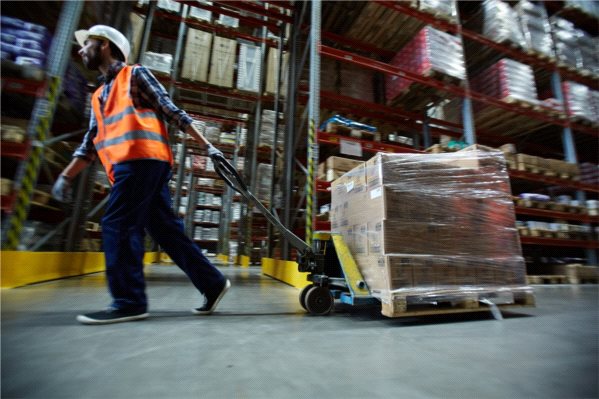
Proces kompletacji, czyli pan Jan na zakupach
Pan Jan dostał od żony listę zakupów i wybrał się do supermarketu. Chodzi po sklepie między regałami od półki do półki z listą, wybierając produkty do koszyka. W ten sposób realizuje proces kompletacji. Najprostsza manualna kompletacja zlecenia w magazynie odbywa się na...
Po pierwsze, należy zastanowić się, co jest wartością dodaną w procesie kompletacji. Żona oczekuje od pana Jana, że dostarczy wszystkie produkty z listy w wymaganych ilościach i wróci z zakupów o przyzwoitej porze. Wartością dodaną procesu jest więc pobieranie towaru z półek, podczas gdy szukanie produktów, chodzenie między półkami, sprawdzanie listy itp. to czynności, na które pan Jan chce poświęcić jak najmniej czasu. Ten sam mechanizm obowiązuje przy kompletacji zleceń w magazynie. Efektywna praca oznacza minimalizację czasu bezproduktywnego. Przykład pana Jana to w najprostszy sposób prowadzenia kompletacji zlecenia na zasadzie „człowiek do towaru” (man to goods) – podczas jednego przejścia przez magazyn kompletowane jest jedno zlecenie klienta. W takim procesie, zakładając pracę ze skanerem i ze wsparciem systemu WMS, około 50% czasu pracy magazyniera zajmuje chodzenie po magazynie, a tylko około 20% to efektywny czas pobierania towaru. Jeżeli dodatkowo weźmiemy pod uwagę, że kompletacja to najbardziej pracochłonny proces w magazynie (ok. 60% całkowitej pracochłonności, oczywiście zależnie od specyfiki magazynu i asortymentu), to jej efektywność jest kluczowa dla efektywności pracy całego magazynu.
Warto więc zadać pytanie o to, jak obecnie wygląda kompletacja? Jakie można zastosować techniki, aby zmaksymalizować wydajność w tym obszarze? Co chcemy osiągnąć poprzez implementację nowych rozwiązań w procesie kompletowania?
Proces procesowi nierówny
Różnorodność asortymentu na rynku pociąga za sobą różnorodność procesów i technik w magazynie. Magazyny obsługują różne rodzaje kompletacji zleceń w zależności od odbiorcy, np. przygotowanie towaru dla sklepów wiąże się z procesowaniem dużego wolumenu towaru i dużej liczby sztuk na pozycję zamówieniową. Już tutaj zakres możliwych struktur zamówień jest bardzo szeroki: inaczej wygląda zamówienie przy zatowarowaniu sklepu nowym asortymentem, inaczej przy bieżącym uzupełnianiu zapasu na półkach. Inaczej wygląda zamówienie dla małego sklepu typu convenience, inaczej dla hipermarketu. Na drugim biegunie mamy zamówienia w handlu internetowym B2C (business to customer) – tutaj mówimy o niewielkiej liczbie sztuk i pozycji na zamówienie i jednocześnie o masowej ilości zamówień i bardzo szerokim asortymencie.
