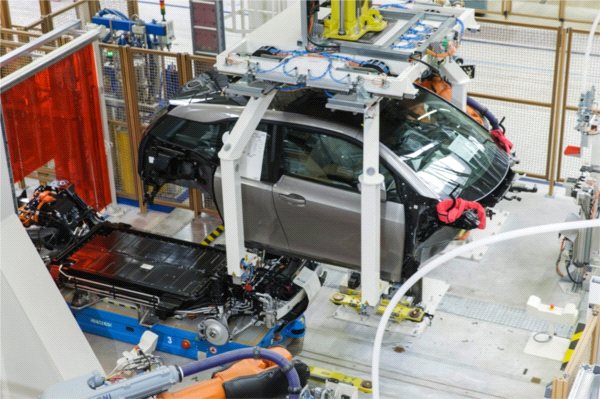
Nietuzinkowa fabryka
Umiejscowiona na przedmieściach Lipska, na pierwszy rzut oka bardzo niepozorna, a w środku… prawdziwe centrum dowodzenia. To właśnie z tej fabryki wyjeżdżają najbardziej zaawansowane modele bawarskiego producenta - elektryczne BMW i3 oraz i8.Dziennie z lipskiej fabryki wyjeżdża...
Dziennie z lipskiej fabryki wyjeżdża 750 pojazdów, w tym 120 pojazdów elektrycznych. Sam parking przygotowany jest na 4000 miejsc parkingowych. Zatrudnienie „kolosa BMW” wynosi 4700 osób, a powierzchnia, jaką zajmuje, to 227 hektarów i skumulowana jest w 8 halach produkcyjnych. Oprócz elektrycznych pojazdów w Lipsku produkowane są: 5-drzwiowa seria 1, kabriolet, coupe oraz seria 2 Active Tourer.
Roczna produkcja wynosi około 320 tys. aut, w tym aż 44 tys. pojazdów elektrycznych. Uruchomienie nowoczesnej linii produkcyjnej umożliwiającej budowę elektrycznych pojazdów kosztowało koncern BMW blisko 400 mln euro. Efekt? Zdumiewający. Do produkcji tych samochodów wykorzystywane są najnowocześniejsze technologie, a praca człowieka została ograniczona do minimum. We wrześniu 2013 r. rozpoczęła się produkcja modelu i3, a w maju 2014 r. dołączył model i8.
Proces powstawania elektrycznych pojazdów
Pierwszy etap produkcji elektrycznych modeli BMW rozpoczyna się na terenie USA, a konkretnie w fabryce Moses Lake w stanie Washington. To właśnie tam produkuje się włókno węglowe, kluczowy element karoserii elektrycznych „beemek”. Do produkcji włókien węglowych wymagana jest wysoka temperatura sięgająca nawet 1300OC, co oznacza, że proces produkcji wymaga dużej ilości energii. Fabryka Moses Lake wykorzystuje do tego w 100 procentach energię odnawialną. Włókna węglowe zostają ułożone obok siebie, a następnie w celu stabilizacji przeplatane są włóknem szklanym. Efektem tego zabiegu jest powstanie elementu o grubości 3 mm, który następnie zostaje odpowiednio docięty i wysłany do Niemiec, gdzie przechodzi proces tłoczenia, podgrzewania i przetworzenia na karbonowe laminaty. Po dotarciu do fabryki docelowej laminat zostaje poddany procesowi wtryskiwania żywicy, który ma za zadanie go utwardzić. Co ciekawe, około 10 proc. włókien węglowych wykorzystywanych do produkcji elektrycznych modeli BMW to materiał pochodzący z recyklingu.
Produkowane modele i3 oraz i8 składają się z dwóch elementów. Pierwszym elementem jest moduł Drive obejmujący kompletny układ napędowy oraz technologie zawieszenia. Produkcja modułu Drive odbywa się w zakładzie w Dingolfing. 50 proc. aluminium wykorzystanego do produkcji modułu Drive pochodzi z odzysku. Drugim elementem jest moduł Life obejmujący przedział pasażerski, który wykonuje się przy użyciu tworzywa sztucznego z dodatkowymi wzmocnieniami z włókna węglowego (CFRP). Dzięki wykorzystaniu tych technologii, proces produkcyjny zostaje skrócony o połowę i trwa około 20 godzin. Na uwagę zasługuje również niski poziom hałasu panujący w hali produkcyjnej oraz brak typowych dla fabryk samochodów iskier , jakie powstają podczas spawania elementów karoserii. Poszczególne elementy pojazdu łączone są ze sobą za pomocą procesu klejenia. Inżynierowie BMW opracowali odpowiedni proces termiczny – miejsce, w którym nakładany jest klej, zostaje podgrzane, dzięki czemu skracany jest czas oczekiwania na uzyskanie pełnego wiązania. Moduł Life składa się z około 150 części – jest to ponad 30 proc. mniej niż w przypadku konstrukcji stalowej.
Nacisk na ekologię
Dzięki przemyślanej budowie hal fabrycznych (liczne świetliki dachowe) fabryka wykorzystuje jak najwięcej naturalnego światła, a system klimatyzacji wykorzystuje naturalny przepływ powietrza. Fabryka w Lipsku to prawdziwe centrum innowacji i technologii. Nie znajdziemy tutaj również klasycznej lakierni samochodowej, ponieważ do lakierowania powierzchni pojazdów wykorzystywana jest metoda odseparowania warstw lakieru na sucho. Efektem tego jest eliminacja odpadów w postaci resztek lakieru, a dodatkowo zużycie energii jest o 25 proc. mniejsze niż w przypadku tradycyjnej lakierni. Fabryka w Lipsku zasilana jest czterema turbinami wiatrowymi, które znajdują się na jej terenie. W halach produkcyjnych temperatura powietrza waha się w granicach 23-25oC, ponieważ w takiej temperaturze klej zachowuje najlepszą elastyczność.