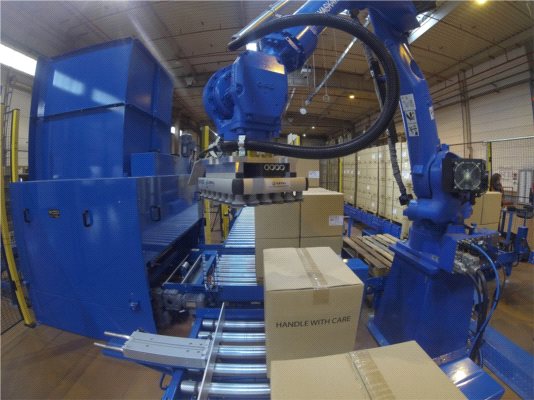
Budowanie łańcucha dostaw przyszłości
Najlepszą metodą przewidywania przyszłości jest jej tworzenie. Dlatego w laboratoriach FM Logistic już dzisiaj toczą się prace na innowacyjnymi rozwiązaniami, technologiami i projektami, które pozwalają firmie na zaoferowanie bardziej elastycznego podejścia do potrzeb klientów:...
Inwestycja w innowacje jako element strategii
Droga od pomysłu do wdrożenia innowacji jest dość długa. Często jest to proces zajmujący wiele lat. A to oznacza dość spore koszty dla organizacji. Po pierwszym etapie określenia potrzeb następuje poszukiwanie koncepcji rozwiązania zaistniałego problemu i zbieranie pomysłów. Każdy z nich musi później zostać poddany szerokiej weryfikacji pod kątem wykonalności. Tylko najlepsze koncepcje mają szansę na wejście w fazę tworzenia prototypów, które będą testowane również w realnych warunkach biznesowych i w konkretnych lokalizacjach, np. magazynach dedykowanych klientowi, dla którego zaprojektowano dane rozwiązanie. Nawet, gdy docelowy projekt zostanie już wybrany, pozostaje jeszcze etap jego komercjalizacji i wdrożenia.
– Dlatego tylko przygotowane organizacje mogą z powodzeniem prowadzić tego typu projekty – mówi Patrick Bellart, dyrektor ds. innowacji technologicznych i automatyki w FM Logistic, odpowiedzialny za poszukiwanie i wdrażanie nowoczesnych rozwiązań korzystnych dla biznesu. – W strukturach firmy na całym świecie wyodrębniliśmy 15 zespołów badawczo-rozwojowych. Dodatkowo powołaliśmy 12 lokalnych menedżerów. Przeznaczyliśmy także budżet na projekty innowacji technologicznych. To wszystko pozwala nam efektywnie zarządzać procesem projektowania i wdrażania nowoczesnych rozwiązań w całej organizacji – dodaje.
Na pozycję rynkową firm logistycznych coraz częściej wpływa wdrażanie nowoczesnych i innowacyjnych technologii, które pozwalają na skracanie czasu realizacji zamówień i rozwiązują problem stale rosnących kosztów pracy. W dzisiejszych czasach to jedyny skuteczny sposób na utrzymanie konkurencyjności. Innowacyjne podejście doceniają klienci i otoczenie biznesowe. Poszukiwanie nowych rozwiązań, często dedykowanych konkretnym klientom, stało się więc stałym elementem strategii działania operatorów logistycznych. Innowacyjne rozwiązania w logistyce stają się powoli wizytówką firm.
Innowacyjni pracownicy
Cennym źródłem nowatorskich pomysłów są pracownicy. To oni, często jako pierwsi, zgłaszają potrzebę zmian. Firma FM Logistic postanowiła te inicjatywy wykorzystać. Powstał konkurs, którego celem jest wyróżnienie tych pomysłów, dzięki którym udoskonalane są konkretne procesy i codzienne czynności w bieżącej pracy poszczególnych oddziałów na całym świecie. Ocenie podlegają m.in. oryginalność zgłaszanego projektu, łatwość wdrożenia, wpływ na osiągane wyniki finansowe i wydajność, poprawa komfortu pracowników, a także redukcja zużycia materiałów i energii. Konkurs Continuous Improvement został ogłoszony w styczniu 2017 roku i przebiegał w kilku etapach. Od lutego do lipca wyłaniani byli reprezentanci poszczególnych platform (centrów) logistycznych. Polskie eliminacje krajowe rozegrano 13 września 2017 roku na terenie centrum w Bronisławowie. Zwycięskie zespoły projektowe zostały zaproszone do siedziby firmy w Roissy (Francja), gdzie odbył się wielki finał. W pierwszej edycji zwyciężył zespół pracowników FM Logistic z Polski, który opracował i wdrożył z powodzeniem nadstawę FM DualFrame.
