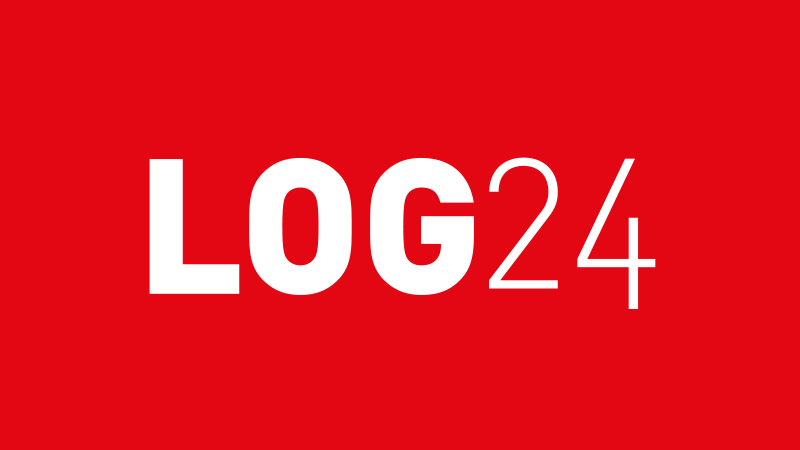
Cyberpracownicy
Branża motoryzacyjna zalicza się do czołówki, jeżeli chodzi wdrażanie innowacyjnych technologii w fabrykach. Choć kojarzy ona nam się głównie z szerokim zastosowaniem robotów, ostatnie miesiące przyniosły szereg pomysłów na to, jak wspomóc pracowników, zamiast eliminować ich z...
Z kosmosu do hali produkcyjnej
Powiedzmy sobie wprost – technologie kosmiczne nie powinny marnować się tylko na potrzeby NASA i podobnych organizacji. Na szczęście coraz więcej z nich schodzi na ziemię i znajduje naprawdę praktyczne zastosowania.
GM i NASA przez dziewięć lat wspólnie pracowały nad rozwojem rozwiązań technicznych, które miały sprawdzać się w przestrzeni kosmicznej. Jedną z nich było RoboGlove – zrobotyzowana rękawica, która miała wspierać astronautów przy pracy. Szybko zauważono, że przyda się ona także w innych aplikacjach.
General Motors, jeden z największych producentów samochodów na świecie, postanowił naturalnie sprawdzić możliwość zastosowania rękawicy w swoich fabrykach. RoboGlove było krótko testowany w zakładzie produkcji przedseryjnej GM. Dało się zauważyć, że urządzenie mimo sporego potencjału da się jeszcze udoskonalić, sięgając po biotechnologię.
W tym celu rozpoczęto współpracę z Bioservo Technologies AB. Szwedzka firma specjalizuje się w opracowywaniu innowacyjnych rozwiązań dla medycyny i ma w portfolio technologię SEM GloveTM (Soft Extra Muscle — miękki dodatkowy mięsień). Połączenie rozwiązań wykorzystywanych w RoboGlove i SEM GloveTM pozwoli uzyskać niezwykle użyteczny w fabrykach produkt.
Jak działa RoboGlove?
Rękawica opracowana przez GM i NASA stanowi efekt uboczny prac nad humanoidalnym robotem Robonaut 2 (R2), wysłany w kosmos w 2011 roku. RoboGlove to zwiększające siłę urządzenie ubieralne. W rękawicy zastosowano najnowocześniejsze czujniki, siłowniki i cięgna będące odpowiednikami nerwów, mięśni i ścięgien w ludzkiej ręce. Jednym z wymogów przy projektowaniu R2 była zdolność do obsługi narzędzi przeznaczonych dla człowieka. Konstruktorom robota udało się zbudować mechanizm, który pod względem zręczności dorównuje dłoni. Technologię tę wykorzystano następnie w RoboGlove.
Z badań GM wynika, że już po kliku minutach ciągłego manipulowania jednym narzędziem pracownik może czuć zmęczenie.
Bioservo najpierw przystąpi do pracy nad nowym narzędziem chwytającym do zastosowań przemysłowych, które będzie mogło działać z większą efektywnością, zmniejszając jednocześnie zmęczenie dłoni operatora. Z badań GM wynika, że już po kliku minutach ciągłego manipulowania jednym narzędziem pracownik może czuć zmęczenie.
Rękawica będzie w stanie dwu-trzykrotnie zmniejszyć siłę którą musi przyłożyć robotnik do wykonania danej czynności. Nie będzie jednak pomocna przy dźwiganiu ciężkich przedmiotów, a tylko przy manipulacji narzędziami. To jednak jeden ze znaczących kroków w kierunku rozwoju i wprowadzenia technologii miękkiego egzoszkieletu do użytku na skalę globalną.
