
Ludzie, a nie technologia
Największe możliwości wzrostu i poprawy wyników w polskim sektorze produkcyjnym daje praca nad rozwojem potencjału pracowniczego a nie tylko cyfryzacja czy automatyzacja procesów – wynika z analiz firmy konsultingowo-wdrożeniowej 4Results. Firma opiera swoje wnioski na podstawie projektów reorganizacji działania przedsiębiorstw produkcyjnych z ostatnich trzech lat.
Pandemia koronawirusa nie zmieni, a wręcz nasili potrzebę poszukiwania wydajności fabryk. Przed jakimi zatem wyzwaniami stoją polscy producenci i gdzie mogą oni przede wszystkim szukać metod poprawy swoich wyników?
Sporo niedoskonałości
To nie cyfryzacja, nie robotyzacja i nie nowe metody zastosowania sztucznej inteligencji są obecnie największymi wyzwaniami dla polskiego przemysłu. Znacznie większe znaczenie dla poprawy wyników finansowych i wzrostu firm produkcyjnych ma odpowiednie wykorzystanie dostępnych w organizacjach zasobów ludzkich i ich właściwy rozwój. Tak twierdzą eksperci, którzy na co dzień zajmują się restrukturyzowaniem i poprawą efektywności przedsiębiorstw.
– Na podstawie doświadczeń z kilkudziesięciu projektów reorganizacji sposobu działania przedsiębiorstw zrealizowanych w ciągu ostatnich trzech lat można zaryzykować tezę, że dziś żadna z firm produkcyjnych pracujących w Polsce nie prowadzi produkcji w pełni efektywnie. Można nawet pójść dalej i powiedzieć, że ponad 90 proc. przedsiębiorstw działa w sposób niedoskonały, ponosząc w różnych punktach działania straty istotnie wpływające na całościowe wyniki finansowe. Główne powody uszczuplenia marży nie wynikają z braku rozwiązań informatycznych czy nowoczesnych technologii, ale z niewykorzystania potencjału pracowników i kadr zarządzających oraz ze złej organizacji pracy – mówi Izabela Starnawska, partner zarządzający w 4Results.
„Można nawet pójść dalej i powiedzieć, że ponad 90 proc. przedsiębiorstw działa w sposób niedoskonały, ponosząc w różnych punktach działania straty istotnie wpływające na całościowe wyniki finansowe.”
Uwolnienie potencjału drzemiącego w ludziach na wszystkich szczeblach organizacji, daje przedsiębiorstwom większe korzyści w porównaniu z nadmiarową koncentracją na wdrażaniu innowacyjnych rozwiązań. Co więcej – aby firmy mogły w pełni odczuć korzyści z nowoczesnych technologii i cyfryzacji, najpierw trzeba do tego odpowiednio przygotować pracowników.
W jaki sposób firmy tracą pieniądze?
