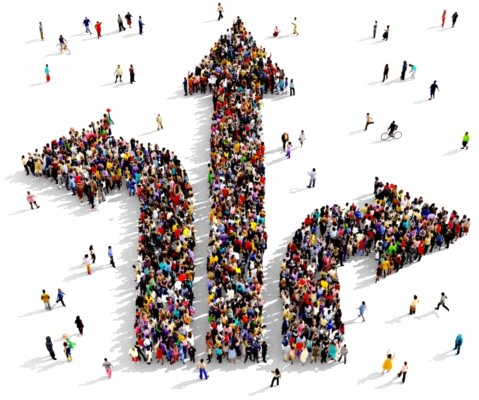
Przecierając szlaki digitalizacji
Na początku czerwca omówiliśmy obszerny raport PwC, poświęcony digitalizacji firm produkcyjnych i obszarom, dzięki którym cyfrowi czempioni zyskują przewagę nad rywalami. Powracając do tematu, tym razem przedstawimy kilka przykładów firm z czołówki rankingu, które wdrożyły...
Safran i skokowy rozwój
Safran, międzynarodowa grupa działająca w obszarze wysokich technologii, dąży do wykonania milowego kroku na polu wzrostu konkurencyjności dzięki programowi cyfrowej transformacji. Firma obsługuje klientów na rynku napędów, sprzętu lotniczego, kosmicznego i obronnego. Rynki te wiążą się z poważnymi wyzwaniami, wśród których niepoślednią rolę grają znaczący wzrost zamówień, szerokie portfolio produktów i różnorodność części do produkcji.
Inicjatywa „Factory of the Future” firmy Safran jest kluczową częścią cyfrowej transformacji, która wprowadza przełomowe i rozproszone technologie w sercu swoich zakładów produkcyjnych. Sednem tej inicjatywy jest świadomość, że taka futuralizacja jest kluczowa dla rozwiązania problemu niespotykanego wcześniej tempa zmian na rynku. Na przykład nowy silnik Leap osiąga w ciągu czterech lat poprawę osiągów, której jego poprzednik, CFM56, nie osiągnął w ciągu 20 lat produkcji seryjnej.
Ekosystemy technologiczne
Rozwój wysoce zaawansowanych ekosystemów technologicznych i pracowniczych jest istotną platformą do sprostania tak silnemu wzrostowi. Safran pokazuje, że nie trzeba budować nowej fabryki, aby wdrażać przełomowe technologie produkcji. Firma zbudowała innowacyjne linie produkcyjne w istniejących zakładach. Na przykład silniki Leap są wytwarzane na linii z cyfrowym systemem projekcji, który pomaga właściwie pozycjonować komponenty i podzespoły, a opatentowany system utrzymuje i obraca silnik w poziomie. Safran stworzył pierwszą zautomatyzowaną linię produkcyjną łopatek turbiny śmigłowca, począwszy od surowego odlewu a kończąc na części gotowej do zamontowania na silniku. Firma wdraża także roboty współpracujące (koboty) na kilku liniach produkcyjnych, umożliwiając łączenie możliwości robota (siła, precyzja, powtarzalność itp.) z umiejętnościami charakterystycznymi dla ludzi (know-how, analiza, decyzyjność itp.). Operator i system robotyczny współpracują ze sobą bezpośrednio lub za pomocą zdalnego sterowania, a nawet z egzoszkieletem, który zwiększa możliwości ludzkiego ciała.
