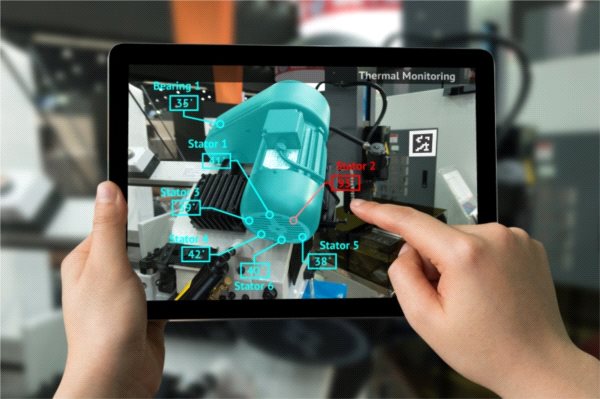
Przemysł 4.0 i jego genetyka
Obserwując i analizując spotkania techniczne czy też konferencje można jednoznacznie powiedzieć, że w świadomości inżynierów oraz menadżerów, zagościło na stałe pojęcie czwartej rewolucji przemysłowej. Jednak bardzo często format tej rewolucji jest sprowadzany tylko do...
Mówi się, że czwarta rewolucja to fabryki przyszłości – inteligentne fabryki. Niestety często na drugi plan przesuwane są pozostałe aspekty rodzących się zmian. A te są bardzo ważne, ponieważ bez ich udziału nie będzie fabryki jutra. Aby zrozumieć czwartą rewolucję należy spojrzeć na wszystkie możliwe wymiary i zrozumieć, że jest to zmiana której nie jesteśmy w stanie ominąć. Chcąc czy nie chcąc będziemy a nawet już jesteśmy czynnymi aktorami w tym procesie.
Wymiary nadchodzących czy też już implementowanych zmian
Zmiany o których się mówi przy okazji czwartej rewolucji to głównie zmiany spowodowane cyfryzacją i wszelką możliwą automatyzacją. Oczywiście to je można uważać, za paliwo do zmian. Jednak biorąc pod uwagę wszystkie wymiary, cyfryzacja i automatyzacja to tylko odpowiedź na coraz większe oczekiwania wynikające ze zmian społecznych i prawnych. Zmiany prawne są czynnikiem, który nadaje tempo w określonych gałęziach gospodarki, jak przemysł farmaceutyczny czy tytoniowy. Ustawodawca wprowadzając określone przepisy narzuca potrzebę implementacji nowych rozwiązań (więcej szczegółów poniżej). Ale i inne gałęzie gospodarki też mają swoich prekursorów. W pierwszym kroku należy zaznaczyć, że czwarta rewolucja została zapoczątkowana poprzez zmiany w nas samych – to my jesteśmy tymi inspiratorami. Wykształcenie, zmiana stylu życia, migracja ludności do miast (budowa „technopolii”), media społecznościowe czy też łatwy dostęp do internetu, to one są odpowiedzialne za rozwój. Można wręcz powiedzieć, iż te zmiany powinny zostać paradoksalnie zdefiniowane jako trójwymiarowa przestrzeń. Te wymiary to: Inteligentna fabryka (Smart Factory), Cyfryzacja (Digital Thread), Zarządzanie łańcuchem wartości (Value Chain Management).
Technopolie – okręgi przemysłowe, w których podstawowym budulcem jest wiedza i innowacyjność. To w nich koncentrują się parki technologiczne i parki naukowe. Powstały one podczas trzeciej rewolucji, ale swój rozkwit zawdzięczają czwartej rewolucji. Zyskują na znaczeniu, ponieważ są to obszary o dużej rentowności oraz mają wysoko wykwalifikowane społeczeństwo a także duże nakłady na rozwój i innowacyjność.
Oczywiście nowoczesne przedsiębiorstwo powinno działać i odnajdywać się w tych trzech wymiarach. Jest to bardzo trudne i wymaga w pierwszej kolejności przygotowania odpowiedniego planu działania. Jego przygotowanie jest znaczącym wyzwaniem. To w pierwszej kolejności praca na dużej ilości danych, następnie modelowanie wielu procesów biznesowych czy też produkcyjnych, a na końcu gwarancja, że wszelkie działania celują w szybką i spójną dostawę rozwiązania do klienta. Bardzo ważnym czynnikiem jest też sprzężenie zwrotne czyli informacja, opinia klienta o produkcie czy rozwiązaniu.