Potrzeba matką wynalazku – to znane powiedzenie sprawdziło się i tym razem. To potrzeby klienta stały za opracowaniem i wdrożeniem nagrodzonego rozwiązania.
– Początek prac nad projektem FM DualFrame to maj 2016 roku. Chcieliśmy znaleźć rozwiązanie, które pomoże nam w pokonaniu problemu jednego z naszych głównych klientów, jakim były niemieszczące się w samochodach palety z towarami – opowiada Tomasz Sęk, kierownik ds. projektów w centrum logistycznym w Wolborzu. – Badaliśmy dostępne na rynku rozwiązania, jednak nie spełniały one naszych oczekiwań. Przystąpiliśmy więc do pracy nad własnym. Na platformie w Wolborzu powstały pierwsze prototypy specjalnych ram, dzięki którym można na jedną nieregularną paletę towarów nadstawić drugą – dodaje.
FM DualFrame to projekt przynoszący dzisiaj konkretne korzyści firmie i jej klientom. Dzięki niemu udało się m.in. zmniejszyć o 26% ilość przejechanych kilometrów, zmniejszyć zużycie paliwa, o 5% ograniczyć emisję CO2, a także zredukować o 5% koszty transportu po stronie klientów i ograniczyć o 4% uszkodzenia przewożonych towarów. Nadstawy mogą być wyposażone w urządzenia GPS, które ułatwiają zarządzanie ich obrotem pomiędzy centrami firmy i punktami dostaw towarów. Dzięki temu, że w składzie zespołu projektowego znalazł się przedstawiciel działu prawnego, zabezpieczona została strona prawna projektu. FM DualFrame został zgłoszony do Urzędu Patentowego RP. Uzyskał też certyfikat Europejskiej Gwarancji Najwyższej Jakości. Trwają także prace nad uzyskaniem znaku CE.
Kierunek: automatyzacja i elastyczność
Można by powiedzieć, że wystarczy wyposażyć centra logistyczne w odpowiednią liczbę robotów i systemów komputerowych, które już samodzielnie obsłużą kolejne transporty towarów. Nie jest to jednak takie proste. Z jednej strony wydaje się, że powtarzalność wykonywanych na terenie centrów logistycznych operacji: rozładunku, magazynowania, załadunku jest łatwa do opanowania przez obecne na rynku urządzenia i roboty. Okazuje się jednak, że tak łatwo nie jest. O ile występuje powtarzalność wykonywanych czynności, o tyle trudność sprawia przede wszystkim fakt, że za każdym razem mamy do czynienia z innym towarem, który im podlega. A to oznacza, że potrzebujemy coraz to innych robotów i systemów, które będą umiały poradzić sobie z ich obsługą. To z kolei wiąże się z dużymi kosztami. Dlatego ważne jest, by nowe rozwiązania cechowała elastyczność zastosowania w różnych operacjach dla wielu różnych klientów.
– Najlepszym przykładem jest wybór robotów. Tutaj pojawia się taki sam dylemat. Albo mamy roboty przemysłowe, które są zazwyczaj wydajne przy stosowaniu ich do odpowiedniego typu kartonu, do odpowiedniej aktywności. Są one dobrym rozwiązaniem w sytuacji, gdy dopasujemy urządzenie do produktu – przekonuje Patrick Bellart. – Koszty jednostkowe będą wtedy niskie. Z drugiej strony mamy roboty mobilne, tzw. kolaboracyjne, które są zazwyczaj bardziej wszechstronne. Można je przestawić np. na krótkie serie. Po czym są one używane do innej operacji, co jest dość częstą praktyką w logistyce. Łatwość ich zastosowania polega również na skalowalności. Stawiam najpierw jedno urządzenie, później w miarę zwiększania kontraktu drugie, trzecie. Gdy klient zmienia swój plan, można odjąć jedno urządzenie i przeznaczyć do obsługi innego klienta. Dla nas, jako operatora, taka sytuacja jest idealna – dodaje.