GM planuje zostać pierwszym odbiorcą zaawansowanej zrobotyzowanej rękawicy w sektorze produkcyjnym i testować ją w niektórych swoich zakładach. Produkcją i sprzedażą rękawicy także innym firmo zajmie się Bioservo. Prócz zastosować przemysłowych, rozwój będzie dotyczył także aplikacji medycznych. RoboGlove może ułatwić pracę np. rehabilitantom, podobnie jak pracownicy fabryk często wykonującym wykonując monotonne, powtarzalne ruchy.
Potencjał egzoszkieletów
Potencjał wykorzystywania egzoszkieletów w przemyśle sięga jednak znacznie dalej. Panasonic opracował serię kombinezonów, które mają pomagać człowiekowi w podnoszeniu ciężkich przedmiotów i unikaniu kontuzji kręgosłupa. Najbardziej aktualnie zaawansowana wersja – Power Assist Suit AWN-03 – zakładana jest na plecy i biodra. Kombinezon wyposażony jest w czujniki i siłowniki, aktywowane w momencie rozpoczęcia podnoszenia. Waga podnoszonego przedmiotu redukowana jest o 15 kg, a akumulator wystarczy na osiem godzin pracy. Panasonic chce nadal udoskonalać kombinezon i przygotować jeszcze mniejszą wersję, zapewniającą udźwig na poziomie 24 kg , po czym rozwiązanie wprowadzić go do produkcji masowej.
Swoją wersję egzoszkieletu – znacznie większą i mniej wygodną, ale oferującą znacznie większą siłę wsparcia – opracowuje Hyundai. To już niemal cały, ubierany robot, z mechanicznymi nogami i rękami. Prócz przemysłu, ma on znaleźć zastosowanie także w wojsku i zmniejszyć zmęczenie żołnierzy noszących ciężki ekwipunek. Zapewne z tego względu Koreańczycy nie podają zbyt wielu informacji na temat konstrukcji swojego rozwiązania.
Połączenie możliwości omawianych rozwiązań i ich upowszechnienie sprawią, że w przyszłości praca w fabryce przestanie być jednym z niekorzystnych dla zdrowia zawodów.
Po egzoszkielet sięgnęło także BMW, które w amerykańskiej fabryce w Spartanburgu testuje trzy różne rozwiązania. Jednym z nich są kamizelki Ekso Vest. Przypominające plecak rozwiązanie zapewniają wsparcie dla pleców i ramion. Dzięki elementom pneumatycznym ułatwione jest podnoszenie ciężkich przedmiotów. Urządzenie póki co nie jest zmechanizowane, lecz badana jest możliwość dołączenia siłowników i umożliwienia podnoszenia jeszcze większych ciężarów. Ale już teraz pracownicy, którzy biorą udział w pilotażowym projekcie, nie chcą więcej pracować bez kamizelki.
Airbus w swoim projekcie inspirował się uprzężą stosowaną przez kamerzystów. Nieco toporna uprzęż oparta na lekkiej i miękkiej ramie jest wykorzystywana w fabryce helikopterów w Marignane. Airbus pracuje teraz nad bardziej zaawansowanym egzoszkieletem, dodatkowo kontrolowanym przez elektronikę.
Krzesło bez krzesła
Sukces odniósł także wynalazek szwajcarskiego start-upu Noonee: Chairless chair. Wykonane z karbonu „krzesło bez krzesła” to rodzaj zewnętrznego szkieletu, zakładanego po tylnej stronie nóg. Pracownik mocuje go pasami do bioder, kolan i kostek. Dwie wyściełane skórą powierzchnie podpierają pośladki i uda, a dwa pręty z tworzywa wzmocnionego włóknem węglowym dopasowują się do konturu nóg. Połączenia i miejsce zgięcia znajdują się po tylnej stronie kolana. Chairless chair można hydraulicznie dopasować do wzrostu człowieka i do pożądanej pozycji. Ciężar ciała pracownika przenoszony jest na podłoże przez te właśnie, ruchome elementy. To „krzesło bez krzesła” waży zaledwie 2,4 kg.
