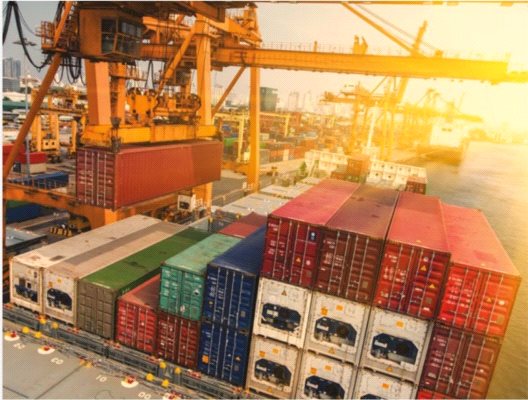
Usprawnienia procesów logistycznych
Jak podejście metodyczne i analiza danych mogą ustrzec przed ryzykiem i błędnymi inwestycjami w sprzęt magazynowy? CASE STUDYCelem projektów usprawniających procesy logistyczne jest najczęściej zmniejszenie kosztów lub zwiększenie efektywności procesów....
Celem projektów usprawniających procesy logistyczne jest najczęściej zmniejszenie kosztów lub zwiększenie efektywności procesów. Podejście menedżerów do takich projektów jest najczęściej dwojakie. Po pierwsze, na usprawnienia procesów spojrzeć można w sposób metodyczny – główny nacisk kładziony jest na znalezienie rzeczywistych przyczyn problemów oraz opracowanie rozwiązań, które je wyeliminują. Dzięki wnikliwej analizie danych możliwe jest dokładne określenie, w jakim stopniu rozwiązania usuną przyczyny źródłowe oraz jakie będą koszty wdrożeń. Firmy prowadzące usprawnienia dostają wówczas niemal gwarancję sukcesu projektu i mogą dokładnie zaplanować jego budżet. Z drugiej jednak strony, taki sposób pracy wymaga stosunkowo dużych nakładów czasu na analizę danych.
Odmiennym spojrzeniem na usprawnienia procesów jest podejście intuicyjne, w którym wykorzystywane są głównie doświadczenie i wyczucie menedżerów. Taka „droga na skróty” zapewnia szybkie zmiany, nie daje jednak pewności, że usunięte zostaną przyczyny, a nie tylko symptomy problemów.
Studium przypadku
W artykule przedstawiamy, w jaki sposób podejście metodyczne i analiza danych pozwalają podejmować przemyślane decyzje menedżerskie i unikać błędnych inwestycji. Studium przypadku, którym się posługujemy, dotyczy projektu usprawnienia rozładunku kontenerów morskich w magazynie. Przedsiębiorstwo, które zleciło projekt, importowało rocznie ok. 3000 kontenerów z Dalekiego Wschodu. W celu maksymalizacji wypełnienia kontenerów pudła przewożone były luzem, bez palet. Negatywną konsekwencją takiego sposobu załadunku był długi czas rozładunku kontenera w magazynie. Ręczne rozładowanie i ułożenie pudeł na palecie zajmowało bowiem dwóm pracownikom ok. 3 godziny. Roczna pracochłonność rozładunku 3000 kontenerów wynosiła zatem ekwiwalent 18 000 roboczogodzin, czyli ok. 10 etatów.
Kierownictwo przedsiębiorstwa uznało tę pracochłonność za zbyt wysoką i rozpoczęło działania zmierzające do automatyzacji procesu rozładunku kontenerów. Zaproponowaliśmy firmie, aby przed zakupem sprzętu dokonać analizy wpływu automatyzacji na efektywność rozładunku procesu.
Przebieg procesu
Prace rozpoczęto od zdiagnozowania przyczyn źródłowych problemu. Dokonano obserwacji procesu oraz zebrano opinie pracowników rozładowujących kontenery. Pierwszą wskazaną przez pracowników przyczyną wysokiej pracochłonności rozładunku była duża różnorodność asortymentu, która w ich opinii znacznie wydłużała czas rozładunku. Pracownicy wskazywali również, że długość ręcznego rozładunku uzależniona jest od masy pudeł znajdujących się w kontenerze. Uznano, że w przypadku procesu wspomaganego mechanicznie taka korelacja nie będzie występowała. Podczas obserwacji procesu zauważono również, że na drugiej zmianie spada wydajność rozładunku. Postawiono hipotezę, że automatyzacja wyeliminuje ten problem.
Aby zweryfikować te przyczyny źródłowe, zorganizowano testy procesu automatyzacji rozładunku. W procesie testowym wykorzystano grawitacyjny podajnik rolkowy. Jeden koniec podajnika wjeżdżał do kontenera, gdzie pracownik ładował na niego kartony. Na drugim końcu podajnika drugi pracownik zdejmował spływające kartony i rozkładał je na paletach. Test opisanego procesu trwał dwa tygodnie. W oparciu o zabrane dane przeprowadzono następnie analizy oraz zbadano, czy wskazane przyczyny nieefektywności zostały wyeliminowane dzięki automatyzacji.
Wnioski z testów – weryfikacja hipotez
W pierwszej kolejności zweryfikowano hipotezę wskazującą, że automatyzacja rozładunku wyeliminuje zależność między liczbą asortymentów w kontenerze a średnim czasem rozładunku kartonu. Na Rysunku 1 przedstawiono wykresy długości rozładunku jednego kartonu w zależności od liczby indeksów w kontenerze dla rozładunku manualnego i automatycznego.
Zarówno dla procesu ręcznego, jak i automatycznego, nie występuje korelacja między liczbą asortymentów w kontenerze, a średnim czasem rozładunku jednego kartonu. Automatyzacja procesu nie wyeliminuje zatem nieefektywonści.
Zweryfikowano również hipotezę dotyczącą wyeliminowania, dzięki automatyzacji procesu, negatywnej zależności czasu rozładunku od masy pudeł znajdujących się w kontenerze. Również w tym obszarze dokonano statystycznej analizy danych, której wyniki przedstawiono na Rysunku 2.
Jak wynika z wykresów, zarówno dla procesu ręcznego, jak i automatycznego, średnia długość rozładunku uzależniona jest od masy kartonów. Oznacza to, że również w tym zakresie automatyzacja nie zwiększy wydajności rozładunku.
Analizom poddano także trzecią hipotezę, według której automatyzacja procesu powinna wyeliminować problem zmniejszonej wydajności rozładunku na drugiej zmianie. Wyniki analiz w tym zakresie przedstawiono na Rysunku 3.
Za pomocą „wykresów świeczkowych” przedstawiono medianę oraz pierwszy i trzeci kwartyl rozkładu czasu rozładunku dla pierwszej i drugiej zmiany. Jak wynika z wykresów, zarówno w procesie ręcznym, jak i automatycznym, wydajność rozładunku spada na drugiej zmianie. Usprawnienia w tym obszarze powinny zatem dotyczyć zmian organizacyjnych, a nie automatyzacji. Podczas testu obliczono również średnią wydajność rozładunku kontenerów. Dla procesu ręcznego wyniosła ona 300 kartonów na godzinę, a dla procesu automatycznego wydajność wyniosła zaledwie 259 kartonów na godzinę.
Wyniki testów wskazują zatem, że wprowadzenie automatyzacji procesu w badanym przypadku spowodowałoby spadek wydajności procesu o ok. 14%. Analiza danych i podejście metodyczne uchroniło przedsiębiorstwo przed błędną inwestycją w podajniki rolkowe. Kierownictwo firmy podjęło decyzję, że prace zmierzające do usprawnienia procesu rozładunku dotyczyć będą aspektów organizacyjnych oraz szkoleń i budowania świadomości personelu.