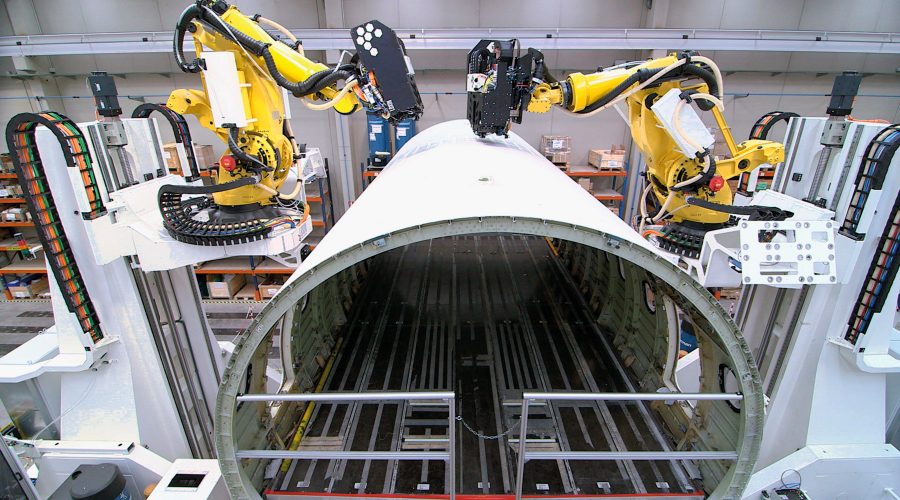
Robotyzacja złożonych procesów produkcyjnych
Branża lotnicza stawa najwyższe wymagania dotyczące jakości wykonywanych procesów. Automatyzacja produkcji dzięki wysokiej powtarzalności oraz dokładności realizowanych operacji stanowi odpowiedź na potrzeby producentów. Jednak wraz ze wzrostem wydajności, pojawiają się kolejne wyzwania.
Roboty przemysłowe obracają się tysiące razy w kilku osiach, w ciągu jednego dnia, jednocześnie nitując kadłuby samolotów. Jest to test skrajnych warunków pracy dla przewodów do przesyłu danych, pneumatycznych oraz energetycznych. Aby wytrzymać te ruchy, hiszpański producent Loxin opiera się na prowadnikach przewodów wykonanych z wysokowydajnego tworzywa sztucznego, opracowanych przez firmę igus.
Brakowało dokładności
Pasażerowie myślą o wielu rzeczach podczas lotu na swoje letnie wakacje. Myślą o relaksie, plaży i koktajlach. Jednak niewielu myśli o nitach, o niepozornych elementach złącznych, które bezpiecznie spajają razem części kadłuba samolotu. W zadaniu, które trwa tygodnie, wykwalifikowani pracownicy wbijają nity w metalowe kadłuby ważące kilka ton. Czy automatyzacja tej pracochłonnej czynności nie była możliwa? Z pewnością była wskazana, ale przez długi czas niemożliwa, ponieważ roboty nie były wystarczająco dokładne. Aby dotrzeć do każdego punktu kadłuba, potrzebowały więcej niż tylko elastyczności. Musiały także opanować kilka kroków roboczych – od wiercenia i frezowania po nitowanie. Z precyzją 0,2 milimetra.
Dzięki robotom udało się zautomatyzować proces nitowania. Wieloosiowe roboty hiszpańskiej firmy Loxin pracują w dziale produkcyjnym dużego producenta samolotów. Po lewej i prawej stronie obok podniesionego kadłuba. Roboty są zamontowane na platformach, które można podnieść do wysokości kilku metrów za pomocą podnośników – podobnie jak wózek widłowy (Rysunek 1). Ciężkie roboty ważące tony, docierają na odpowiednią wysokość i przesuwają się do punktu pracy z dokładnością co do milimetra, na sześciu osiach. Wiercą otwory w metalu, frezują wgłębienie na główkę nitu, odkurzają pył, nakładają szczeliwo i ustawiają nity.
W zależności od sekcji kadłuba roboty muszą stale zmieniać kąty oraz średnice podczas wiercenia, frezowania i nitowania. Ale ta elastyczna wielozadaniowość nie była jedyną przeszkodą, którą Loxin musiał pokonać podczas opracowywania tego rozwiązania.
