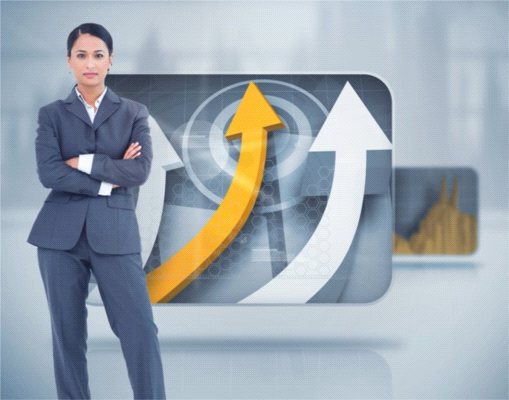
Dążenie do efektywnej produkcji
Od czasu kiedy wydano słynną książkę The Machine That Changed the World autorstwa Jamesa Womacka i Daniela Jonesa minęło 20 lat. W publikacji zaprezentowano wyniki kilkuletnich badań dokumentujących przewagę modelu Lean nad modelem produkcji masowej. W przełomowych latach 90...
Jednak ta metoda zarządzania wciąż nie jest powszechnie stosowana, chociaż efekty, które przynosi, robią wrażenie na największych światowych koncernach. Tym bardziej warto przyjrzeć się z bliska sposobom jej implementacji na przykładzie Borg Warner Cooling Systems – niemieckiej firmy z sektora automotive.
W dobie silnej konkurencji, praktycznie w każdym sektorze przemysłu, pojawia się coraz większa potrzeba efektywnego zarządzania, którego celem jest skuteczne i ekonomiczne gospodarowanie zasobami. Poczynając od kapitału ludzkiego, przez szeroko rozumiane procesy produkcji, aż do zarządzania parkiem maszynowym. Innymi słowy, tylko ta firma, która jest w stanie szybko wykryć błędy i straty na wszystkich poziomach – od rachunkowości administracyjnej do produkcji – może stale optymalizować swoją wydajność, poprawiając tym samym konkurencyjność.
Naprzeciw tym oczekiwaniom wychodzi filozofia Lean Manufacturing. Jej istotą jest zarządzanie polegające na konsekwentnym i kompleksowym eliminowaniu strat wynikających z marnotrawstwa czasu, siły roboczej, materiału czy energii. Według autora koncepcji TPM Nakajima Seiichii, sześć największych źródeł strat w produkcji związanych jest z: awariami, przezbrojeniami, złą jakością produktu, krótkimi zatrzymaniami (mikroprzestoje), zmniejszoną szybkością obróbki, przygotowaniami do pracy (rozruch).
Efektem „szczupłego wytwarzania” powinno być natomiast utrzymanie wysokiej jakości i wydajności produkcji, przy jednoczesnym obniżeniu kosztów. Firmą wspierającą przedsiębiorstwa produkcyjne w optymalizacji metodą Lean jest niemieckie przedsiębiorstwo Forcam GmbH, obecne od niedawna również na polskim rynku, które opracowało dla Borg Warner dostosowany do indywidualnych wymagań system zarządzania produkcją.
Problem i cel
Fabryka Borg Warner Cooling Systems w Niemczech jest częścią amerykańskiego koncernu – dostawcy w sektorze automotive, posiadającego 60 fabryk ulokowanych w 19 krajach. Fabryka w Markdorfie jest jedną z nich. Zakład zajmuje się produkcją systemów chłodzenia silnika dla samochodów, jak również dla ciężkiego sprzętu budowlanego oraz maszyn rolniczych. Zatrudnia obecnie 320 pracowników. Kluczowym problemem w fabryce była niska wydajność produkcji spowodowana m.in.:
- brakiem dokładnych pomiarów rzeczywistego wskaźnika OEE (Ogólna Wydajność Sprzętowa)
- zarządzaniem w modelu zdalnym i niewystarczającą wiedzą o procesach produkcji ze strony menedżerów
- brakiem informacji o problemach technicznych w czasie rzeczywistym w różnych jednostkach zakładu
- brakiem synchronizacji działań pomiędzy halą produkcyjną a administracją (ERP – Produkcja)
- niską kulturą CIP (Proces ciągłego doskonalenia)
Powodowało to straty w postaci nieefektywnego wykorzystania kapitału ludzkiego, energii i czasu, w efekcie przekładając się na duże straty finansowe.