4Results zaznacza, że sektor przemysłowy składa się z odmiennych branż, w których firmy działają w różnych modelach i skali. Dlatego odnoszenie danych statystycznych zebranych w poszczególnych branżach do szerokiego sektora może być mylące. Z całą pewnością można natomiast powiedzieć, że w polskich firmach produkcyjnych powszechnie występują zjawiska przyczyniające się do powstawania strat i obniżania efektywności. Poczynając od najczęściej spotykanych, są to:
- zbyt długi czas przezbrojenia maszyn i przygotowania parku maszynowego do realizacji nowych zleceń;
- niewłaściwe harmonogramowanie produkcji, niosące szkodliwe i groźne konsekwencje, po pierwsze w postaci nadprodukcji zbędnych SKU, co przyczynia się do zamrażania kapitału firmy i nadmiarowego obciążania magazynu, po drugie w postaci niepotrzebnie wydłużanego czasu realizacji zamówień klientów, co w licznych sytuacjach prowadzi do permanentnego przeciążania parku maszynowego i załogi oraz pogorszenia satysfakcji klientów;
- nieumiejętność organizacji stanowisk pracy lub brak konsekwencji w panowaniu nad efektywnością na stanowisku – poczynając od tego rozumianego fizycznie, objawiającego się ustandaryzowanym ułożeniem w hali produkcyjnej czy działach utrzymania ruchu maszyn, urządzeń, części i narzędzi oraz potrzebnych do pracy informacji czy oznaczeń, przez sposób ulokowania półproduktów i wyrobów gotowych w magazynach, aż po porządek rozumiany jako przepływ pracy, zleceń oraz informacji w całej organizacji (w zespołach, między liderami a grupami roboczymi, wśród liderów, pomiędzy wydziałami produkcyjnymi, w procesie produkcyjnym, między kadrą kierowniczą a pracownikami itd.);
- zbyt długie czasy realizacji zamówień – najczęściej problem polega na nieoptymalnym przepływie w procesie wytwarzania (np. niepotrzebnym ruchu półproduktów do kompletowania, niewłaściwej alokacji stanowisk przy taśmach produkcyjnych, czy niepraktycznej organizacji pracy wydziałów montujących wyrób gotowy składający się z różnych półproduktów). To pociąga za sobą straty będące sumą niepotrzebnie wykonanych czynności, nadmiaru czynnika ludzkiego w procesie, zajętej przestrzeni magazynowej, czasu realizacji zleceń itd.;
- nieumiejętność trwałego wdrażania pożądanych zmian – to, że większość firm działa nieefektywnie, nie oznacza, że ich kierownictwo jest niekompetentne. Gdy zarząd jest zaangażowany w firmę, zazwyczaj doskonale wie, jakie zmiany są pożądane. Problem jednak tkwi w braku umiejętności ich przeprowadzenia: albo zawodzą metody, albo kierownictwo średniego szczebla nie ma odpowiedniego przygotowania, albo po prostu brakuje czasu, by konsekwentnie przeprowadzić zmianę do końca;