Zmiana skoncentrowana na człowieku
Oprócz ekosystemów technologicznych służących do transformacji produkcji, Safran zdaje sobie sprawę z tego, że ludzie są nadal nieodzowną częścią fabryki przyszłości i rozwija rozległy ekosystem pracowników, aby zwiększyć wiedzę i umiejętności operatorów w tym nowym środowisku. Mocne poparcie załogi dla cyfrowej transformacji było kluczowym elementem tej inicjatywy. Na przykład obróbka detali w zamkniętych maszynach zmienia rolę operatorów. Przesuwają się oni w górę łańcucha umiejętności, aby stać się koordynatorami komórki obróbkowej, zdolnej do obsługi kilku maszyn jednocześnie i wymagającej zaawansowanej komunikacji (duże ekrany i tablety itp.). Mogą skoncentrować się na zadaniach nadzoru i kontroli o wysokiej wartości dodanej, podczas gdy maszyny działają niezależnie. Safran współpracuje z innymi firmami przemysłowymi w celu utworzenia centrum szkoleniowego w Bondoufle pod Paryżem, co zaowocuje znacznym wzrostem kwalifikacji. Począwszy od 2018 r. około 300 studentów uczestniczy w programach trzyletnich studiów doktoranckich, a kolejne 300 osób będzie kontynuowało szkolenia w zakresie nowych metod produkcji: połączonych maszyn, Internetu Rzeczy, wytwarzania addytywnego, rozszerzonej rzeczywistości, kobotów i innych zaawansowanych technologii.
BASF: Lider transformacji cyfrowej w chemii
Myślenie kryjące się za ekosystemami zdefiniowanymi w raporcie PwC nie jest niczym nowym dla BASF. Jest to kluczowe dla zasady „Verbund” (integracji), która jest tradycyjną siłą firmy. Verbund kładzie nacisk na inteligentną integrację nie tylko zakładów produkcyjnych, ale też przepływów logistyczne i infrastruktury, a także na wiedzy i popytu. To okazało się mocną podstawą do uruchomienia BASF 4.0 -, kompleksowej inicjatywy cyfrowej, której wyniki zwiększają wydajność i wzrost.
Większa efektywność
Ta inicjatywa napędza cyfrową transformację we wszystkich obszarach działalności firmy. Kluczowym obszarem jest „inteligentna produkcja”. Aplikacje rozszerzonej rzeczywistości wspierają pracowników produkcyjnych w ich codziennych działaniach. Skracają czas przejścia na kolejną zmianę, pomagając uczynić zadania namacalnymi i rzeczywistymi, a dane są dostępne natychmiastowo we właściwym czasie i we właściwym miejscu. BASF postawił sobie za zadanie rozwinąć rozszerzoną rzeczywistość w ponad 400 zakładach na całym świecie w ciągu najbliższych lat. Podobnie ma się sytuacja z predyktywnym utrzymaniem ruchu, które ma zostać wdrożone w 100 dużych zakładach produkcyjnych. Predyktywne utrzymanie ruchu przewiduje krzywą wydajności najważniejszych maszyn i urządzeń. Dane te są wykorzystywane do uruchamiania prac konserwacyjnych lub do zmiany parametrów operacyjnych. Jednym z głównych tematów w dziedzinie digitalizacji w obszarze badań i rozwoju jest modelowanie naukowe i symulacja z użyciem komputerami o wysokiej wydajności. Superkomputer BASF Quriosity pomoże skrócić czas wprowadzania produktu na rynek, umożliwiając przetwarzanie większej liczby i znacznie bardziej złożonych symulacji i modelowania oraz poprzez odkrywanie nieznanych dotąd zależności. Zwiększa to wydajność BASF pod względem skracania czasu cyklu i tempa pozyskiwania wyników. Przykłady obejmują symulacje w obszarze katalizatorów przemysłowych i środków ochrony roślin. W przypadku katalizatorów szczególnie ważne jest zwiększenie ich wydajności, a tym samym minimalizacja wpływu na środowisko naturalne, poprzez zmniejszenie ilości surowców i generowanie mniejszej ilości odpadów. Ważne jest również, aby produkty ochrony roślin działały wydajniej i w bardziej ukierunkowany sposób, aby lepiej spełniać bieżące i przyszłe wymagania.
BASF wykorzystuje również technologie cyfrowe, aby zwiększyć przejrzystość danych w całym łańcuchu dostaw. Poprawia to niezawodność dostaw i buduje bliższe relacje z klientami, dostawcami i strategicznymi partnerami. Dzięki współpracy z partnerami w łańcuchu dostaw poprzez zintegrowany ekosystem, BASF zapewnia dostęp do danych w czasie rzeczywistym w celu umożliwienia proaktywnego zarządzania informacją przy jednoczesnym zwiększeniu zdolności reagowania klienta i generowaniu zrównoważonego rozwoju firmy.