Celem głównym wdrożenia stało się więc dążenie do bardziej efektywnej produkcji poprzez: integrację Lean Manufacturing oraz zmiany w sektorach: Organizacyjnym, Metod i procedur oraz Narzędzi.
Jeżeli nie jesteś w stanie czegoś zmierzyć, nie dasz rady tego usprawnić – stwierdzenie Lorda Kelvina zaadaptowane na potrzeby koncepcji Lean Manufacturing jest jak najbardziej adekwatne. Dlatego tak ważne w „szczupłej produkcji“ są dokładne pomiary, czy to pracy maszyn, czy całych procesów produkcyjnych. W Borg Warner również zastosowano tę zasadę, stosując oprogramowanie Factory FrameWork, które dla fabryki w Markdorfie kompleksowo i systematycznie przetwarza dane operacyjne z 40 maszyn.
Dzięki kompleksowemu monitoringowi, który umożliwia wizualizację bieżącego stanu produkcji w trybie on-line, jak na dłoni widać było wszystkie „słabe” obszary produkcji w Borg Warner (błędy techniczne, logistyczne i organizacyjne). Te dane, precyzyjnie analizowane przez system, pozwoliły na usprawnienie procedur i procesów, które doskonalone są systematycznie do chwili obecnej.
Wynikiem monitoringu są wiarygodne i porównywalne dane wydajnościowe dotyczące cyklu życia, szybkości i jakości produkcji maszyn, systemów i fabryki. Niemiecki producent otrzymuje więc informację kluczową – rzeczywisty wskaźnik OEE. Obliczanie OEE opiera się na stosunku trzech kluczowych parametrów produkcyjnych, monitorowanych i wizualizowanych w czasie rzeczywistym. Są to: dostępność (ile czasu mogłoby zostać przeznaczone pod produkcję?), wydajność (jak szybko zakład produkował?), jakość (jak dobrze zakład produkował?). Na podstawie tych danych zmierzono, że produktywność w Borg Warner Cooling Systems wzrosła o 4,3% zaledwie w przeciągu 6 miesięcy od rozpoczęcia wdrożenia.
Właściwe dane dla właściwej osoby we właściwym czasie
Co to tak naprawdę oznacza? Przede wszystkim optymalizację na wszystkich etapach procesu produkcji w Borg Warner. Od mistrza do menedżera: wszystkie zaangażowane osoby są stale włączone w proces optymalizacji wydajności na ich odcinku pracy.
Każdy pracownik biorący udział w procesie produkcji w Borg Warner Cooling Systems otrzymuje kluczowe dla niego dane, umożliwiające szybką reakcję i korektę działań. Dla lidera produkcji są zbierane dane dotyczące zmiany produkcyjnej, wyświetlane w sposób graficzny i tabelaryczny. Pozwala to na jasny przegląd wszystkich obszarów produkcyjnych, jak również zakłóceń i przestojów. Planista otrzymuje wsparcie w postaci informacji o opóźnieniach i zakłóceniach w produkcji. Otrzymuje on również dane związane z kalkulacją kosztu produktu, analizę porównawczą wyznaczonego celu ze stanem faktycznym czy wskaźniki dotyczące czasu produkcji i przezbrojeń. Dzięki temu może szczegółowo zaplanować m.in. redukcję cyklu pracy, czasy przestoju, nastaw i przezbrojeń, skuteczniej wykorzystując moc przerobową w fabryce. Sektor utrzymania ruchu otrzymuje natomiast dane o awariach w postaci graficznego przedstawienia danych – diagram Pareto (“hit lists“ awarii). Dla tego działu dostępne jest szczegółowe, siedmiostopniowe pogrupowanie problemów związanych z awariami.
