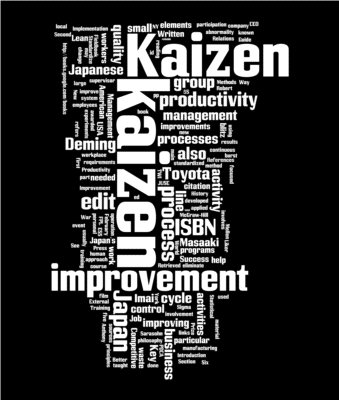
Ewolucja w stylu Kaizen
Kaizen to filozofia ciągłej poprawy, zakładająca, że każdy proces może i powinien być ciągle oceniany i doskonalony w zakresie wymaganego czasu, zużywanych zasobów, jakości i innych jego aspektów.Kaizen nie zawęża się jedynie do systemów produkcyjnych, ale oznacza także...
Kaizen nie zawęża się jedynie do systemów produkcyjnych, ale oznacza także ciągłe doskonalenie w życiu osobistym, domowym, społecznym i zawodowym. Korzenie zastosowania Kaizen w zarządzaniu przedsiębiorstwem znajdują się w koncernie Toyota, gdzie stał się nieodłącznym i kluczowym elementem najlepszego współcześnie systemu produkcyjnego na świecie, znanego jako Toyota Production System (TPS). Za przykładem Toyoty poszły kolejne firmy branży motoryzacyjnej, początkowo japońskie, a następnie inni producenci samochodów na całym świecie. Aktualnie trudno jest znaleźć przedsiębiorstwo branży motoryzacyjnej, elektronicznej czy AGD, które nie rozwijałoby Kaizen w zarządzaniu, czy to jako samodzielnej strategii, czy też jako kluczowego elementu Lean Manufacturing. Także większość zagranicznych inwestorów, którzy lokalizują produkcję w Polsce, opiera zarządzanie w swoich zakładach produkcyjnych na podejściu Kaizen.
Małe nakłady
Kaizen oznacza poprawę osiąganą małymi krokami bez dużych nakładów inwestycyjnych. Wiele usprawnień można osiągnąć przy małych środkach lub bez wydatków. Zamiast inwestowania dużych nakładów w środki trwałe, inwestuje się w ludzi. Masaki Imai, niestrudzony propagator koncepcji Kaizen, twórca i prezes KAIZEN Institute, w swojej książce zatytułowanej po prostu „Kaizen” napisał następujące słowa: „Nawet największy głupiec jest w stanie zwiększyć produktywność, jeśli wyda na to odpowiednio dużą ilość środków. Prawdziwą sztuką jest zwiększenie produktywności bez dodatkowych inwestycji w nowe urządzenia i technologie”.
Właściwie wdrażany Kaizen może bez dużych inwestycji lub wprowadzania nowych technologii poprawić jakość, znacznie zredukować koszty i wyjść naprzeciw wymaganiom klientów dotyczącym realizacji dostaw czy realizacji usługi.
Gemba Kaizen
Ciągłe doskonalenie może przebiegać tylko w konkretnym miejscu działania zwanym w języku japońskim gemba. Oznacza ono rzeczywiste miejsce, gdzie przebiega rzeczywiste działanie. W przedsiębiorstwie gemba mieści się na hali produkcyjnej, w miejscu produkcji gdzie przebiegają działania dodawania wartości dla klienta. Przy czym wartość stanowi to, za co klient jest gotów zapłacić.
Tylko to może podlegać ciągłemu doskonaleniu, co jest regularnie mierzone
Gemba Kaizen to podejście w zarządzaniu polegające na ciągłym doskonaleniu procesu kreowania wartości poprzez rozwiązywanie problemów w gemba, przy zaangażowaniu wszystkich, zarówno kierowników, jak i pracowników operacyjnych. Nieodzownym warunkiem powodzenia ciągłego doskonalenia jest znajomość gemba i faktycznie przebiegających tam procesów. Inicjatywa zmian wychodzi nie „z góry”, ale z samego miejsca pracy; menedżer, który zna gemba, może zarządzać jego doskonaleniem. Ma ono sens tylko w konkretnym miejscu pracy na hali produkcyjnej czy w miejscu kontaktu z klientem, czyli tam, gdzie jest dodawana wartość. Zrozumienie tego, co faktycznie dzieje się na danym stanowisku pracowniczym jest podstawą wszelkich usprawnień w ramach Kaizen.