- rosnące ilości reklamacji oraz zbyt duże ilości odpadów generowanych w trakcie produkcji w odniesieniu do potencjału i jakości wykorzystywanych maszyn oraz zatrudnionych ludzi. Wynika to m.in. z rosnącej ilości błędów popełnianych przez pracowników a spowodowanych nieefektywnym wdrażaniem do pracy nowych pracowników (nierzadko obcokrajowców), długiego procesu rozwoju pracowników, co pozwala uzyskać zastępowalność pracowników na różnych stanowiskach produkcyjnych oraz braku modelu kompetencji w wydziałach produkcyjnych. Model taki powinien służyć nie tylko właściwemu rozwojowi umiejętności, ale wpływać na składniki wynagrodzeń (model kompetencji, jako element motywowania i premiowania pracowników);
- niewłaściwa komunikacja w organizacji – w firmach produkcyjnych komunikacja między działami ma silny wpływ na efektywność. Najczęstsze problemy w niewłaściwym harmonogramowaniu produkcji biorą się z zakłóconego przepływ informacji między działami rynkowymi (sprzedaż, obsługa klienta) a produkcją. Poza tym negatywny wpływ mają też: silosowe przetwarzanie danych i planowanie pracy odrębnie w poszczególnych wydziałach produkcyjnych oraz niedostateczne komunikowanie przez zarząd i liderów grup celów firmy. Dodatkowe problemy może stwarzać brak spotkań operacyjnych liderów zespołów lub niewłaściwe ich prowadzenie.
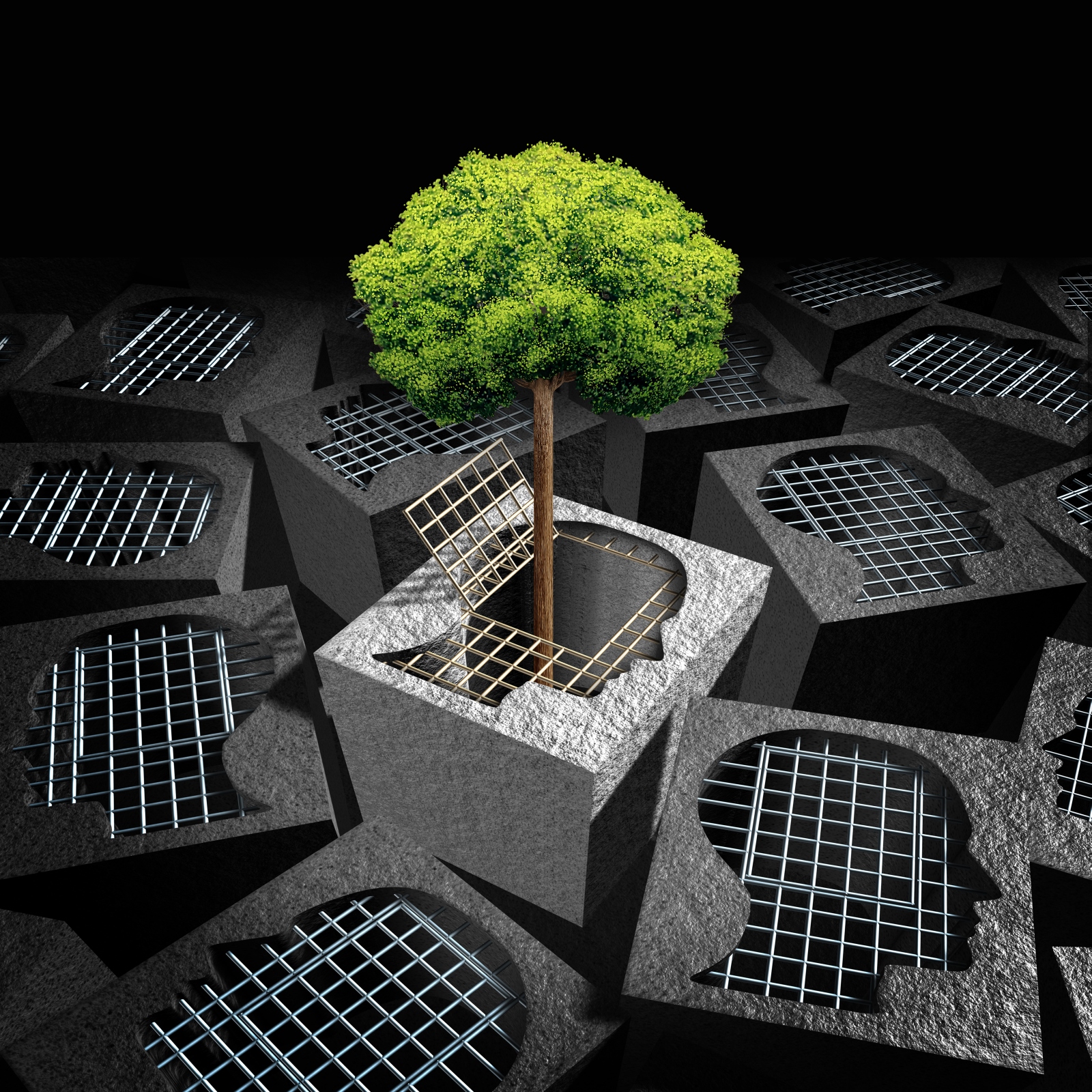
Ścieżki i scenariusze rozwoju
Na wszystkie wyżej wymienione zjawiska największy wpływ ma to, w jaki sposób w danej firmie została zorganizowana praca, w jaką wiedzę zostali wyposażeni ludzie na poszczególnych stanowiskach oraz według jakich metod na co dzień działają pracownicy.
– Z prowadzonych projektów optymalizacji przedsiębiorstw wynika, że przeciętna firma produkcyjna w Polsce w zasięgu ręki ma duże możliwości poprawy wyników w oparciu o te zasoby, które już posiada. Mam na myśli takie rezultaty jak np. 30 proc. wzrost efektywności, kilkuprocentowy wzrost marży, skrócenie o połowę czasu realizacji zamówień czy uwolnienie z magazynu kilkunastu procent zamrożonego w nim kapitału. Tego rodzaju rezultaty wypracowywane są dzięki wdrażaniu konkretnych zmian w metodach i stylu zarządzania, a także zmian postaw pracowników i wdrażania zasad działania w grupach i między zespołami. Co warto podkreślić, tego rodzaju wyniki firmy wypracowują bez większych inwestycji w sprzęt czy nowe technologie – dodaje Izabela Starnawska.
Firmy produkcyjne mają do wyboru co najmniej kilka koncepcji ukierunkowanych na poprawę wyników, wzrost efektywności czy zmianę organizacji pracy. Punktem wyjścia zazwyczaj jest identyfikacja problemu lub wyzwania, która często jest wynikiem analizy przedsiębiorstwa. Zdefiniowany problem pomaga dobrać odpowiednie podejście i metodę jego rozwiązania.
