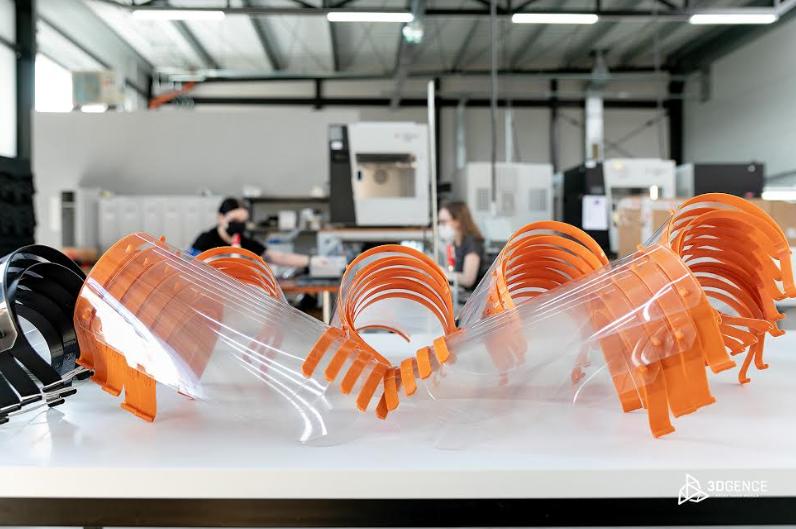
Druk 3D wkroczył do produkcji seryjnej
Przez lata druk 3D traktowany był jako wsparcie procesu produkcyjnego. Wciąż jednak bardzo rzadko korzystano z niego w produkcji seryjnej. Wszystko zmieniło się w czasie pandemii COVID-19. Branży druku 3D bardzo szybko udało się przestawić na produkcję niezbędnego sprzętu dla placówek medycznych. Pokazała tym samym, że wykorzystanie drukarek 3D może dziś z powodzeniem uzupełniać procesy wytwórcze w wielu firmach, w tym również z sektora produkcyjnego.
12000 sztuk przyłbic dla 111 placówek medycznych. W kilka tygodni. Tak polski producent drukarek 3D – 3DGence odpowiedział na potrzeby służby zdrowia.
– W takich sytuacjach kryzysowych, kiedy w hurtowniach zabrakło asortymentu, najważniejsze było, aby zapewnić personelowi medycznemu niezbędne wyposażenie do pracy. Wykorzystanie technologii druku 3D to umożliwia – tłumaczy Andrzej Kukuła, prezes zarządu 3DGence.
Po możliwości tej technologii sięgnęło w czasie pandemii COVID-19 wiele firm. Produkowały w trybie 24/7 elementy wyposażenia medycznego niezbędne lekarzom i pielęgniarkom. Dzięki ich działaniom druk 3D przekroczył granicę między produkcją małoseryjną a seryjną. Kto na tym skorzysta?
Od prototypowania do projektów na życzenie
Początki technologii druku 3D datuje się na wczesne lata 70. XX wieku, co oznacza, że jest ona wykorzystywana już od kilkudziesięciu lat na całym świecie. Od tej pory twórcy pracują nad udoskonalaniem sprzętu i materiałów używanych do wykonywania wydruków. Wraz z wprowadzaniem nowych filamentów i coraz wydajniejszych drukarek rozszerza się też pole zastosowania wytwarzania addytywnego w przemyśle. Coraz więcej przedsiębiorstw decyduje się na wdrożenie drukarki 3D do swojego parku maszynowego, ze względu na szereg korzyści.
Przez długi czas na urządzeniach 3D powstawały prototypy. Tak jest zresztą do dziś. Firmy budują je i udoskonalają na bieżąco, eliminując pojawiające się błędy. Ponieważ robią to na miejscu i wykorzystując własne materiały, cały proces jest szybszy i przede wszystkim tańszy niż w przypadku współpracy z zewnętrznymi dostawcami. Co ważne, nie wymaga zajmowania linii produkcyjnych, a to zapobiega przestojom i wysokim kosztom.
Nie dziwi zatem, że firmy przemysłowe zaczęły wykorzystywać go również do produkcji elementów końcowych. Najpierw do wytwarzania na miejscu części zamiennych do maszyn i linii produkcyjnych. Dzięki temu mogą zmniejszyć nakłady przeznaczane na przechowywanie takich części. Uniezależniają się też od zewnętrznych dostawców. Dzięki drukowi 3D wyeksploatowane czy zepsute elementy maszyn można szybko zastąpić wydrukowanymi na miejscu odpowiednikami, które mogą służyć firmie, gdy czeka ona na dostawę z innego kraju. Technologia 3D pozwala w tym przypadku na znaczne oszczędności czasu i pieniędzy. Korzystają z niej w taki sposób przede wszystkim przedsiębiorstwa z branży automotive, między innymi Opel, ale też firma z sektora AGD, czyli Electrolux.
Co ciekawe, druk 3D umożliwia także personalizowanie produktów i dopasowywanie ich do potrzeb poszczególnych klientów. Po to zastosowanie technologii sięga znów branża automotive. Właściciele Mini Cooperów od BMW mogą się dzięki temu cieszyć z samochodów, których wygląd dokładnie odwzorowuje ich oczekiwania.
W 5 dni do sukcesu, czyli szybka produkcja seryjna na wyciągnięcie ręki
Druk 3D nie mógł jednak zatrzymać się tylko na prototypach, częściach zamiennych czy produkcji małoseryjnej. Wciąż jednak brakowało spektakularnych przykładów zastosowania tej technologii w produkcji na większą skalę. Sytuację zmieniła pandemia COVID-19. Postępujące problemy służby zdrowia sprawiły, że świat zaczął szukać rozwiązań dostępnych od ręki, gwarantujących dokładność i szybkość działania.
