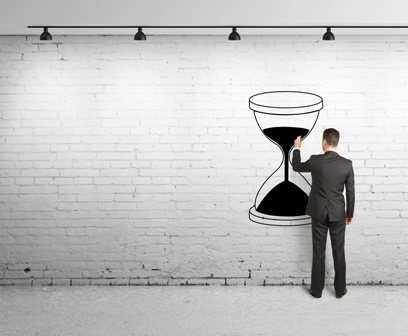
Lean logistics
Mało jest na świecie ludzi, którzy nie używaliby artykułów wyprodukowanych lub dostarczanych zgodnie z zasadami lean.I nie chodzi tu tylko o przemysł motoryzacyjny. Każdy był kiedyś przecież w MC Donalds, KFS, Subway lub pił Coca Colę i Pepsi, a każda kobieta kupowała kiedyś...
I nie chodzi tu tylko o przemysł motoryzacyjny. Każdy był kiedyś przecież w MC Donalds, KFS, Subway lub pił Coca Colę i Pepsi, a każda kobieta kupowała kiedyś produkty Johnson & Johnson. Wszyscy znamy takie marki, jak Nike, Kodak, Dell, Motorola, Intel, Sony, Samsung, Philips, Hitachi itp.
Lean production
Wystarczy przyjrzeć się ogólnym procesom produkcji. Czy widział ktoś, żeby w MC Donalds strugano ziemniaki lub mielono mięso na hamburgery, a w Subway wypiekano pieczywo, skubano kurczaki z piór czy pozbawiano łusk tuńczyki? Czy firma Dell produkuje chipy, procesory lub matryce LCD, a w fabryce LG są wtryskarki do produkcji obudów? Wiadomo przecież, że silniki do Boeingów są produkowane tysiące kilometrów od miejsca, które nazywa się fabryką samolotów i jest wielką montownią, czyli jak to Amerykanie nazywają: lean assembly. Aby zmontować Dreamlinera, który produkowany jest w fabryce Boeinga w Everett koło Seattle, potrzebna jest bardzo sprawnie działająca logistyka. Silniki Rolls-Royce produkuje się w Wielkiej Brytanii, skrzydła w fabryce Mitsubishi w Japonii, ruchome krawędzie skrzydła w fabryce Boeinga w Australii, centralny kadłub w zakładach Alenia we Włoszech itd. Czy w związku z tym fabryka działająca zgodnie z zasadami lean manufacturing potrzebuje jakiegoś specyficznego systemu logistyki? Tak – potrzebuje logistyki działającej zgodnie z zasadami lean. Nie należy zapominać, że pojęcie lean zostało wymyślone przez amerykańskich teoretyków, którzy próbowali zgłębić system produkcyjny Toyoty (ang. Toyota Production System), choć dzisiaj nikt na tę subtelność zdaje się nie zwracać specjalnej uwagi.
Czym zatem różni się lean manufacturing od lean logistics? Czy w łańcuchu dostaw nie mamy do czynienia z pojęciem MUDA (marnotrawstwo, a raczej jego eliminacja 5S, 5WHY, TPM, SMED, just-in-time? Podstawowa różnica pomiędzy lean manufacturing a lean logistics odnosi się jedynie do drugiego słowa.
Lean logistics
Lean logistics to w potocznym rozumowaniu logistyka bez marnotrawstwa. A ponieważ marnotrawstwa nie da się całkowicie wyeliminować, lean logistics to logistyka, która podejmuje zaplanowane, niekończące się działania mające na celu eliminację marnotrawstwa. Logistyka, która podejmuje takie działania, jest z reguły zorganizowana w sposób szokująco odmienny. Jej efektem może być zwiększenie szybkości i terminowości dostaw, ale nie rozumianej jako „pracuj ciężej, dłużej, za mniej”.
Typowe, publikowane rezultaty wdrożenia lean logistics to np. 30% podniesienie bezpieczeństwa, 30% zwiększenie błędów jakościowych, 30% zwiększenie produktywności wysyłek, 15% obniżenie poziomu zapasów.
Dopóki nie nauczymy się dostrzegać marnotrawstwa w swoim łańcuchu dostaw, w pojedynczym elemencie takiego łańcucha czy w zasobach, którymi zarządzamy, dopóty nic w organizacji się nie zmieni.