Spośród najczęściej wybieranych metod można wymienić:
- Lean Manufacturing – podejście, które koncentruje się na eliminacji start i marnotrawstwa istniejącego w procesie produkcyjnym poprzez zaangażowanie metod ciągłego doskonalenia, a pozwalających na wdrożenie długoterminowych rozwiązań
- Training Within Industry (TWI) – działania ugruntowujące zarządzanie wiedzą o procesach produkcyjnych, zasadach i regułach pracy w danym przedsiębiorstwie. Po jego wdrożeniu liderzy grup i pracownicy uczą się nawzajem standardów, a organizacja jest zdolna do szybkiego wdrażania pracowników do pracy;
- Total Productive Maintenance (TPM) – działania ukierunkowane na optymalne wykorzystanie parku maszynowego, nie tylko pod kątem czasu pracy i wydajności maszyn, ale też redukcji ich awarii, zwiększenia bezpieczeństwa pracy, zapewnienia długiego okresu eksploatacji.
- Sales & Operations Planning (S&OP) – zapewnienie przepływu informacji od działów rynkowych firmy (sprzedaż, marketing, obsługa klienta) do działów odpowiadających za produkcję i zakupy w celu zapewnienia optymalnego przepływu pracy w obszarze produkcji, redukcji zapasów i kosztu surowców, utrzymania ciągłości dostaw, skrócenia czasu realizacji zamówień oraz poprawy satysfakcji klientów.
- Quick Response Manufacturing – działania reorganizujące sposób pracy wewnętrznych struktur firmy, dzięki którym jest ona w stanie znacznie szybciej realizować zamówienia. Strategia QRM adresowana jest przede wszystkim do firm wytwarzających krótkie serie lub produkujące w długich cyklach, wytwarzających złożone wyroby lub produkty dostosowywane do indywidualnych zamówień;
- Różnego rodzaju inne programy Doskonałości Operacyjnej ukierunkowane na rozwiązanie problemów w obszarze produkcji, zakupów, magazynowania, jakości, sprzedaży czy dystrybucji.
” Punktem wyjścia zazwyczaj jest identyfikacja problemu lub wyzwania, która często jest wynikiem analizy przedsiębiorstwa. Zdefiniowany problem pomaga dobrać odpowiednie podejście i metodę jego rozwiązania. ”
Niezależnie od tego na czym koncentruje się projekt, wspólnym mianownikiem jest jednak praca z ludźmi – i dotyczy to zazwyczaj wszystkich szczebli organizacji, od członków zarządu, po operatorów maszyn czy magazynierów. – Bez uprzedniego wykonania pracy u podstaw z ludźmi żadna nowoczesna technologia czy specjalistyczny system informatyczny nie wpłynie znacząco na poprawę rezultatów przedsiębiorstwa. Firmy powinny sięgać po nowoczesne technologie dopiero po osiągnięciu statusu organizacji zdolnej do samodoskonalenia i umiejącej kształtować pożądane postawy wśród swoich pracowników – mówi Izabela Starnawska.
Chodzi o to, by w oparciu o własny kapitał ludzki mieć zdolność identyfikowania zachowań pracowniczych w firmie, które można ukształtować poprzez wdrożenie firmowych zasad i norm postępowania. Następnie wspólnymi siłami, w zespołach zasady te są utrwalane, by uzyskać lepsze i powtarzalne wyniki. Dzięki temu organizacje zmieniają swoją kulturę działania – uwzględniają szacunek wobec każdego człowieka i lepiej rozumieją potrzeby klientów. Firmy, które podążają tą drogą, stają się coraz bardziej konkurencyjne.
Polski przemysł może być bezkonkurencyjny
Eksperci z 4Results zwracają uwagę, że pomimo niewykorzystanego w pełni potencjału, polskie firmy produkcyjne do czasu wybuchu pandemii radziły sobie bardzo dobrze. Przychody największych firm z sektora produkcyjnego rosły średnio trzykrotnie szybciej niż PKB. Na uwagę zasługuje rekordowy 15 proc. wzrost CIT w 2019 r. (po części wynika on z uszczelnienia systemu podatkowego), jak również najwyższe w historii dodatnie saldo w wymianie towarowej Polski z zagranicą. Co ciekawe, udało się to zrobić pomimo obserwowanych już w minionym roku kłopotów gospodarczych Niemiec, naszego największego zagranicznego odbiorcy. Mimo tego, że w 2019 r. sprzedaż do Niemiec rosła zaledwie w tempie 1,8 , polskie firmy znacznie powiększyły eksport na inne rynki (głównie Czech, Wielkiej Brytanii i USA). To pokazuje, że niezależnie od warunków u największego odbiorcy, rodzimi producenci umieją działać na różnych rynkach zagranicznych.