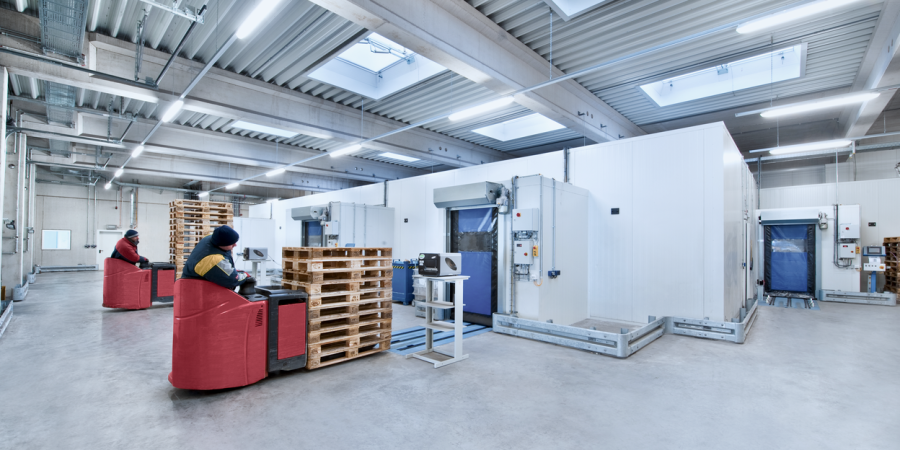
Automatyczny magazyn w logistyce mięsnej
Rynek mrożonek mięsnych wykazuje dynamiczny wzrost rok do roku, co z kolei generuje rosnące zapotrzebowanie na odpowiednie moce produkcyjne i magazynowe w całym łańcuchu dostaw. Infrastruktura niezbędna do obsługi tego rynku wymaga wydajnych, zautomatyzowanych systemów intralogistycznych, które gwarantują maksymalną efektywność i dostępność operacyjną.
Polska należy do czołowych producentów mięsa w Europie. Całkowita wartość sektora mięsnego w 2023 roku wyniosła ponad 100 miliardów złotych, co odpowiada około 23 miliardom euro (źródło: Der Markt für Fleisch in Polen, Bundesministerium für Ernährung und Landwirtschaft, Bonn). Według danych z serwisu Statista, wartość sprzedaży przetworzonego mięsa w Polsce w 2024 roku wyniesie około 4,85 mld euro. Dla porównania, globalny rynek mięsa przetworzonego wygeneruje wartość około 630 mld euro w tym samym okresie (źródło: Markt für verarbeitetes Fleisch, Fortunebusinessinsights.com).
Największy udział w rynku ma mięso mrożone – ponad 70% (Źródło: Markt für verarbeitetes Fleisch, Fortunebusinessinsights.com). Popularność mrożonek wynika głównie z ich łatwości w przechowywaniu i transporcie. Mrożone mięso ma dłuższy termin przydatności do spożycia i mniejsze ryzyko mikrobiologicznego skażenia niż świeże produkty. Sieci handlowe często wykorzystują je do produkcji żywności, ponieważ jest ono łatwo dostępne i wygodne w użyciu. Młodsze pokolenie konsumentów preferuje pakowane mrożonki mięsne, które można łatwo kupić i szybko przygotować, bez konieczności dalszej obróbki.
Atrakcyjny insourcing
Wzrastające ceny usług transportowych i magazynowych w sektorze logistyki mrożonek i świeżej żywności, spowodowane deficytem zasobów oraz rosnącymi kosztami pracy i energii, sprawiają, że coraz bardziej opłacalne stają się inwestycje w wewnętrzne, czyli wydajne systemy oparte na insourcingu. Rozwiązania takie jak kompaktowe systemy składowania kanałowego, regały przesuwne czy wysokiego składowania o wysokości do 45 metrów, wspierane przez automatyczne układnice, pozwalają na maksymalizację efektywności przestrzennej nawet w ograniczonych powierzchniowo magazynach.
