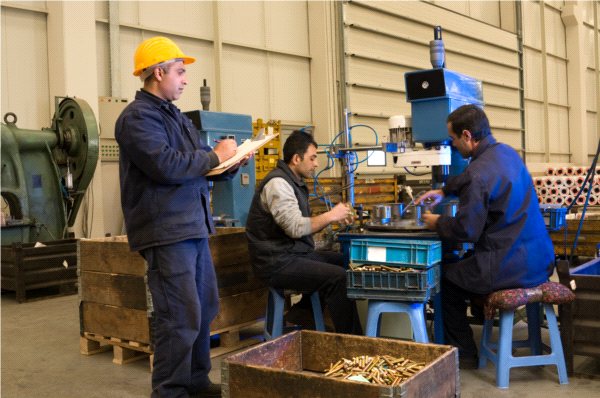
Czy dwa plus dwa równa się cztery?
Umiejętność porównania tego co na „wejściu” z tym co na „wyjściu” jest probierzem efektywności funkcjonowania wszystkich komórek organizacyjnych przedsiębiorstwa. Możliwość śledzenia zaawansowania przetwarzania, powstawania wyrobu gotowego to szansa na bieżące reagowanie i...
Czy rozliczanie produkcji w aspekcie pobranych materiałów, komponentów, surowców, części, w stosunku do przekazanych wyrobów gotowych do magazynu należy do zadań logistyki produkcji czy logistyki w ogóle? Kto powinien precyzyjnie odpowiedzieć na pytanie szefa: dlaczego z takiej ilości surowca lub części wykonano 100 sztuk wyrobów gotowych, a nie 102 sztuki czy też 98? A przecież pierwszy przypadek (102 sztuki) oznaczałby, że w sposób niewłaściwy zostały przyjęte normy zużycia – są mianowicie zaniżone. Drugi przypadek (98 sztuk) świadczyłby z kolei o tym, że pracownicy lekceważąco podchodzą do procesów jakości, ponieważ dostawcy (wybrani na podstawie kryterium kosztów) dostarczają materiały o zaniżonej jakości i nikt tego nie kontroluje.
Jak należy liczyć i kwalifikować to, co znajdujemy podczas np. rocznej inwentaryzacji na linii technologicznej, a co nie jest jeszcze wyrobem gotowym? Niektórzy nazywają to robotami w toku, inni produkcją niezakończoną. Czy pracownicy firm potrafią zidentyfikować ilości i rodzaje materiałów – wyrażone w różnych jednostkach miary – które materiałami już nie są, a wyrobami gotowymi jeszcze nie są? W jaki sposób określić wartość produkcji niezakończonej? Czy jej wartość to suma wydanych surowców i materiałów do produkcji? Wydawać by się mogło, że to tylko kilka zagadnień ilustrujących przepływy rzeczowe w przedsiębiorstwie, jednak są jeszcze firmy, w których porównanie tego, co opuściło magazyn zaopatrzenia z tym, co znajduje się na linii produkcyjnej oraz w magazynie wyrobów gotowych, stanowi poważny problem. I tylko „bezgraniczne” zaufanie kierownictwa firmy do pracowników, ich wiedzy i umiejętności (nie kradną, poważnie traktują firmę i jej majątek, mają wymagane, wcześniej sprawdzone kwalifikacje) pozwala przypuszczać, że produkują oni według najlepszej wiedzy (technologicznej, logistycznej, technicznej, ekonomicznej) i niczego świadomie nie zaniedbują, zużywając do produkcji jednej sztuki tyle materiałów, ile trzeba, a nic ponad to. Czy może jest jednak sposób na to, aby te ilości mogły być liczone poprawnie i żeby były na bieżąco weryfikowane?
Przykład pierwszy
Nie liczone zużycie
Przedsiębiorstwo branży meblarskiej zatrudniało ok. 200 osób. W magazynie pojawiały się surowce, materiały, części – wykorzystywane do produkcji wyrobu gotowego występującego w przeróżnych odmianach. Cechami odróżniającymi produkty gotowe od siebie były przede wszystkim rozmiary, kolor wykończenia, wypełnienie. Ilość wyrobów, jaka była zaplanowana na dany dzień, była znana. Więc w czym problem jeśli chodzi o policzenie? Przedsiębiorstwo opierało produkcję przede wszystkim na zamówieniach. Normy zużycia nie były tajemnicą dla nikogo, wyrób nie był zbyt skomplikowany – maximum do 20 części, jedne liczone w sztukach, inne w metrach bieżących lub w kilogramach. Od 15 do 20 procent całego wolumenu stanowił asortyment przeznaczony dla super- i hipermarketów. W związku z tym, że cała produkcja dnia poprzedniego wyjeżdżała do klientów dopiero w dniu następnym, codzienne porównanie ilości materiałów i wyrobów gotowych, nie stanowiłoby problemu. Nikt jednak tego nie robił, wszystkim bowiem wydawało się, że na wyprodukowanie zamówionej ilości wyrobów wydano niezbędną ilość materiałów. W rzeczywistości było jednak inaczej.