Zasady Kaizen
W strategii Kaizen przyjmuje się, że nie jest możliwe zarządzanie czy rozwiązywanie problemów „zza biurka”. Kierownictwo nie może utrzymywać kontaktu z „rzeczywistością” jedynie poprzez dzienne, tygodniowe czy miesięczne raporty i spotkania. Niezmiernie ważne dla skutecznego i efektywnego zarządzania miejscem wytwarzania produktów i usług jest pozostawanie w bliskim kontakcie z gemba, jego bezpośrednia analiza, ocena i zrozumienie. Osiąga się to poprzez stosowanie się do poniższych zasad.
Złote zasady zarządzania gemba:
- Kiedy pojawia się problem, najpierw należy iść do gemba – zasada ta odnosi się również do rutynowego odwiedzania gemba przez kierowników czy osoby nadzorujące i obserwowania tego, co tam się dzieje. Ten nawyk należy wykorzystywać przy rozwiązywaniu specyficznych problemów i dla generowania pomysłów na ciągłe doskonalenie.
- Należy obserwować znajdujące się tam rzeczywiste przedmioty (jap. gembutsu). Może to odnosić się do popsutej maszyny, wadliwego czy reklamowanego produktu, a nawet niezadowolonego klienta.
- Należy od razu podejmować tymczasowe środki zaradcze, szybko usuwające objawy.
- Należy znaleźć przyczynę źródłową problemu. Przyczynę źródłową rozpoznaje się zadając kilkakrotnie pytania „dlaczego?”
- Należy opracowywać standardy, by zapobiegać ponownemu wystąpieniu problemu. Po potwierdzeniu skuteczności środków zaradczych należy wprowadzić standardy nowego postępowania,
Stosując powyższe zasady, każda nieprawidłowość będzie wywoływała działania Kaizen, które z kolei będą doprowadzać do wdrażania nowych standardów i/lub poprawiania już istniejących, co zapewnia ciągłość efektów Kaizen.
Proces ciągłego doskonalenia jakości, kosztów i dostawy przebiega skutecznie w małych samodzielnych jednostkach organizacyjnych, które mogą elastycznie dopasowywać się do potrzeb klientów. Tymi jednostkami mogą być organizacje (komórki) przedmiotowe lub jednostki ustawione sekwencyjnie jedna za drugą, przy czym każda odpowiada za określony odcinek linii produkcyjnej. W takim przypadku tylko ostatnia jednostka ma bezpośredni kontakt z zewnętrznym klientem, a pozostałe mają klientów wewnętrznych. Poprzez regularne ankietowanie klientów oceniana jest skuteczność wprowadzanych ulepszeń ukierunkowanych na poprawę zadowolenia klientów.
Jasne cele
Warunkiem skutecznego rozwijania Kaizen w przedsiębiorstwie jest jasno określony cel. W procesie formułowania strategii firmy najwyższe kierownictwo określa główne cele strategiczne oraz cele cząstkowe. Muszą one zostać przekształcone w bardziej szczegółowe i konkretne cele oraz plany, wyrażone odpowiednimi miernikami, które są zrozumiałe dla niższych poziomów struktury organizacyjnej, a w szczególności dla poziomu operacyjnego. Na przykład: główny cel to obniżka kosztów o 10 procent, a cele cząstkowe to wzrost produktywności o 5 proc. i redukcja wielkości zapasów o 20 proc. w danym roku. Z celów tych będą wynikały cele i plany wyrażone za pomocą takich mierników jak np. wskaźnik OEE, wskaźnik rotacji zapasów, PPM (Parts Per Milion – liczba wadliwych części na milion możliwych), wskaźnik udziału czasu dodawania wartości w cyklu produkcyjnym, itd. Cele operacyjne, plany i osiągane rezultaty powinny być przejrzyście eksponowane za pomocą wykresów w miejscach dostępnych dla każdego pracownika. Tylko to może podlegać ciągłemu doskonaleniu, co jest regularnie mierzone.
Jednym z celów ciągłego doskonalenia jest jak największe zbliżenie czasu realizacji procesu do czasu tworzenia wartości
Masaaki Imai twierdzi, że wszystkie działania kierownictwa związane z Kaizen mają tylko wtedy znaczenie, jeżeli prowadzą do zwiększonej satysfakcji klienta w zakresie kosztów i jakości. Ostatecznie to klienci ustalają standardy jakości, a robią to przez podejmowanie decyzji, jakie produkty kupić i od kogo. Kluczowe instrumenty rozwijania Kaizen w przedsiębiorstwie to: utrzymanie stanowiska pracy zgodnie z zasadami 5S, standaryzacja, eliminacja marnotrawstwa.
