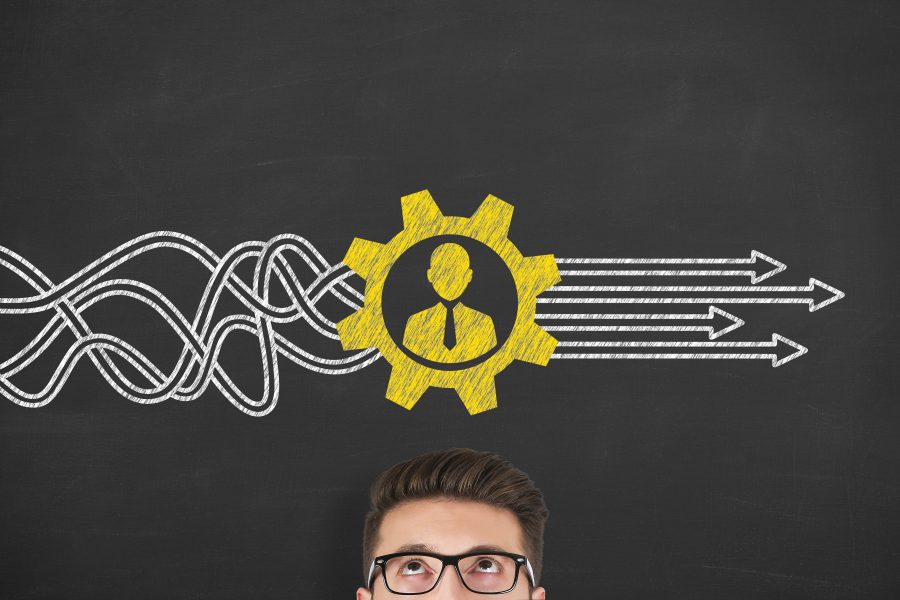
Od armii wolności do zrozumienia procesu
Training Within Industry – to zbiór zasad według których powinno się doskonalić kadry – od majstrów, przez brygadzistów po średni management tak, by oni mogli szkolić swoich pracowników. Zasady tak uniwersalne, że po 80 latach nie tylko się nie zestarzały – są coraz bardziej aktualne.
Historia TWI zaczyna się w samym środku II Wojny Światowej. Amerykańskie fabryki produkują nie tylko na potrzeby USA, ale i zaspokajają niezaspokojone potrzeby sprzętowe armii brytyjskiej i radzieckiej w ramach programu Lend-Lease. I wtedy, w październiku 1941 roku, 2 miesiące przed przystąpieniem USA do wojny, amerykański Komisarz do spraw Zatrudnienia Sidney Hillman wypowiada słowa, które staną się na kolejne lata mottem amerykańskiego przemysłu: „Tak jak kochamy wolność, nie możemy dopuścić do upadku największej armii wolności. Musimy produkować dwa samoloty na każdy jeden Hitlera, dwa czołgi na jego jeden, dwa statki na jego jeden, dwie bronie na jego jedną”.
TWI a Lean
Hillman stworzył podstawy programu TWI. Programu, którego filarami są świadomość środków produkcji, współodpowiedzialność za produkcję i jej wynik, wzajemny szacunek pracowników i przełożonych, dbałość o wartość dodaną. Na efekty nie trzeba było długo czekać. Z 600 firm produkcyjnych, które brały udział w programie TWI podczas II wojny światowej: wszystkie uczestniczące firmy skróciły czas szkolenia nowych pracowników o 25 proc. lub więcej,
• 86 proc. firm zwiększyło wydajność o 25 proc. lub więcej,
• 88 proc. firm zredukowało pracochłonność na produkt o 25 proc. lub więcej,
• 55 proc. firm zredukowało braki o ponad 25 proc.,
• 100 proc. firm zredukowało reklamacje o ponad 25 proc.
Tu można oczywiście postawić pytanie, co TWI ma wspólnego z Lean Manufacturing? To właśnie ten system stał się jednym z wzorów, na którym Taiichi Ono oparł swój Toyota Production System, z którego później wyłonił się Lean Manufacturing. Dziś TWI jest integralną częścią TPS.
W 2008 roku na TWI Summit Jim Huntzinger powiedział: Twoja firma nie stanie się lean, jeżeli wdrożysz w niej tylko TWI. Ale bez TWI nigdy nie stanie się lean.
Co zatem oznacza TWI? Program uczy czterech umiejętności:
• instruowania pracowników,
• doskonalenia metod pracy,
• zapewnienia bezpieczeństwa pracy,
• rozwijania umiejętności przywództwa.
Dzięki TWI brygadziści, mistrzowie, a nawet doświadczeni operatorzy uczą się, jak szybko wyszkolić pracownika, w świadomym wykonywaniu pracy. To wiąże się nie tylko z odpowiednim przygotowaniem szkoleniowym. Każdy ze szkoleniowców musi również umieć wykonać pracę, której uczy tak, by móc udzielać wskazówek, a jednocześnie wyjaśnić, dlaczego te wskazówki są ważne. Kolejny krok TWI to umożliwienie szkolonemu wykonywania pracy już w czasie szkolenia. Czwarty – to monitorowanie postępów pracy.