Innym istotnym czynnikiem jest automatyzacja procesów logistycznych. Dzięki niej doskonalone są operacje logistyczne, skracany jest czas poszczególnych operacji oraz ogranicza się udział ludzi w niektórych procesach, a tam, gdzie nie jest to możliwe, automatyzacji podlegają najbardziej uciążliwe i najtrudniejsze prace. Przykładem mogą być automatyczne systemy inwentaryzacji, ale także rozwiązania w postaci zupełnie nowych, specjalnie opracowanych systemów i robotów np. do rozcinania opakowań zbiorczych.
Same plusy
Za innowacyjnością firm kryją się konkretne wymierne korzyści z wdrażanych technologii zarówno dla samych operatorów logistycznych, ale także dla ich klientów. Liczba operacji logistycznych wzrasta, ich koszty maleją, mniej jest także strat materiałowych. Nie bez znaczenia są także korzyści pozamaterialne.
– Bardzo ważnym elementem w działalności FM Logistic, jeśli nie najważniejszym, są pracownicy firmy. To dzięki nim możliwy jest rozwój organizacji i jej sukcesy. Możliwość doskonalenia się, rozwijania własnych ambicji, w końcu wdrażanie własnych pomysłów, to bardzo cenna wartość dla każdego człowieka – podkreśla Patrick Bellart. – Czynnik integrujący, jaki występuje w pracach nad nowym projektem, jest bardzo ważnym elementem projektów wdrożeniowych. Wymiana doświadczeń pomiędzy pokoleniami pracowników, do jakiej dochodzi podczas takich prac, pozwala na naturalne podnoszenie kwalifikacji zawodowych naszych zespołów – dodaje.
Inną korzyścią, jaką firma osiąga, pracując nad innowacjami, jest chociażby wpływ na kreowanie wizerunku na rynku. Wśród klientów postrzegana jest jako nowoczesna i sprawna organizacja, nastawiona na wspólny z klientem sukces. Dzieli się z nim także wiedzą i doświadczeniami. Przykładem takiej inicjatywy są konferencje organizowane przez polski oddział FM Logistic pod nazwą „Open Minds Debate”, podczas których prezentowane są projekty z zakresu logistyki, ale również z takich obszarów jak transport, medycyna, ekonomia współdzielenia czy wirtualna rzeczywistość. W ten sposób firma stara się zarazić swoją innowacyjnością również swoich klientów.
Przykłady wdrożonych innowacji
Inventory Viewer – to nowa generacja rozwiązań w zakresie inwentaryzacji. Czy to dla celów podatkowych, czy w cyklu rozliczeniowym, inwentaryzacje wymagają znacznych środków. Platformy logistyczne muszą korzystać średnio z 5 do 15 podnośników i zatrudniać do tego wielu pracowników. Szukając rozwiązań usprawniających procesy, firma Hub One, usługodawca technologii informacyjnych i komunikacyjnych dla profesjonalistów wraz z FM Logistic, stworzyły wspólnie Inventory Viewer (IV) – zautomatyzowany system inwentaryzacji, niewymagający korzystania z podnośników. Rozwiązanie zostało z powodzeniem przetestowane w kilku miejscach.
Wyniki pracy wdrożonych systemów wskazują na 98,5% stopień dokładności, który odzwierciedla wysoką wartość dodaną, jaką zapewnia IV w okresach inwentaryzacji. Obsługiwane przez niego lokalizacje są przetwarzane w ciągu 3 sekund, a nie jak w przypadku klasycznego systemu inwentaryzacji 30 sekund. Zdjęcia wykonywane podczas pracy mają wysoką rozdzielczość, dzięki czemu umożliwiają rozwiązywanie niezgodności z pozycji komputera, bez konieczności obecności w magazynie.