Finansista, zamiast eliminować marnotrawstwo, będzie dążył do obniżania kosztów funkcjonowania łańcucha dostaw w organizacji. W ten sposób być może osiągnie się mierzalne efekty finansowe, premie i awans, ale nie będzie to lean logistics.
Fundamentem lean jest poszanowanie ludzi. W organizacji lean muszą więc być jasne reguły współpracy. Wykonawcy zadań, czy to pracownik pracujący na linii montażu telewizorów w lean manufacturing, czy kierowca w lean logistics, muszą wiedzieć, że to właśnie oni są źródłem wiedzy na temat możliwości eliminacji marnotrawstwa i od ich zaangażowania, motywacji i samozadowolenia będzie zależało, w jakim stopniu przyczynią się do jego wyeliminowania. Lean logistics to kolejny wymiar lean manufacturing. Może dotyczyć zarówno logistyki wewnętrznej, międzyzakładowej, jak krajowej czy globalnej.
Muda w łańcuchu dostaw
Siedem typów muda zdefiniowanych przez ojca TPS Taichi Ohno nabiera nieco innego wymiaru w łańcuchu dostaw.
Muda nr 1 – nadprodukcja, czyli sytuacja, w której podaż przewyższa popyt, to w naszym przypadku dostarczanie materiałów, półproduktów, wyrobów gotowych szybciej, niż wymaga tego proces klienta. To np. błędna priorytetyzacja zadań, kolejkowanie środków transportu.
Muda nr 2 – oczekiwanie to np. czas pomiędzy przyjazdem samochodu w celu załadunku naczepy a opóźnieniem pomiędzy otrzymaniem informacji o zamówieniu klienta i rozpoczęciu jego realizacji, to zła synchronizacja czasowa procesów, przyjazdy przed czasem – w stosunku do okna czasowego przeznaczonego na obsługę dostaw przychodzących, to powolne uzupełnianie zapasów, to niezbilansowana praca.
Muda nr 3 – transport – to transport, który powoduje dodatkowy niepotrzebny koszt.
Muda nr 4 – niepotrzebny ruch – to np. podróże, spacery związane ze złym systemem składowania zapasów, mało ergonomiczną konstrukcją strefy pakowania, wieloetapowe procesy logistyczne (uzupełnianie zapasów), mała powierzchnia strefy wydań, angażowanie się w szukanie sprzętu.
Muda nr 5 – zapasy – dowolna aktywność logistyczna, której rezultatem jest umieszczenie większej liczby zapasów niż potrzeba lub nie w tej lokalizacji, gdzie potrzeba: obsługa wcześniejszych dostaw niż potrzeba, zamawianie i odbiór ilości większej niż potrzeba, dostawy do złych lokalizacji / magazynów / zakładów, obsługa zwrotów (od klientów), zwroty nieprzetworzonych materiałów (zaburzenia PP), zalegające zapasy nierotujące (zamrożony kapitał, deprecjacja), pojemniki wypełnione pojedynczymi SKU (nadmierna liczba pojemników).
Muda nr 6 – przestrzeń – złe wykorzystanie przestrzeni, która jest mniejsza/większa niż optymalna, opakowania (kartony, które nie są wypełnione po brzegi), nieoptymalne przewisy.
Muda nr 7 – braki i ich naprawa – dowolna aktywność wymuszająca wykonanie jeszcze raz tej samej pracy lub naprawy błędu: błędy na fakturach, dokumentach transportowych, arkuszach inwentaryzacyjnych, źle oklejone kody kreskowe, błędy w etykietach logistycznych, niekompletne zamówienia, uszkodzenia opakowania wymagające operacji przepakowania, uszkodzenia nośników logistycznych, uszkodzenia, defekty, wady wyrobów gotowych, towarów.
Wdrożenie lean logistics
Aby wdrożyć lean logistics, należy nauczyć się widzieć strumień wartości (jeden z pięciu elementów odchudzonego myślenia – lean thinking . Obnażyć jego stan bieżący, określić stan idealny i zaprojektować „n” stanów przyszłych.