Powyżej wspomnianą różnorodność dobrze ilustruje przykład jednego z europejskich magazynów dystrybucyjnych branży elektronicznej, który obsługuje sieć sklepów tradycyjnych oraz kanał sprzedaży e-commerce. Średnia liczba pozycji na zamówienie w tym magazynie wynosi:
- dla detalu: 14 pozycji / zamówienie
- dla e-commerce: 1,2 pozycji / zamówienie
Średnie wolumeny zamówień w tym magazynie wynoszą:
- dla detalu: 150 litrów / zamówienie
- dla e-commerce: 4 litry / zamówienie
Czy można zatem obsłużyć tak różnorodne struktury zamówień jednakowym standardem procesu? Z pewnością nie. Wielopozycyjne zamówienie o wolumenie palety można w miarę sprawnie skompletować tradycyjną ścieżką „człowiek do towaru”. Natomiast jednopozycyjne, jednosztukowe zamówienia kompletowane tą samą metodą powodują bardzo znaczący spadek wydajności. Nieefektywny czas, podczas którego pracownik przemieszcza się między lokalizacjami, może wtedy osiągnąć nawet ponad 90%.
Już wiemy, że naszą bolączką jest nieefektywny czas w procesie. Istnieje wiele metod zredukowania tego czasu, na przykład:
- kompletacja wielu zamówień w jednym cyklu (multi order picking): czas chodzenia pomiędzy lokalizacjami kompletacyjnym rozkłada się na kilka zleceń, czyli jego udział w jednostkowym zleceniu spada;
- kompletacja szeregowa (pick & pass): zamówienie jest kompletowane przez osoby pracujące w ograniczonej strefie magazynu i przekazywane kolejno od strefy do strefy (często z wykorzystaniem np. przenośników);
- kompletacja skonsolidowanej porcji wielu zamówień (batch picking) i sortowanie na indywidualne zamówienia: tutaj również czas bezproduktywny rozkłada się na wiele zleceń;
- kompletacja „towar do człowieka”: osoba kompletująca pracuje stacjonarnie, minimalizacja czasu bezproduktywnego przez zastosowanie mechanizacji i automatyki.
Powyższe przykłady prezentują różne możliwości minimalizacji czasu bezproduktywnego. Która metoda jest najlepsza? Nie ma tutaj uniwersalnego rozwiązania. Metoda pick & pass dobrze sprawdza się dla zamówień o dużej liczbie pozycji zamówieniowych i dużej liczbie sztuk małych produktów w zamówieniu. Metodą multi order picking możemy efektywnie kompletować zamówienia o małej i średniej liczbie pozycji i niewielkim wolumenie, w tym również e-commerce. Przy bardzo dużej liczbie drobnych zamówień e-commerce sprawdza się batch picking z sortowaniem. Kompletacja „towar do człowieka” zapewnia bardzo wysoką wydajność, jednak jej ograniczeniem jest rotacja towaru – zbyt szybko rotujące produkty mogą „zatkać” system goods to man.
Wniosek? Dobór strategii kompletacji zależy od struktury zamówień, charakterystyki produktu, jego rotacji, rozmiarów, warunków składowania itp. Konieczne może się okazać zastosowanie kilku strategii w ramach procesowania jednej grupy zamówień i późniejszej konsolidacji skompletowanych towarów (np. osobno dla małych i osobno dla gabarytowych artykułów lub osobno dla szybko i wolno rotujących).