Wytrzymałość na skomplikowane ruchy
Inżynierowie musieli zaprojektować roboty, aby były naprawdę elastyczne. Sześć osi służy do przemieszczania głowicy do dowolnej części kadłuba. Problem zasilania jest równie skomplikowany. Narzędzia na efektorze końcowym robota są podłączone do wielu przewodów energetycznych, pneumatycznych i transmisji danych. Przewody te muszą perfekcyjnie podążać za wykrzywionymi ruchami ramienia, nawet przy dużej prędkości – bez ocierania się o siebie ani uderzania o wrażliwą powierzchnię kadłuba. W przeciwnym razie dochodzi do długich przestojów spowodowanych przerwaniem przewodu i uszkodzeniem samolotu.
W poszukiwaniu niezawodnego systemu zasilania Loxin porównał systemy kilku producentów – Przez długi czas nie mogliśmy znaleźć solidnego i niezawodnego rozwiązania – wspomina Unai Martínez, główny inżynier w Loxin. – Liczba przewodów i masa stanowiły problem. Loxin eksperymentował z peszlami. Ze względu na szybkie zużycie wynikające z tarcia łatwo się zrywały. W życiu codziennym uszkodzenie materiału oznaczałoby zastąpienie całego peszla, w tym usunięcie przewodów na głowicach. W najgorszym przypadku spowodowałoby to zatrzymanie produkcji na kilka dni.
Zabezpieczone przewody
Loxin w końcu znalazł to, czego szukał w Niemczech. W firmie igus, specjaliście od motion plastics z Kolonii, który od dziesięcioleci opracowuje prowadniki kablowe. Asortyment obejmuje między innymi serię triflex. Są to ochronne tuby podobne do węży, wykonane z odpornego na zużycie tworzywa sztucznego o wysokiej wydajności, które podążają nawet za najbardziej skomplikowanymi, trójwymiarowymi ruchami robotów przemysłowych. Wewnątrz, przewody transmisji danych, pneumatyczne i zasilające są bezpiecznie zamocowane oraz zabezpieczone przed zużyciem. – Przewody są chronione przed naprężeniami mechanicznymi z powodu rozciągania, skręcania i rozszerzania. Ta ochrona jest szczególnie ważna, gdy głowice robota zajmują skrajną pozycję – wyjaśnia Unai Martínez.
Aby zapewnić, że e-prowadniki zamontowane po prawej i lewej stronie ramienia poruszają się jak najbliżej ramienia i nie uderzają w samolot, Loxin używa systemu odciągu. Jeśli ramię robota powróci do swojego pierwotnego położenia po ruchu, mechaniczny system cofa prowadnik – a okrągłe uchwyty, które są zamontowane na ramieniu, zapewniają bezpieczne prowadzenie. Ramię robota ma pełną swobodę ruchów, nie ocierając się o siebie ani nie tworząc pętli. Loxin był również w stanie osiągnąć lepszą mobilność robotów, co może teraz uprościć ich pracę wokół kadłuba samolotu, a to z kolei oszczędza cenny czas montażu.
Ruchy okrężne 540°
Na ramieniu robota zastosowano prowadnik, który chroni przewody od podstawy ramienia robota do pierwszej osi. Prowadnik porusza się w rynnie prowadzącej. Jeśli ramię robota obraca się, prowadnik składa się, podczas gdy górny bieg spoczywa na dolnym biegu. Prowadnik umożliwia ruch obrotowy do 540° przy prędkościach do 1 m/s. Ponieważ jest wykonany z wysokowydajnych tworzyw sztucznych, to charakteryzuje się bardzo dobrą odpornością na zużycie. Testy w laboratorium testowym firmy igus wykazały, że żywotność e-prowadnika wynosi ponad milion cykli.
– Jesteśmy bardzo zadowoleni z rozwiązania, ponieważ nasze zakłady mają teraz mniej przestojów – podsumowuje Unai Martínez z Loxin. Firma igus jest również zadowolona z tej niezwykłej referencji. Loxin został nagrodzony vectorem 2018 za ambitne rozwiązanie w zakresie zasilania. Konkurs ten jest organizowany przez igus co dwa lata, a jej zwycięzcy są wybierani przez niezależne jury.