W trakcie przygotowywania odpowiedniego modelu warto pamiętać, że te trzy wymiary odnoszą się do zagadnień:
- inżynierii (projektowanie, technologia wytwarzania),
- zarządzania przedsiębiorstwem (operacje wytwarzania, optymalizacja i wydajność),
- aranżacji i optymalizacji łańcucha dostaw (zarządzanie dostawami, rejestracja parametrów, ciągła informacja dla klienta),
- gromadzenia i przetwarzania ogromnych ilości danych (marketing/ analiza biznesowa produktu, algorytmy uczące się, ocena ryzyka i bezpieczeństwa, zdefiniowanie potrzeb i oczekiwań klienta),
- budowy wartości produktu czy też odpowiedniej opinii o rozwiązaniu, marce, usłudze.
Obrazując to w formie wytwarzanego produktu – dobry plan zbudowany w trzech wymiarach, określa, jak produkt zostanie dostarczony do klienta w sposób spójny tzn. jest właściwie zaprojektowany, zbudowany, przetestowany, zapakowany i dostarczony na czas, a klient na końcu może wyrazić swoją opinię o nim i zagwarantuje nam dalszy rozwój.
Inteligentna fabryka – jeden z wymiarów
Fabryka przyszłości, czyli tak naprawdę smart factory, to miejsce, gdzie podstawowym i najważniejszym zagadnieniem jest łączenie zasobów sprzętowych (urządzenia wytwórcze, roboty) z personelem (kadry zarządzające oraz produkcyjne) w celu pozyskania danych produkcyjnych w czasie rzeczywistym. To łączenie jest możliwe dzięki zautomatyzowanym metodą zbierania i archiwizacji danych i ich analizie. Wykorzystanie wszystkich wypracowanych wyników prowadzi do:
- zapewnienia pełnej widoczności procesów produkcyjnych w czasie rzeczywistym,
- optymalizacji i kontroli procesów produkcyjnych,
- ciągłego nadzoru nad wytwarzanym produktem – jego jakości oraz rejestracji wszelkich parametrów wytwarzania,
- wskazania miejsc w których można jeszcze poprawić wydajność – określenie tzw. wąskich gardeł produkcji,
- pełnego zdalnego (samoczynnego) zarządzania maszynami i dzięki temu: optymalizacji zużycia mediów, a także minimalizacji przestojów i mikro stopów, uruchomienia konserwacji prewencyjnej.
Nim jednak w szczegółach zostaną zdefiniowane parametry fabryki przyszłości warto jeszcze zastanowić się jakim typem jest dana fabryka. W ostatnich latach pojawiła się ciekawa koncepcja ich klasyfikacji. W dokumencie „Industry 4.0 – how to navigate digitization of the manufacturing sector”, autor (McKinsey) na podstawie „map kompasu cyfrowego dla przemysłu 4.0” i zdefiniowanych 8 głównych czynników, wartości określa trzy podstawowe archetypy fabryk przyszłości (rys. 1):
- Smart automated plants (zakłady produkcyjne o wysokim stopniu automatyzacji i robotyzacji): fabryki, które odpowiadają na zapotrzebowanie na produkty masowe, wytwarzane po niskich kosztach, na liniach produkcyjnych w pełni zautomatyzowanych o wysokim stopniu cyfryzacji oraz wysokiej opłacalności.
- Customer-centric plants address trend markets (zakłady produkcyjne zorientowane na klienta – pełna personalizacja produktu): to zakłady mogące w krótkim czasie się przezbroić/ dopasować do określonych oczekiwań klienta (Ultra – responsywność). Fabryki produkujące wysoce zindywidualizowane produkty na dużą skalę i po przystępnych cenach, aby sprostać trendowi masowej personalizacji. Zautomatyzowana produkcja krótko seryjna.
- E-plant in a box (mobilny zakład produkcyjny): mobilność to słowo jednoznacznie określa rodzaj tej fabryki. Jest to zakład, który może być przenoszony z miejsca w miejsce w zależności od dostępu do surowca czy też rynku zbytu. Zakład, który w krótkim czasie jest w stanie wyprodukować określoną ilość produktów w danej lokalizacji.
