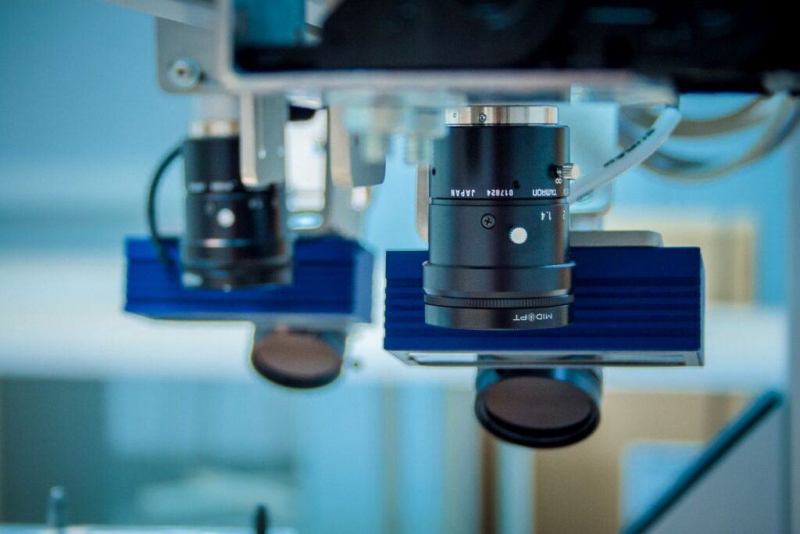
Rosnąca doskonałość systemów wizyjnych
Wielu producentów nadal nie stosuje zautomatyzowanej kontroli jakości. Tymczasem, niestety, poleganie na ręcznej kontroli jakości często nie zapewnia oczekiwanych efektów. To monotonna praca, a wykonywana pod presją czasu prowadzi do wszelkiego rodzaju błędów – m.in. spowodowanych rozproszeniem uwagi i zmęczeniem. Te z kolei mogą prowadzić do zwracania produktów, a nawet – negatywnie oddziaływać na reputację firmy. Jak temu zapobiec? Wdrażając systemy wizyjne.
Automatyzacja rozwija się wraz z rozwojem przemysłu, a przemysł – wraz z rozwojem automatyzacji. Siła robotów od dawna jest wykorzystywana m.in. na liniach montażowych, gdzie ich ogromna moc przekracza ludzkie ograniczenia. Jednak firmy odkrywają, że roboty można wykorzystać nie tylko do pokonywania ludzkich ograniczeń fizycznych, ale także umysłowych. Wzrok jest jednym z najbardziej zaawansowanych zmysłów człowieka. Dlatego systemy wizyjne (w skrócie MVS, od Machine Vision Systems) wzorują się na ludzkim oku, ale są od niego – w pewnych aspektach – doskonalsze. Te szyte na miarę rozwiązania, przeprowadzające kontrolę jakości na linii produkcyjnej lub w magazynie, osiągają maksimum skuteczności.
Błądzić jest rzeczą ludzką
Ludziom tradycyjnie powierza się kontrolę jakości, ponieważ wymaga ona osądu. Człowiek może z łatwością ocenić, czy np. dana butelka jest odpowiednio wypełniona. Jednak interesująca rzecz dzieje się, gdy sprawdza nie jedną butelkę, ale tysiące butelek poruszających się z dużą prędkością wzdłuż linii rozlewniczej. Po wielokrotnym zobaczeniu „właściwego” obrazu, kiedy człowiek widzi kilka butelek o odpowiednim poziomie napełnienia, a następnie spostrzega taką, która jest w połowie pusta, mózg może użyć „nadrukowanego” obrazu pełnej butelki i nie zarejestrować problemu. – Systemy wizyjne, w których system kamer rejestruje obrazy i analizuje je dzięki odpowiednim algorytmom, pokonuje to ludzkie ograniczenie. Człowiek po prostu nie jest tak idealnie przystosowany do powtarzalnych zadań jak maszyna. – zauważa Jakub Rudner, menedżer ds. Rozwoju Nowych Technologii w Etisoft. – Mimo, że coraz więcej producentów jest tego świadomych, systemy wizyjne nadal nie są rozwiązaniem stosowanym na szeroką skalę. – dodaje ekspert.
W pełni zautomatyzowana kontrola na straży jakości
Jak podaje portal industryweek.com, badania kontroli jakości prowadzone od lat 70. XX wieku do chwili obecnej, wskazują, że dokładność kontroli wykonanej przez człowieka wynosi do 80%. Nadal pozostaje więc margines błędu na poziomie 20%. Tymczasem systemy wizyjne – w ramach swoich zastosowań – są skuteczne w niemal 100%. Co to oznacza? Po pierwsze pozwalają uniknąć wszystkich pomyłek związanych z subiektywną i obarczoną błędem oceną dokonywaną przez pracownika. Mogą badać najbardziej szczegółowe kształty dowolnego obiektu i być w równym stopniu skupione na każdym z nich, nawet jeśli są ich tysiące. Po drugie, dzięki systemom wizyjnym zwiększa się ogólna prędkość produkcji. Automatyzacja procesów kontroli jakości oznacza przeprowadzenie wielu inspekcji na linii produkcyjnej z bardzo dużą prędkością – wielokrotnie szybciej niż dokonałby tego jakikolwiek zespół inspekcyjny. Po trzecie, zautomatyzowana kontrola jakości odbywa się w ramach ustalonych zakresów tolerancji. Z kolei automatyczne dokumentowanie całego procesu pozwala na powiązanie danych (zdjęć danych liczbowych) z dokumentacją, numerem seryjnym, partią produkcyjną – z wszystkim, co powinno podlegać kontroli jakości.
Przewaga dzięki automatyzacji
Dzięki sztucznej inteligencji (AI) oprogramowanie stosowane w systemach wizyjnych z pewnością będzie się stawać coraz doskonalsze. Koło zębate można łatwo zidentyfikować za pomocą tradycyjnego oprogramowania wizyjnego, ponieważ ma określony kształt z minimalnymi zmianami. A co z przedmiotami, których wygląd może się znacznie różnić? – Mając wystarczająco duży zbiór danych, systemy sztucznej inteligencji mogą uczyć się wzorców w taki sposób, aby sprostać i takiemu wyzwaniu. – tłumaczy Jakub Rudner z Etisoft. Systemy wizyjne, niestrudzenie sygnalizując problemy, „uwalniają” inspektorów do robienia tego, co ludzie robią najlepiej – rozwiązywania problemów. Dzięki MVS jesteśmy w stanie zwiększyć wydajność, produkcję, a także bezpieczeństwo w każdym zakładzie.