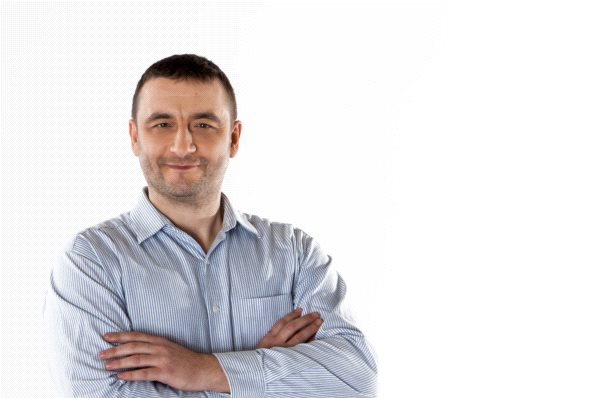
Odnaleźć się w zdigitalizowanym świecie
O wyzwaniach, jakie dla firm produkcyjnych oraz ich menedżerów niesie cyfrowa rewolucja, rozmawiamy z dr Jackiem Kozłowskim.Hasła związane z ideą Przemysłu 4.0 słychać już praktycznie zewsząd. W jakich obszarach dziś tak naprawdę widać już tę koncepcję w praktyce?
O...
Hasła związane z ideą Przemysłu 4.0 słychać już praktycznie zewsząd. W jakich obszarach dziś tak naprawdę widać już tę koncepcję w praktyce?
O Przemyśle 4.0. mówi się coraz więcej i to bardzo dobrze. Doradzając firmom i analizując ich procesy wytwórcze, logistyczne czy biurowe, doskonale widzimy jak duże rezerwy tkwią w polskich zakładach produkcyjnych. Zmiany są potrzebne, a idea w pełni zautomatyzowanej fabryki działa na wyobraźnię decydentów na tyle, że coraz uważniej przypatrują się oni swoim procesom, szukając sposobów na to, by je usprawnić. To czy zoptymalizują produkcję wdrażając rozwiązania Przemysłu 4.0., czy też zdecydują się wprowadzić inne rozwiązania, to kwestia drugorzędna. Ważne, że przemysł dostrzega potrzebę zmian.
Patrząc na rynek, można podzielić zakłady produkcyjne na te, które dopiero zaczynają realizować duże projekty IT i na te, które na przestrzeni ostatnich lat wydały znaczące środki na modernizację parku maszynowego, wdrożyły oprogramowanie ERP, MES czy SFC, i które dzięki temu dzisiaj realizują produkcję w znacznym stopniu zautomatyzowaną. Wykorzystują one czytniki RFID, ekrany dotykowe, wirtualną rzeczywistość, ale przede wszystkim w coraz większym stopniu opierają się na danych wykorzystywanych do prognozowania popytu, ograniczenia wypełnienia magazynów, zapobiegania przestojom czy awariom. Nie jest to jeszcze spełnienie idei Przemysłu 4.0., gdzie fabryka jest w pełni zautomatyzowana i w zasadzie autonomiczna, niemniej w wybranych obszarach, niektóre firmy należy ocenić wysoko pod względem zaawansowania prac. Potrafią one nie tylko realizować opłacalną produkcję w krótkich seriach, ale także dostarczać produkt na tyle konkurencyjny i wysokiej jakości, że z powodzeniem sprzedają go na wymagających, zachodnich rynkach. Nie bez powodu dzisiaj marka „Made in Poland” zyskuje na wartości i staje się synonimem wartościowego a nie tylko najtańszego produktu.
Doświadczenia pokazują jednak, że wbrew pozorom, do zrobienia jest jeszcze wiele. Nie zawsze sięgamy po bardzo zaawansowane rozwiązania i technologie IT a mimo to udaje nam się zwiększyć efektywność produkcji o kilkadziesiąt procent. Na przestrzeni ostatnich lat zrealizowaliśmy projekty, gdzie produkcję w toku ograniczyliśmy o 65 42 proc. a problemy jakościowe zmniejszyliśmy o 95 42 proc.. To pokazuje skalę tego, co jest jeszcze do zrobienia w obszarze produkcji w Polsce.
Biorąc pod uwagę potencjał, specyfikę polskiego rynku, branże i poziom zaawansowania rodzimych firm – w jakich obszarach najłatwiej będzie im realizować projekty z pogranicza Przemysłu 4.0?
We wszystkich obszarach istnieje spore pole do optymalizacji, ale po pierwsze nie zawsze musi to oznaczać wdrażanie rozwiązań Przemysłu 4.0, a po drugie raczej nie należy się spodziewać masowych inwestycji w Fabryki 4.0. Tu zdecydowanie zalecam metodę małych kroków, zwłaszcza, że nawet patrząc globalnie, zdecydowana większość zakładów produkcyjnych znajduje się dopiero na początkowym etapie inwestycji. Tzw. „digital masters” jest zaledwie kilka procent. W tej sytuacji trudno o punkt odniesienia.
