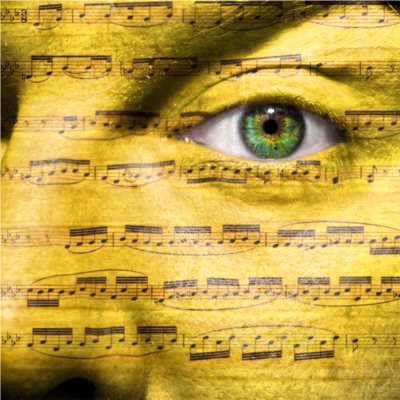
Produkcja jak z nut
Zawsze lubiłem wsłuchiwać się w rytm produkcji. W dźwięki dobiegające z hali produkcyjnej, wydobywane przez pracujące maszyny. Dźwięki ciężkie, metaliczne i te lekkie, melodyjne towarzyszące liniom produkcyjnym niczym nieco inny wymiar orkiestry symfonicznej, grającej bez...
W świecie metalowych maszyn, rozgrzanych pieców, przemieszczających się produktów po liniach produkcyjnych zapis nutowy zastępowany jest przez harmonogram produkcji. Każda maszyna, każdy człowiek powinny mieć rozpisane nuty na swój instrument, czyli na specjalizowane partie (dzienne karty pracy) dostosowane do swoich możliwości zasobu produkcyjnego. O tym, w jakim tempie i co zagrają, decyduje planista, czyli odpowiednik kompozytora koncentrującego się na efektywnym wykorzystaniu dostępnego potencjału zasobów.
Harmonogram ma wiele twarzy
Szczegółowy harmonogram produkcji w praktyce to „tylko” plan i „aż” plan. Bazuje on na dostępnych zasobach własnych i podwykonawców działających w ramach łańcucha dostaw. O tym, jakiej harmonogram jest jakości i na ile jego realizacja jest prawdopodobna, decyduje wiele czynników, wśród najważniejszych możemy wymienić kulturę i dojrzałość organizacyjną przedsiębiorstwa, know-how w zakresie harmonogramowania i planowania produkcji, dostępne narzędzia informatyczne i informacyjne, poprawność danych planistycznych, stan techniczny gniazd/maszyn/narzędzi oraz wiedzę na temat realizowanych procesów produkcyjnych.
Harmonogram może doskonale ukrywać marnotrawstwo, ułomności organizacyjne, kiepskie dane planistyczne, złe wykorzystanie zasobów ludzkich, maszynowych, narzędzi i aparatury kontrolno-pomiarowej. Jest niewiele wart, jeżeli nie jest na bieżąco zasilany danymi zwrotnymi z produkcji. Aby harmonogram odzwierciedlał rzeczywistość i był potężnym narzędziem w walce o jak najlepsze wykorzystanie zasobów, musi być na bieżąco (najlepiej on-line) zasilany informacjami o realizacji operacji technologicznych i przezbrojeniach, planowanych i nieplanowanych postojach, absencjach pracowników, braku dostępności materiałów i półproduktów do produkcji, opóźnieniach w ramach obsługi łańcucha dostaw, itp. Jego mała szczegółowość spowoduje, że nie będzie on odzwierciedleniem rzeczywistości produkcyjnej. W takim przypadku o kolejności wykonywanych zadań decyduje nie harmonogram, ale mistrz, brygadzista, a często sam szef produkcji.
Największą wadą stosowania harmonogramowania wstecz jest tworzenie „dziur czasowych” w harmonogramie
Brak specjalizowanych narzędzi informatycznych wywołuje konieczność stosowania uproszczeń i jest najczęstszym powodem wykorzystywania najbardziej ulubionego narzędzia do planowania produkcji w naszym kraju, „króla wszystkich króli”, jego wysokości: MS Excel’a. Intencją tego artykułu nie jest jednak próba zmuszenia do rozwodu czytelnika z MS Excel. Czasami po prostu warto spojrzeć inaczej, przez pryzmat korzyści i szans, na swoje procesy w firmie, bowiem w świecie harmonogramowania istnieją bardziej doskonałe narzędzia niż MS Excel.