Wprowadzono rejestrację „braków”, które zostały poddane systemowej i fizycznej likwidacji
Pierwszym sygnałem, że dzieje się coś nie tak, były przypadki produkcji czegoś, co było już wyprodukowane. Jak to sprawdzono? Mimo że nie funkcjonowała żadna systemowa procedura zmuszająca pracownika do ewidencjonowania tego, co stało się już wyrobem gotowym, to łatwo policzalne były zasadnicze elementy wchodzące w skład każdego z wyrobów. Pojawiła się nieścisłość w ewidencji tego, co trafia do magazynu surowców oraz tego, co trafia z magazynu surowców na produkcję.
Jeden człowiek
Jeśli chodzi o proces ewidencji, to nie był on dopracowany. Na domiar złego w dziale zaopatrzenia pracował jeden pracownik, a ewidencja trafiających materiałów do magazynu surowców oraz przekazywania ich do produkcji nie leżała w zakresie kompetencji ani odpowiedzialności tego pracownika. Jedynym zadaniem magazynu surowców było codzienne przyjmowanie materiałów, składowanie, a następnie wydawanie ich na produkcję na podstawie tzw. specyfikacji produkcyjnych, których zresztą nikt nie podpisywał. Poza tym magazyn pracował do godziny 16.00, a produkcja do 22.00. Ewidencja przyjęć i wydań z magazynu surowców prowadzona była przez tego jednego pracownika „działu zaopatrzenia”, którego najważniejszym zadaniem było zamawianie materiałów i który ze względu na brak czasu nie miał możliwości dalszego śledzenia ich drogi. Zamawianie materiałów zajmowało mu prawie 90 proc. czasu, gdyż większość materiałów zamawiana była za granicą. Poza tym pracownik ten nie był rozliczany z wielkości utrzymywanych zapasów, choć wiedział, że pojawienie się zapasu nadmiernego nie było czymś, nad czym szefostwo firmy przechodziło do porządku dziennego i wiązało się odpowiednimi konsekwencjami. Stany magazynowe surowców były uaktualniane z dużym opóźnieniem. Dostawy surowców odbywały się codziennie.
Brak kontroli
W obsadzie etatowej działu produkcji nie było nikogo, kto mógłby się zajmować normami zużycia. Nie było żadnych działań pozwalających porównać chociażby na koniec miesiąca, ile wydano z magazynu surowców, a ile wyprodukowano mebli. Nie wiedziano również ile i jakie materiały wycofano z produkcji, bo np. nie spełniały norm jakościowych, itd. Nikt tego typu pytań sobie nie zadawał i nie próbował szukać odpowiedzi.
Pracownicy działu kontroli jakości nie prowadzili kontroli używanych do produkcji materiałów. To pracownicy, operatorzy maszyn, decydowali o tym, czy element nadaje się do produkcji. Zadaniem pracowników działu kontroli jakości było sprawdzenie funkcjonalności i wykonania tzw. zewnętrznego, tzn. tego, co mógł zobaczyć klient. Natomiast ile i jakie materiały mogły się znajdować czy znajdowały się wewnątrz wyrobu – nikt w takie szczegóły nie wnikał. Pracownicy byli doświadczeni, wiedzieli, co produkują.
Fakt nie porównywania ilości materiałów na bieżąco (brak procedur) zachęcał pracowników do wykonywania z surowców i materiałów przewidzianych do produkcji planowanej także wyrobów „pozaplanowych”. Część takich pozaplanowych produkcji została wyłapana, pracownicy zwolnieni dyscyplinarnie, ale zapewne nie wszyscy.
Na „cicho”
Dodatkowym utrudnieniem w śledzeniu materiałów, była możliwość zamiany wyrobów poprzez dokonywanie przeetykietowania. Szczególnie dotyczyło to mebli kierowanych do sieci supermarketów, a także akcji promocyjnych, gdzie trudno było przewidzieć, które z zaplanowanych wyrobów będą miały „wzięcie” u klientów (mebli podczas promocji nie może przecież zabraknąć).