Stanowiska pracy – 5S
Doskonalenie organizacji, porządku i czystości fizycznego stanowiska pracy zgodnie z zasadami 5S jest jednym z kluczowych instrumentów rozwijania strategii Kaizen w przedsiębiorstwie, umożliwiającym zaangażowanie pracowników w procesy ciągłego doskonalenia. Wyróżnia się pięć następujących zasad, a jednocześnie kroków właściwego utrzymania stanowiska pracy, czyli tzw. 5S.
Utrzymywanie stanowiska pracy – 5S
- Sortowanie (jap. seiri) – polega na odróżnianiu na stanowisku pracy rzeczy niezbędnych od tych, które są zbędne i usunięciu tych zbędnych.
- Systematyka (jap. seiton) – polega na porządkowaniu rzeczy niezbędnych, które pozostały po przeprowadzeniu selekcji, tak aby można łatwo z nich korzystać.
- Sprzątanie (jap. seiso) – utrzymywanie miejsca pracy, stanowiska roboczego i maszyn w czystości. Czyszczenie wszystkiego, narzędzi, maszyn, regałów, półek i podłogi.
- Standaryzacja (jap. seiketsu) – polega na znajdowaniu najprostszego i najefektywniejszego sposobu dla kroków 1,2,3 i ustanowieniu standardów dla ich wykonywania i powtarzania.
- Samodyscyplina (jap. shitsuke) – polega na budowaniu samodyscypliny i nawyku angażowania się w 5S poprzez utrzymywanie standardów i ich poprawianie. Każdy pracownik powinien przestrzegać zasad 5S jak swoich własnych.
Systematyczne postępowanie zgodnie z powyższymi zasadami prowadzi do osiągnięcia lepszej organizacji, efektywności i dyscypliny w miejscu pracy.
5S nie może być chwilowym programem czy akcją, ale musi się stać trwałą częścią codziennej pracy. Ważne jest też, aby pracownicy zaakceptowali kampanię 5S, zanim się ona zacznie, w celu zmniejszenia ich oporu wobec zmian. Przed wdrożeniem programu 5S należy omówić jego zasady oraz wskazać korzyści, jakimi są m.in.: stworzenie czystego, higienicznego, przyjemnego i bezpiecznego środowiska pracy, ożywienie gemba i skutkujące znaczną poprawą postaw i motywacji pracowników, eliminacja marnotrawstwa, ułatwienie pracy, zwalnianie przestrzeni, w konsekwencji poprawa wydajności pracy i redukcja kosztów.
Ocena i motywacja
Stosowanie 5S w gemba pomaga pracownikom nauczyć się samodyscypliny, a zdyscyplinowani pracownicy są zawsze zaangażowani i zainteresowani Kaizen. Można mieć wtedy pewność, że będą stosować się do standardów, które kierownictwo jest zobowiązane ustalić dla każdego z kroków 5S. Standardy te powinny uwzględnić sposoby oceniania postępów na każdym etapie. Powinno się regularnie robić przegląd postępów, ponieważ dopiero po zatwierdzeniu pierwszego kroku można przejść do następnego. Kierownictwo organizacji powinno również wzbudzić chęć rywalizacji wśród pracowników – oceniać stan 5S w każdym gemba oraz stosować odpowiednie bodźce (nagrody i „kary” mające dopingować do poprawy pozycji w rankingu).
Po uznaniu piątego kroku za zakończony kierownicy powinni się skupić na nowym celu, czyli na wzbudzeniu odpowiedniego zaangażowania i entuzjazmu dla zmian. Ponieważ często wraz z wysiłkiem pracowników włożonym w realizację działań 5S przychodzi zadowolenie i następuje stagnacja, ważne jest, aby nie pozwolić na przerwanie działań i na powrót do stanu wyjściowego. Kierownictwo musi budować system zapewniający ciągłość działań zmierzających do odpowiedniej organizacji stanowisk pracy.