Poszukiwany kompozytor
Planista ze względu na rolę, jaką pełni (m.in. posiada potencjał dużego wpływu na produktywność i rentowność organizacji), powinien być wysokiej klasy fachowcem, doskonale rozumiejącym wady i zalety systemów harmonogramowania. Powinien posiadać wiedzę na temat realizacji procesów produkcyjnych i ściśle współpracować z działami, które mogą w sposób znaczący zaburzać jego pracę np. dział konstrukcyjny, technologiczny, dział zakupów, produkcja itp. Podobnie jak kompozytor ma znać się na swoich nutach i przewidywać powstałe konsekwencje, kiedy niektóre instrumenty przestaną grać.
Początki wsparcia planowania
Skoncentrujmy się jednak na najlepszych praktykach biznesowych, czasami spektakularnych, których skuteczność została udowodniona w praktyce, pomimo że koncepcje te czasami stoją do siebie w silnej opozycji – niczym pies z kotem. Harmonogramowanie nie dotyczy tylko i wyłącznie wątku najlepszego wykorzystania zasobów produkcyjnych, ale również planowania dostępności materiałów, półproduktów w konkretnym czasie pod konkretną maszynę czy gniazdo produkcyjne. Wątek planowania materiałów i zasobów produkcyjnych jest często strategią kolizyjną, ale ten temat podejmę później.
Harmonogramowanie w najczystszej postaci z definicji jest procesem pchającym. Obsługa procesów ssących wymaga innych algorytmów lub narzędzi do zarządzania. Aby można było zbudować dowolny harmonogram, potrzebujemy informacji źródłowych o sposobie zaspokojenia popytu rynkowego. Pierwsze algorytmy zaspokajania popytu wywodzą się z lat 50-tych XX wieku, kiedy prym wiodła produkcja masowa. Algorytmy te obsługiwały model produkcji na magazyn czyli MTS (ang. Make to Stock) i były wspierane systemami komputerowymi klasy MRP (ang. Material Requirement Planning). Informacje o popycie wprowadzało się do planu głównego podając numer pozycji produkowanej, ilość i datę (najczęściej tydzień) realizacji. W standardzie wykorzystywano do tego celu algorytm zamkniętej pętli MRP z kierunkiem harmonogramowania wstecz. Efektem pracy algorytmu MRP była propozycja zakupu materiałów i propozycja zleceń produkcyjnych. Wymagane daty były obliczane w taki sposób, aby określić najpóźniejszą datę uruchomienia produkcji/zakupu materiałów. W praktyce algorytm harmonogramowania wstecz generował szereg niebezpieczeństw. Na przykład systemy ERP/MRP generowały daty wsteczne uruchomienia zleceń produkcyjnych i zakupu materiałów, o których informowały w tzw. komunikatach MRP (komunikatach wyjątku), nie określając przy tym realności wykonania takiego harmonogramu, a wobec braku wehikułu czasu systemy powodowały dużą nierealność generowanych harmonogramów.
Nieprecyzyjne dane
Bardzo dużą bolączką systemów harmonogramowania opartych na uniwersalnej jednostce, jaką jest czas, jest założenie posiadania precyzyjnych danych, brak odzwierciedlenia czasów innych niż czas operacji technologicznej i czas przezbrojenia. Oczywiście nie dotyczy to wszystkich systemów, ale konsekwencje są takie, że nie odzwierciedlane są czasy przesunięć materiałów i półproduktów z jednego obiektu (dział/gniazdo produkcyjne/podwykonawca) na drugi. Nie uwzględniane są także równoległości operacje (standard preferuje sekwencje). W przypadku linii produkcyjnych obrabiany materiał czy detal płynie wzdłuż linii i jest sukcesywnie uszlachetniany. Nie jest transportowany w partiach, lecz w ilościach mniejszych, np. jednej sztuki przekazywanej dalej.