To, w którym obszarze będą realizowane projekty Przemysłu 4.0. zależy w zasadzie od trzech czynników: budżetów, świadomości menedżerów, a także rzeczywistych potrzeb. Ten pierwszy czynnik nie jest już barierą – wiele zakładów okrzepło na tyle, że są one w stanie sfinansować inwestycje z własnych środków, nie sięgając po zewnętrzne wsparcie. To czego potrzeba, to decyzja i świadomość potrzeb. Z naszych doświadczeń wynika, że menedżerowie często je dostrzegają, ale boją się postawić ten pierwszy krok, zakładając, że nie są jeszcze na niego gotowi operacyjnie czy merytorycznie. Warto też zauważyć, że o ile każda fabryka chce produkować więcej, niższym kosztem, o tyle nie każda musi realizować produkcję na zamówienie, nie każda musi od razu drastycznie skracać czas produkcji i ograniczać jej koszty. To wpływa na tempo zmian. Z dużą dozą prawdopodobieństwa można jednak założyć, że pierwsze skrzypce w cyfrowej rewolucji będą odgrywały te firmy, które do tej pory pod względem inwestycji w nowe technologie wiodą prym, a więc np. motoryzacyjne czy silnie regulowane branże jak farmaceutyczna, które musi spełnić wyśrubowane wymagania.
Co w kontekście idei Przemysłu 4.0 warto zrobić? Jak przygotować się do jej wdrożenia?
Uwzględniając fakt, że idea Smart Factory, przenosi ciężar planowania, realizacji (w tym sterowania) i kontroli produkcji z ludzi na komputery, najistotniejszym czynnikiem wydaje się odpowiednie przygotowania organizacji na te zmiany.
W przypadku organizacji rozpoczynających swoją przygodę z Przemysłem 4.0, przede wszystkim doradzamy nad właściwym poprowadzeniem tego procesu. Gruntownie analizujemy procesy produkcyjne, logistyczne, biurowe i wspomagające, identyfikując czynniki ograniczające transformację i wskazujemy możliwe rozwiązania eliminujące problemy organizacyjne, procesowe czy techniczne. Nie zawsze potrzebne są rozwiązania cyfrowe, niekiedy wystarczy ograniczyć się do doradztwa lub też wprowadzenia „analogowej” zmiany, która choć nie wymaga inwestycji w IT, przynosi wymierne efekty. Dlatego przed wdrożeniem systemów IT, warto uporządkować procesy wykorzystując takie metody jak: Lean Management, MTM, czy Six Sigma, przystosowanych do wyzwań stawianych przez Przemysł 4.0. Co ważne, pracujemy wspólnie z klientem we wszystkich fazach wdrażania zmiany i jesteśmy odpowiedzialni za efekt końcowy projektu, którym jest przygotowanie struktury organizacji do wejścia w przemysł 4.0.
Przed wdrożeniem rozwiązań Przemysłu 4.0, bardzo ważne jest przeprowadzenie szkoleń i wdrożeń w zakresie tzw. cyfrowej kultury, zmian kompetencyjnych, podniesienia kwalifikacji zarówno pracowników niskiego jak i wysokiego szczebla. Następnie prace nad ustabilizowaniem i „ułożeniem” podstawowych procesów w firmie. Nie można np. stworzyć automatycznych systemów planistycznych czy kontrolnych, nie posiadając normatyw a w efekcie wiedzy o C/T i L/T produkcyjnych, czasach przezbrojeń etc… W praktyce często spotykamy się z sytuacją, że już w pierwszych fazach transformacji, nieświadomi skutków klienci oczekują wdrożenia zaawansowanej technologii. W efekcie przynosi to jedynie niewielkie i najczęściej lokalne usprawnienie, którego efekt często zostaje „wchłonięty” przez nieefektywne i nieprzygotowane obszary sąsiadujące.
Rozwiązanie informatyczne czy automatyczne, samo w sobie w większości przypadków nie rozwiązuje problemów w organizacji, czego organizacje nie są świadome, podejmując decyzję o wdrożeniu rozwiązań z obszarów automatyki czy IT. Faktyczne efekty, najczęściej w postaci oszczędności, generowane są w wyniku kompleksowych projektów optymalizacyjnych, które podobnie jak procesy tradycyjne, poprzedzone muszą być analizą strategiczną i studium wykonalności, w efekcie których określone zostaną cele, potrzeby i zasoby, niezbędne do realizacji założonych celów. W przypadku Przemysłu 4.0 działania te muszą być rozszerzone o analitykę danych oraz nową kulturę organizacyjną, pozwalającą odnaleźć się w nowym, zdigitalizowanym świecie.