W projekt włączyło się Audi, które testuje Chairless chair od ponad roku w zakładach w Neckarsulm i Ingolstadt, zaś dalekosiężne plany zakładają ich wykorzystanie we wszystkich fabrykach koncernu. Przy wykonywaniu wielu czynności montażowych oraz np. podczas krótkich przerw w pracy, daje możliwość siedzenia w ergonomicznej, korzystnej dla zdrowia pozycji. Nowoczesna konstrukcja zapewnia lepszą postawę ciała i zmniejsza obciążenie nóg. Krzesła i stołki na których można usiąść podczas pracy, używane dziś na wielu odcinkach taśmy produkcyjnej, stają się zbędne. Wprowadzając takie udogodnienie, Audi pragnie również zredukować przestoje produkcyjne spowodowane fizycznym zmęczeniem pracownika. – Używając chairless chair poprawiamy ergonomię czynności montażowych. Ponadto spodziewamy się, że dzięki niemu osoby z niepełnosprawnością będą mogły przejąć nowe zadania – zauważył dr Mathias Keil, kierownik ds. metod inżynierii przemysłowej w Audi AG.
Ręka w rękę z robotem
Ford zamiast na rozwiązania ubieralne, postawił na robiące coraz większą karierę roboty współpracujące. Jednak prowadzony w fabryce w Kolonii program pilotażowy nieco przypomina korzystanie z egzoszkieletu – pracownik korzysta z siły robota, jednak to człowiek decyduje o tym, jakie ruchy zostaną wykonane.
Zaawansowane i przyjazne dla człowieka urządzenia są wykorzystywane do pomocy pracownikom fabryki przy montażu amortyzatorów do modelu Fiesta. Zadanie to wymaga zegarmistrzowskiej precyzji, siły oraz dużej zręczności. Pracownicy fabryki wykonują je we współpracy z robotami, co zapewnia idealne spasowanie części za każdym razem.
Próby przeprowadzane w fabryce Forda w Kolonii, w Niemczech, stanowią część badań nad programem Industry 4.0. Ford zebrał opinie od ponad 1000 robotników pracujących przy linii produkcyjnej, aby określić, do jakich zadań roboty nadawałyby się najlepiej.
– Roboty pomagają w łatwiejszym, bezpieczniejszym i szybszym wykonywaniu zadań, wspierając tym samym naszych pracowników. Ich umiejętności otwierają przed nami nieskończoną paletę możliwości w dziedzinach produkcji i designu nowych modeli Forda – skomentował Karl Anton, dyrektor działu Vehicle Operations w Ford of Europe.
Ford zebrał opinie od ponad 1000 robotników pracujących przy linii produkcyjnej, aby określić, do jakich zadań roboty nadawałyby się najlepiej.
Roboty mierzące 1 metr wysokości pracują „ręka w rękę” z pracownikami fabryki przy linii produkcyjnej przy dwóch stacjach roboczych. Zamiast ręcznie operować ciężkim amortyzatorem i urządzeniem montażowym, robotnicy mogą teraz skorzystać z pomocy robota przy podnoszeniu części i automatycznie ustawić jej położenie w nadkolu zanim wcisną przycisk, inicjujący montaż.
– Praca z ciężkimi narzędziami pneumatycznymi trzymanymi nad głową to ciężkie zajęcie wymagające siły, wytrzymałości i dokładności. Robot to dla nas bardzo duża pomoc – powiedział Ngali Bongongo, robotnik pracujący przy produkcji w fabryce Forda w Kolonii.
Koboty wyposażone są w zaawansowane technicznie sensory, umożliwiające natychmiastowe zatrzymanie, kiedy na ich drodze znajdzie się ludzkie ramię lub nawet palec, co zapewnia bezpieczeństwo pracowników. Podobna technologia używana jest także w przemyśle farmaceutycznym i elektronicznym. Program wdrożenia robotów do pracy w fabryce został opracowany we współpracy z niemieckim producentem robotów KUKA Roboter GmbH, w ciągu ponad dwóch lat.
Ford bada możliwości szerszego zastosowania robotów współpracujących, które mogą zostać zaprogramowane do wykonywania niemal każdej czynności, od przygotowywania kawy aż po uścisk „rąk”.
Zostać Iron Manem
Połączenie możliwości omawianych rozwiązań i ich upowszechnienie sprawią, że w przyszłości praca w fabryce przestanie być jednym z niekorzystnych dla zdrowia zawodów. Możliwość korzystania z tak zaawansowanej technologii wpłynie też na atrakcyjność zawodu – w artykułach prasowych poświęconych stosowaniu egzoszkieletów w fabrykach nieraz pada określenie Iron Man. A kto nie chciałby zostać Iron Manem?
Czy cyberpracownicy to także odpowiedź na robotyzację? Według wielu ekspertów – tak. Wykorzystanie egzoszkieletów pozwoli bowiem połączyć to co najlepsze z dwóch światów: siłę i wytrzymałość robotów oraz inteligencję i zdolność reagowania na nieprzewidziane człowieka, bezkonkurencyjnego – póki co – na tych polach.