Planista podobnie jak kompozytor ma się znać na swoich nutach i znać konsekwencje, kiedy niektóre instrumenty przestaną grać
W sposób specjalny należy podejść do operacji rozkrojów blach, płyt wiórowych, PCV, materiałów tekstylnych itp. Rozkrój to operacje semi-równoległe realizowane najczęściej w ramach zagregowanych zleceń nadrzędnych.
Szczegółów wpływających na optymalność pracy algorytmu jest dużo więcej, np.: minimalna i maksymalna wielkość partii produkcyjnej i zakupowej (w końcu w dobie produkcji masowej produkowaliśmy głównie w partiach), jak również informacje o strukturach produktów (BOM), marszrutach (kartach technologicznych), recepturach (w produkcji procesowej), dostępnych i dopuszczonych do stosowania wersjach i wariantach struktur i marszrut oraz czasach ich obowiązywania, dopuszczonych zamiennikach czy możliwych odstępstwach. Algorytm MRP, aby przetwarzał dane w ściśle określonych horyzontach czasowych, wymagał definicji grodzi planowania i popytu.
Dodatkowo, naleciałości z produkcji w modelu MTS zaowocowały ogólną anonimowością zleceń produkcyjnych, tzn. informacja o popycie pochodząca z obiektu nadrzędnego dotyczy tylko obiektu podrzędnego i tak poziom po poziomie w dół struktury. Oznacza to, że powiązanie zlecenia sprzedaży (popyt klienta) zawarte jest tylko na zleceniu produkcyjnym na poziomie zero. Cała reszta nie jest wprost powiązana ze zleceniem sprzedaży, co oznacza wspomnianą wyżej anonimowość zleceń.
Największą wadą stosowania harmonogramowania wstecz jest tworzenie „dziur czasowych” w harmonogramie. Dziur tych nie tworzy harmonogramowanie wykorzystujące kierunek w przód, idealnie nadające się do produkcji na magazyn. Zadaniem jego jest określenie najszybszej daty, w której system wyprodukuje wyroby.
„Pierwsze wstecz, drugie w przód”
Producenci oprogramowania w celu śledzenia realizacji zlecenia sprzedaży konkretnego klienta wymyślili nową formą sterowania popytu CTO (ang. Configure to Order – konfiguracja na zamówienie). Strategia ta rozwiązała szereg problemów i odpowiednio wdrożona potrafi generować realne korzyści biznesowe.
W krajowych realiach jest bardzo dużo przedsiębiorstw, które produkują na zamówienie klienta, wykorzystując strategię MTO (ang. Make to Order). Dla potrzeb zaspokajania popytu w ramach strategii MTO wykorzystuje się kierunek harmonogramowania wstecz. Aby uniknąć problemów opisanych powyżej, dla celów potwierdzenia daty realizacji zamówienia klienta i potwierdzenia daty produkcji, niektórzy producenci oprogramowania ERP wprowadzili osobny kierunek harmonogramowania „pierwsze wstecz, drugie w przód”. W przypadku pojawienia się dat wstecznych, algorytm automatycznie w kalkulacji propozycji zleceń produkcyjnych i zapotrzebowania zakupu przełącza się z kierunku wstecz na kierunek w przód, z pełnymi tego konsekwencjami. Te konsekwencje to m.in. wymuszenie innej – niż oczekiwana przez klienta – daty realizacji zamówienia klienta.
Zarówno kierunek harmonogramowania wstecz, jaki i „pierwsze wstecz, drugie w przód” mają kilka innych poważnych wad. Jeżeli nasz harmonogram produkcji w 100 procentach ma odzwierciedlać zamówienia klienta, produkcja będzie raz przeciążona, drugi raz niedociążona, a to jest bardzo kosztowne. Zauważyli to praktycy w Toyota Motors. Ale o tym w kolejnym artykule.