Od czasu do czasu pojawiały się doniesienia o nielegalnym handlu pochodzącymi z zakładu tkaninami
Dochodziło do absurdalnych sytuacji, gdy pracownik magazynu zgłaszał brak określonej sztuki. Na produkcji wszczynano poszukiwania części, półfabrykatów potrzebnych do produkcji mebla, który z różnych przyczyn nie został wcześniej wytworzony. Jeżeli ich tam nie znajdowano, materiały pobierano z magazynu na „cicho” i po prostu produkowano. Taki mechanizm sprzyjał licznym kradzieżom, co z kolei wymusiło na kierownictwie firmy stworzenie procedur wykluczających tego rodzaju praktyki.
Wdrożenie systemu
Rozwiązaniem stało się wdrożenie zintegrowanego systemu informatycznego wspomagającego zarządzanie przedsiębiorstwem. Aby móc śledzić przepływ materiałów w procesie produkcyjnym, zaimplementowano system automatycznej identyfikacji. Po wielu próbach – najdłużej wdrażany był moduł produkcji, gdzie jak zwykle problemem okazały się listy materiałowe – dzięki uporowi kierownictwa firmy system został wdrożony. Pojawił się jednak problem związany z identyfikowaniem tego, co nie było liczone w sztukach, ale w kilogramach, metrach bieżących, metrach kwadratowych.
Pojawiła się nieścisłość w ewidencji tego, co trafia do magazynu surowców oraz tego, co trafia z magazynu surowców na produkcję
Do chwili wdrożenia JBA SYSTM 21 w firmie funkcjonowały aż trzy różne systemy. Po stronie zaopatrzenia oraz zbytu funkcjonował system, a raczej namiastka systemu, który pozwalał na bezstresowe prowadzenie inwentaryzacji. Nie zawierał autoryzacji ani też historii transakcji, więc zawsze, o każdej porze, każdy, kto miał dostęp do klawiatury, mógł w absolutnie dowolny sposób dokonać np. przesunięcia magazynowego, przyjęcia czy też wydania do produkcji. To w połączeniu z dostępem fizycznym do magazynów pozwalało na „zgrywanie” stanów ilustrowanych wydrukiem z komputera, a stanów ilustrowanych arkuszem spisowym. Możliwość takiego „zgrywania” nigdy nie powinna mieć miejsca. Stan ten trwał dosyć długo. Dzięki jednak uporowi szefa produkcji, pracownika zaopatrzenia, jak również pracowników magazynu wyrobów gotowych, po prawie pięciu latach JBA SYSTM 21 został wdrożony.
Szereg korzyści
Implementacja systemu wymusiła zmiany świadomościowe i organizacyjne w firmie: zmiany postaw pracowników, pojawienie się zupełnie nowych stanowisk. System ułatwił pracownikom zaopatrzenia (zatrudniono jeszcze dwóch) realizację zadań związanych z zakupami. Znalazł się czas na prowadzenie analiz zachowań i ocenę dostawców, a także na poszukiwanie nowych. System wymusił również na pracownikach produkcji i magazynu surowców stworzenie procedur związanych z kontrolą jakości przyjmowanych dostaw.
Po rozwiązaniu problemu zużycia surowców wzmocnieniu uległa marka firmy, stosowanie MRP pozwoliło bowiem na szybkie potwierdzanie realnych terminów zamówień. Okazało się również, że i hipermarkety można zmusić do prognozowania popytu, a w związku z tym zaprzestano produkcji na magazyn dla tych właśnie odbiorców.
Przejrzystość procesów
Śledzenie przepływu materiałów w procesie produkcyjnym zostało wzmocnione wprowadzeniem stacjonarnych czytników przemysłowych w newralgicznych punktach produkcji. Pozwoliło to odpowiednio reagować osobom odpowiedzialnym za zapasy w sytuacjach tworzenia się zapasów tam, gdzie ich być nie powinno. Pracownicy decyzyjni mieli natychmiast dostęp do tych informacji.
Wzmocnieniem procedur eliminujących możliwość kradzieży – pozaplanowej produkcji z lekceważeniem wymogów jakości, a więc zużywanie większej niż norma ilości materiałów – było wprowadzenie procedur ewidencji na styku magazyn zaopatrzenia – produkcja, produkcja – magazyn wyrobów gotowych. Alokowano tam dodatkowych ludzi i wymuszono konsekwentne przestrzeganie przyjętych procedur.
