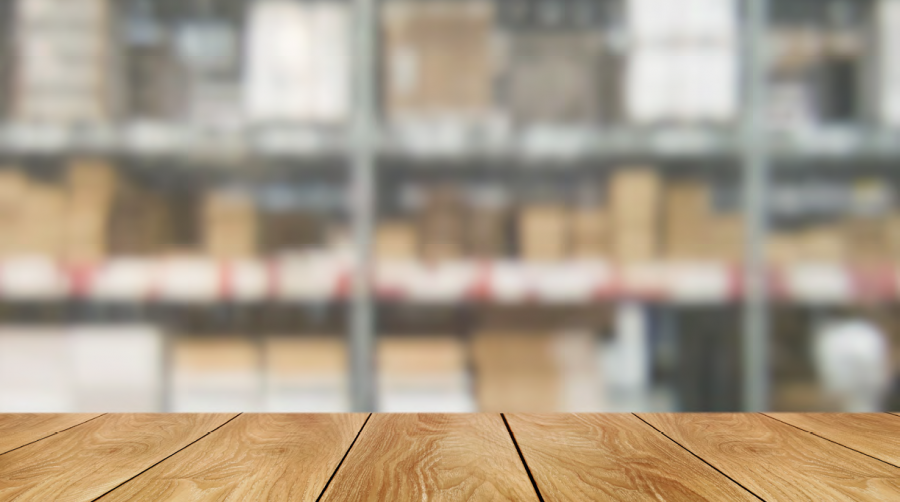
Najlepsza technika składowania
W idealnym świecie magazyny nie byłyby potrzebne – towar harmonijnie przepływałby przez kolejne ogniwa łańcucha dostaw i zawsze znajdowałby się we właściwym miejscu i czasie. Oczywiście, taka wizja logistyki jest dziś dość abstrakcyjna i być może nigdy nie ziści się w praktyce. Nawet koncepcje typu just in time, oparte na zbliżonej idei, przewidują dla magazynów pewną rolę do odegrania – na wielu etapach łańcucha dostaw powstają przecież bufory (produkcyjne, wysyłkowe), które muszą być gdzieś czasowo składowane. Niezależnie więc, w jakim kierunku zwrócą się globalne tendencje w logistyce, pytanie o optymalny sposób składowania towarów zawsze pozostanie zasadne.
Magazynowanie, mimo że nie przynosi wprost dodatkowej wartości dla klienta, jest rzecz jasna źródłem generowania kosztów. Najczęściej są to nakłady ponoszone na utrzymanie budynków i urządzeń do składowania (w tym podatki) oraz wypłaty wynagrodzeń dla pracowników. Dodatkowo należy pamiętać, że nieumiejętne gospodarowanie przestrzenią magazynową, czyli brak stosownego zabezpieczenia dostępności powierzchni na wypadek wzrostu przepływów, może prowadzić do powstania dodatkowych kosztów (np. przez częściowy outsourcing usług składowania).
Optymalizacja kosztów magazynowania sprowadzać się będzie zatem do dwóch podstawowych zadań:
• jak najlepszego wykorzystania powierzchni magazynów,
• umożliwienia wydajnej obsługi procesów związanych ze wstawianiem i wydawaniem jednostek ładunkowych z magazynu.
Między wspomnianymi elementami najczęściej zachodzi korelacja ujemna – położenie większego nacisku na jeden z nich skutkować będzie obniżeniem efektu drugiego. Zjawisko to można zaobserwować w przypadku niemal wszystkich dostępnych obecnie technik składowania, co doskonale obrazuje schemat na Rycinie.
W czym wybierać?
Na Rycinie zaobserwować możemy wyraźny podział na cztery zasadnicze grupy. Jak nietrudno zauważyć, obszar niskiego wykorzystania powierzchni oraz niskiej wydajności obsługi procesów nie jest reprezentowany przez żadną z technik, co świadczy o tym, że skrajnie nieopłacalne sposoby składowania nie występują. Na przeciwnym biegunie znajdziemy odosobniony wyjątek w postaci magazynów automatycznych.
