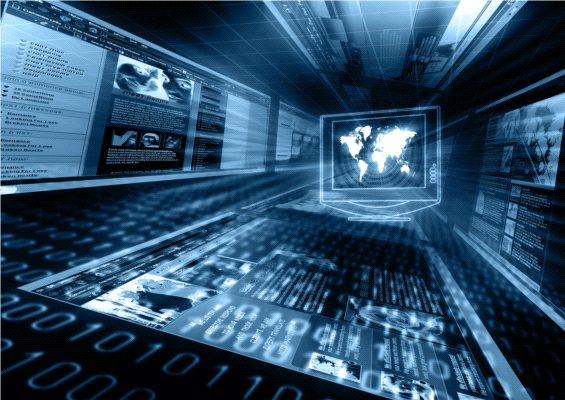
Potęga danych w zarządzaniu produkcją
Producenci, którzy chcą pozostać „the best in the class” muszą uwzględniać dynamicznie zmieniający się popyt, pogłębiającą się indywidualizację produkcji i co za tym idzie - skrócenie czasu życia produktów. Producenci zauważają również, że wysoka jakość stawia czasem pod znakiem...
W wieku XIX Lord Kelwin wypowiedział dość proste zdanie, że jeżeli czegoś nie można zmierzyć, to nie można tego ulepszyć. Wydaje się, że słowa te idealnie wpisują się w logistykę produkcji, o czym może świadczyć parafraza dokonana przez W. Edwardsa Deminga: „jeśli nie mierzymy procesu, to nie możemy nim zarządzać”, a następnie przez architekta koncepcji Six Sigma, dr Mikela J. Harry’iego, który również użył myśli fizyka: „jeśli nie mierzymy, to nic nie wiemy, jeżeli nie wiemy, to nie możemy działać, jeżeli nie działamy to narażamy się na straty”.
W czasach Kelwina pojęcie fabryka, czy zakład produkcyjny było określeniem miejsca wytwarzania dóbr. Produkty i ich jakość definiowały producenta czy też proces produkcyjny. Dziś, w erze globalizacji, proces produkcyjny jest czymś więcej. Ma nowe składowe, takie jak: elastyczność, różnorodność, czas dostawy, czas cyklu produkcyjnego, przejrzystość procesu, genealogię bądź traceability produktów. Rynek nazwał to zjawisko „adaptive manufacturing”, co można tłumaczyć jako „produkcję gotową do adaptacji”. Całe postrzeganie współczesnej produkcji to już niejako podłączenie maszyn produkcyjnych bezpośrednio do rynku odbiorcy, do klienta. Producent nie tylko powinien sprostać tym nowym siłom rządzącym na światowym rynku, ale też umieć z nich czerpać.
ERP – czy potrzeba więcej?
Szybkość przepływu informacji i konieczność reakcji jest kluczowa na produkcji. Sposób przesyłania danych również. Dotychczasowy model wertykalny, nie przystaje do dzisiejszej filozofii zarządzania „continuous improvement”. Jedynie uzupełnienie o horyzontalny przepływ danych da pewność, że szybsza informacja to szybsza reakcja na zmiany: skracanie czasów wprowadzania produktów na rynek (time to market), osiąganie zdolności produkcyjnych (time to volume) i redukcja czasu produkcyjnego (lead time). ERP za pośrednictwem wprowadzonych danych nie jest w stanie modyfikować założonych planów na podstawie bieżących zdarzeń i, co najważniejsze, nie posiada wglądu w proces produkcji w toku. Nic nie wie ani o ewentualnych zakłóceniach na produkcji, ani nie dostarcza informacji o genealogii produktu, co jest krytyczne w momencie wystąpienia wadliwej produkcji.
Producent nie tylko powinien sprostać tym nowym siłom rządzącym na światowym rynku, ale też umieć z nich czerpać
System ERP już w rozszyfrowaniu swojego akronimu – Enterprise Resource Planning – wspiera realizację celów i zarządzanie całego przedsiębiorstwa w oparciu o jego zasoby. Niestety, w tak zwanym czasie rzeczywistym ERP już tak ambitny nie jest, a raczej z definicji, być nie może. Jednostki czasowe jakimi się ERP zajmuje to tygodnie, dni lub w najlepszym wypadku, zmiany, w związku z czym nie może służyć do bieżącego w czasie nadzorowania procesów i ich harmonogramowania. Za to systemy klasy MES, dzięki współpracy z systemami technologicznymi typu SCADA (Supervisory Control And Data Acquisition) i HMI (Human-Machine Interface), są gotowe przesyłać użytkownikowi informacje w czasie bieżącym. MES jest nie tylko odbiorcą danych ale również ich dostawcą, w tym właśnie do systemu ERP, co z kolei pozwala firmie upewnić się co do tego, czy założone harmonogramy produkcji, a przez to i cele biznesowe i finansowe są realizowane.
Siła MES
MES to system, który w szybki i efektywny sposób pozwala modelować procesy produkcyjne oraz odbierać informacje o ich przebiegu. Pozwala śledzić produkty, komponenty oraz surowce na każdym etapie ich życia w zakładzie; począwszy od złożenia zamówienia, poprzez realizację produkcji, kończąc na wysyłce do odbiorcy. Dzięki wykorzystaniu definiowalnych raportów daje pełny obraz zjawisk zachodzących na hali produkcyjnej na najniższych poziomach szczegółowości (maszyny i pracowników). Celem tego systemu jest kontrolowanie i gromadzenie informacji o procesie produkcyjnym tak, by był on co do szczegółu przejrzysty, tak pod względem przebiegu procesu jak i wykorzystanych zasobów.