Nieco inaczej wygląda transformacja w przypadku organizacji przygotowanych do spełnienia wyzwań Przemysłu 4.0. Nie odpowiadamy wtedy na pytanie czy, tylko które rozwiązanie usprawniające będzie najbardziej efektywne. Czy możemy je wdrożyć w strukturze organizacyjnej pionowej czy poziomej przedsiębiorstwa. Działamy analogicznie do dotychczasowych praktyk stosowanych dla przemysłu 3-ej generacji z tym, że modyfikujemy dotychczasowe metody Lean, czy 6sigma, dostosowując je do pracy w środowisku Smart Factory. Oferujemy konkretne narzędzia wspomagające pracę automatów, robotów, systemów informatycznych, traktując je jako pełnoprawne elementy systemu decyzyjnego, wykonawczego i zarządczego. Wypracowujemy narzędzia do kontroli tych systemów a przede wszystkim ich optymalizacji w punktu widzenia funkcji celu wypracowanej wspólnie z klientem. Wdrażamy rozwiązania wspomagające podstawową i zaawansowaną akwizycję oraz analitykę danych, których zwieńczeniem są modele i systemy sztucznej inteligencji, wspomagające procesy decyzyjne lub bezpośrednio sterujące tymi procesami.
Jakie są korzyści wynikające z cyfrowej transformacji fabryk? Czy mógłby Pan podać konkretny przykład?
Niedawno zrealizowaliśmy projekt w firmie Neuca, będącej krajowym liderem w obszarze dystrybucji farmaceutyków. Problem planistyczny w Neuce był bardzo skomplikowany. Aby uświadomić sobie skalę złożoności zagadnienia, należy spróbować sobie odpowiedzieć na następujące pytania. W jaki sposób zarządzić magazynem, w którym codziennie kompletowanych jest około 200 000 linii oraz kilkadziesiąt tysięcy zleceń? W jaki sposób przewidzieć czas potrzebny na skompletowanie nowego, unikatowego, niewystępującego wcześniej zlecenia? W jaki sposób uwzględnić w planie dynamicznie napływające zlecenia (kilkaset w ciągu godziny)? W jaki sposób optymalizować sekwencję zleceń do realizacji, biorąc pod uwagę fakt, że każde z nich może przejść jedną z 16 dostępnych marszrut i kilkadziesiąt stanowisk automatycznych i manualnych?
Organizacja była wysoce rozwinięta w zakresie akwizycji danych, ich udostępniania on-line i komunikacji z zewnętrznymi, naszymi autorskimi systemami. Dzięki wykorzystaniu analityki danych i sztucznej inteligencji, znacząco zoptymalizowaliśmy zarządzanie magazynem poprzez zastosowanie automatycznego algorytmu – robota planistycznego, wspomagającego proces kompletacji. Tym samym zastąpiliśmy ludzi, którzy wykonywali tę czynność dotychczasowo, znacząco podnosząc efektywność procesu. Dotychczasowi planiści zostali przygotowani do pracy w nowych warunkach. Poprzez system szkoleń wypracowano nowe standardy ich pracy, skupiające się na kontroli i ciągłej optymalizacji procesu kompletacji, identyfikacji wąskich gardeł i ograniczeń, które mogły by zakłócać pracę robota planistycznego
Mimo wysokiej kultury informatycznej, firmie brakowało znajomości dokładnych czasów komplementacji każdego zlecenia, ze względu na złożoność procesu, liczbę zamówień, liczbę pojemników i codziennie kampanie promocyjne, lokalizację produktów. Liczbę pracowników potrzebnych w kolejnym dniu szacowano jedynie w oparciu o historię, jednocześnie informacja o zwiększonej kompletacji pozwalała zabezpieczyć zasoby do obsługi tylko danego stanowiska, nie stanowiąc komunikatu zarządczego objaśniającego wpływ promocji na pozostałą część procesu kompletacyjnego. Dzięki zaawansowanej analizie ogromnych zbiorów danych historycznych Istotne elementy procesu zostały uwzględnione w modelach sztucznej inteligencji, jako bazy wiedzy kalkulatorów i normatyw a w efekcie bazy wiedzy dla robota planistycznego
W efekcie udało się uniknąć inwestycji w nowy magazyn, którego koszt wynosi około 50 mln zł. Skrócono Lead Time o 42 proc., zwiększono także kluczowe wskaźniki takie jak wydajność oraz znacząco zredukowano koszty obsługi. Opracowano nowe standardy pracy, jej opomiarowania, nowatorskie podejście do kluczowych wskaźników procesu i rozliczania pracowników. W tym zakresie również wykorzystano modele sztucznej inteligencji. W efekcie o kilkanaście procent zmniejszono parametr „cost-to-serve”
Dziękuję za rozmowę
Dr Jacek Kozłowski zdobywał doświadczenie zdobywał realizując projekty badawczo-rozwojowe dla największych światowych firm stosując metodykę Six Sigma w środowiskach produkcyjnych oraz usługowych m.in. dla Neuca, Farmada Transport, Trinity Corporate Services, Harper Hygienics, Wamtechnik, UDS, Max-Pol, Bakalland, Delecta, Mercor. Dr Kozłowski jest partnerem ASD Consulting i czynnym wykładowcą na Politechnice Warszawskiej na Wydziale Inżynierii Produkcji. Jego zainteresowania naukowe dotyczą wykorzystania metod sztucznej inteligencji w procesach produkcyjnych.