Rycina. Korelacja stopnia wykorzystania powierzchni i wydajności obsługi dla poszczególnych technik składowania
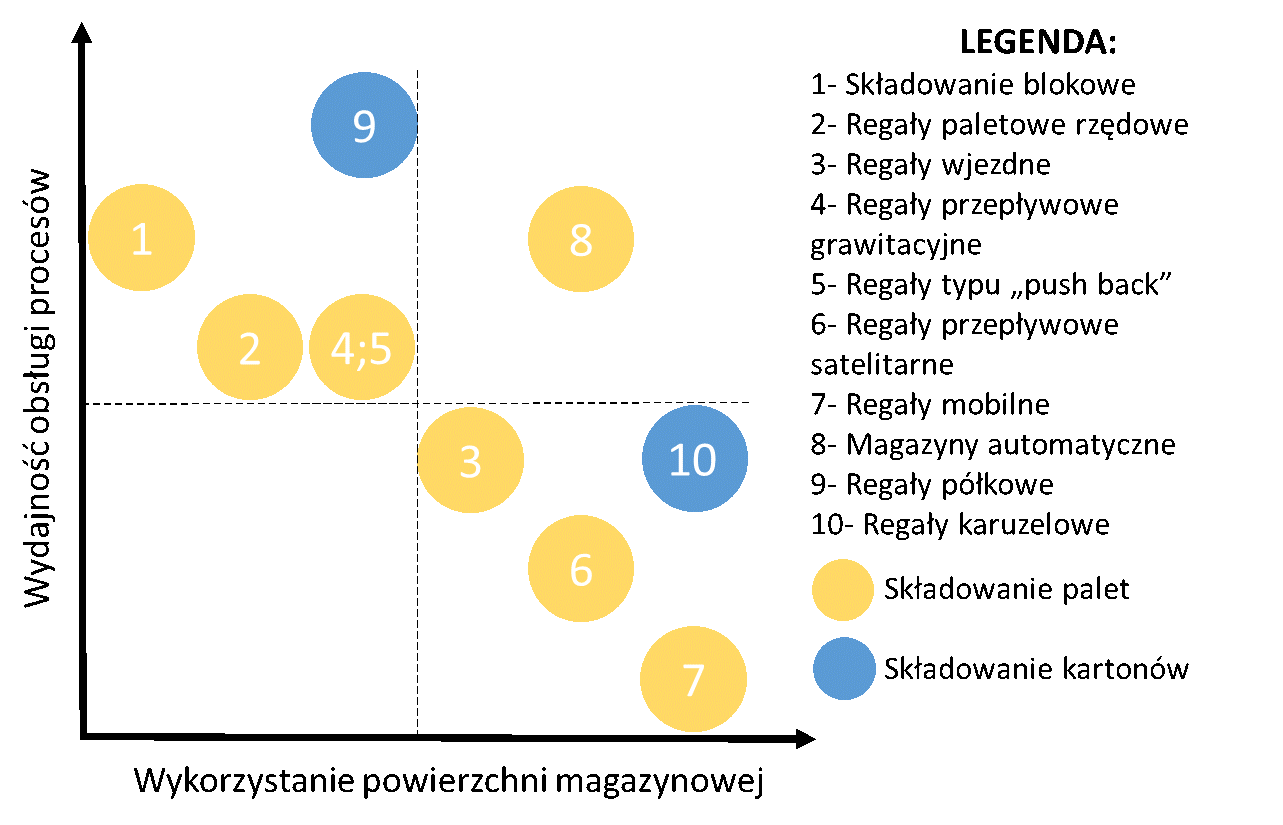
Wysokie wykorzystanie powierzchni oraz wysoka wydajność procesów mogą zostać osiągnięte tylko w wyniku poniesienia nieporównywalnie wyższych kosztów inwestycyjnych, co w wielu przypadkach nie jest uzasadnione ekonomicznie.
Grupa technik o relatywnie niskim wykorzystaniu powierzchni, ale o stosunkowo wysokiej wydajności procesów jest już zdecydowanie szersza:
- Składowanie blokowe – jako jedyna forma zagospodarowania przestrzeni magazynowej nie wykorzystuje regałów. Ograniczenie możliwości składowania wynika tu wprost z przechowywania towaru bezpośrednio na posadzce lub maksymalnie w kilkupaletowych blokach (dla wielu towarów jest to jednak niemożliwe ze względu na ryzyko uszkodzenia). Z tego też względu cała przestrzeń powyżej bloków pozostaje niewykorzystana. Z drugiej strony w układzie tym towar jest łatwo dostępny przy użyciu czołowego wózka widłowego.
- Regały paletowe rzędowe – zdecydowanie najpowszechniejszy sposób aranżacji magazynów, zawdzięczający swoją popularność przede wszystkim dużej uniwersalności tego rozwiązania. Palety zlokalizowane w niezależnych gniazdach gwarantują bezproblemowy dostęp do każdej z nich. Niestety konieczność wyznaczenia licznych dróg transportowych między regałami wpływa na niski sposób wykorzystania przestrzeni.
- Regały przepływowe grawitacyjne – stopnień wykorzystania powierzchni magazynowej ograniczony jest przez konstrukcję regału, która musi zapewnić swobodny przepływ palety przy wykorzystaniu siły grawitacji. Towar wstawiany z jednej strony regału, transportowany jest systemem rolkowym ku jego końcowi, skąd paleta zostanie wydana. Obsługa palet nie przysparza dużej trudności z uwagi na niedużą wysokość regału.
