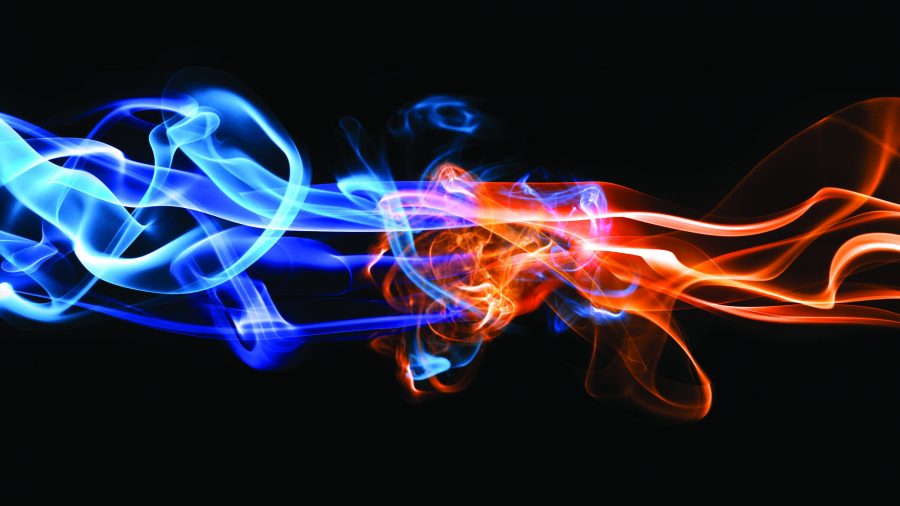
Pogodzić ogień z wodą
Od kilku lat czołowym problemem firm produkcyjnych w Polsce jest niezadowalająca obsługa klienta. Przebija to wyraźnie w prowadzonych przez MPM corocznych badaniach wyzwań stojących przez polskim przemysłem. Co najmniej 60 proc. przedsiębiorstw deklaruje potrzebę poprawy terminowości, ale udaje się to zrealizować tylko co drugiej z nich. Coraz więcej firm zaczyna odczuwać problemy z tym związane: począwszy od kar, po utratę klientów czy rosnącą presję na udzielanie rabatów zauważaną przez handlowców.
Jednocześnie firmy próbują zredukować swoje zapasy – im dłużej trwa hossa rynkowa, tym mocniej zaczyna niepokoić groźba powtórki kryzysu z 2009 roku. Zarządy chcą odzyskać zamrożoną w zapasach gotówkę zanim będzie za późno. Tyle jeśli chodzi o zamiary – zamiast bowiem spodziewanej poprawy płynności finansowej w dużej ilości zakładów zapasy rosną. Mówiąc krótko – firmy tracą kontrolę nad zapasami nie zapewniając poprawy obsługi klienta.
Pod koniec 2018 roku zdecydowaliśmy się z bliska zbadać przyczyny. W 2019 konsultanci MPM przyjrzeli się szczegółowo procesom, decyzjom itp. w 16 firmach z różnych branż, od przemysłu spożywczego, przez elektronikę po automotive. W siedmiu z nich dominującym (lub jedynym) modelem produkcji było wytwarzanie wyrobów gotowych na magazyn. Pozostałe działały w modelu produkcji na zamówienie (w dwóch wypadkach łącznie z projektowaniem). Nie jest to oczywiście reprezentatywna liczba firm, ale pozwala ona już zauważyć typowe błędy i sposoby radzenia z nimi przez najlepszych.