Kierownicy powinni także dawać przykład, zaczynać od kroków 1,2,3 w określonym obszarze swojego biura, gasić światło, gdy idą na obiad, podnosić przedmioty z podłogi, nigdy nie pozostawiać problemów bez rozwiązania, utrzymywać swoje standardy, stosować harmonogramy i monitoring ich realizacji, zawsze dokumentować i wizualizować poprawę, zawsze prezentować zdjęcia warunków pracy przed i po każdym kroku (zdjęcia powinny mieć datę, a także zaznaczone miejsce, gdzie została dokonana zmiana). Korzyści z wdrażania i przestrzegania zasad 5S można podzielić na wymierne i niewymierne.
Korzyści stosowania 5S
Korzyści wymierne:
- zmniejszenie opóźnień i liczby braków
- redukcja pomyłek i błędów oraz mniej strat czasu na szukanie
- wyższa jakość
- redukcja i eliminacja zbędnych działań
- większe bezpieczeństwo pracy
- zmniejszenie liczby awarii urządzeń
- sprawniejsza i uproszczona kontrola przebiegu produkcji
Korzyści niewymierne:
- lepiej zorganizowane stanowiska pracy
- schludniejsze stanowiska pracy
- wzrost bezpieczeństwa pracy
Przykłady z Polski
Ideę czystych i dobrze zorganizowanych stanowisk roboczych świetnie oddaje następujący przypadek: zakład produkcyjny koncernu GKN zlokalizowany w Polsce na Dolnym Śląsku był w początkowej fazie rozwijania Kaizen, ale osiągnął już bardzo spektakularny wynik w zakresie jakości, a mianowicie 2 PPM (jedynie 2 wadliwe produkty na milion możliwych). Nowy menedżer produkcji obejmujący wówczas swoje obowiązki zaskoczył wszystkich swoim komentarzem: „Gratuluję sukcesu, ale na pierwszy rzut oka nie wiadomo z czego ta niewątpliwie wysoka jakość produkcji wynika”. Od tego momentu rozpoczęło się intensywne i kompleksowe wdrażanie zasad 5S w całym zakładzie produkcyjnym. Aktualnie hala produkcyjna pomalowana w jasnych kolorach „lśni” czystością, a stanowiska robocze uderzają uporządkowaniem i czystością. Umożliwia to szybkie rozpoznawanie problemów chociażby takich jak wycieki oleju z pras. Obecnie można już powiedzieć, że „widać bezpośrednio, z czego wynika wysokie bezpieczeństwo i jakość produkcji”.
Innym polskim przykładem rozwijania strategii Kaizen jest fabryka samochodów GM Manufacturing Poland pod Gliwicami, wcześniej Opel Polska. Przedsiębiorstwo od początku swojej lokalizacji w Polsce wdraża strategię Kaizen, dzięki czemu stale utrzymuje się w czołówce zakładów koncernu GM w Europie, zarówno pod względem jakości, jak i produktywności. Pracownicy wręcz mówią, że „kaizenowanie” stało się ich druga naturą. Stosują zasady 5S również w gospodarstwach domowych. Gdy wykonują pewne prace w swoich garażach, to układają narzędzia w kolejności ich zastosowania, a po skończeniu prac odkładają je na oznaczone miejsca. Wcześniej przeprowadzili selekcję rzeczy potrzebnych i niepotrzebnych. Oznacza to, że zasady 5S traktują jak swoje własne zasady, zgodnie z piątą zasadą „Samodyscyplina”.
Wykluczanie marnotrawstwa
Eliminacja marnotrawstwa to fundamentalny, zasadniczy i wymierny cel Kaizen. Marnotrawstwo przyczynia się do wzrostu kosztów, opóźnień, problemów z jakością i w konsekwencji niższej satysfakcji klientów. Rozpoznawanie i eliminacja muda jest kolejnym kluczowym elementem rozwijania strategii Kaizen w organizacjach. Muda, japoński termin określający marnotrawstwo (straty), to wszystko to, co nie przyczynia się do kreowania wartości dla klienta. Zrozumienie i rozpoznawanie muda w procesach jest pierwszym krokiem wdrażania Kaizen w organizacji. Praca jest serią procesów lub kroków, począwszy od surowców, a skończywszy na gotowym produkcie lub zrealizowanej usłudze. W każdym procesie wartość jest dodawana do produktu i przesyłana do następnego procesu. W każdym procesie zasoby (ludzie i maszyny) albo dodają wartość, albo jej nie dodają. Muda odnosi się do każdego działania, które nie dodaje wartości.