Silniejszy wzrost
Cyfrowe modele biznesowe otwierają możliwości sprzedaży nowych usług klientom, w tym nowych strumieni dochodów poza produktami chemicznymi. Firma BASF opracowała do tej pory ponad 50 takich modeli, z których wiele zostało zrealizowanych, umożliwiając klientom współpracę przy specyfikacjach produktów w sposób, który wcześniej nie był możliwy. Na przykład, portfel produktów cyfrowych Maglis dla rolników pomaga im w zarządzaniu polami i wspiera ich w podejmowaniu przez cały rok bardziej świadomych decyzji na temat sposobów uprawy i wprowadzania na rynek swoich upraw. Wraz z BASF rolnicy mogą tworzyć indywidualne plany zarządzania polami i uprawami, które umożliwiają im zarządzanie ryzykiem i poprawę wydajności. BASF dostrzega elastyczność, powtarzalne doskonalenie i wczesne zaangażowanie klientów jako klucze do pełnego wykorzystania możliwości cyfrowych technologii.
W branży przetwarzania gazu platforma online OASE łączy się z klientami, którzy mogą symulować i poprawiać warunki pracy swoich zakładów, pobierać dane na temat kupowanych od BASF surowców oraz uzyskiwać dostęp do materiałów e-learningowych i informacji ogólnych.
Pracownicy BASF znajdują się w centrum cyfrowej transformacji. Obejmuje ona 115 000 pracowników, którzy są podzieleni na 13 działów operacyjnych, siedem działów funkcjonalnych, trzy platformy technologiczne, cztery regiony, sześć placówek Verbund i dodatkowe 347 zakładów produkcyjnych na całym świecie. Zróżnicowane portfolio branż klientów i rozwiązań biznesowych wymaga zrównoważonego podejścia do digitalizacji. Kierują nią Chief Digital Officer, który bezpośrednio podlega dyrektorowi generalnemu i odpowiada za stworzenie cyfrowego ekosystemu w ścisłym powiązaniu z silnym kręgosłupem IT. Zasada Verbund służy jako strategiczne wytyczne w tym długoterminowym procesie transformacji. Budując ekosystemy cyfrowe zgodnie z zasadami Verbund, BASF jest liderem transformacji cyfrowej w przemyśle chemicznym.
GE Digital: Zasilanie dla nowej ery produktywności przemysłowej
Cyfrowa transformacja w firmie GE nie tylko przekształca produktywność wewnątrz firmy, ale zapewnia trampolinę, która będzie kierować kolejną falą wzrostu produktywności przemysłowej na zewnątrz. Zastosowanie zaawansowanych technologii cyfrowych w celu przekształcenia procesów przemysłowych i wydajności przynosi namacalne rezultaty. Plan GE, zakładający osiągnięcie wzrostu wydajności o wartości 1 mld USD w latach 2015-2020 został zrealizowany już do końca 2017 r.
Osiągnięcie to jest kluczowym krokiem na pierwszym etapie cyfrowej strategii przemysłowej GE – wykorzystania potencjału digitalizacji do poprawy wydajności wewnętrznej i efektywności operacyjnej. Firma nazywa to „GE dla GE”. Nauka płynąca z tych wdrożeń jest następnie wykorzystywana do zaoferowani klientom automatyzacji i aplikacji w pakietach, pod hasłem „GE dla klientów”. Wreszcie koncepcja „GE dla świata” otwiera dostęp do innowacji GE dla praktycznie każdej firmy w praktycznie każdej kategorii przemysłowej poprzez współtworzenie ich przy użyciu aplikacji Predix dla Przemysłowego Internetu Rzeczy.
