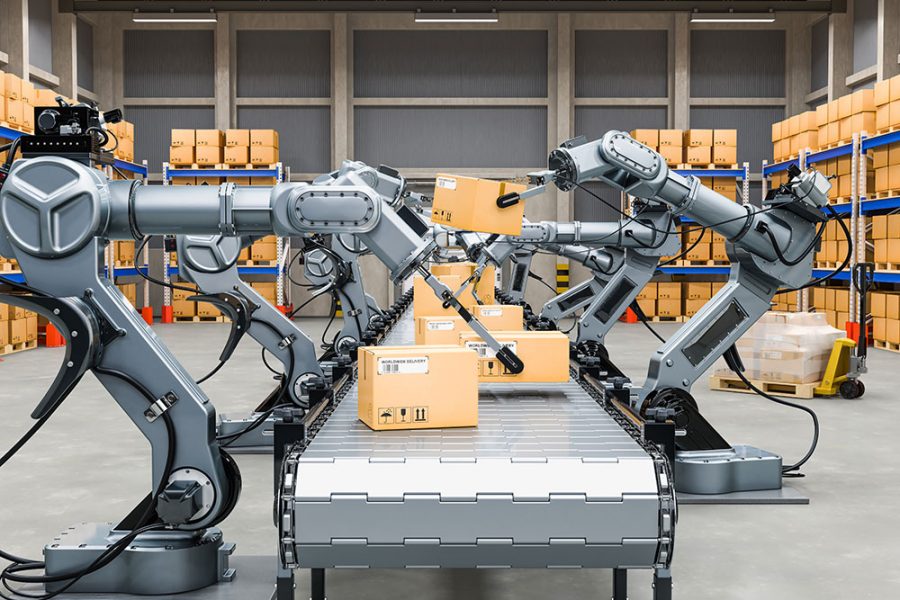
Granice automatyzacji magazynu
Technologie automatyzacji niskiego poziomu aż do futurystycznej koncepcji dark warehouse. Gdzie leżą granice automatyzacji magazynu i jakie bariery w procesie automatyzacji napotykają przedsiębiorstwa.
Zalety płynące z automatyzacji magazynu to przede wszystkim większa wydajność, szybszy czas realizacji zleceń, mniejsza ilość błędów i niższe wydatki na pensje pracowników. Wadami zaawansowanych systemów automatyki są wysokie koszty inwestycji i mniejsza elastyczność procesów. W wysoce zautomatyzowanym magazynie znacznie trudniejsze staje się skalowanie wydajności pracy, co dobrze ilustrują sezonowe wahania popytu. Jeśli systemy automatyki zostaną zaprojektowana do pracy z wydajnością sezonowych maksimów, to przez resztę czasu ich potencjał nie będzie w pełni wykorzystywany.
Magazynom obsługiwanym manualnie łatwiej jest funkcjonować w warunkach sezonowo zmiennego popytu, dzięki możliwości regulowania poziomu zatrudnienia. Automatyczny magazyn nie jest w stanie płynnie dostosować się do zmian popytu, dlatego najlepiej sprawdza się wtedy, gdy poziom zleceń jest względnie stały przez cały rok.
Decyzja o inwestycji w automatykę jest łatwiejsza dla tych przedsiębiorstw, których magazyny pracują w wymiarze 24 godziny na dobę. Taki tryb pozwala szybciej uzyskać zwrot poniesionych nakładów.
Na jakie poziomy zaawansowania można podzielić automatyzację magazynu?
Automatyzacja niskiego poziomu
Do automatyzacji niskiego poziomu zaliczają się rozwiązania z zakresu automatycznej identyfikacji produktów i systemy informatyczne wspierających pracę magazynu.
Do technologii automatycznej identyfikacji towaru zaliczają się:
Terminale radiowe
Mobilne, wyposażone w skaner terminale radiowe, umożliwiają magazynierom dwukierunkową komunikację z informatycznym systemem magazynowym. Pracownik na wyświetlaczu terminala otrzymuje instrukcję określającą trasę zbiórki, ilość i rodzaj asortymentu oraz dokładne miejsce jego położenia. Urządzenia umożliwiają także wyświetlenie zdjęcia produktu i dodatkowych informacji o nim. Magazynier potwierdza wykonanie operacji skanując umieszczoną na produkcie etykietę. Mobilne terminale radiowe funkcjonują w oparciu o sieć Wi-Fi.
Kody kreskowe
Najstarsza i najczęściej stosowana metoda automatycznego rejestrowania, opiera się na wykorzystaniu etykiet zawierających kody kreskowe. Stanowi je układ czarnych i białych kresek, pozwalających zapisać informacje liczbowe i tekstowe.