- Regały typu „push back” – również w tym przypadku długość regału jest ograniczona przez sposób transportu palet wewnątrz gniazd regałowych przy użyciu szyn jezdnych (co czyni rozwiązanie bardziej kosztowym w porównaniu z pozostałymi). W przeciwieństwie do regałów przepływowych wstawienie i wydanie palety odbywa się po tej samej stronie. Również tutaj niska wysokość sprzyja sprawnemu wykonywaniu operacji.
- Regały półkowe – ich charakterystyka zbliżona jest do regałów paletowych rzędowych, z tą różnicą, że służą do składowania zdecydowanie mniejszych jednostek ładunkowych (np. kartonów) i nie wymagają użycia wózka widłowego (towar jest zawsze w zasięgu pracownika). Sposób aranżacji przestrzeni w tym przypadku ma na celu przede wszystkim umożliwienie wydajnego procesu kompletacji. Regały półkowe często są wyposażeniem kilkupoziomowych platform – antresoli, co pozwala zwiększyć stopień wykorzystania przestrzeni.
Większość opisanych wyżej technik składowania znajdzie zastosowanie przede wszystkim w stosunku do towarów charakteryzujących się wysokim poziomem rotacji, a także przy szerokim asortymencie utrzymywanych w małych ilościach (za wyjątkiem regałów przepływowych, które wymagają składowania w większej liczbie). Ze względu na liczne i częste operacje magazynowe, kluczowe jest umożliwienie ich wydajnej obsługi.
Wśród technik o wysokim wykorzystaniu powierzchni, ale jednocześnie dość niskiej wydajności procesów możemy natomiast wyróżnić:
- Regały wjezdne (typu „drive in”) – w porównaniu do wcześniej wspomnianych regałów typu „push back” są zdecydowanie głębsze, a transport wewnątrz regału zastąpiony jest możliwością wjazdu wózkiem. Sporym ograniczeniem jest jednak konieczność układania palet kolejno na każdym poziomie, tworząc „kolumny” od środka regału w kierunku jego zewnętrznej strony. W istotny sposób wydłuża to czas czynności manipulacyjnych.
- Regały przepływowe satelitarne (typu „pallet shuttle”) – są pewną modyfikacją regałów przepływowych grawitacyjnych, gdzie funkcję przenośników rolkowych pełnią platformy mobilne – tzw. satelity transportujące palety między jednym a drugim końcem regału. Rozwiązanie to pozwala tworzyć konstrukcje regałowe o długości nawet kilkudziesięciu metrów. Z drugiej jednak strony czas obsługi procesu może się wydłużyć z powodu konieczności przenoszenia satelity pomiędzy gniazdami regałowymi, a czasem (przy niskim wypełnieniu regału) przez oczekiwanie na dojazd satelity.
- Regały mobilne (jezdne, przesuwne) – swoją formą przypominają tradycyjne regały rzędowe, jednak posiadają tylko jeden korytarz roboczy, co pozwala wykorzystać przestrzeń magazynową do maksimum. Wymagany korytarz za każdym razem musi zostać otwarty przy użyciu zdalnego układu sterowania, co zauważalnie wpływa na spadek wydajności procesu.
- Regały karuzelowe – mają postać pionowej zabudowanej konstrukcji, wewnątrz której rzędy półek przemieszczają się w taki sposób, aby wskazana z nich, była dostępna dla operatora na poziomie roboczym. Regały te przeznaczone są wyłącznie do małych ładunków, a do ich obsługi nie jest wymagany wózek widłowy. W tym przypadku wydajność procesu jest ograniczona przez brak możliwości równoczesnej pracy przez więcej niż jedną osobę.
Powyższe przykłady technik składowania pozwalają na maksymalne zagęszczenie składowanych towarów, co jednakże skutkuje ich gorszą dostępnością. Mogą okazać się użyteczne dla towarów wolno rotujących lub w procesach wymagających składowania gotowych jednostek wysyłkowych.
Diabeł tkwi w szczegółach
Dobierając odpowiedni rodzaj wyposażenia do przechowywania towarów w magazynie, trzeba zdawać sobie również sprawę z ograniczeń wynikających z ich charakterystyki.
Szczególną uwagę należy zwrócić na takie czynniki jak: możliwość zachowania kolejności wydań (FIFO), dostępność do każdej składowanej jednostki czy konieczność składowania wielu jednostek w ramach jednego gniazda regałowego.

Wydawanie towarów zgodnie z kolejnością ich przyjmowania, czyli stosowanie zasady FIFO (First In, First Out) w niektórych przedsiębiorstwach może mieć nadrzędne znaczenie, na przykład ze względu na właściwe zarządzanie partiami produkcyjnymi. W branży spożywczej często stosowana jest natomiast zasada FEFO (First Expired, First Out) wymuszająca wydawanie w pierwszej kolejności towarów z najkrótszą datą przydatności do spożycia. Trzeba pamiętać, że w przypadku niektórych technik składowania może być to czynnik wykluczający sensowność ich zastosowania.
