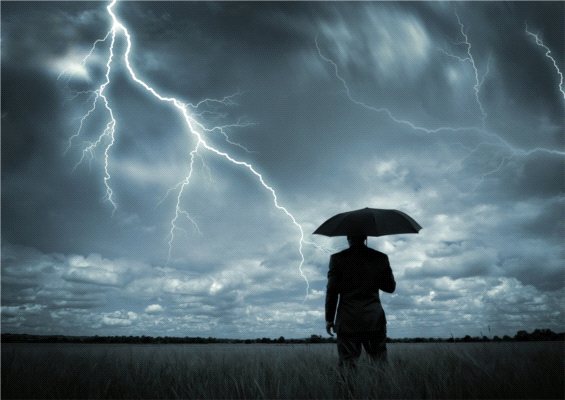
Cała prawda o ERP
Każde przedsiębiorstwo szybciej czy później rozrośnie się do takiej skali, że informacja zacznie tracić na wiarygodności, ludzie i maszyny nie będą w pełni wykorzystani, a pieniądze zamiast pracować będą zamrożone.Według międzynarodowych ekspertów, reprezentantów
Według międzynarodowych ekspertów, reprezentantów świata nauki, receptą na poprawę sytuacji jest wdrożenie zintegrowanego systemu klasy ERP. Do dyspozycji mamy najlepsze praktyki biznesowe, rozwiązania branżowe, rozwiązania prekonfigurowane, dedykowane itp.
Skoro wszyscy wdrażają to samo, to, dlaczego tylko nieliczni odnoszą sukces. Powodów, dla których organizacje odnoszą sukcesy lub zaliczają porażki wdrożeniowe jest wiele i prawie nigdy za sukces, czy porażkę nie odpowiada tylko jedna strona. W niniejszym artykule uchylimy rąbka tajemnicy i przedstawimy dziesięć sukcesów i porażek wdrożeniowych w obszarze produkcji.
Przyczyny sukcesów
Just in Time
Koncepcja Just in Time (dostawa na czas – po raz pierwszy zastosowana w latach 50 poprzedniego stulecia w zakładach Toyoty w Japonii) obejmuje całkowite wyeliminowanie marnotrawstwa, poprzez dostarczanie każdemu procesowi produkcyjnemu wszystkich potrzebnych elementów w wymaganym momencie i wymaganej ilości. Główną korzyścią związaną z JIT jest zredukowanie czasu realizacji do minimum, co przynosi istotne oszczędności związane z redukcją zapasów. JIT jest trudne do wdrożenia, ponieważ integruje cały łańcuch dostaw.
Zarządzanie przezbrojeniami
Przezbrojeniami można zarządzać na wiele sposobów w oparciu o metodę SMED, Teorię Ograniczeń czy Matrycę Przezbrojeń oferowaną przez systemy klasy ERP z tzw. „górnej półki”. Minimalizacja czasów przezbrojeń wpływa na uwolnienie zdolności produkcyjnych, większą elastyczność produkcji, możliwość wykorzystania wąskich gardeł. Zredukowanie do minimum czasów przezbrojeń umożliwia obniżenie zapasów oraz wielkość partii. Zarządzanie przezbrojeniami pozwala produkować to, co zamawiają klienci, a nie na magazyn w wielkich seriach.
Rozliczenie kooperacji
Proces kooperacji jest w praktyce bardzo złożony i wielowątkowy. Kooperacja realizowana jest najczęściej wtedy, kiedy brakuje zdolności produkcyjnych lub kiedy nie dysponuje się odpowiednią technologią wytwarzania i dlatego zleca się np. uszlachetnianie materiału na zewnątrz. Koordynacji podlegają materiały, półprodukty, ich konkretne partie, zewnętrzne gniazda produkcyjne, transport, itp.
Znajomość stopnia realizacji zamówienie klienta
Usprawnienie to stanowi o poważnej przewadze konkurencyjnej i najczęściej nie ma nic wspólnego ze standardową funkcjonalnością zawartą w oprogramowaniu klasy ERP.