Agent cyfrowej zmiany
W strukturach GE, komórka GE Digital działa jako „Agent cyfrowej zmiany”, za cel stawiając sobie zostanie najlepszym cyfrowym przedsiębiorstwem przemysłowym na świecie. Lepsze zarządzanie wydajnością aktywów, usługi terenowe i efektywność operacyjna stały się centralnym punktem innowacji cyfrowych. Duży nacisk położono na technologię wykrywania, technologię przetwarzania danych i technologię zarządzania oraz technologię predykcyjnego utrzymania ruchu. Zyski można dostrzec w zakresie wpływu gromadzenia danych i cyfryzacji wielu ręcznych procesów związanych z zarządzaniem przerwami w dostępie do energii elektrycznej przez zespół służb energetycznych GE. Obniżyło to koszty o około 200 milionów USD, skracając czas naprawy i zasoby potrzebne do naprawy i konserwacji. GE Digital podkreśla znaczenie edge computing, sztucznej inteligencji (AI) i rzeczywistości wirtualnej (VR). Sama ilość danych pochodzących z zasobów sprawia, że przetwarzanie ich z wykorzystaniem edge computing staje się kluczowym krokiem. Na przykład samochód może wygenerować jeden pedabajt (1015 bajtów) danych w ciągu jednego miesiąca. Edge computing pozwoli w efekcie na rozszerzenie platformy Predix firmy GE na urządzenia znajdujące się w zasobach lub obok nich.
Uzyskanie przyszłej przewagi
Dynamiczny rozwój sztucznej inteligencji i uczenie maszynowe umożliwia firmie GE analizowanie, modelowanie i mapowanie odmiennych źródeł danych oraz stworzyć „cyfrowego bliźniaka” środka trwałego. To z kolei pomoże firmom lepiej zrozumieć i przewidzieć wydajność, znaleźć nowe źródła dochodów i zmienić sposób prowadzenia działalności. GE również chce, by wirtualna rzeczywistość odgrywała kluczową rolę – na przykład, gdy instrukcje dla technika wyświetlane są za pomocą okularów VR , skraca się czas poświęcony na naprawy i konserwację. GE przewiduje cyfrową transformację, a Przemysłowy Internet Rzeczy przyniesie zmianę paradygmatu pracy przyszłości. Pracownicy nie będą już musieli informować systemu, co się stało lub co musi się wydarzyć. Zamiast tego system poinformuje pracowników o najlepszych opcjach, ułatwiając im podejmowanie decyzji. GE zmienia także model biznesowy, skupiając się na usługach. W niektórych obszarach swojej działalności firma GE wprowadziła ofertę „moc na godzinę”, a klient płaci za godzinę pracy urządzenia zamiast uiszczać miesięczną opłatę. W świecie usługowym, zamiast sprzedawać aktywa, GE sprzedaje wynik, jaki zapewnia składnik aktywów.
Daimler: Maksymalna elastyczność i przejrzystość
Cyfrowa transformacja obejmuje w dziale samochodowym Daimler AG cały łańcuch wartości. „Inteligentna produkcja” to jej nadrzędny cel. Inteligentna produkcja charakteryzuje się bardzo wysokim stopniem elastyczności. Jest przejrzysta i niezwykle wydajna. Zapewnia i podnosi jakość produktów, a także procesów produkcyjnych dzięki perspektywicznym i samodoskonalącym się procesom. W instalacjach o pełnej elastyczności wszystkie architektury pojazdów i typy napędów powstają na tej samej linii produkcyjnej. Wszystkie zakłady i salony, a także łańcuch dostaw i poddostawcy, tworzą cyfrową sieć inteligentnej produkcji. Na podstawie cyfrowych bliźniaków produktów i produkcji, dane są rejestrowane i oceniane w czasie rzeczywistym. W ten sposób zasoby mogą być wykorzystywane jeszcze efektywniej. Metody cyfrowe wspierają też wdrożenie zielonej produkcji, a pracownicy pracują w ergonomicznie zoptymalizowanych miejscach pracy i procesach. Planowanie zamówień obsługiwane przez metody Big Data identyfikuje i optymalnie zaspokaja potrzeby klientów.