– W momentach trudnych i nieprzewidywalnych, takich jak pandemia, liczy się przede wszystkim elastyczność biznesu i produkcji, czyli umiejętność jak najszybszego dostosowania się do nowych warunków. Druk 3D okazał się doskonałym przykładem takiej elastyczności – mówi Adam Przepolski, kierownik działu usług 3D, 3DGence. – W związku z ogromnym zapotrzebowaniem na sprzęt ochrony osobistej zaprojektowaliśmy prototyp elementu przyłbic i w przeciągu dwóch dni skompletowaliśmy resztę potrzebnych części do montażu. Następnie skontaktowaliśmy się z jednym ze szpitali z prośbą o to, aby przetestował nasze przyłbice. Przeanalizowaliśmy uwagi od personelu medycznego i wprowadziliśmy konieczne poprawki do prototypu. Dzięki temu w zaledwie pięć dni od zgłoszenia zapotrzebowania przygotowaliśmy i przetestowaliśmy prototyp oraz rozpoczęliśmy seryjną produkcję sprzętu dla lekarzy.-
Produkcja taka polega na wykonywaniu dużej liczby jednakowych wyrobów według tej samej technologii. Druk 3D może być już alternatywą do konwencjonalnych metod produkcji. Kluczowe w tym przypadku jest przygotowanie kodu maszynowego, który umożliwi wykonanie modelu 3D w jak najkrótszym czasie. Każdy produkt może przejść taką optymalizację i zostać dostosowany do seryjnej produkcji przy wykorzystaniu druku 3D.
– Aby móc wyprodukować jak najwięcej elementów wykorzystywanych w montażu przyłbic ochronnych, dział R&D w 3DGence zoptymalizował wydruk 3D za pomocą programów do projektowania CAD oraz w pełni wykorzystał możliwości oprogramowania 3DGence SLICER 4.0. Optymalizacja wydruku 3D umożliwia wyprodukowanie w 25 minut dwóch elementów przyłbicy umieszczonych na stole jednej drukarki 3D – 3DGence DOUBLE P255 – tłumaczy Adam Przepolski z 3DGence.
3DGence rozpoczął produkcję sprzętu dla medyków we własnym parku maszynowym, wyposażonym w kilkadziesiąt maszyn do wytwarzania addytywnego. Do wykonywania elementów przyłbic eksperci firmy wykorzystali 32 profesjonalne drukarki 3D – DOUBLE P255, które zostały przezbrojone i przygotowane do produkcji seryjnej tak, by dostarczać wydruki wymaganej jakości w krótkim czasie. Zespół 3DGence pracował na dwie zmiany. W ciągu dwóch tygodni udało się wyprodukować 12 000 przyłbic, które trafiły do 111 placówek medycznych.
Jakość na pierwszym miejscu
Produkcja na większą skalę wymaga zastosowania dobrych jakościowo urządzeń. Warto pamiętać o tym, że na rynku można dziś znaleźć mniejsze, desktopowe drukarki 3D oraz maszyny przemysłowe. Te drugie dostosowane są do potrzeb większych procesów produkcyjnych. Przede wszystkim wykonane są z bardzo wysokiej jakości materiałów i podzespołów. Dzięki temu gwarantują odpowiednią wydajność i dokładność druku. Producenci takich drukarek 3D oferują też swoim klientom przetestowane, certyfikowane filamenty kompatybilne z urządzeniami, a także gotowe profile materiałowe, z których można korzystać w procesie druku. To wszystko przekłada się na doskonałą jakość wizualną i wymiarową wydruków.
Profesjonalne, przemysłowe drukarki 3D zwykle mają większą powierzchnię druku. To pozwala na wytwarzanie sporych elementów. Użytkownicy takiego sprzętu otrzymują również od producenta wsparcie ekspertów. Ich wiedza, doświadczenie i rady mogą okazać się szczególnie pomocne zwłaszcza na początku pracy z drukarką 3D.
Odpowiedni sprzęt, coraz wytrzymalsze materiały oraz wciąż poszerzająca się wiedza na temat możliwości druku 3D mają szansę doprowadzić do prawdziwej rewolucji w przemyśle. Szybka i elastyczna produkcja na dużą skalę jest już możliwa. Co więcej, pozwala uniezależnić się od zewnętrznych dostawców, co jest szczególnie istotne w przypadku zamknięcia granic czy ograniczeń w transporcie.
– Do niedawna technologia druku 3D w przemyśle stosowana była przede wszystkim w procesie szybkiego prototypowania modeli. Dzisiaj drukarki 3D wykorzystywane są do wspierania procesów produkcji, wykonywania funkcjonalnych części czy niezbędnych narzędzi. Co więcej, na przykładzie wydrukowanych elementów przyłbic pokazujemy, że technologia wytwarzania addytywnego może być już śmiało wykorzystywana do produkcji seryjnej – podsumowuje Łukasz Lipiec, Technical Sales Support Engineer w 3DGence.
Pandemia COVID-19 wpłynęła na firmy na całym świecie. Zmienił się nie tylko system pracy, ale i podejście do wprowadzania nowych rozwiązań. Dziś liczą się technologie, które zapewniają elastyczność. Druk 3D udowodnił, że może wspierać proces produkcji nawet w dużej skali i pozwala efektywnie i szybko dostosować się do nowych warunków.