Mroźnia wysokiego składowania stanowi centralny element zautomatyzowanych systemów logistycznych. Zapewnia wymaganą przestrzeń magazynową, a zainstalowane w niej układnice gwarantują szybkie i niezawodne składowanie oraz pobieranie towarów przez całą dobę (24/7). Ponadto magazyny buforowe w strefie towarów wychodzących mogą dodatkowo sekwencjonować kompletne ładunki, przyspieszając załadunek ciężarówek i minimalizując czas, jaki palety z mrożonkami spędzają w strefach klimatyzowanych.
Połączone systemy przenośników oraz inteligentne oprogramowanie sterujące, które współgra z systemem ERP, są kluczowe dla sprawnego zarządzania procesami. System zarządzania magazynem (WMS) odgrywa tutaj centralną rolę, odpowiadając za zarządzanie danymi, datami przydatności, identyfikowalnością partii oraz optymalizacją procesów kompletacji i wydawania towarów.
Podczas budowy nowej mroźni wysokiego składowania należy wziąć pod uwagę kilka kluczowych kwestii:
- zużycie energii
- nakład siły roboczej
- wyższe wymagania technologiczne, izolacyjne i przeciwpożarowe
- rosnąca różnorodność pojemników o zróżnicowanych wymaganiachw zakresie ich obsługi
Rosnące zróżnicowanie
Starannie zaprojektowany projekt determinuje długoterminowe koszty operacyjne, w których istotną rolę odgrywają koszty energii. Szczególną uwagę należy zwrócić na strefy przejściowe między różnymi obszarami magazynowymi. Warto rozważyć zastosowanie śluz, ponieważ podczas przechowywania i pobierania produktów z mroźni dochodzi do znacznych strat energii. Dotyczy to zwłaszcza stref obsługiwanych ręcznie, co wpływa nie tylko na koszty, ale także na jakość przechowywanych towarów.
Dobrze zaprojektowane rozwiązanie pozwala zminimalizować zużycie energii bez przerywania łańcucha chłodniczego. Niezależnie od producenta, solidna koncepcja budowy nowego magazynu głębokiego mrożenia zawsze zaczyna się od rozplanowania procesów i ich organizacji. Na tej podstawie określa się następnie konstrukcję budynku oraz przejścia między obszarami o różnych temperaturach. W kolejnym etapie definiuje się parametry urządzeń klimatyzacyjnochłodniczych, a także regałów wysokiego składowania, układnic i przenośników. Uzupełnieniem projektu jest dobór systemu kompletacji oraz oprogramowania do sterowania procesami.
Podstępna kondensacja
Zachowanie ciągłości łańcucha chłodniczego jest kluczowym wymogiem w magazynowaniu mrożonek. Produkty nie mogą ulegać rozmrożeniu ani pokrywać się kryształkami lodu, co mogłoby świadczyć o przerwaniu ciągu chłodniczego. Wysoka wilgotność powietrza powoduje kondensację pary wodnej na powierzchni produktów, co zakłóca zautomatyzowane procesy kompletacji i uniemożliwia bezpieczne pozycjonowanie jednostek towarowych.
Zgodnie z normami HACCP zalecana temperatura w magazynach głębokiego mrożenia wynosi minimum -18 °C. W praktyce, szczególnie w sektorze logistycznym, panują tam temperatury od -30 °C do -18 °C, co generuje wysokie koszty energii, szczególnie latem. Dlatego projektowanie magazynów powinno uwzględniać minimalizację tych kosztów poprzez zastosowanie zwartej konstrukcji budynku i oszczędności przestrzeni, co jest szczególnie efektywne w zautomatyzowanych magazynach. Konstrukcja budynku powinna także ograniczać powierzchnię promieniowania cieplnego, przy jednoczesnym uwzględnieniu połączenia z istniejącymi obiektami.
Śluzy termiczne zapobiegające oblodzeniu
Przejścia między różnymi strefami magazynowymi wymagają skutecznej izolacji. Ograniczenie liczby punktów styku oraz szybkie i krótkie otwieranie drzwi czy bram minimalizują straty energii. Zaleca się instalację bram szybkobieżnych, kurtyn powietrznych lub śluz termicznych.