Digitalizacja w Daimler AG koncentruje się na pięciu kluczowych obszarach:
• Ogólnoświatowe 360-stopniowe sieci wszystkich fabryk i linii produkcyjnych, począwszy od najmniejszego czujnika
• Cykliczny i ciągły łańcuch procesów, począwszy od projektowania i produkcji do obsługi posprzedażnej
• Wykorzystanie dużych ilości danych – coraz częściej w czasie rzeczywistym – w celu zapewnienia i dalszej poprawy jakości i wydajności
• Adaptowalne fabryki, które w ciągu kilku godzin można przekonwertować na nowe serie produkcyjne
• Przejrzysty i inteligentny łańcuch dostaw, oparty na autonomicznych pojazdach, inteligentnie zamawiane koszyki produktów i fabryki bez papieru.
Firma rozpoczęła już ogólnoświatową implementację we wszystkich pięciu podstawowych obszarach. Na przykład w dziedzinie łączności 360-stopniowej wykorzystuje się Wi-Fi i śledzenie lokalizacji, podobnie jak oprogramowanie Integra, które łączy ze sobą wszystkie zakłady i linie produkcyjne. W odniesieniu do cyfrowego łańcucha procesów nacisk kładziony jest na planowanie i symulacje. Jednym z przykładów jest wirtualna stacja montażowa Avatar, gdzie za pomocą wirtualnej rzeczywistości ergonomia produkcji jest zapewniona już na wczesnym etapie procesu opracowywania produktu. Dalsze przypadki użycia to współpraca między człowiekiem a robotem, analizy dużych danych, takie jak predykcyjne utrzymanie ruchu, wykorzystanie sztucznej inteligencji; oraz inteligentna logistyka, takie jak chipy RFID i systemy transportu autonomicznego.
Pomimo (a może właśnie z powodu) stosowania tak niezwykle nowoczesnych technologii, proces cyfryzacji obejmuje również transformację kulturową firmy. Spłaszczona została hierarchia organizacyjna, przez co osiągnięto wyjątkowo wysokie tempo procesów decyzyjnych. Niszczenie silosów w organizacji maksymalizuje jej usieciowienie. Koncentracja kierowana jest w stronę ludzie – klientów i pracowników.
Dział Mercedes-Benz Cars Operations (MO) jest odpowiedzialny za produkcję samochodów w ponad 30 lokalizacjach na całym świecie. W ramach elastycznej i wydajnej sieci produkcyjnej obejmującej około 78 000 pracowników obejmuje to główne funkcje planowania produkcji, Tecfactory, logistyki i zarządzania jakością. Struktura sieci oparta jest na architekturze produkcji napędu na przednie koła (samochody kompaktowe) i napęd na tylne koła (na przykład klasy S, E i C), a także na architekturze SUV i samochodach sportowych. Towarzyszy temu sieć produkcyjna dla układu napędowego (silniki, skrzynie biegów, osie, komponenty). Centralnym punktem każdej sieci produkcyjnej w architekturze jest fabryka wiodąca, która stanowi centrum kompetencji do rozpoczęcia produkcji nowych pojazdów, rozwoju technologii i zapewnienia jakości. Dzięki tej strategii MO jest w stanie produkować pojazdy przy jeszcze większej elastyczności i wydajności w połączeniu ze sprawdzoną najwyższą jakością.
Dział Daimler jest z kolei w stanie szybciej zareagować na zmiany popytu, a także zintegrować wdrażanie do produkcji pojazdów elektrycznych z bieżącą produkcją seryjną. Sukces jest oczywisty: w wyniku dużego popytu, Mercedes-Benz Cars ustanowił kolejny rekord produkcji w 2017 roku, produkując ponad 2,4 miliona pojazdów. To siódmy rekord produkcji z rzędu. Przy pomocy Przemysłu 4.0 strategia wzrostu będzie kontynuowana.
Witold Zygmunt, na podstawie raportu „Global Digital Operations Study 2018” PwC