Dalsza poprawa efektywności i jakości
Powyższe rozważania koncentrowały się na minimalizacji bezproduktywnej części procesu. Pytanie, czy możemy poprawić efektywność jego produktywnej części, jaką jest pobieranie, które generuje drugi w kolejności czas w procesie kompletacji. Poza tym jakość tej części procesu przekłada się bezpośrednio na jakość dla klienta. Błąd popełniony przy pobieraniu oznacza błędnie dostarczony lub niedostarczony towar – czyli utraconą sprzedaż lub dodatkowy koszt na obsługę reklamacji. Zależy więc nam tu nie tylko na jak najwyższej wydajności, ale również na minimalizacji błędów. Istnieją różne metody wsparcia czynności pobierania towaru i zmniejszenia ryzyka popełnienia błędu w procesie magazynowym – od powszechnego już potwierdzania operacji skanowaniem artykułu bądź lokalizacji, po bardziej wyrafinowane narzędzia, np. pick by voice lub pick by light. System pick by voice sprawdza się wszędzie tam, gdzie pracownik powinien mieć dwie wolne ręce do przekładania towaru, ale potwierdzanie poprawności pobrania jest tu ograniczone. Pick by light bardzo dobrze funkcjonuje np. w procesach kompletacji szeregowej lub multi order picking, wskazując pracownikowi dokładnie liczbę sztuk do pobrania oraz miejsce pobrania. Zastosowanie takiego systemu wraz z właściwie dobraną strategią kompletacji może skutkować nawet kilkukrotnym wzrostem wydajności w porównaniu do prostego manualnego procesu.
Kompletacja w łańcuchu procesów magazynowych
Przedstawione alternatywne metody mogą być wspierane różnorodnymi technikami o różnym poziomie automatyzacji, co tworzy w sumie szeroką paletę możliwych rozwiązań. Wspomniane strategie kompletacji, czy przykładowe środki techniczne to tylko wierzchołek góry lodowej. Rynek oferuje obecnie mnogość różnorodnych rozwiązań o różnym stopniu automatyzacji. Które z nich jest najlepsze?
Odpowiedź można uzyskać jedynie w wyniku opracowania wielowariantowej koncepcji, kalkulacji kosztów oraz nakładów. Pamiętajmy, że nie możemy projektować procesu kompletacji w oderwaniu od pozostałych procesów magazynowych: uzupełniania lokalizacji po jednej stronie, kontroli, konsolidacji, pakowania i wysyłki po drugie stronie. Zastosowanie wąsko wyspecjalizowanej techniki kompletacji, zapewniającej wysoką wydajność pobierania, może pociągać za sobą zwiększony nakład pracy na proces uzupełniania lub konieczność pracochłonnej konsolidacji zamówień i w konsekwencji niższą wydajność całego procesu.
Dodatkowo w projektowaniu należy uwzględnić szereg innych czynników, jak np. strategia rozwoju firmy, prognozy wzrostu, zmiany w portfolio produktów, dostępność i jakość personelu. Jak widać, nawet przy projektowaniu pojedynczego procesu, obszar naszej analizy staje się bardzo szeroki.
Podejście holistyczne
Wiosek? Projektując magazyn, powinniśmy spojrzeć na projekt całościowo, a nie wycinkowo, skupiając się tylko na jednym procesie. Jest to tzw. podejście holistyczne, które zakłada, że nie jesteśmy w stanie rozpoznać prawidłowości rządzących pojedynczymi składnikami zjawiska bez analizy układu całościowego, który tworzą. Przykładem jest wspomniana powyżej poprawa funkcjonowania jednego elementu, która może pociągnąć za sobą negatywne efekty w działaniu całego układu. Znakomitym przykładem takiego układu całościowego jest właśnie centrum dystrybucyjne: skomplikowany system przetwarzający artykuły o różnorodnej charakterystyce, rotacji, wymogach i ograniczeniach.
Na taki układ składa się wiele mniejszych ogniw, które często pośrednio lub bezpośrednio wpływają na funkcjonowanie całości. Dlatego projektując magazyn, chcąc uzyskać sprawnie działający układ o wielu ogniwach, powinniśmy traktować projekt centrum dystrybucyjnego jako zintegrowaną całość. Należy wziąć pod uwagę zależności między procesami, wpływ każdego z nich na pozostałe, przepływy miedzy nimi. W końcu należy przeanalizować różne warianty rozwiązań, aby decyzja o inwestycji poważnych środków finansowych była poparta liczbami i przyniosła korzyści w przyszłości.