Zmniejszenie poziomu produkcji w toku
Produkcja w toku to nic innego niż zamrożone pieniądze i ogólnie pojęta dezinformacja. Dlatego każda forma minimalizacji poziomu produkcji w toku, która nie skutkuje brakiem materiału, przestojami czy wydłużeniem czasu realizacji produkcji jest bardzo pożądana. W praktyce zmniejszenie poziomu produkcji w toku oznacza, lepsze raportowanie produkcji, kontrolę ruchów materiałowych, bardziej precyzyjną informację o zużyciu materiałów, rejestrację odpadów użytkowych i nieużytkowych, ewidencję barków itp.
Zmniejszenie poziomu zapasów magazynowych i znajomość rzeczywistego zużycia surowców
Każde usprawnienie w tej kategorii to uwolnione pieniądze do obrotu. Powodów, dla których stany zapasów są wysokie jest wiele. Pierwszym powodem są przesłanki czysto technologiczne, czyli niepodzielności materiałów (np. rury, blachy, wały itp.) Drugim powodem są przesłanki handlowe, a więc ograniczona dostępność (np. kontyngenty zakupowe, materiały dostępne sezonowo itp.), długi czas dostawy, minimalne partie zakupowe, drogi transport itp. Trzecim bardzo ważnym powodem wysokich zapasów są czynniki natury ludzkiej tzn. braku zapasów w przedsiębiorstwach nie wybacza się, w przeciwieństwie do jego wysokiego poziomu. Koszt zatrzymania produkcji może być wysoki.
Harmonogramowanie produkcji
Posiadanie bardzo precyzyjnej informacji na temat realizowanych zleceń produkcyjnych i operacji technologicznych w danym gnieździe to stan jak najbardziej pożądany przez każdego szefa produkcji. Marzenie to jest trudne do realizacji w systemie klasy ERP i najczęściej efekty odnoszą ci, którzy podjęli trud i wysiłek wdrożenia systemu klasy APS (Advanced Planning Scheduling).
Znajomość stopnia wykorzystania zasobów maszynowych w czasie rzeczywistych – OEE
Wiele firm dąży do takiego stanu, ale niewiele go osiąga. Jest trudny do realizacji i nie zawsze opłacalny kosztowo. Usprawnienie wymaga rejestracji postojów planowanych i nieplanowanych, raportowania produkcji, raportowania przezbrojeń, raportowania braków, kontroli jakości itp. Wiarygodna informacja wymaga wdrożenia systemu klasy MES (Manufacturing Execution System).
Znajomość obciążenia zasobów ludzkich
Jest to usprawnienie, o które postuluje większość przedsiębiorstw produkcyjnych. Systemy ERP w standardzie zakładają, że zasoby te dla potrzeb bilansowania ich dostępności są stałe, podczas gdy w praktyce są zmienne. Ważne jest bowiem odpowiedź na pytanie ilu ludzi zatrudnić, aby zaspokoić bieżący i przyszły popyt. W założeniach wydaje się to bardzo proste do realizacji, jednak w praktyce jest szalenie trudne do osiągnięcia. Zasoby ludzkie w przeciwieństwie do maszynowych są uzależnione od zdarzeń typu zwolnienie, chorobowe, urlopy, zastępstwa, wypadki itp.
Znajomość rzeczywistych kosztów wytworzenia wyrobów gotowych
Usprawnienie to w praktyce jest wielkim wyzwaniem dla organizacji. Wymaga wdrożenia skomplikowanych modeli kosztowych i oddzielenia rachunkowości finansowej od zarządczej. Wdrożenia ciągłego procesu usprawnień polegającego na aktualizacji zużycia materiałowego i czasów technologicznych. Wytworzenia kultury i świadomości dokładnego raportowania produkcji. Od strony księgowej zgodnie z obowiązującymi przepisami informację o rzeczywistych kosztach wytworzenia można otrzymać najszybciej w okolicach dwudziestego dnia następnego miesiąca, czyli post factum. Firmy, które nie skoncentrowały się tylko i wyłącznie na rachunku kosztów standardowych osiągnęły dużo więcej niż oczekiwały.