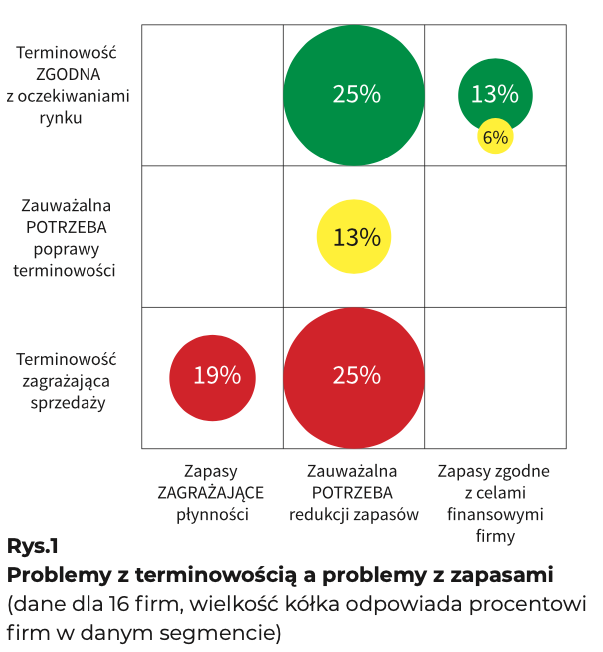
Spośród zbadanych firm wyróżniają się dwie przeciwstawne grupy (rys.1): firmy o słabych wynikach w których zapasy, koszty bądź obsługa klienta były na krytycznie groźnym poziomie (na rysunku oznaczone kolorem czerwonym) oraz wybijające się przedsiębiorstwa, w których terminowość lub zapasy spełniały lub przekraczały oczekiwania rynkowe (kolor zielony – przy czym jedna firma z tej grupy pomimo dobrych zapasów i terminowości miała kłopoty z kosztami i została oznaczona na żółto). Mimo znacznych różnic potrzeb klientów, stosowanych technologii, szerokości asortymentu czy trwałości produktów i komponentów okazało się, że w obu tych grupach wskazywano na podobne wyzwania. Jednak inaczej do nich zabrały się firmy „zielone”, a inaczej te, które sobie nie radziły.
Produkcja nie trzyma się planów
Spośród zidentyfikowanych zagadnień dotrzymywanie planów produkcyjnych (rys 2) jest najczęściej poruszanym tematem w kontekście słabych wyników firmy (tzn. zapasów, kosztów, terminowości).
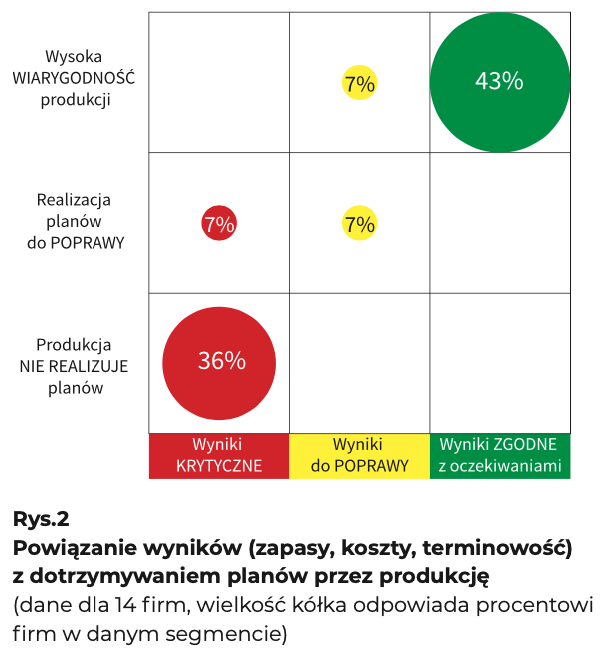
Miara ta mówi o stopniu, w którym zadania zlecone produkcji są realizowane na czas, w wymaganej ilości i jakości (rodzaj wewnętrznej terminowości). W przypadku przedsiębiorstw „czerwonych” powszechne są narzekania planowania na produkcję, a produkcji na planowanie. Na wysoką niepewność realizacji planów wpływa zarówno awaryjność maszyn, absencja pracowników, ich kompetencje, jak i brak dostępności komponentów czy nierealne lub często zmieniane harmonogramy produkcji. Ostatnie czynniki są często pokazywane przez produkcję, jako wiodące i z tego powodu wiele firm doskonalenie łańcucha dostaw chce rozpocząć od usprawnienia planowania.