Komentarze
Łukasz Kańtoch, prezes zarządu, ISL Innowacyjne Systemy Logistyczne
Wśród oferowanych przez ISL rozwiązań zapewniających szybką i bezbłędną kompletację towarów, a w konsekwencji przyspieszenie realizacji zamówień, można wymienić systemy pick to light i speedy pick znajdujące zastosowanie w automatycznych systemach magazynowych typu Rotomat i regałach tradycyjnych. W regale automatycznym Rotomat w wersji HSP High Speed Picking o wysokości do 10 m podwójna listwa ledowa w oknie dostępowym wskazuje dokładną lokalizację danego towaru w regale, ilość sztuk do pobrania, lokalizacje sortowania/kompletacji do pojemników kompletacyjnych umieszczonych poniżej, a także umożliwia dotykowe zatwierdzanie zleceń. Towary wydawane są według najbliższej półki i sortowane już ręcznie do pojemników zbiorczych umieszczonych pod regałem, umożliwiając obsługę nawet do 1000 linii/h. Rozwiązanie szczególnie polecane jest do składowania i kompletacji elektroniki, kosmetyków, farmaceutyków, produktów optycznych, materiałów biurowych itp.
W przypadku regałów tradycyjnych i wózków kompletacyjnych zastosowanie znajduje system speedy pick działający w oparciu o przenośne panele z wyświetlaczem umieszczane na półce regału przy każdym pojemniku z towarem, na których wyświetla się informacja o lokalizacji danego towaru, liczbie sztuk, które należy pobrać z danego pojemnika lub którą należy do niego odłożyć. Zatwierdzanie zleceń odbywa się poprzez wciśnięcie przycisku na panelu sterowania. Sygnalizacja świetlna (różne kolory dla np. różnych statusów) na modułach może wskazywać kolejność kompletowania zamówienia na podstawie listy zleceń z zewnętrznego systemu IT. System speedy-pick jest elastyczny, gdyż działa bezprzewodowo, umożliwia równoczesną kompletację wielu linii zamówieniowych, jest intuicyjny i łatwy w rozbudowie.
Dariusz Ziomek, Systemy głosowe, IBCS Poland
Proces kompletacji jest zwykle procesem złożonym, który narażony jest na powstanie błędów na wielu płaszczyznach. Wybór strategii oraz metody kompletacji powinien być poprzedzony przeprowadzeniem szczegółowej analizy, gdyż w zależności od charakteru działalności pod uwagę będą brane różne czynniki. Należy jednak pamiętać, że dzisiejsze narzędzia do zarządzania magazynem tj. systemy WMS posiadają wiele rodzajów strategii i metod kompletacji, tym samy pozwalają na szybkie dostosowanie się do dynamicznych zmian w branży logistycznej.
Z perspektywy procesu kompletacji na jakość obsługi klientów wpływa czas realizacji zamówień oraz ich dokładność. Szybszą realizację zadania możemy osiągnąć poprzez redukcję przestojów pracownika i minimalizację jego czynności manualnych w procesie kompletacji.
Należy również zadbać o optymalne zaplanowanie rozmieszczenia całego asortymentu, jak i przejrzysty i logiczny system oznaczenia miejsc magazynowych, tak aby pracownik mógł szybko zlokalizować i pobrać właściwy towar.
Jednym z rozwiązań, które wpływa na zwiększenie wydajności i dokładności, a przy tym pozwala na redukcję kosztów operacyjnych, jest system głosowy. System głosowy to rozwiązanie, w którym wymiana danych pomiędzy systemem nadrzędnym typu WMS/EPR, a pracownikiem odbywa się za pomocą komend głosowych. Pozwala to na redukcję opóźnień powodowanych wprowadzaniem danych za pomocą klawiatury lub czytnika, jak i odczytywaniem poleceń z wyświetlacza terminala mobilnego lub kartki papieru. Efektem tego jest wzrost produktywności nawet do 35%. Komunikacja głosowa sprawia, że proces staje się prostszy, płynny, pracownik jest bardziej skupiony niż w przypadku pracy z terminalem mobilnym. Wpływa to na wzrost dokładności procesu. Dodatkowo system głosowy umożliwia szybkie wdrożenie nowych pracowników, którzy niekoniecznie muszą posługiwać się językiem polskim.