Unikalny moduł rozcinania opakowań zbiorczych. Otwieranie opakowań zbiorczych podczas operacji copackingu jest zadaniem powtarzalnym, mogącym stanowić źródło dolegliwości mięśniowo-szkieletowych (MSD, musculoskeletal disorders) i skaleczeń. Tylko w centrum logistycznym FM Logistic zlokalizowanym w Fauverney operacji otwierania poddawanych jest 1,2 mln opakowań rocznie. Komisja Europejska szacuje, że MSD jest przyczyną 50% nieobecności w pracy trwających trzy lub więcej dni oraz 60% przypadków trwałej niezdolności do pracy. Dlatego wiadomo było, że rozwiązanie tego problemu jest istotne nie tylko z uwagi na poprawę funkcjonowania łańcucha dostaw, ale też podniesienia komfortu pracy na platformach. Mimo tego, że w Grupie FM od jakiegoś czasu wykorzystywane były urządzenia do półautomatycznego otwierania opakowań zbiorczych, operator wraz z firmą Axys Robotique postanowił stworzyć urządzenie, które rozwiąże wciąż istniejące problemy. Nowy moduł do rozcinania opakowań zbiorczych to narzędzie, które tnie, dostosowując się do grubości i jakości rozcinanego kartonu, oraz wytrzymuje znaczne obciążenia mechaniczne. Dzięki niemu możliwe stało się całkowite wyeliminowanie konieczności otwierania opakowań przez pracowników, co zdecydowanie poprawiło warunki ich pracy (nastąpił znaczący spadek dolegliwości mięśniowo-szkieletowych) i zmniejszyło liczbę skaleczeń nożem do kartonu. Ponieważ zastosowanie urządzenia znacząco zwiększyło produktywność operacji copackingu, podjęto decyzję o zaimplementowaniu go do wszystkich pozostałych centrów firmy. Równocześnie Dział Automatyzacji pracuje nad wzbogacaniem modułu o nowe funkcje, jak np. obsługa foliowanych jednostek logistycznych.
Robot kartezjański to kolejny projekt będący efektem współpracy FM Logistic z lokalnym integratorem systemowym Automat System. To przemysłowy robot sprzężony z układem obsługiwanych przez sterownik przenośników zapewnia automatyczny rozładunek palet przy dowolnej konfiguracji warstw, bez żadnej uprzedniej regulacji, przy równoczesnym systematycznym zasilaniu jednej lub kilku linii pakowania. Docelowo przewiduje się wyposażenie robota w dodatkowe funkcje, takie jak np. automatyczne etykietowanie opakowań detalicznych.
Scentralizowane gniazdo owijania palet. Tylko na platformie w Fauverney, każdego roku zużywane jest 4,5 mln metrów bieżących folii do owijania palet. Dział Automatyzacji opracował całkowicie zautomatyzowane urządzenie przystosowane do owijania palet dowolnego kształtu i wielkości. Gniazdo składa się z dwóch automatycznych owijarek z igłową perforacją folii, znajdujących się na przenośniku wyposażonym w obrotowe stoły. Odpowiednio rozmieszczone czujniki automatycznie rozpoznają wymiary podstaw palet. Oprócz natychmiast zauważalnych korzyści w zakresie ergonomii (paleta jest owijana automatycznie bez jakiejkolwiek ludzkiej ingerencji), dzięki nowemu narzędziu zoptymalizowana została konfiguracja strumieni towarów. Scentralizowane gniazdo owijania palet obecnie stanowi rozwiązanie nadające się do wprowadzenia we wszystkich centrach operatora o porównywalnych potrzebach.
Przenośne wewnętrzne platformy przeładunkowe Autodock. Przejście od załadunku ręcznego do w pełni zautomatyzowanego systemu załadunkowego pozwoliło zwiększyć dynamikę, a w konsekwencji efektywność łańcucha logistycznego realizowanego dla klientów operatora. Dzięki platformie przeładunkowej Autodock, fazy załadunku i rozładunku przebiegają do 6 razy szybciej niż w przypadku standardowych urządzeń. Tego typu platforma wyposażona jest w pomost z urządzeniem poziomującym oraz odbojniki. Jej zamontowanie nie wymaga wielu przeróbek, a w razie przeprowadzki może być z łatwością przewieziona na nowe miejsce.
E-Shopper. To rozwiązanie pozwalające na znaczne skrócenie czasu kompletowania zamówień dokonanych przez Internet. E-Shopper to po prostu inteligentny koszyk, którego zadaniem jest optymalizowanie przygotowania zamówień internetowych. Pozwala operatorowi na przygotowanie nawet 48 przesyłek jednocześnie, sprawdzenie ich zawartości dzięki zintegrowanemu systemowi ważenia oraz zapewnienie możliwości śledzenia wyboru produktów za pomocą wbudowanego systemu informatycznego. Zwalnia także operatora z obowiązku kontroli. Ten niezwykle pomysłowy i precyzyjny koszyk sprawdza w czasie rzeczywistym przygotowanie przesyłek i wykrywa potencjalne błędy, zachowując wysoki poziom niezawodności. Ponieważ czas logistyczny jest krótszy, codziennie pozwala to na zaoszczędzenie prawie 2 godzin w magazynie oraz uzyskania maksymalnej wydajności.