Czerwone firmy zazwyczaj zaczynają od powołania planisty produkcji (czasem wręcz jest to pierwsze i jedyne stanowisko planistyczne w firmie). Zadaniem tej osoby jest tworzenie i aktualizacja harmonogramów. Najczęściej wykorzystywany jest do tego Excel zbudowany przez planistę. W przypadku kilku planistów każdy często buduje własne narzędzie, co bardzo utrudnia wzajemną zastępowalność (choćby z powodu choroby). Im bardziej szczegółowy plan, tym mocniej trzeba uwzględniać specyfikę pracy maszyn, ludzi, narzędzi czy materiałów i tym bardziej planowanie uzależnia się od eksperckiej wiedzy i doświadczenia harmonogramistów. Szybko się jednak okazuje że choć produkcja widzi co ma zrobić w najbliższych okresach, to plany te ulegają ciągłym zmianom. Problemem też staje się „eksperckość” harmonogramistów i ich wąska specjalizacja. W przypadku choroby zastąpienie takiej osoby jest często niewykonalne i produkcja nagle dostaje dużo gorszej jakości plany. Niektóre firmy próbują rozwiązać ten problem przez wdrożenie systemów automatyzujących harmonogramowanie. Intencja jest prosta: wspomniana wiedza zostanie przeniesiona z głowy do firmy, a proces aktualizacji harmonogramów zostanie drastycznie przyspieszony. Wiąże się z tym konieczność zapewnienia systemowi aktualnej i rzetelnej informacji o postępach produkcji. Są w tym celu stosowane dwa podejścia: wdrożenie systemów klasy MES (Manufacturing Execution System) oraz – bardziej w przypadku pozostania przy excelowych narzędziach – organizowanie zazwyczaj codziennych operatywek produkcyjnych.
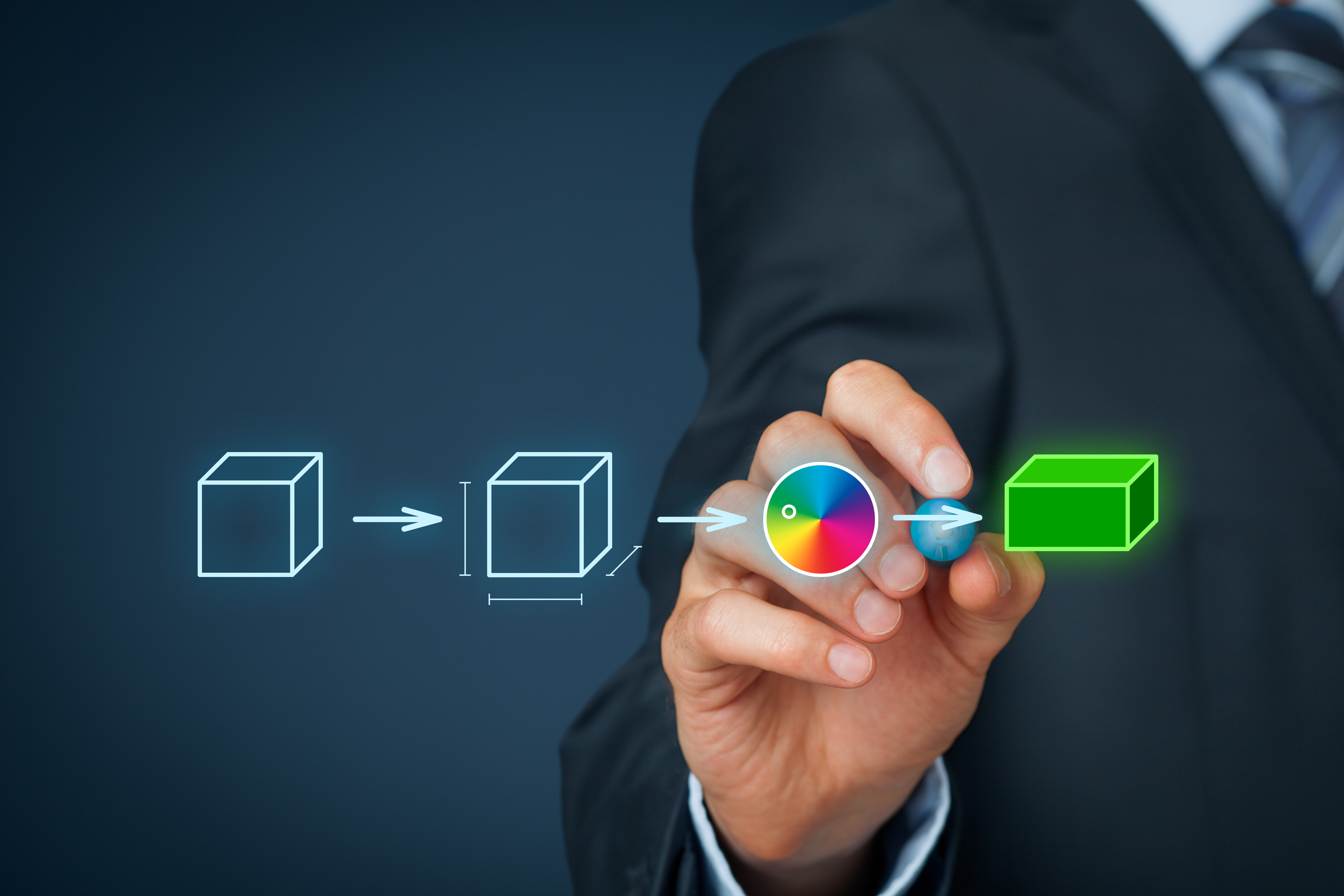
MES jako kaganiec
W firmach czerwonych celem systemów MES było niemal zawsze „wymuszenie na produkcji terminowego i wiarygodnego raportowania postępu prac”. Mówiąc krótko: firma (przy aplauzie planowania) traktowała MES jako rodzaj kagańca zintegrowanego z elektryczną obrożą narzuconego produkcji. Nic więc dziwnego, że takie rozwiązania często prowadzą do wzrostu konfliktów wewnątrz firmy i w żadnym z obserwowanych przypadków nie przyczyniały się do poprawy jej wyników. Zaczyna się gra o przetrwanie, bo tak siłowo wprowadzane rozwiązanie zaczyna albo być lekceważone przez produkcję, albo harmonogram zaczyna ją paraliżować.