Przyczyny porażek
Brak znajomości rzeczywistych kosztów wytworzenia wyrobów gotowych
Precyzyjna informacja wymaga precyzyjnych danych, ale nie zawsze jest się przygotowanym na tak dokładną ewidencję, na tak dużym poziomie szczegółowości. Jest to także związane z kosztami dostarczenia tak precyzyjnej informacji. Załóżmy, że przedsiębiorstwo pracuje na trzy zmiany, posiada trzy wydziały produkcyjne, już z prostych obliczeń wynika, że potrzebuje zatrudnić minimum dziewięć nowych osób do rejestracji produkcji. Jeżeli czegoś nie usprawnimy będziemy mówili jedynie o rejestracji kart pracy, które przygotuje pracownik bezpośrednio produkcyjny. Czy jest to naprawdę zarejestruje czas rzeczywisty? Aby więc zarejestrować rzeczywisty czas operacji potrzebni są ludzie do ich rejestracji i armia ludzi ze stoperami, którzy ten czas zmierzą.
Bardzo ważnym ograniczeniem są poważne braki funkcjonalne dostępnego na rynku oprogramowania klasy ERP. Większość ERP’ów nie ma możliwości zaimplementowania równoległego modelu kosztowego dla celów rachunkowości zarządczej, np. TDABC – rachunek kosztów ABC sterowany czasem, TA – rachunek kosztów przerobowych. Większość systemów ERP potrafi dostarczyć jedynie informacji dla celów podatkowych, a inne w obawie przed astronomiczną liczbą transakcji w systemie, dostarcza koszt wytworzenia alokowany nie na wyrób gotowy, ale na rodzinę produktów. Nie należy zapominać także o organizacji, która prawie nigdy nie dysponuje dokładnymi danymi na temat zużycia materiałów i czasów technologicznych.
Brak skrócenia Lead Time – czasu wytworzenia wyrobów gotowych
Jeżeli były takie oczekiwania, a celu nie osiągnięto, to oznacza, że cała para poszła nie w ten gwizdek. Nie wykorzystano zdolności produkcyjnych (być może system funduje „dziury” czasowe na wąskich gardłach), nie zoptymalizowano przezbrojeń, nie poprawiono danych, wdrożono stary model w nowym systemie. System nie dostarcza informacji o stopniu zaawansowania zamówień klientów, informacje docierają z opóźnieniem, uniemożliwiającym realne i skuteczne harmonogramowania. Informacje o dostępnych zdolnościach produkcyjnych, dostępności narzędzi pomocniczych i aparatury kontrolno-pomiarowej są mocno zafałszowane. System nie uwzględnia priorytetów, co wymusza ręczne sterowanie harmonogramem.
System nie dostarcza realnych informacji o zdolnościach produkcyjnych maszynowych i ludzkich
Marzenia szefów produkcji, często pozostają jedynie marzeniami. Brak precyzyjnych informacji, informacja po czasie (o tym, że mieliśmy rano wolne moce produkcyjne dowiemy się w najlepszym przypadku pod koniec zmiany lub następnego dnia).
Brak OEE – wskaźnik wykorzystania zasobów produkcyjnych
Brak wdrożonego systemu klasy MES. OEE jest przydatny tylko wtedy, kiedy jest dostarczany online. Można posłużyć się tutaj przykładem pewnego krajowego przedsiębiorstwa, które postanowiło dostarczać informacje o OEE w swoim systemie klasy ERP (z najwyższej półki). Zatrudniono szesnaście osób, aby otrzymywać informację z jednodniowym opóźnieniem. Komórki analityczne były zadowolone, miały wskaźniki dla zarządu. Analitycy, którzy nigdy nie widzieli produkcji z bliska założyli wzrost OEE. Firma wdrożeniowa zarobiła kosmiczne pieniądze. Szef produkcji nie ukrywał rozczarowania, jak miał zwiększyć wartość wskaźnika OEE, jeśli nie miał bieżącej informacji o jego poziomie.