Krystian Czaja, projektant systemów logistycznych, WDX
Projektowanie systemów logistycznych opiera się w dużym stopniu na optymalizacji procesów wewnątrzmagazynowych. Nieodłącznym i często najbardziej czasochłonnym, jak i pracochłonnym elementem jest kompletacja. Możemy jednak wskazać kierunki zmian, które przyczynią się do zwiększenia jej efektywności.
Istotnym aspektem jest organizacja czasu i kategoryzacja pracy pracowników w przedsiębiorstwie. Kompletacja złożonego zamówienia powinna odbywać się na zasadzie współpracy poszczególnych stref funkcjonalnych magazynu. W praktyce oznacza to, że jedna osoba powinna mieć wyznaczony obszar swojego działania, kompletując częściowe zamówienia do kilku klientów. Finalnie po dokonaniu procesów konsolidacji i konfekcji towar może opuścić magazyn przy sprawnej kooperacji kilku osób i/lub urządzeń. Wykluczamy w ten sposób kompletację zamówienia przez jednego pracownika, który sam, poruszając się w obrębie kilku stref, będzie zdecydowanie mniej efektywny.
Prawidłowo dobrany i zdefiniowany system informatyczny przeznaczony do zarządzania magazynem może w dużym stopniu poprawić wydajność kompletacji. Obecnie dostępne moduły programów WMS-a są w stanie analizować dane historyczne praktycznie wszystkich ruchów magazynowych. Analiza dostarcza informacji dotyczących rotacji towaru i przydzielenia mu optymalnego miejsca do składowania. Asortyment najszybciej rotujący umiejscowiony będzie w lokalizacjach o lepszej dostępności czy mniejszej odległości od stref pakowania i konsolidacji, co przy większej skali przyczyni się do skrócenia czasu kompletacji zamówień.
Usprawnienie procesu kompletacji jest również możliwe poprzez zastosowanie systemów nazywanych „pick-by”. Przykładowo rozwiązanie pick by light polega na zainstalowaniu w systemie regałowym specjalnych modułów przy danym asortymencie. W momencie kompletacji, na module przypisanym do towaru, który widnieje na zamówieniu, zapala się dioda ułatwiająca jego lokalizację. Z kolei system pick by point polega na podświetleniu poszukiwanego asortymentu przy pomocy reflektora umiejscowionego nad danym korytarzem roboczym. Technologia ta pozwala przede wszystkim na sprawne wdrożenie nowych pracowników do poszczególnych stref magazynu, co przekłada się na zwiększenie wydajności procesów kompletacyjnych.
WDX posiada w ofercie cały asortyment produktów i rozwiązań usprawniających proces kompletacji. Należy do nich zaliczyć również system Quickpick Remote® współpracujący z wózkami widłowymi marki Crown. Technologia ta na nowo definiuje proces kompletacji, automatyzując i upraszczając kluczowe procesy robocze za pomocą pilota wbudowanego w rękawicę sterującą. Dzięki QuickPick Remote® operator przy pomocy rękawicy może kierować wózkiem na odległość.
W rezultacie pracownik wykonuje mniejszą liczbę czynności, a wydajność pracy wzrasta. Kolejnym interesującym rozwiązaniem jest zastosowanie spiralnego przenośnika grawitacyjnego usprawniającego transport skompletowanych zamówień np. z pięter podestów wielopoziomowych. System ten nie wymaga automatyzacji ani wdrażania złożonych modułów informatycznych, a przy niewielkich kosztach potrafi zwiększyć efektywność kompletacji zamówień.