Oczywiście powyższy model nie wyczerpuje wszystkich możliwych typów fabryk, jednak powyższą definicję należy traktować jako wzór. Co najważniejsze, ten podział wynika z funkcji skali produkcji względem kosztów produkcji i personalizacji. Pomimo tych rozgraniczeń, nowoczesna fabryka bez względu na typ bazuje zawsze na podwalinach – tzw. pryncypiach. Do nich należy zaliczyć:
- rozwój kompetencji pracowników na każdym szczeblu zakładu,
- optymalizacja czyli podnoszenie wydajności, ciągłe doskonalenie zdolności operacyjnej,
- cyfryzacja, rozwój infrastruktury cyfrowej z zachowaniem pełnego bezpieczeństwa procesów,
- polityka bezpieczeństwa w zakresie zagrożeń działaniami cyberprzestępców.
Wracając do definicji wymiarów inteligentnej fabryki, warto ją przedstawić jako następujące po sobie połączone procesy i systemy, które bazując na urządzeniach i zarejestrowanych parametrach, przechodzą do wyższych poziomów, czyli kontroli procesu, agregacji, analizy i interpretacji danych oraz ich archiwizacji w celu późniejszego przetwarzania. Ciekawym przedstawieniem fabryki jutra jest jej ukazanie na bazie dobrze znanego modelu, standardu ISA-95, który – pomimo stworzenia podczas trwania trzeciej rewolucji i wielu lat obecności w świadomości inżynierów czy menadżerów – jest wciąż aktualny.(Rys 2)
BI – Analiza i Raportowanie danych. Warstwa która jest grupowana jako strefa BIG DATA. W którym są definiowane modele biznesowe. Czas dostępności i operacji na danych można definiować w minutach.
ERP – planowanie produkcji/ logistyka. Zarządzanie przedsiębiorstwem. Analiza i raportowanie realizacji zleceń. Czas obróbki danych mierzony w minutach.
MES – Tworzenie i zarządzanie recepturami, Zarządzanie produkcją i procesami. Mierniki wydajności, analiza dostępności, liczenie KPI, OEE. Czas przetwarzania danych mierzony w sekundach.
SCADA – (warstwa IoT) Systemy sterowania linią produkcyjną, rejestracja parametrów produkcji. Agregacja danych produkcyjnych. Czas przetwarzania danych 1/10 sekundy.
IIoT– inteligentne urządzenia wykonawcze, czujniki, odczyt i udostępnienie parametrów. Czas dostępu do danych 1/100 sekundy.
Jak widać na przedstawionym schemacie nowoczesna fabryka to organizm działający na wielu płaszczyznach i udostępniający dane dla określonych grup pracowników począwszy od operatorów i technologów a skończywszy na osobach decydujących o strategii rozwoju przedsiębiorstwa.
Bazą tej piramidy, są fizyczne „obiekty” do których należy zaliczyć w pierwszej kolejności pracowników liniowych a następnie inteligentne maszyny, czujniki, narzędzia. To miejsce gdzie pracownicy i maszyny współdziałają ze sobą za pośrednictwem strukturalnej komunikacji i zintegrowanych systemów dostarczających w czasie rzeczywistym dane o ich stanie i procesach, które aktualnie wykonują. Na tej warstwie skrót IIoT mówi o łatwości łączenia sprzętu z obszarem odpowiedzialnym za akwizycję danych i ich analizę z wykorzystaniem usług pracujących w chmurze (CLOUD, BIG DATA).
Wydobyte w ten sposób dane są dokładniejsze, bardziej spójne, niemal w czasie rzeczywistym (częstotliwość pracy czujników jest obecnie mierzona w jednostkach 1/100 a nawet 1/1000 sekundy) i pozwalają organizacjom szybciej wykryć nieefektywność i problemy, oszczędzając czas i pieniądze. A zespół analityków czy też menadżerów, jest w stanie podjąć mądrzejsze i szybsze decyzje biznesowe. Jest to w szczególności ważne dla firm przemysłowych.
Głównym problemem spowalniającym implementację IIoT w istniejących zakładach produkcyjnych jest sprzęg nowych technologii ze starszymi urządzeniami i maszynami w szczególności tymi korzystającymi z różnych protokołów i różnych architektur systemowych. W przeciwieństwie do automatyzacji osiągniętej w ciągu ostatnich kilku dziesięcioleci, obecne metody łączności ukierunkowane na IIoT i Smart Manufacturing muszą być otwarte, oparte na ustandaryzowanych protokołach komunikacyjnych i zdolne do publikowania zarejestrowanych wartości w Internecie czy też Intranecie.
Kolejne poziomy piramidy służą do sterowania procesami, są magistralami komunikacyjnymi – pomiędzy Operations Technology (OT) – wymieniającymi dane bezpośrednio z maszynami i narzędziami oraz systemami i aplikacjami IT (IT). Dodatkowo coraz częściej w tych warstwach znajdują się aplikacje, w których „interfejs personelu” oprócz wykonywania nadzoru nad produkcją może rejestrować procesy inspekcyjne czy też kontrolne a także uruchamiać zadania naprawcze i konserwacyjne, prewencyjne – zapobiegające ewentualnym awarią.