Bezpośredni dostęp do każdej składowanej jednostki ma duże znaczenie szczególnie w magazynach przyprodukcyjnych, gdzie istotne jest zlokalizowanie odpowiedniej części pod konkretne zamówienie klienta. Zaleta ta znajdzie także zastosowanie w czasie okresowych inwentaryzacji, do których są zobligowane przedsiębiorstwa.
Składowanie wielu jednostek w jednej lokalizacji (gnieździe lub tunelu regałowym) niesie za sobą ryzyko niewykorzystania pełnego potencjału składowania, gdy liczba palet z konkretnym towarem jest mniejsza niż liczba miejsc w danej lokalizacji. Jeśli jednak równocześnie zachowany jest bezpośredni dostęp do każdej lokalizacji (regały półkowe i karuzelowe), wówczas otwiera się szansa na utworzenie lokalizacji mieszanych, co może okazać się dobrym pomysłem w kontekście zaoszczędzenia dodatkowego miejsca na półkach regałowych.
Werdykt końcowy
Zrozumienie charakterystyki poszczególnych technik składowania oraz ich ograniczeń jest podstawą w wyborze rozwiązania zapewniającego skuteczne wykorzystanie powierzchni magazynu. Powinien to być jednak zaledwie wstęp do szerokiej analityki, uwzględniającej specyfikę oferty asortymentowej (szerokość i głębokość asortymentu), właściwości fizyczne towarów (objętość, kształt), organizację przepływów magazynowych, a także koszty inwestycji. Dopiero szczegółowa analiza wymienionych czynników pozwoli precyzyjnie odpowiedzieć na pytanie: Jak wybrać najlepszą technikę składowania, aby skutecznie wykorzystać naszą powierzchnię magazynu? Należy bowiem mieć świadomość, że w praktyce nie istnieją w pełni uniwersalne rozwiązania, które można przyjąć za wzorcowe i zastosować w każdych warunkach.
Asortyment o dużej szerokości (liczbie linii produktów) oraz głębokości (liczbie wariantów w ramach każdej linii) na ogół wiąże się z dużą liczbą zróżnicowanych zamówień od klientów. W takim przypadku preferowane będą regały z dostępem do każdej jednostki składowania, umożliwiające szybką kompletację. W sytuacji odwrotnej, kiedy wydawane będą zazwyczaj te same produkty (często całe palety), dobrym pomysłem mogą okazać się regały do składowania wielu jednostek w jednej lokalizacji, pozwalające zaoszczędzić przestrzeń.
Właściwości fizyczne towarów często determinują zastosowanie zróżnicowanych jednostek składowania, co wpływa na dobór technologii magazynowej. Bardzo małe elementy mogą być przechowywane w pojemnikach, dla których odpowiednie będą regały półkowe. Duży gabaryt produktów ogranicza natomiast liczbę sztuk na jednostkę składowania, co pozwala skłonić się ku rozwiązaniom pozwalającym efektywnie składować dużą ich liczbę. Dla towarów o specyficznym kształcie, gdzie nie jest możliwe zastosowanie tradycyjnych technik, wykorzystywane są regały specjalistyczne do składowania luzem (np. regały wspornikowe dla dłużyc).
Organizacja przepływów magazynowych, a więc wielkość i rozlokowanie poszczególnych stref magazynowych, może być pewnym ograniczeniem przy adaptacji rozwiązań w istniejącym już magazynie. Bufory rozładunkowe oraz wysyłkowe, a także specjalne wymagania procesowe (np. stanowisko VAS, strefa sortowania) zmniejszają możliwości odpowiedniej konfiguracji technologii składowania w magazynie. Ryzyko to jest mniejsze przy projektowaniu nowego magazynu.
Jak przy każdej decyzji biznesowej ostateczny wpływ na wybór koncepcji składowania może mieć wysokość nakładów finansowych. Nie zawsze duże inwestycje w bardziej zaawansowane technologie będą uzasadnione z punktu widzenia skali działalności. W niektórych sytuacjach nawet najprostsze rozwiązania mogą okazać się optymalne dla określonego typu asortymentu. Podobnie w drugą stronę, nie zawsze warto iść utartym schematem i wybierać tylko powszechne metody. Być może w wyniku dogłębnej analizy, po rozważeniu wszystkich ograniczeń, uda się stworzyć unikalny w skali naszej branży i co najważniejsze praktyczny układ składowania.
Artykuł ukazał się w czasopiśmie Eurologistics nr 4/2021