W zielonych firmach często podobne rozwiązania są wdrażane w zupełnie inny sposób. Tam, gdzie zaczęto od sterowania produkcją widać pierwszą zasadniczą różnicę: porządki w tym obszarze nie były wprowadzane, by dyscyplinować produkcję, ale by wyeliminować zakłócenia generowane przez nią samą oraz przez planowanie. Doskonale w tym sprawdzają się techniki lean manufacturing, takie jak SMED pozwalający zmniejszyć partie produkcyjne, TPM zwiększający dostępne moce produkcyjne czy 5S zmniejszające straty wynikające z bałaganu. Ze strony planowania zaś często uderzano w fundamenty: jakość danych o zapasach, strukturach materiałowych czy technologiach. Niejako efektem ubocznym takich działań jest wzrost zaangażowania nadzoru i pracowników produkcyjnych, a także ich zrozumienia wobec potrzeb planowania i tego, jak to się przekłada na zmniejszenie ich własnych problemów.
Duży nacisk położono również na raportowanie. Dobrym przykładem różnicy między firmami czerwonymi a zielonymi jest przykład podejścia do systemu MES. W jednej z najbardziej zaawansowanych firm w naszym badaniu MES jest obecny na każdym stanowisku. Nie zajmuje się on tylko zbieraniem informacji o postępie produkcji, ale także zbiera dane o problemach jakościowych oraz stanie maszyn. MES nie służy dyscyplinowaniu produkcji, ale jej pomaga. Pracownik wie, że szybka i dokładna informacja pozwoli równie szybko uzyskać pomoc np. utrzymania ruchu. Postęp prac zbiera się niejako przy okazji.
Kaganiec z obrożą szybko się wdraża. Potem trzeba lat, by wyeliminować negatywne skutki takiego siłowego podejścia. Wypracowanie wspólnego zrozumienia sensu częstego monitorowania sytuacji na produkcji zajmuje miesiące, ale przynosi długotrwałe korzyści. Trzeba tam jednak zacząć od przekonywania, od pokazania szerszego kontekstu i korzyści jakie mieć będą operatorzy, mistrzowie i cała firma z nowego rozwiązania.