Przy okazji wprowadzono rejestrację „braków”, które zostały poddane systemowej i fizycznej likwidacji, czyli zanim fizycznie zutylizowano zidentyfikowane „braki”, powstawał dokument „likwidacja” jako dokument obrotowy aktualizujący stany magazynowe. Decyzję o likwidacji podejmowała komisja powołana na stałe. Zadaniem komisji było także dyscyplinowanie dostawców, a także „uwrażliwianie” pracowników produkcji na jakość stosowanych w kolejnych operacjach surowców i części. Działania te przyniosły poprawę zarówno poziomu jakości dostarczanych surowców i materiałów, jak również samych wyrobów gotowych przez prawie całkowitą eliminację tego, co nie spełniało wymogów, a do tej pory często bywało tolerowane. Dwa w jednym.
Wprowadzenie ZSI (zintegrowanego systemu informatycznego) wymusiło na odpowiedzialnych pracownikach uporządkowanie struktur kartotek – indeksów materiałowych, powołano do życia stanowisko, którego podstawowym zadaniem było właśnie „czuwanie” i przestrzeganie raz przyjętych zasad określania składni indeksów materiałowych, których wizualną postacią stały się kody kreskowe EAN – GS1 128.
Przykład drugi
Za przykład drugi może posłużyć duża firma tekstylna – producent tkanin i wyrobów gotowych z tych tkanin. Tu problemem był brak wdrożonego modułu produkcji ZSI. Cała produkcja, łącznie z zakładem wykończalni, rozliczana była z metrów bieżących, które w magazynie wyrobów gotowych zamieniały się w sztuki powstałych wyrobów gotowych. Porównanie metrów bieżących opuszczających dział wykończalni z ilościami sztuk w magazynie wyrobów gotowych odbywało się raz w miesiącu. Trwało to bardzo długo ze względu na rozległy asortyment – ale prawie zawsze ta procedura kończyła się powodzeniem.
Znikające bele
Panujące w zakładzie sformalizowane – wręcz skostniałe – kontakty między wydziałami oraz przestarzałe procedury dopuszczające powstawanie tzw. ubytków naturalnych zachęcały pracowników do postępowania nie zawsze uczciwego. Od czasu do czasu pojawiały się doniesienia o nielegalnym handlu pochodzącymi z zakładu tkaninami. Drobiazgowo prowadzone postępowanie wyjaśniające wykazało, iż między tkalnią a farbiarnią brak było jasnych procedur pozwalających jednoznacznie określić, jaka ilość w metrach bieżących (powstałych wcześniej z ton surowca) winna trafić do wykończalni po zakończeniu procesu barwienia. Właśnie na drodze z farbiarni „znikały” całe bele tkaniny wyjeżdżające z zakładu w zaplombowanych big bagach z odpadami, które przekazywane były do jednego z podzakładów w celu dalszego wykorzystania. Podobnie jak u producenta mebli, tu również brak było precyzyjnych procedur zmierzających do wykluczenia różnic między tonami wykorzystywanego surowca (bawełny) a ilościami otrzymanej tkaniny, będącej zarówno materiałem handlowym, jak też i materiałem wyjściowym do produkcji wyrobów gotowych.
Ograniczenie niedoborów
Wprowadzone rozwiązania ograniczyły, ale nie wyeliminowały w 100 stu procentach możliwości powstawania „niedoborów”. Zwiększono kontrolę wywozu odpadów oraz obniżono wartości ubytków naturalnych. Dodatkowym działaniem pozwalającym na ograniczenia ubytków było zrewidowanie dotychczas obowiązujących zasad w zakresie prowadzenia kontroli jakości kupowanego surowca. W przedsiębiorstwie pojawiło się stanowisko klasyfikatora bawełny, chociaż nadal badania zanieczyszczeń, długości włókien, klasy koloru były podstawowymi badaniami jakościowymi sprowadzanego surowca.
Działania logistyki
Na samym etapie produkcji – od jej pierwszego kontaktu z magazynem surowców, aż po kontakt ostatni z magazynem dystrybucji – istnieje wiele zadań do realizacji typowych jedynie dla logistyki produkcji, np.: śledzenie przepływów na linii technologicznej, stopnia przetwarzania, pojawiania się kolejnej postaci przetwarzanych materiałów, aż do pojawienia się wyrobu gotowego. Są to działania w znakomity sposób ułatwiające kontrolę realizacji zamówień odbiorców i których dokonuje się poza zadaniami związanymi z transportem wewnątrz- i międzywydziałowym, z „karmieniem” ZSI aktualnymi danymi, ciągłym uaktualnianiem BOM-ów, itd.. Jeśli wielkość (jednostki naturalne i finansowe) i skład każdego z tych strumieni znajdzie swoje uzasadnienie w systemowym działaniu, w postaci dającego się wygenerować dokumentu, to można powiedzieć, że wdrożenie systemu się powiodło, a 2 + 2 = 4.