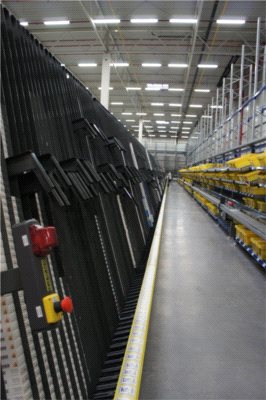
Nauka z Neuca
Na początku roku otwarto magazyn Neuca w Ołtarzewie pod Warszawą, który jest krokiem milowy w realizacji procesu centralizacji logistyki w całej Grupie Neuca. W ten sposób holding chce utrzymać pozycję lidera na rynku dystrybucji farmaceutyków w Polsce.Do końca 2009r. Neuca,...
Do końca 2009r. Neuca, wówczas jeszcze pod nazwą Torfarm, przeprowadzała swoje operacje logistyczne w 35 magazynach rozsianych na terenie całego kraju, których łączna powierzchnia wynosiła 76,4 tys. m², zatrudniając w nich 2770 osób. Aktywne wdrażanie nowej strategii pozwoli po roku zmniejszyć ilość magazynów do 28 (67,7 tys. m²) i zredukować personel do 2360 osób. Docelowo, od 2013 r., działać ma 12 magazynów, w tym trzy w pełni zautomatyzowane magazyny centralne, realizujące tzw. pierwszą dostawę, i 9 lokalnych, realizujących drugą i trzecią dostawę. Ich łączna powierzchnia wynosić ma 63,7 tys. m² , a obsługiwać ma je 1410 osób.
Nowa strategia ma pozwolić w pełni wykorzystać efekt skali i przynieść widoczne oszczędności w wysokości 27,5 mln zł rocznie. Obecnie koszty logistyki magazynowej wynoszą 2,14 procent całości przychodów. Współczynnik ten ma ulec redukcji do 1,61 procent. Wszystko to dzięki większej wydajności pracy, ograniczeniu zatrudnienia, mniejszej ilości magazynów i zmiany systemu pracy w magazynach lokalnych na jednozmianowy. Analogicznie planowane jest zmniejszenie kosztów transportu z 1,4 procent do 1,17 procent. Centralizacja punktów składu pozwoli bowiem wyeliminować istniejące w tej chwili zjawisko dublowania się tras. Do tego wszystkiego rotacja zapasów skróci się o sześć dni, a to oznacza odmrożenie kapitału w wysokości 100 mln zł.
Automatyka w magazynie
Najważniejszym elementem realizacji nowej strategii jest magazyn w Ołtarzewie. Jest to drugi po Katowicach magazyn centralny. Wkrótce w Gądkach pod Poznaniem nastąpi otwarcie trzeciego.
Magazyn w Ołtarzewie został uszyty specjalnie na miarę potrzeb Grupy Neuca (w systemie BTS – build to suit) i należy do najbardziej nowoczesnych centrów logistycznych w branży, obsługując apteki z 40 procent terytorium Polski. Kompletacja prowadzona jest na powierzchni 5 tys. m², skąd 150 osób jest w stanie wydać w ciągu doby do 300 tys. produktów. Dla porównania, w tradycyjnym magazynie do zapewnienia takiej skali operacji potrzebne byłoby 11 tys. m² i zatrudnienie ponad 800 osób.
Taką wydajność zapewnia szereg wdrożonych i zaawansowanych technologicznie rozwiązań. W wąskich korytarzach suną cicho wózki indukcyjne, poruszające się tylko w linii prostej, po wykutej w tym celu w podłodze prowadnicy. Pracownik decyduje tylko o tym, czy jechać do przodu, czy do tyłu. I o tym, w którą stronę skierować widły: prawo czy lewo? Pozwala to jednocześnie lepiej wykorzystać powierzchnię magazynu, poprzez ustawienie regałów bliżej siebie, i zminimalizować ryzyko wypadku.
Nieco dalej automat do wydawania szybko rotujących towarów sam kompletuje wysyłki. Ze specjalnych slotów, uzupełnianych przez 25 pracowników, spadają na taśmę zamówione produkty, które następnie lądują w pojemniku – nośniku. Nośnik, ciągle bez ingerencji człowieka, rusza dalej w swoją stronę. Wydajność automatu to 20 000 pozycji na godzinę. Taką pracę gdzie indziej wykonuje do 110 osób. Średni czas realizacji zamówienia przez ten automat to 5 minut. W tradycyjnym magazynie to operacja zajmuje 20-40 minut.
Jest tu też pierwsza w branży dystrybucji farmaceutyków w Polsce mikroukładnica (OSR) wykorzystywana do kompletacji towarów rzadko rotujących. W tym przypadku dwie osoby obsługujące OSR, to odpowiednik 40 osób pracujących w starym systemie. Jej mechanizm jest skomplikowany, ale ogólna zasada działania prosta: to nie człowiek idzie po towar, ale towar przyjeżdża do człowieka. Pracownik stoi tylko na swoim stanowisku i czeka na to, aż pojemnik z danym artykułem podjedzie do niego. Następnie wyjmuje wyświetloną na ekranie ilość sztuk, przekłada do kompletowanej przez siebie przesyłki, i zapomina o wszystkim. Pojemnik sam wraca na swoje miejsce. Na inną taśmę pracownik przekłada nośnik z przesyłką, jeśli ta już jest gotowa.
Taśmy te oplatają cały magazyn. Nośniki jeżdżą po nich bezustannie, przywodząc na myśl jakiś zminimalizowany i zdehumanizowany roller coaster, z tym że zamiast szczerbatych dziesięciolatków w wagonikach znajdują się leki na ból głowy i maści na żylaki. Jeśli potrzeba, jadą one do strefy kompletacji artykułów, których gabaryty, kształt lub rodzaj opakowania nie pozwalają na umieszczenie ich w slotach; które przechowywane są w chłodniach (do 15⁰C) lub lodówkach (do 8⁰C). Gdy kompletacja przesyłki zostanie zakończona, nośnik wędruje na miejsce kontroli, gdzie pod czujnym okiem kamer pracownicy sprawdzają czy wszystko się zgadza. Robiąc to skanują kod kreskowy pojemnika, co zostaje odnotowane w systemie. Przyda się to, jeśli będzie później potrzeba rozpatrzenia reklamacji. Data i godzina pozwalają na precyzyjne wyselekcjonowanie odpowiedniego nagrania z archiwum. Po przejściu kontroli nośniki wracają na taśmę, przejeżdżają przez maszynę, która je zamyka, binduje, etykietuje i trafiają na jedną z 48 ramp, z których każda odpowiada linii dystrybucji. Kierowca skanuje czekające na niego nośniki i jeśli system zatwierdzi ich ilość, ładuje do samochodu. A list przewozowy drukowany jest z automatu.
Koszt inwestycji magazynu w Ołtarzewie wyniósł 27 mln zł. Planowane oszczędności dzięki tej inwestycji mają wynieść 9 mln zł. Oszczędności te uwzględniają także koszty funkcjonowania w zdublowanych lokalizacjach (do momentu zamknięcia starych magazynów) oraz redukcji personelu.