Zbyt krótki horyzont planowania
Kluczem do sukcesu wszystkich firm „zielonych” było sięgnięcie do głębokich przyczyn problemów. W analizowanych przypadkach były nim niewłaściwe planowanie mocy produkcyjnych i problemy z dostępnością materiałów. Sezonowy lub permanentny brak zdolności prowadził do nakręcającego się konfliktu ze sprzedażą / klientami. Napływające zamówienia zawsze były prezentowane jako strategiczne i priorytetowe, a więc wymagające realizacji w wymaganym terminie. Kłopot w tym, że im bardziej ulegano takiej mrzonce, tym bardziej problem narastał. Pogarszająca się obsługa klienta doprowadzała do coraz większej nerwowości klientów, a to potrafiło się czasem odbić na spadku produktywności. Chcąc robić więcej niż można zaczęto produkować mniej…
Jeśli popyt przekracza możliwości, a ich rozbudowa dla firmy jest zbyt ryzykowna trzeba zarządzić popytem. Jest to możliwe, gdy z klientami rozmawia się o nadchodzącym popycie. Nie wszyscy będą obsłużeni równie dobrze, bo nie ma na to możliwości. Albo firma podejmie decyzję o priorytetach albo wygra ten kto najgłośniej krzyczy.
„Powszechne są narzekania planowania na produkcję, a produkcji na planowanie.”
Firmy „zielone”, które musiały radzić sobie z nadmiernym popytem wdrożyły mniej lub bardziej zaawansowane planowanie długoterminowe Sales & Operations Planning (S&OP). W jednym z najciekawszych przypadków – przedsiębiorstwie produkującym wyroby projektowane na zamówienie (Engineering to Order, EtO) wysiłek planowania i sprzedaży przeniesiono z pytania jakim cudem dotrzymać obiecanego już terminu dostawy złożonych zamówień na szukanie optymalnego z punktu widzenia sprzedaży i produkcji terminu dla jeszcze negocjowanych zapytań ofertowych. Prócz wiedzy inżynierskiej jak spełnić szczególne oczekiwania klientów handlowcy zaczęli także sprzedawać zdolności produkcyjne. Dzięki dobremu zgraniu na poziomie S&OP wiedzieli oni, że te terminy były realne i dotrzymywalne. Komfort ich pracy uległ znacznej poprawie.
Dostępność komponentów w części firm dotyczyło materiałów o długich czasach dostawy. Często nawet w firmach typu EtO są one problemem. Klient, który jest prawie zdecydowany wciąż zwleka. Zakupy powinny wkrótce ruszać, ale nie mając zamówienia nie mogą rozpocząć procesu. Jeśli materiał jest w miarę wspólny można zaryzykować chwilowym wzrostem zapasu. Ale co jeśli to drogi komponent specyficzny? Podobnie rzecz się ma i w innych typach produkcji. Specyficzne materiały o długich czasach dostawy wymagają kupowania w oparciu o prognozy, których wiarygodność jest jaka jest. Czasem firmom udawało się wyeliminować tego typu materiały lub tańszych dalekowschodnich dostawców zastępowano drogimi europejskimi. Oszczędności po stronie zredukowanego zapasu przewyższały koszty nabycia. Czasem jednak nie można było posłużyć się takim rozwiązaniem. Wtedy sięgano po proces planowania średnioterminowego Master Scheduling (zwanym też Master Production Schedule, MPS). Zdejmuje on z zakupów konieczność zgadywania, które materiały trzeba już kupić i jak duży zapas będzie bezpieczny. Przenosząc to na wyższy poziom struktury materiałowej (z zakupów na przewidywanie spływu produktów / rodzin wyrobów) umożliwia podjęcie decyzji o ryzyku budowania zapasu.