Ostatni poziom piramidy to Systemy Business Intelligence. Służą one do agregacji danych i odpowiadają za organizację danych w praktyczne wskaźniki, jak wskaźniki wydajności (KPI), produktywności, które reprezentują strategiczne cele przedsiębiorstwa. W połączonej cyfrowo organizacji (Smart Manufacturing) osoby zarządzające są automatycznie powiadamiane o miejscach, które nie działają zgodnie z planami i oczekiwaniami. Dyrekcja w nowoczesnym zakładzie musi mieć dostęp do podstawowych wartości produkcyjnych, tak aby płynnie móc przeprowadzić analizę przyczyn, a w zależności od funkcji analitycznych systemu BI móc otrzymać sugestie lub wskazanie obszarów wymagających poprawy. Jak widać wszystkie poziomy są ważne dla organizacji i tylko ich właściwe działanie gwarantuje sukces. Dlatego najważniejszym elementem dobrego planu jest odpowiednie przygotowanie definicji i właściwe wdrożenie interfejsów wymiany danych. Prawidłowa komunikacja jest kluczem do sukcesu nowoczesnego zakładu.
Nowoczesny zakład produkcyjny a klient końcowy
Oczywiście inteligentne systemy rejestracji parametrów i procesów, oprócz funkcji związanych ze zwiększaniem wydajności czy optymalizacją kosztów, mogą, a w zasadzie są w stanie udostępnić dane związane z procesem wytwarzania. Tak naprawdę oznacza to, że klient końcowy, może otrzymać informacje o produkcie – o parametrach procesów – jakim był poddawany. Może również sprawdzić jego autentyczność. W nawiązaniu do początku opracowania należy w tym miejscu wspomnieć, że są dziedziny przemysłu, które muszą jednoznacznie informować odbiorcę o jakości i autentyczności swojego produktu. Nowe wprowadzane obecnie prawa, jak na przykład dyrektywa fałszywkowa, nakładają na producenta obowiązek wprowadzania inteligentnych rozwiązań z grupy IIoT. Tak naprawdę dzięki takim poczynaniom ustawodawcy, są zakłady, które muszą w najbliższym czasie zaimplementować systemy znakowania jednostkowego i rejestracji, agregacji danych. Co prawda nie są to stricte rozwiązania umożliwiające płynną analizę procesu produkcyjnego, ale jednak są rozwiązaniami, które udostępniają bardzo dużą ilość informacji. Te dane mogą być – przy odpowiednim poszerzeniu inwestycji – kluczowe w zakresie analizy wydajności czy efektywności produkcji.
W przypadku farmacji, wspomniana dyrektywa nakłada obowiązek serializacji każdego opakowania leku i raportowanie jego wyprodukowania, do serwerów dostępnych w chmurze (CLOUD). Ten typ rozwiązania w rzeczywistości swoją architekturą, jest bardzo zbliżony do rozwiązań klasy smart factory. Na dzień dzisiejszy, każdy producent, postrzega te oczekiwania jako konieczność wydania określonej , niemałej sumy pieniędzy, jednak przy odpowiednim zamodelowaniu – zaplanowaniu wdrożenia, może pozyskać bardzo dużą ilość danych. A te dane, przy odpowiedniej analizie, udostępnią unikalną wiedzę w zakresie miejsc, które mają niską wydajność czy też generują znaczące straty.
Inne wymiary czwartej rewolucji
Obecny kierunek rozwoju zakładów produkcyjnych jest ustawiony na pozyskiwanie maksymalnej ilości danych o procesie produkcyjnym czy o samym produkcie (Cyfryzacja). Ta sytuacja jak widać jest wynikiem oczekiwań klienta (Zarządzanie Łańcuchem wartości) jak i wprowadzania nowych przepisów. Te dwie definicje to kolejne dwa wymiary umożliwiające określenie przestrzeni i kierunku rozwoju czwartej rewolucji przemysłowej. Aby móc powiedzieć o pełnym zrozumieniu zmian i przygotować się do opracowania odpowiedniego planu działania, należy bardzo dokładnie przeprowadzić analizę tych wymiarów. Następne części cyklu opowiedzą na co zwrócić uwagę w tym procesie oraz jak go wykonać.