Błędny poziom zapasów materiałowych
Dla przykładu posłużę się arkuszem blachy, który będzie w procesie produkcji podlegał rozkrojowi na wycinarce laserowej. Konstruktor do wykonanie detalu, czy półproduktu potrzebuje blachy o konkretnym wymiarze. Jednak jednostką zamówieniową nie jest kawałek blachy o rozmiarze np. 0,5m na 0,3 m lecz określona liczba kilogramów (huta czy hurtownik sprzedaje blachę w kilogramach). Zaopatrzenie zamawia więc konkretną liczbę kilogramów blachy, powiększoną np. do wielkości minimalnej partii zakupowej. Blacha na magazyn przyjmowana jest w kilogramach (a nie w arkuszach czy rolkach). A co wydaje magazynier na produkcję? Powinien wydać to, czego oczekuje system produkcyjny. Ten zaś oczekuje wydania zgodnie z informacją zawartą w BOM’ie czyli np. 10,01 kg blachy. Tymczasem magazynier nie może wydać 10,01 kilogramów blachy. Może wydać cały arkusz o wadze znacznie większej niż 10,01 kg. W ten sposób informacji o stanach magazynowych ulegają zaburzeniu, ponieważ systemy wydają wirtualnie materiał w ilościach określonych w BOM’ach.
Nieskuteczne harmonogramowanie produkcji
Gdyby harmonogram umiał mówić nie jeden właściciel firmy, szef produkcji czy planista nasłuchałby się. Usłyszałby o złych czasach operacji, nad którymi nikt nie pracuje od lat i ślepo ufa technologom. Opowiedziałby o marginalizowaniu czasów przezbrojeń i mentalności produkcji w wielkich partiach (jak za Forda). Braku uwzględnienia czasów kolejkowania, oczekiwania, kolejki, czasów międzyoperacyjnych, kontroli jakości w opisie technologicznym. Zapewne usłyszelibyśmy o kiepskich algorytmach planistycznych zaimplementowanych w algorytmach MRP, CRP, RCCP. Nie obeszłoby się bez krytyki utrzymywania gigantycznych liczby wersji i wariantów BOM’ów i marszrut przy braku wsparcia algorytmów do automatycznego wyboru najbardziej korzystnych wersji i wariantów. Harmonogram z pewnoscią przekazałby swoje uwagi na temat tego, że w realnym świecie operacje wykonywane są równolegle, a nie sekwencyjnie, jak tego oczekuje system klasy ERP itp.
Brak informacji o stanie realizacji zamówieni u klienta
Systemy klasy ERP mają swoje korzenie w latach 50 i 60, czyli wtedy, kiedy królowała produkcja na magazyn. Współczesne systemy klasy ERP cały czas są obciążone przekleństwem anonimowej produkcji bez powiązania ze zleceniem klienta. Czasami wystarczą proste modyfikacje, aby ujawnić proces produkcji. Niestety większość wdraża standard bez wsparcie tych, którzy rozumieją logikę ERP’a i politykę firm wdrożeniowych.
Śledzenie partii
Jest to prawdziwe wyzwanie dla organizacji. Zarządzanie partią przy odpowiednio skomplikowanym procesie produkcyjnym jest wyzwaniem przerastającym możliwości organizacyjne przedsiębiorstw, a bez wsparcia systemu klasy ERP, systemem klasy MES, rejestracja partii jest fikcyjna.
Brak odzwierciedlenia poprawnych ruchów magazynowych na produkcji
Jak utrzymuje Aberdeen Group ponad połowa firm posługujących się systemem ERP przyznała, że nie wie co dzieje się na hali, czyli są rozbieżność pomiędzy danymi w systemie, a aktualnymi stanami magazynowymi i realizowanymi zleceniami produkcyjnymi w czasie rzeczywistym.
Moduł produkcyjny jest wąskim gardłem przedsiębiorstwa
Przeładowany model biznesowy, implementacja starego modelu pracy w nowoczesnym oprogramowaniu, wiara właścicieli w skuteczność swoich metod, nieznajomość nowoczesnym metod zarządzania produkcją. Wszystko to powoduje, że produkcja sobie, a system klasy ERP sobie. Harmonogramowanie w Excelu, produkcja rejestrowana w systemach satelitarnych, itp.
Sukcesy cieszą, porażki zniechęcają. Sukcesy są w zasięgu ręki, jednak wymagają determinacji, profesjonalnego doradztwa, transferu wiedzy, nowoczesnych narzędzi informatycznych i otwartości na zmianę organizacji. Firmy które przestały być zakładnikami obecnie funkcjonujących rozwiązań, odniosły wielkie sukcesy.