Pierwsze systemy klasy MES pojawiły się już 20 lat temu. Były wtedy jeszcze zbyt niedojrzałe, zbyt kosztowne i zbyt mało efektywne, by ich wdrożenie można było uznać za korzystne dla usprawnienia procesów produkcji. Obecnie czas życia produktów na rynku jest krótszy, marginesy zysków mniejsze, a wymagania klientów wyższe. Zebrane przez system MES informacje o procesie produkcyjnym wspomagają zarządzanie na zasadach „Lean Manufacturing”, czyli „szczupłej produkcji” lub filozofii Six Sigma. Główną ideą jest ciągłe udoskonalanie procesu produkcji w celu eliminacji czynności nieproduktywnych, a przez to usprawnienie i skrócenie cykli produkcyjnych przy zachowaniu wysokiej jakości i redukcji kosztów. Obecnie coraz częściej można zauważyć połączenie zalet filozofii Six Sigma i metodologii Lean Manufacturing, a nowy twór wychodzący z połączenia obydwóch podejść do produkcji nazywa się Lean Six Sigma lub Lean Sigma.
Według raportu przygotowanego przez Instytut AMR Research, które wzięło pod lupę zakłady produkcyjne z różnych branż, które wdrożyły systemy MES, koszt jego wdrożenia potrafi się zwrócić już po sześciu miesiącach. Może to uzmysłowić jak wielki potencjał oszczędności jest możliwy do wygenerowania w obrębie logistyki produkcji.
MES o efektywności
System MES gromadząc szczegółowe dane na poziomie operacyjnym jest doskonałym środkiem na wdrożenie „szczupłej” metodologii. Wskaźników, które dostarczą nam informacji o efektywności procesu produkcyjnego, tzw. KPI, jest wiele. Jednym z najważniejszych czynników ewaluacyjnych to OEE (Overall Equipment Effectivness – Całkowita Efektywność Wyposażenia) co daje nam informacje o wykorzystaniu parku maszynowego. Liczy się je na podstawie trzech elementów: dostępności, efektywności i jakości.
MES w szybki i efektywny sposób pozwala modelować procesy produkcyjne oraz odbierać informacje o ich przebiegu
Dzięki możliwości śledzenia procesu produkcyjnego i automatycznym dostępie do informacji w czasie rzeczywistym, menedżer produkcji może wnikliwie kontrolować proces produkcyjny i logistyczny na takim poziomie szczegółowości, jaki wcześniej nie był osiągalny. Według organizacji MESA International (Manufacturing Enterprise Solutions Association) korzyści finansowe jakie daje wdrożenie systemu MES wylicza się w przedziale od około 5 proc. do nawet 30 proc. Wynikają one bezpośrednio ze zwiększenia wydajności produkcji, zmniejszenia kosztów strat produkcyjnych, kosztów produkcji czy tak kosztochłonnej, produkcji wadliwej.
MES o genealogii
Ekspansja pająka jednak nie jest powodem do radości, zwłaszcza dla menedżerów Mazdy. Stawonóg wykorzystał konstrukcję odpowietrznika zbiornika paliwa w sportowych Mazdach i tkał tam sieci. Problem okazał się na tyle poważny, że na początku marca koncern ogłosił akcję przywoławczą 65 tysięcy samochodów. To jeden przykład. Inny z ostatniego czasu, już poważniejszy, to wycofanie ptasiego mleczka z półek sklepowych, ze względu na podejrzenie o możliwości znalezienia w nich szkła.
Prasa co jakiś czas ujawnia przypadki wadliwej produkcji u największych światowych producentów. Według badań Aberdeen Group aż 3 proc. przychodów pochłaniają błędy wychwycone w trakcie i po zakończeniu produkcji. Jak może tu przysłużyć się MES? System nie tylko wspiera standardy jakości i bezpieczeństwa takie jak HACCP, IFS, BRC, TQM, ale też umożliwia zbieranie informacji o genealogii produktu końcowego. Informuje o tym, kto, kiedy, co wyprodukował oraz jakie materiały wchodzą w skład produktu końcowego. Udostępnia możliwość gromadzenia i odnalezienia danych o dostawcy komponentów, partii, numerze seryjnym, warunkach produkcyjnych oraz jakichkolwiek zmianach, alarmach lub innych wyjątkowych sytuacjach dotyczących całego procesu produkcji. Dzięki traceability produktu producent otrzymuje wiadomości w jakiej np. partii czy serii produktu jest podejrzenie o znalezienie szkła.
Z pewnością nie można oczekiwać, że po wdrożeniu nawet najbardziej zaawansowanych systemów informatycznych błędy na produkcji się nie pojawią, ale dzięki takim narzędziom jak MES straty można ograniczyć.
Potęga MES
Wartość systemu MES jest nie do przecenienia. Według najnowszej edycji Logica MES Product Survey, która objęła badaniem 60 systemów MES od 57 dostawców, szacuje, że sprzedaż tych systemów wzrośnie w tym roku o 25 proc., co jest znacząco większe, gdyż we wcześniejszych latach zazwyczaj prognozowano wzrosty w przedziale od 10 do 15 proc.
Potęga MES tkwi w skrojonym na miarę rozwiązaniu, które wspiera czynności zarządcze poprzez gromadzenie setek tysięcy rozproszonych danych właściwych dla danej produkcji. Jeszcze 10 lat temu zalet wdrożenia upatrywano w informacji o wydajności warstwy technologicznej zakładów produkcyjnych. Dziś to przede wszystkim informacje o zasobach, surowcach, ich zużyciu, zarządzaniu recepturami, wydajności maszyn, czyli o całej produkcji w toku. Kierowanie ich do właściwych osób we właściwym czasie to sposób na sprawne zarządzanie logistyką produkcji i w myśl „continuous improvement” szansa na ciągłe doskonalenie, którego wymaga rynek.