„Każdy ze szkoleniowców musi umieć wykonać pracę, której uczy tak, by móc udzielać wskazówek, a jednocześnie wyjaśnić, dlaczego te wskazówki są ważne.”
Karty TWI
Istotnym elementem TWI jest przygotowanie kart TWI – to podstawowy element prawidłowego przygotowania do szkolenia. Karta TWI zawiera opis czynności, ich kolejność, oraz wyjaśnienie przyczyn, dla których kolejne czynności są ważne w procesie produkcyjnym. To klucz do sukcesu. Pracownik świadomy wagi wykonywanych czynności rozumie cały proces, przy którym pracuje.
System kart TWI eliminuje typowe błędy, jakie mogą się pojawić, kiedy firma korzysta z zewnętrznych szkoleniowców. Ci zwykle pokazują jak wykonać określony proces, ale nie dają dodatkowych wskazówek i nie wyjaśniają, czemu określona czynność jest ważna dla całego procesu. W systemie TWI podanie przyczyny wykonywania kolejnych czynności jest równie ważne jak samo szkolenie. Bez przejścia tego etapu, etapu świadomie wykonywanej pracy, nie da się przejść do kolejnych etapów. Dlaczego? Bo pracownik nie znając powodów, dla których musi wykonać określone czynności, nie zrozumie zasad pracy.
To zresztą największy grzech w firmach: pracownik nie zna powodów, nie zna zasad, ale za to ma świadomość, że nikt go nie kontroluje. Co prawda ma stanowiskową instrukcję pracy – ale te zwykle są zawiłe i trudne do zrozumienia. Poza tym, żadna nie wyjaśnia, dlaczego określone czynności są ważne dla całego procesu.
Trzy fundamenty doskonalenia
Kolejnym krokiem TWI po szkoleniu ze zrozumieniem, jest doskonalenie. Doskonalenie to nic innego, jak sztuka większej, szybszej i lepszej jakościowo produkcji przy tych samych zasobach. Doskonalenie opiera się na trzech fundamentach: dzieleniu pracy na poszczególne czynności, analizie tych czynności w aktualnej metodzie pracy i wyciąganiu wniosków – co można zmienić, w jaki sposób udoskonalić poszczególne czynności, żeby wykonać prac szybciej, lepiej, bardziej efektywnie.
Ta ostatnia analiza powinna odpowiedzieć na cztery pytania:
1. Co powinienem robić inaczej? (może kolejność czynności należy zmienić, by usprawnić pracę)
2. Które czynności wykonuję niepotrzebnie? (np. chodzę po materiał, przez co tracę czas)
3. Czy potrafię znaleźć inne wzorce? (benchmark – przykręcam śruby kluczem, a inni używają do tego mimośrodu i oszczędzają czas)
4. Jak mogę rozbudować czynność, by była bardziej efektywna? (np. automatyczne wkręcanie śruby może być połączone z polerowaniem elementu)
Odpowiedzi na te pytania i wdrożenie tych odpowiedzi w życie dadzą efekt doskonalenia: więcej, szybciej i lepiej.
Ważnym elementem TWI jest bezpieczeństwo pracy. Nie można dobrze zarządzać obszarem pracy, jeżeli nie jest bezpieczny. A zarządzać znaczy nie tylko nadzorować, ale wykształcić w szkolonym pracowniku umiejętność kreowania bezpiecznego środowiska pracy. Można to zrobić w kolejnych czterech krokach. Po pierwsze – nauczyć pracownika określania miejsc potencjalnie niebezpiecznych (np.: przenoszenie blachy obudowy zmywarki może grozić przecięciem skóry dłoni). Po drugie – wybór środków zaradczych, eliminujących zagrożenie (np.: użycie rękawic ochronnych). Po trzecie – wprowadzenie tych środków w życie. I wreszcie po czwarte – kontrola rezultatów eliminacji zagrożenia. Cały system opiera się na identyfikacji zagrożeń i ich eliminacji. To brygadziści i mistrzowie pytają operatorów, gdzie dostrzegają zagrożenia.
Przywództwo w czterech krokach
Ostatnim, ale równie ważnym jak wszystkie pozostałe, filarem TWI jest nauka odpowiedzialnego przywództwa, postrzeganego jako sposób efektywnego zarządzania problemami w organizacji i ich rozwiązywania. I tu znów jak w całym czteroelementowym TWI – przywództwo rozpatrywane jest w czterech krokach.
„Kiedy przełożeni rozwiązują problemy razem z pracownikami, rodzi się ta szczególna więź menedżer – pracownik.”