Od pewnego czasu wzrasta popularność kodów QR (Quick Response Code), będących dwuwymiarową odmianą kodów kreskowych. Pozwalają one zapisać większą ilośc informacji, znajdują zastosowanie wszędzie tam, gdzie ważna jest szybkość odczytu (np. gdy towary są w ruchu). Kody QR, w przeciwieństwie do klasycznych kodów kreskowych, umożliwiają odczyt nawet w przypadku częściowego uszkodzenia lub zabrudzenia etykiety.
RFID (Radio frequency identification)
Zastosowanie technologii RFID polega na pobraniu przy pomocy anten informacji zawartej w znaczniku (chipie). Chipy RFID pozwalają na zapisanie większej ilości informacji niż etykiety z kodem kreskowym. W zależności od wersji, etykiety RFID mogą być przeznaczone tylko do odczytu, albo pozwalać na wielokrotne nadpisywanie danych.
Technologia RFID pozwala na odczytywanie etykiet z różnej odległość. Dla porównania, laserowy czytnik kodów kreskowych dobrze sprawdza się tylko na bliskich dystansach, albo tylko dalekich (modele typu long range). Inną zaletą RFID jest możliwość skanowania wielu etykiet jednocześnie.
Barierą w wykorzystaniu technologii RFID jest stosunkowo wysoka cena etykiet, a także trudności we współpracy z niektórymi grupami artykułów (np. z płynami, papierem w ryzach czy produktami w metalowych puszkach).
Bramki RFID
Bramki RFID służą do rejestrowania ruchu towarów lub osób na terenie zakładu. Składają się z części sprzętowej, zawierającej m.in. anteny do detekcji chipów, oraz oprogramowania umożliwiającego współpracę z nadrzędnym system informatycznym.
OCR (Optical Character Recognition)
OCR to systemy wizyjne, składające się z kamer i oprogramowania, pozwalające odczytywać znaki (litery, cyfry, kody kreskowe) umieszczone na artykułach. Metodę OCR wykorzystuje się przeważnie w sytuacji, gdy warunki środowiskowe lub wymiary i kształt przedmiotu uniemożliwiają zastosowanie etykiet z kodem kreskowym lub RFID.
DPM (Direct Part Marking)
DPM to technologia znakowania bezpośredniego. Najczęściej używana jest w sytuacji, gdy warunki środowiskowe uniemożliwiają zastosowanie innych rozwiązań.
Innym rozwiązaniem z zakresu automatyzacji niskiego poziomu jest oprogramowanie, takie jak informatyczne systemy zarządzania magazynem WMS (Wrehouse Management System). Pozwalają one zautomatyzować wiele operacji związanych z obsługą magazynu, w tym m.in.:
Inwentaryzacja
Oprócz zastąpienia papierowego dokumentów związanych z inwentaryzacją, systemy WMS oferują funkcje tzw. inwentaryzacji ciągłej. Dzięki niej można sukcesywnie kontrolować poszczególne lokalizacje magazynu, bez potrzeby przerywania jego pracy.
Zarządzanie miejscami zbiórki
Oprogramowanie WMS monitoruje dane dotyczące ilości towaru w miejscach zbiórki. Łączy je z danymi na temat stanu magazynowego artykułu oraz zapotrzebowaniem wynikającym z zamówień. Dzięki bieżącej analizie tych informacji, system może we właściwym momencie wygenerować zlecenie uzupełnienia miejsca zbiórki. Zapewnia to sprawny przepływ towarów w magazynie, przy minimalnym zaangażowaniu pracowników.
Przydział miejsc magazynowych
W oparciu o zdefiniowane strategie, system WMS może wyznaczyć optymalne dla danego towaru miejsce składowania. System może kierować się wieloma parametrami: klasa rotacji artykułu, odległość od miejsca zbiórki, stopień zapełnienia nośnika, wymiary nośnika, klasa ADR, czy podział na strefy magazynowe.
Wybór ścieżki kompletacji
System WMS może wyznaczyć najkrótszą drogę realizacji zbiórki. Program uwzględnia przy tym liczne kryteria i obostrzenia. Takich jak np. brak możliwości położenia jednego produktu na drugim, czy ograniczenia związane z ADR. W przypadku wydzielenia w magazynie stref zbiórki, system utworzy scenariusz kompletacji dla każdej strefy z osobna.
Systemy automatycznego składowania
Systemy te automatyzują proces składowania i kompletacji towarów. Na regałach zamiast palet znajdują się zazwyczaj pojemniki o ściśle określonych wymiarach. Zbiórka odbywa się dzięki wsparciu komponentów automatyki, na którą składają się regały przesuwne, układnice, przenośniki i transportery. Popularne typy regałów automatycznych to: regały z układnicami, windowe i karuzelowe.
Alternatywą dla automatycznych regałów wysokiego składowania jest struktura nazywana grid lub hive. Grid to przypominająca szachownicę, rozległa, horyzontalna struktura. W poszczególnych polach tej szachownicy mieszczą się pojemniki z asortymentem. Nad pojemnikami mogą poruszać się autonomiczne pojazdy prowadzące zbiórkę.