7 kategorii strat i marnotrawstwa typu muda
- Nadprodukcja – straty wynikające z produkowania więcej, niż potrzebuje w określonym czasie klient – bezpośredni odbiorca.
- Składowanie zapasów – straty wynikające z utrzymywania zapasów materiałów, produkcji w toku i wyrobów finalnych.
- Transport – straty wynikające z przemieszczania materiałów, półproduktów i produktów.
- Ruch – straty związane z przemieszczaniem się ludzi i wyposażenia.
- Oczekiwanie – straty związane z oczekiwaniem na ludzi, materiały, półwyroby i produkty.
- Defekty – straty wynikające z wystąpienia jakichkolwiek defektów. Defekty zawsze pociągają za sobą koszty braków, napraw, przeharmonogramowania itd.
- Niewłaściwe procesy – straty wynikające z braku dopasowania produktu i procesu. Straty te pojawiają się, gdy wkłada się w produkt więcej pracy, niż tego oczekuje klient oraz gdy używa się narzędzi, które są dokładniejsze, bardziej skomplikowane i droższe niż to konieczne.
W tradycyjnym podejściu zakłada się, że zwiększenie produktywności następuje poprzez pracowanie dłużej, ciężej i szybciej oraz zastosowanie dodatkowych maszyn i pracowników, podczas gdy Kaizen koncentruje się eliminacji strat i marnotrawstwa jako sposobu zwiększania produktywności.
Udział czasu dodawania wartości w łącznym czasie cyklu produkcyjnego często nie przekracza procenta. Oznacza to, że 99 proc. czasu realizacji przypada na działania niezwiązane z dodawaniem wartości, włączając w to oczywiście czas oczekiwania i bezczynności. Dlatego jednym z celów ciągłego doskonalenia jest jak największe zbliżenie czasu realizacji procesu do czasu tworzenia wartości.
Zaszczepienie świadomości
Najważniejsze w Kaizen jest nauczenie ludzi stosowania i utrzymywania właściwej postawy. Wymaga to zmiany sposobu myślenia i postrzegania pracy przez indywidualnych pracowników. Menedżerowie i pracownicy muszą zacząć traktować takie działania jak przezbrojenia maszyn, usuwanie awarii, transport, sortowanie, sprawdzanie, testowanie, a nawet kontrolę jakości produktów jako marnotrawstwo i definiować problemy, a następnie formułować sugestie ich redukcji lub eliminacji.
Skuteczne stymulowanie i motywowanie pracowników do zaangażowania w rozwiązywanie problemów redukcji i eliminacji strat nie jest łatwe, w szczególności w kulturze, gdzie nadrzędnym wobec sukcesu zespołu jest sukces indywidualnego pracownika, a satysfakcja z osiągnięcia planowanego wyniku jest niewystarczającą motywacją do angażowania się w rozwiązywanie problemów i doskonalenie.
Elementem koniecznym do zwalczania marnotrawstwa jest zaszczepienie jego świadomości oraz świadomości tworzenia wartości dodanej u wszystkich pracowników i całego kierownictwa. Budowanie świadomości odbywa się m.in. poprzez treningi, gdzie uczestnicy odbywają „spacer” po obszarze swojej organizacji i poszukują marnotrawstwa. Jest to bardzo ważne, ponieważ tylko organizacje, w których wszyscy pracownicy widzą marnotrawstwo, mogą poprawiać swoją konkurencyjność. Od pracowników nie oczekuje się wykonywania rutynowo swojej pracy, ale doskonalenia wykonywanych operacji poprzez wykorzystanie osobistego doświadczenia, wiedzy i kreatywności.
Ulepszenie PDCA
Standaryzacja, obok uporządkowanych i czystych stanowisk zgodnie z zasadami 5S oraz eliminacją strat z procesów, jest trzecim nieodłącznym i kluczowym elementem strategii Kaizen. Ciągłe doskonalenie powinno być rozwijane jako utrzymanie i poprawianie standardów pracy poprzez małe i stopniowe usprawnienia. W strategii Kaizen odpowiedzialność za utrzymanie standardów spada na pracowników, podczas gdy za poprawę standardów odpowiadają kierownicy.