Osobnym typem problemów są braki komponentów o krótkich czasach dostawy. W jednej z „zielonych” firm były one głównym sprawcą pierwotnych problemów z terminowością. Zapanowano nad nimi restrykcyjnie trzymając się okresu zamrożonego i zbudowaniu niewielkich zapasów bezpieczeństwa na wypadek problemów z dostawą. Decyzje te zostały zaakceptowane mimo spodziewanego wzrostu zapasów. Jednak szybko okazało się że nie dość że dostępność komponentów wzrosła, to faktyczny zapas spadł. Dlaczego? Bo największym wrogiem łańcucha dostaw jest chaos, zwłaszcza generowany przez paniczne próby gaszenia pożarów. Uspokojenie planów umożliwia zapanowanie nad strukturą zapasów, co często prowadzi do ich zmniejszenia. W tym miejscu warto wspomnieć o koncepcji w Polsce jeszcze nie sprawdzonej (stan na styczeń 2020), a niosącej nadzieję poradzenia sobie z problemem dostępności komponentów o krótkich (i prawdopodobnie średnich) czasach dostawy – Demand Driven Material Requirements Planning (DDMRP). Powinna ona działać bez konieczności tak restrykcyjnego zamrażania planów.
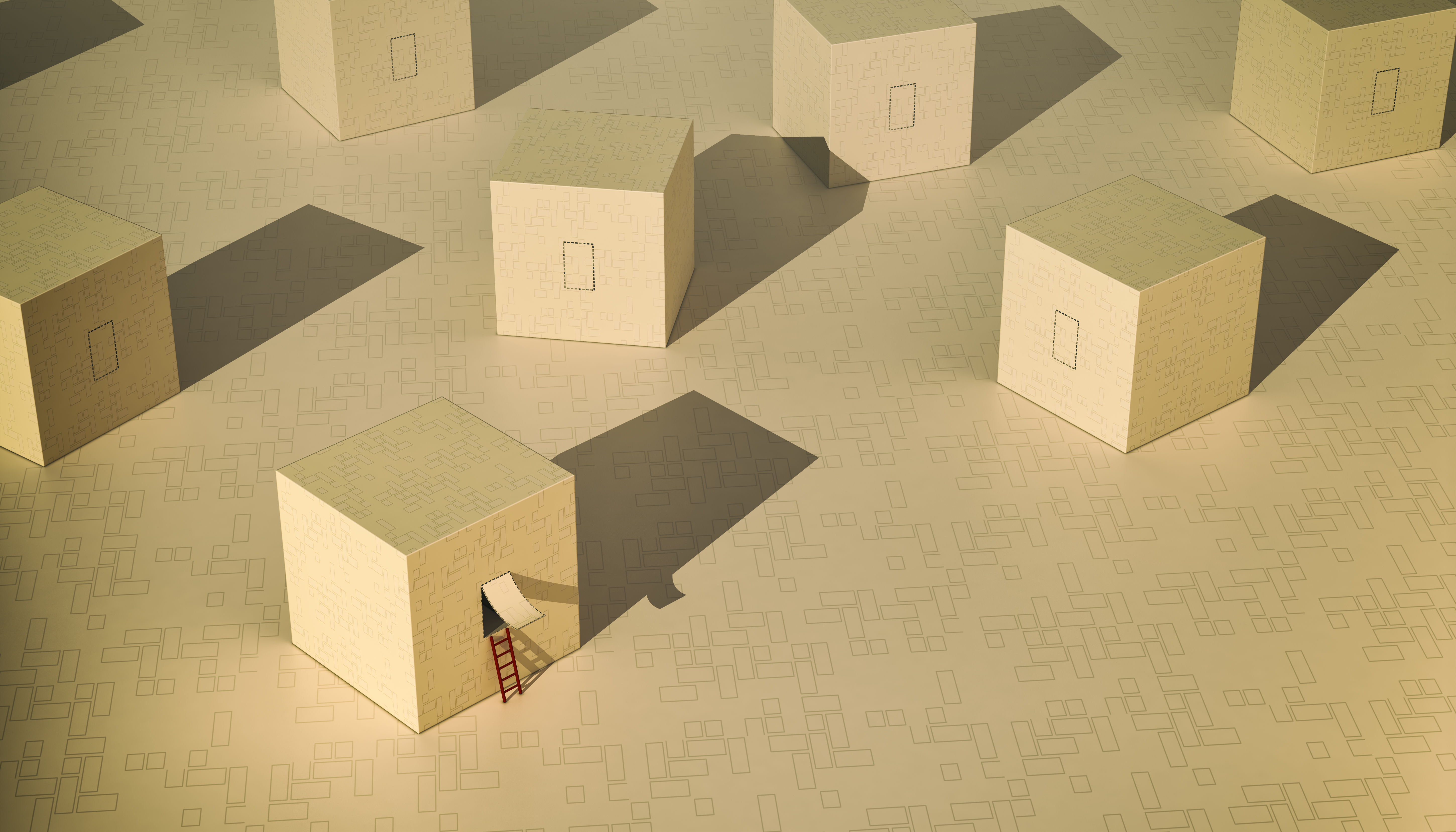
Kilka wskazówek
W artykule tym omówiliśmy najczęściej poruszany wśród badanych firm temat: dostrzegalny silny związek między niedotrzymywaniem planów a niezadawalającymi efektami firmy. Zobaczyliśmy że firmy „czerwone” próbując go rozwiązać tak naprawdę skupiają się na skutkach, a nie dotykają przyczyn. Często też postrzegają to jako problem ludzki koncentrując się niemal wyłącznie na systemach kontroli i rozliczania. „Zielone” firmy zazwyczaj postępują odwrotnie – ludzie np. na produkcji traktowani są jak potencjalni sprzymierzeńcy, osoby z którymi należy uzgodnić rozwiązanie. Wysłuchać co mają do powiedzenia i dać im możliwość włączenia się w zmianę. Wtedy zaczynają oni mocno wspierać zmianę. Firmy efektywne nie walczą ze skutkami a skupiają się na przyczynach. Najczęstsze z nich to zabezpieczenie dostępności mocy produkcyjnych w ciągu całego roku lub w sezonie oraz dostępności materiałów