Automatyczne wózki magazynowe
Automatyczne wózki magazynowe podzielić można na dwa zasadnicze rodzaje: AGV (Automated Guided Vehicle) i (Autonomous Mobile Robots). Czym się od siebie różnią?
AGV to samojezdne wózki transportowe. Nawigacja odbywa się przy pomocy przewodów, pasków magnetycznych, czujników lub laserów. Oznacza to konieczność odpowiedniego przygotowania tras, wzdłuż których robotyAGV będą się poruszały. Ich użycie wiąże się z usztywnieniem organizacji ruchu w magazynie, a także kosztami dodatkowej infrastruktury.
AMR to autonomiczne pojazdy mobilne. Są bardziej zaawansowane i niezależne od robotów AGV. Przy poruszaniu się nie potrzebują specjalnie przystosowanych tras, wystarczy im wgrać cyfrowy plan obiektu. Dzięki posiadanym systemom, AMR mogą samodzielnie zmapować magazyn.
Wózki AMR posiadają zdecydowanie bardziej wszechstronne od AGV. Można w krótkim czasie zmienić trasę na jakiej operują, a także przypisać im nowe zadania. Są właściwym wyborem dla tych magazynów, które często mierzą się z różnego rodzaju zmianami.
Wybór pomiędzy AGV i AMR powinien być umotywowany indywidualnymi cechami magazynu. To jego charakterystyka fizyczna, ale też organizacja pracy, profil oraz zmienność operacji magazynowych i miejsc składowania.
Dark warehouse
Dark warehouse to stosunkowo nowa koncepcja w pełni zautomatyzowanego magazynu. Wszystkie procesy magazynowe, w tym przyjęcie towaru, składowanie, kompletacja i wysyłka realizowane są w nim przez maszyny. Brak przebywającego na stałe personelu powoduje, że przy bieżącej pracy magazynu nie potrzebne jest oświetlenie. Pierwszy tak automatyczny magazyn powstał w 2018 roku w Japonii i obsługuje jedną z największych chińskich platform e-commerce. Jedynymi pracownikami, którzy okresowo pojawiają się w magazynie są serwisanci.
Dark warehouse pozwala maksymalnie wykorzystać wszystkie korzyści płynące z automatyzacji magazynu. Wśród jego atutów (poza oszczędnością energii) można wymienić:
- Zmniejszenie powierzchni zajmowanej przez magazyn – wyeliminowanie wszelkich powierzchni niezbędnych przy manualnej obsłudze operacji pozwala znacznie ograniczyć rozmiar obiektu.
- Dzięki temu, że takie magazyny zajmują mniej miejsca niż ich tradycyjne odpowiedniki, można umieszczać je w bardziej dogodnych (co za tym idzie droższych) lokalizacjach, leżących np. blisko dużych miast. W wielu przypadkach może to skrócić czas realizacji zleceń i ograniczyć koszty dostaw.
- Dark warehouse niemal całkowicie eliminuje problem dostępności siły roboczej i radykalnie obniża jej koszty.
- Większe bezpieczeństwo – maksymalne ograniczenie ilości personelu przekłada się na ilość wypadków przy pracy, a także bezpieczeństwo produktów. Wiele towarów wymaga warunków przechowywania szkodliwych lub uciążliwych dla ludzi, a w dark warehouse ten problem nie występuje.
Jakie są bariery w popularyzacji dark warehouse?
Istotnymi barierami w realizacji i upowszechnieniu wizji dark warehouse są przede wszystkim:
- Wysokość nakładów i kwestia ROI – pełna automatyzacja magazynu wymaga bardzo wysokich nakładów finansowych. Trudno oszacować kiedy i czy w ogóle uda uzyskać się zwrot z takiej inwestycji.
- Niska dojrzałość modelu – o ile poszczególne komponenty automatyki magazynowej funkcjonują od lat, to całkowita automatyzacja jest zjawiskiem nowym. Oznacza to, że brakuje utartych schematów i podmiotów doświadczonych w tego typu wdrożeniach.
- Niskie możliwości adaptacji – obiekty typu dark warehouse są zaprojektowane do obsługi konkretnej grupy produktów. Jeśli pojawia się potrzeba wprowadzenia nowego rodzaju towaru, który na przykład znacznie różni się od innych gabarytami, może okazać się to niemożliwe.
- Konsekwencje społeczne – budowa w pełni zautomatyzowanego magazynu może wiązać się z koniecznością zwolnienia pracowników i wzrostu bezrobocia w regionie.
Rosnący stopień automatyzacji magazynu jest trendem od którego nie ma odwrotu. Wiedza o wymaganiach, ograniczeniach i ryzykach typowych dla różnych poziomów jej zaawansowania pomaga w podejmowaniu racjonalnych decyzji, właściwych dla sytuacji danego przedsiębiorstwa.