Dzięki integracji oprogramowania Forcam z SAP ERP pracownicy Borg Warner otrzymują również w czasie rzeczywistym zwizualizowane dane dotyczące zleceń produkcyjnych, operacji oraz dane z maszyn. Oprogramowanie wykonuje również mapowanie kodów błędów: informacje o przestojach są zbierane samodzielnie i bezpośrednio z kontrolera maszyny lub alternatywnie – wprowadzane przez operatora z użyciem terminala (worker-client).
Na wdrożeniu zyskała też kadra kierownicza. Menedżerowie produkcji mają bowiem dostęp do sprawozdań i analiz porównawczych z wykorzystaniem wskaźników operacyjnych na wszystkich maszynach, dzięki czemu złe planowanie jest łatwo zauważalne. Zostali również przeszkoleni w zakresie tworzenia i rozwijania w organizacji kultury CIP (Continuous Improvement Process). Należy bowiem pamiętać, że reorganizacja przedsiębiorstwa w stylu Lean Manufacturing nie kończy się na samym wdrożeniu rozwiązań technologicznych, ale jest procesem ciągłym, polegającym na systematycznym doskonaleniu. W Borg Warner wprowadzono model zarządzania top-down, w którym wszystkie stanowiska produkcyjne bez wyjątku – od operatora maszyny do kierownika zakładu – są wspierane przez Zaawansowaną Technologię Zarządzania Produkcją (SFM).
Dla pracowników prowadzone są okresowe spotkania w ramach CIP, które służą praktycznemu wykorzystaniu danych uzyskanych w czasie rzeczywistym z hali produkcyjnej i odnoszących się do monitorowania, analizowania i ustanawiania celów związanych z zagadnieniami takimi jak: przestoje w pracy/awarie, proces produkcji, organizacja, jakość, optymalizacja narzędzi czy logistyka.
Rezultaty wdrożenia
Dzięki implementacji spełniono wszystkie zakładane cele wdrożenia. Przede wszystkim uzyskano dokładny pomiar kluczowych wskaźników, w tym rzeczywisty wskaźnik OEE. Wykazano, że faktyczna produktywność zakładu wzrosła o 4,3 % w ciągu pierwszych 6 miesięcy od wdrożenia.
Wdrożenie oprogramowania Factory Framework umożliwiło także zsynchronizowanie działań pomiędzy halą produkcyjną a administracją (ERP), dzięki czemu nastąpiła całkowita integracja danych: począwszy od maszyn, zleceń produkcyjnych, zasobów, a kończąc na personelu (pracownicy i kierownictwo).
Zmieniono model komunikacji. Z zarządzania zdalnego Borg Warner przeszedł na model CIP, który angażuje wszystkich pracowników odpowiedzialnych za proces produkcji. Umożliwiło to redukcję opóźnień związanych np. z obiegiem informacji – przed wdrożeniem obowiązywała komunikacja e-mail, telefoniczna i papierowa, po wdrożeniu wszystkie dane wyświetlane są w czasie rzeczywistym on-line. Dane te dostępne są (w określonym zakresie) dla każdego uczestnika procesu CIP. Menedżerowie posiadają wiedzę o procesach produkcji, co ułatwia podejmowanie kluczowych decyzji w trybie natychmiastowym.
Podsumowując, w fabryce Borg Warner Cooling Systems uzyskano wysoką przejrzystość realizacji zleceń produkcyjnych, jak i cykli pracy maszyn. Problemy produkcyjne są natychmiast rozpoznawalne oraz dokładnie analizowane. W przedsiębiorstwie rozwijana jest kultura CIP. Całkowita efektywność fabryki jest mierzona i poprawiana w trybie stałym. Pozwala to na ciągłe podnoszenie produktywności przedsiębiorstwa i zwiększa jego konkurencyjność na światowym rynku dostawców automotive.
W efekcie tak skutecznego wdrożenia w Markdorfie, na wprowadzenie technologii Forcam zdecydowała się również fabryka Borg Warner Turbostystem, znajdująca się w Rzeszowie. Co więcej, po wdrożeniu oprogramowania w rzeszowskim zakładzie władze Borg Warner Turbosystem podjęły decyzję o realizacji projektu typu roll-out, obejmującego inne fabryki tej dywizji.