Powietrze w magazynach głębokiego mrożenia jest znacznie bardziej suche niż w cieplejszych strefach, co powoduje ryzyko oblodzenia w strefach przejściowych. Zastosowanie śluz termicznych z ogrzewaniem podłogowym i ściennym skutecznie eliminuje ten problem, zapewniając płynność procesów logistycznych.
Kluczowe aspekty projektowania magazynów głębokiego mrożenia
Przy projektowaniu magazynów głębokiego mrożenia należy uwzględnić następujące czynniki:
- Zwarta konstrukcja budynku i unikanie zbędnych przestrzeni.
- Minimalizacja liczby przejść oraz zastosowanie śluz termicznych.
- Instalacja bram szybkobieżnych i kurtyn powietrznych.
- Wykorzystanie materiałów i technologii odpornych na niskie temperatury.
- Optymalizacja przepływu zimnego powietrza w odniesieniu do konstrukcji regałów i przechowywanych towarów.
- Uwzględnienie promieniowania cieplnego emitowanego przez silniki i przetwornice częstotliwości.
- Ergonomiczne stanowiska pracy dla kompletacji ręcznej.
- Ułatwienie serwisowania i napraw dzięki zastosowaniu połączeń wtykowych i śrubowych.
- Przestrzeganie przepisów przeciwpożarowych dla magazynów chłodniczych i mroźniczych.
Kluczowe znaczenie ma także odpowiednie zaprojektowanie i zwymiarowanie technologii chłodniczej. Warto już na wczesnym etapie projektu zaangażować specjalistę, który uwzględni wszystkie istotne czynniki, takie jak lokalizacja parowników odpowiedzialnych za rozprowadzanie chłodnego powietrza oraz dostępność przestrzeni wokół nich.
Odporność urządzeń na niskie temperatury
Elementy mechaniczne, takie jak silniki, napędy, smary i uszczelnienia, muszą być dostosowane do pracy w ekstremalnie niskich temperaturach. Elektronika magazynu, w tym bariery świetlne i szafy sterownicze, wymaga podgrzewania, aby działała prawidłowo.
Kwestie ochrony przeciwpożarowej również wymagają szczególnej uwagi. Standardowe systemy gaśnicze, takie jak woda, są niewystarczające w niskich temperaturach. W takich przypadkach należy zastosować tryskacze z płynem niezamarzającym lub systemy zapobiegające pożarom poprzez redukcję poziomu tlenu w pomieszczeniach.
Łatwość serwisowania
Zastosowanie połączeń wtykowych i śrubowych ułatwia serwisowanie i minimalizuje ryzyko przestojów, co jest kluczowe w sektorze mrożonek, gdzie magazyny często pracują w systemie trzyzmianowym. Dzięki temu konserwacja jest szybsza i bardziej efektywna, a magazyn pozostaje dostępny nawet podczas napraw.
Ergonomia stanowisk obsługiwanych ręcznie
W miejscach, gdzie ręczna kompletacja jest nieunikniona, konieczne jest stworzenie ergonomicznych stanowisk pracy, które minimalizują obciążenie pracowników pracujących w ekstremalnie niskich temperaturach. Systemy sterowane światłem lub głosem ograniczają liczbę błędów, zwiększając jednocześnie produktywność. Automatyzacja procesów logistycznych zmniejsza również zapotrzebowanie na pracę ręczną w trudnych warunkach.
Korzyści z automatyzacji – referencje klientów
Zautomatyzowane mroźnie magazynowe umożliwiają efektywne monitorowanie produktów i utrzymanie stałej temperatury. Kompaktowe systemy chłodzenia redukują koszty operacyjne, jednocześnie zwiększając możliwości przechowywania.
Przykładem firmy oferującej kompleksowe rozwiązania w zakresie automatyzacji jest Kardex Mlog, posiadająca ponad 50-letnie doświadczenie w projektowaniu i utrzymaniu systemów logistycznych. Ich układnice paletowe działają w ponad 3000 instalacjach na całym świecie, zapewniając klientom niezawodność i efektywność. Kompleksowa realizacja magazynu trwa zazwyczaj 12–15 miesięcy, a modernizacje istniejących obiektów są znacznie szybsze i mniej czasochłonne.