i komponentów pod zmieniający się popyt. W większości przypadków konieczne było znaczne wydłużenie horyzontu planowania (S&OP czy MPS). Nie wyczerpuje to wszystkich możliwych zagadnień, ale sądzimy, że gdyby porządek w przypadku tych dwóch został powszechnie wprowadzony to ilość „zielonych” firm gwałtownie by wzrosła.
Na koniec warto wskazać kilka wskazówek dla tych z Czytelników, którzy szukali by porad w jaki sposób pogodzić ogień z wodą, lepszą terminowość z mniejszymi zapasami:
- Oceń jak dziś pracuje twój łańcuch dostaw. Podstawowe miary to terminowość dostaw oraz zapasy. Umieść swoją firmę na schemacie z rysunku pierwszego. Jeśli należysz do „zielonych” pochwal się dzięki czemu udało Ci się znaleźć w tym miejscu. Jeśli nie – przejdź do kroku 2
- Zacznij od podstaw. Nikogo nie przekonasz do większych zmian jeśli na twoim podwórku zauważalny jest bałagan. Stany magazynowe są wiarygodne? Technologie, dane o zużyciach (Bill of Materials) są prawidłowe? W systemie nie zalegają zlecenia produkcji, zakupu czy sprzedaży z minioną datą? Czy reguły nadawania indeksów są prawidłowe? Jak długo produkt klasyfikowany jest jako nowość? Itp. itd.
- Sprawdź czy głównym źródłem twojego wyzwania jest zapewnienie zdolności produkcyjnych (maszynowych, ludzkich ale podobnie traktuj dostawców). Czy ich zwiększenie jest bardzo ryzykowne i firma nie chce go podjąć? Czy można zbudować zapas przygotowujący na sezon? Czy ryzyko budowy takiego zapasu jest duże? Jeśli tak – rozważ wdrożenie procesu planowania długoterminowego Sales & Operations Planning (S&OP)
- Jeśli głównym czynnikiem zakłócającym są braki materiałów o długich czasach dostawy rozważ wdrożenie procesu planowania średnioterminowego Master Scheduling (zwanym też Master Production Schedule, MPS)
- Jeżeli jednak to materiały o krótkim czasie dostawy są głównym powodem zakłóceń, to rozważ wdrożenie Demand Driven Material Requirements Planning (DDMRP)
Artykuł pierwotnie opublikowany w czasopiśmie Logistyka Produkcji – nr. 1/2020