Pierwszy to umiejętność zdobywania wiedzy o faktach. W swojej praktyce trafiłem na problem spadku wydajności w procesie wędzenia ryb. Spadała ogólna waga pozyskiwanego produktu. Żeby odpowiedzieć na pytanie dlaczego, trzeba było zadać kolejne pytania. Czy warunki wędzenia są zawsze takie same? Czy ryby nie spadają z wózków w transporcie? Czy waży się ryby mrożone, czy świeże? Czy ryby do wędzarni trafiają mokre, czy suche? Szukam faktów – a to oznacza, że szukam przyczyn. Jeżeli znajdę element, który różni poszczególne procesy – oceniam jego faktyczny wpływ na wydajność.
Drugi krok to próba wypracowania standardu. Tu znów pojawia się karta TWI – opis prawidłowego procesu i przyczyn wykonywania poszczególnych czynności. To tu pojawi się rozwiązanie.
Trzeci krok to wprowadzenie rozwiązania w życie. Czwarty – kontrola, czyli sprawdzanie wyniku.
Aplikacja zamiast tablicy
System TWI zakłada, że to pracownicy mają świadomość najlepszych rozwiązań i najlepszych metod pracy. Trzeba im tylko zapewnić forum wymiany pomysłów. Stąd kolejny element TWI – tablice odpraw. To tu monitoruje się wydajność, przedstawia efekty, tu jest miejsce na sygnalizowanie rozbieżności, które definiują problem. Te rozbieżności są właśnie zgłaszane przez pracowników.
Tablica może być tylko elementem umownym. Można tu zastosować rozwiązania znane z social media – prosta aplikacja na telefon pozwoli pracownikom sygnalizować, czy zetknęli się z problemem (na zasadzie lajków) a potem opowiadać się za proponowanymi rozwiązaniami. To właśnie pracownicy, najbardziej zaangażowani w procesy produkcyjne, potrafią wygenerować najlepsze rozwiązania.
I jeszcze jedno: kiedy przełożeni rozwiązują problemy razem z pracownikami – rodzi się ta szczególna więź menedżer – pracownik. Przełożony pytający pracownika o opinię, czy możliwe rozwiązanie sprawia, że pracownik czuje się doceniony i ważny. To przekłada się zwykle na wyniki pracy. Jednocześnie daje świadomość, że jeżeli sam uczestniczę w rozwiązaniu problemu – sam kreuję rozwój firmy. Umiejętność wprowadzenia pracowników na ten poziom odpowiedzialności za produkcję i firmę, to właśnie przywództwo w rozumieniu TWI.
Oczywiście spotkamy się z opiniami, że TWI to system dla firm produkcyjnych. Ale w rzeczywistości można go stosować w każdej dziedzinie: usługach,służbie zdrowia, biurach, a nawet w mediach. Każdy z filarów TWI może być, oczywiście po przemyśleniu i dopasowaniu, wykorzystany w dowolnym sektorze. TWI to standaryzacja pracy, standaryzacja szkolenia, określenie reguł przywództwa. I w każdym sektorze przyniesie podobne rezultaty.
TWI to też idealne rozwiązanie w obecnej sytuacji niestabilnego rynku pracy, z dużym przepływem pracowników. Nie tylko z powodu systemu szkolenia, który zakłada wdrożenie pracownika już podczas nauki. To właśnie ta nauka, która zakłada uzmysłowienie pracownikowi, że jest tak samo odpowiedzialny za sukces zakładu, jak jego przełożeni sprawia, że TWI może prowadzić do utrzymania pracownika. Zwłaszcza, kiedy zobaczy, że jego propozycje i usprawnienia są wprowadzane w życie.
W wojennych czasach w USA system TWI sprawdził się idealnie. Przeszkolone w trakcie produkcji kobiety potrafiły pracować wydajnie i efektywnie. Jednocześnie same pracownice tamtych lat przyznają, że pierwszy raz w historii pracownik miał tak dużo do powiedzenia w kwestii usprawnienia produkcji. I tyle dumy z wykonywanej pracy.
O autorze
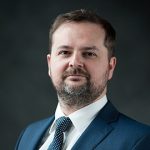
Sp. z o.o.
Ukończone studia MBA, Certyfikat Six Sigma Black Belt oraz ekonomiczne wykształcenie w połączeniu z wieloletnim doświadczeniem powoduje, że doskonale rozumie specyfikę pracy klienta, to czym jest wartość dla klienta oraz obserwuje fakty i dostrzega marnotrawstwa. Jest zafascynowany teorią Lean management, a w szczególności zwiększaniem efektywności procesów i ludzi, co wykorzystuje zarówno w życiu prywatnym jak i w pracy dla biznesu. Swoje doświadczenie zawodowe zdobywał realizując projekty w obszarze Lean management dla największych firm w kraju. Ma za sobą ponad 2000 dni spędzonych na projektach zarówno w obszarze Lean management jak i w obszarze szeroko pojętego zarządzania i strategii.