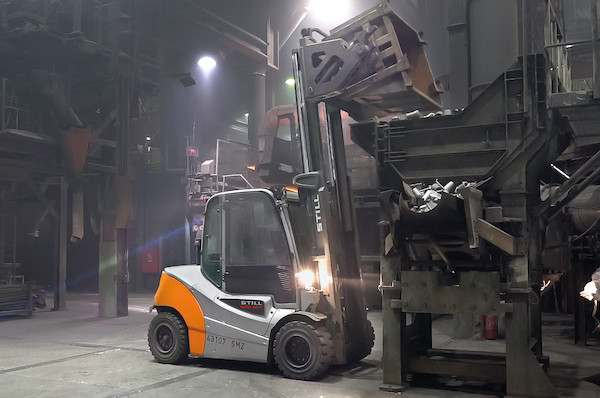
Czar systemów zarządzania flotą
Czy da się realizować te same zadania transportu wewnętrznego przy użyciu kilkunastu wózków mniej? Przykład odlewni FONDIUM pokazuje, że tak. Wystarczy zmodernizować flotę w oparciu o rzeczywiste dane na temat eksploatacji poszczególnych maszyn i wdrożyć dopasowane do specyfiki zakładu rozwiązania.
Podstawową działalnością grupy FONDIUM jest produkcja, odlewnictwo i przetwórstwo elementów żeliwnych do zastosowania w rozmaitych branżach – szczególnie zaś motoryzacyjnej. Firma wypracowała pozycję wiodącego dostawcy komponentów do samochodów osobowych i ciężarowych. Jako swoją przewagę konkurencyjną wskazuje powtarzalną jakość w masowej produkcji seryjnej. Dzięki swojemu know-how przedsiębiorstwo jest w stanie dostarczać części z powodzeniem wykorzystywane w kluczowych dla bezpieczeństwa jazdy elementach podwozia. Grupa wykazuje sprzedaż na poziomie 600 mln euro rocznie i w dwóch zakładach zatrudnia około 2 tys. osób. W jednym z nich dokonano ostatnio modernizacji floty intralogistycznej, która pozwoliła zoptymalizować procesy transportu wewnętrznego i znacząco obniżyć koszt leasingu.
Charakterystyka obiektu
Powstały w 1895 roku zakład produkcyjny w Singen n/Hohentwiel specjalizuje się w odlewnictwie komponentów dla samochodów ciężarowych. Produkowane są tu m.in. zaciski hamulcowe Knorr, piasty kół oraz zwrotnic do takich marek jak Daimler, MAN, Renault, DAF czy Volvo. Projektowanie jest wspierane komputerowo zaawansowanymi rozwiązaniami, a przepustowość seryjnej produkcji sięga 12,5 mln części w skali roku. Warunki pracy wózków widłowych są dość ciężkie. Ładunki dużej masy są często przewożone po stosunkowo nierównym podłożu. Wszystko to wymaga bardzo rozbudowanej, sprawnie funkcjonującej floty intralogistycznej. W związku z tym jest ona zazwyczaj modernizowana w 4-letnich cyklach. Tym razem proces decyzyjny na temat doboru wózków postanowiono zrealizować w oparciu o dane z inteligentnego systemu ewidencji pracy.
Zastosowane rozwiązanie
Od kilku lat w zakładzie FONDIUM korzystano z systemu zarządzania flotą STILL FleetManager. Wprowadzono go w obliczu dużej liczby generowanych braków – z myślą o autoryzacji użytkowników pozwalającej na jednoznaczną identyfikację operatora korzystającego z wózka w konkretnym momencie. Podczas ostatniej modernizacji floty zakładu system posłużył także jako źródło danych dotyczących zajętości maszyn i ich obłożenia pracą, co stało się podstawą optymalizacji decyzji zakupowych. Jednym z najważniejszych poczynionych dzięki niemu odkryć była dokładna informacja, jak duże dystanse pokonują wózki w drodze do centralnej akumulatorowni i jak znaczne ilości czasu poświęcane są na obsługę procesu ładowania. Stało się to przyczynkiem do wdrożenia w zakładzie po raz pierwszy wózków z bateriami litowo-jonowymi wraz ze zdecentralizowanymi stacjami szybkiego ładowania. – Już po 30 minutach ładowania akumulatory Li-Ion nowej generacji odzyskują nawet 50 proc. swojej pojemności. Inaczej niż w przypadku baterii kwasowo-ołowiowych nie ma potrzeby ich otwierania, uzupełniania wody i wyrównywania napięcia. To o tyle istotne, że w zapylonym otoczeniu odlewni operacje te mogły znacząco skracać okres żywotności konwencjonalnych baterii. Co więcej, ładowanie akumulatora bez konieczności wyciągania go z wózka oszczędza czas i nie wymaga zastosowania elektrycznego wózka paletowego. Tego rodzaju maszyny mogą być więc w tym czasie wykorzystywane do innych zadań – tłumaczy Grzegorz Kurkowski, specjalista ds. produktu STILL Polska. – W zakładzie funkcjonuje 50 czołowych wózków elektrycznych RX 60 o udźwigu od 2,5 do 5,0 ton. Wszystkie zostały wyposażone w system GPRS umożliwiający przekazywanie danych do systemu FleetManager, chipy RFID do autoryzacji operatora, dodatkowe ochronne żebrowanie dachu kabiny oraz system oświetlenia STILL SafetyLight 4Plus. Wiele wózków zostało także specjalnie zmodyfikowanych pod kątem konkretnych zadań wykonywanych w zakładzie FONDIUM – na przykład poprzez dodanie obrotowego siedziska operatora na trasach, na których często używa się biegu wstecznego – relacjonuje.
Efekty wdrożenia
Dzięki użyciu w procesie decyzyjnym danych z systemu STILL FleetManager udało się trafnie zidentyfikować obszary oszczędności. Liczbę wózków we flocie, a co za tym idzie – koszty leasingu – udało się zredukować ze 136 maszyn przed modernizacją do 119 po niej. To mniej więcej 12,5 proc. mniej bez żadnej straty dla tempa pracy. Wprowadzenie 23 zdecentralizowanych stacji ładowania oraz zastosowanie umożliwiających częściowe uzupełnianie pojemności baterii akumulatorów litowo-jonowych zmniejszyło ilość czasu potrzebnego na procedurę ładowania. Jako że nie muszą być w nią dłużej angażowane wózki paletowe, można było uwolnić je do innych zadań. Co więcej, wprowadzony przed modernizacją jako narzędzie autoryzacji i identyfikacji użytkowników wózków program do automatycznej ewidencji pracy pozwolił w parze z dorocznymi szkoleniami operatorów zredukować liczbę generowanych braków o 80 proc.
(Still)