SDCA standaryzuje i stabilizuje obecny proces, natomiast PDCA usprawnia
W procesie Kaizen wykorzystuje się cykl PDCA planuj-rób-sprawdź-działaj (ang. Plan-Do-Check-Act), który powinien zapewnić ciągłość działań dotyczących utrzymania i doskonalenia standardów. „Planuj” to ustalenie celu poprawy i planu działania umożliwiającego osiągnięcie tego celu. „Rób” oznacza wdrożenie usprawnienia. „Sprawdź” odnosi się do oceny poprawności wdrożenia i skuteczności usprawnienia w realizacji w procesie. „Działaj” oznacza wprowadzenie usprawnienia i standaryzację nowych procedur.
Nowe procedury muszą zastąpić dotychczasowe, celem uniknięcia ponownego wystąpienia wcześniejszych problemów, a także, aby ustalić punkt odniesienia do kolejnych usprawnień. Cykl PDCA jest powtarzalny i nigdy nie powinno się zadowalać stanem obecnym. To kierownictwo musi inicjować PDCA przez nieustanne stawianie pracownikom nowych ambitnych celów, gdyż pracownicy zwykle wolą stan istniejący i rzadko wykazują inicjatywę, by poprawić aktualną sytuację.
Standaryzacja SDCA
Zanim zacznie się kolejne usprawnianie zgodnie z cyklem PDCA, wszelkie aktualne procesy muszą zostać ustabilizowane. W tym celu wykorzystuje się cykl SDCA, standaryzuj-rób-sprawdź-działaj (ang. Standardize-Do-Check-Act). Tylko jeśli standard został ustalony i jest przestrzegany, a proces stabilny, można przejść do wprowadzania nowego usprawnienia. SDCA standaryzuje i stabilizuje obecny proces, natomiast PDCA usprawnia. Cykle te odnoszą się odpowiednio do utrzymania usprawnienia i dalszego usprawniania – czyli do głównych celów zarządzania w strategii Kaizen. Zadaniem menedżerów jest wprowadzanie standardów, podczas gdy zadaniem pracowników jest ich utrzymanie.
Podstawowe cechy i korzyści standardów
- Określają najlepszy, najłatwiejszy i najbezpieczniejszy sposób wykonywania danej czynności.
- Zapewniają zachowanie know-how firmy. Bez formalnych standardów wiedza na temat sposobów najlepszego wykonania określonych czynności pozostaje jedynie w pamięci pracowników. Jest to sytuacja bardzo ryzykowna, ponieważ wiedza ta zostanie utracona w wypadku odejścia pracownika z firmy.
- Określają kryteria oceny wykonania. Bez odpowiednich standardów nie będzie możliwa właściwa ocena wykonywanej pracy.
- Stanowią punkt odniesienia do utrzymania i dalszej poprawy funkcjonowania. Przestrzeganie standardów oznacza utrzymanie jakości wykonania na określonym poziomie, podczas gdy ciągłe podnoszenie poprzeczki jest równoznaczne z ciągłą poprawą.
- Wyznaczają cele szkolenia pracowników. Standardy, czy to w postaci dokumentów, czy też w innej formie, mają wskazywać, czego należy się nauczyć.
- Stwarzają odpowiedni system samokontroli i nadzoru. Umieszczenie zapisu standardów pracy w hali fabrycznej ma przypominać pracownikom o konieczności ich przestrzegania.
- Dają stały punkt odniesienia i pomagają zapobiegać powtarzaniu się błędów.
Trzy kluczowe instrumenty rozwijania Kaizen w przedsiębiorstwie (5S, eliminacja, marnotrawstwa oraz standaryzacja) powinny być implementowane równolegle i komplementarnie. Jeżeli zabraknie jednego z tych filarów lub będzie on na niższym poziomie zaawansowania, to wdrażanie Kaizen okaże się mało skuteczne i efektywne w poprawianiu konkurencyjności przedsiębiorstwa.
KAIZEN Instytute – Do popularyzowania koncepcji Kaizen przyczynia się założony w 1985 roku przez Massaki Imai KAIZEN Institute. Ta międzynarodowa organizacja doradza przedsiębiorstwom na całym świecie. Zajmuje się m.in. działalnością szkoleniową, doradczą i wdrażaniem oraz audytem standardów i systemów ciągłego doskonalenia. Wspomaga w problematyce Kaizen przedsiębiorstwa każdej wielkości, każdego sektora gospodarki, również organizacje usługowe, a nawet instytucje sektora publicznego. KAIZEN Institute ma także swoje oddziały w Polsce, które prowadzą m.in. szkolenia i doradztwo w zakresie Kaizen.