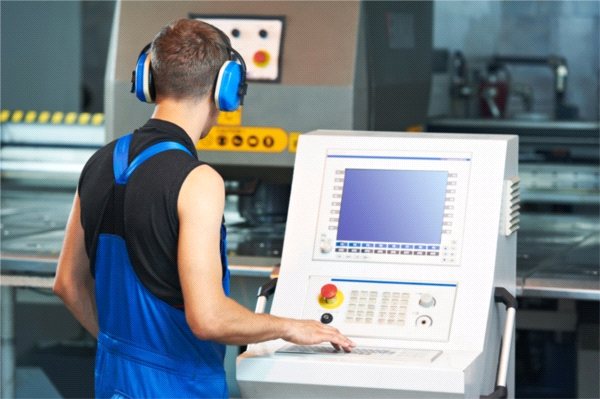
Przewidzieć awarię
Postrzeganie istnienia utrzymania ruchu jako "zła koniecznego" przestaje być standardowym modelem postępowania producentów. Nowocześnie zarządzane przedsiębiorstwa coraz częściej traktują ten dział jako strategiczny element biznesu, którego sprawne funkcjonowanie pozwala nie...
Strategie typu „używaj aż się nie zepsuje” czy „naprawiaj w każdym przypadku” odchodzą do przeszłości. Zaawansowane rozwiązania predyktywnego utrzymania ruchu pozwalają producentom usprawniać operacje, wykorzystując dane na temat stanu zasobów, przewidywać nadchodzące awarie i planować czynności serwisowe tylko w okresach, gdy są one niezbędne. Producenci legitymujący się wysokim poziomem doskonałości operacyjnej notują czasy przestoju o 5% krótsze niż średnia w przemyśle, zaś wzrost OEE sięga 8%. Agencja konsultingowa Roland Berger Strategy Consultans przyjrzała się ewolucji metodologii predyktywnego utrzymania ruchu i problemom, na jakie menedżerowie natrafiają podczas wdrożeń.
Ograniczone możliwości monitoringu
Aktualnie producenci stosują szereg rozwiązań, pozwalających na monitoring stanu ich zasobów. Badają one jeden lub kilka parametrów, takich jak wibracje, zużycie oleju, temperatura itp. Odczyty są wykorzystywane do zidentyfikowania potencjalnych problemów. Przykładowo analiza wibracji pozwala na wykrycie często spotykanych awarii mechanicznych, jak luźne łożyska, zużycie komponentów czy niewspółosiowość wałów.
Ponieważ jednak wiele rozwiązań monitoringu skupia się na jednym lub dwóch typach danych dyskretnych, ich zdolność do detekcji kompletnego spektrum potencjalnych awarii jest ograniczona. Co więcej, systemy monitoringu często nie są w stanie zdiagnozować przyczyny już wykrytej usterki, ani określić jak szybko należy wykonać działania zapobiegające nadchodzącym problemem. Otrzymujemy tylko informację, iż dane nie mieszczą się w określonych granicach.
Alarm ostrzegający o potencjalnym problemie na kluczowej maszynie nie jest zbyt pomocny, jeśli inżynierowie nie dostają informacji o wadze tego problemu. O wiele bardziej użyteczna jest funkcjonalność wskazująca przyczyny usterki i czas, w jakim może się ona pogłębić. Na przykład w przypadku szlifierki będzie to informacja, że silnik wrzeciona jest zużyty i jeżeli nie zostanie wymieniony w ciągu tygodnia, prawdopodobieństwo awarii wynosi 90%. Tutaj kryje się potencjał zwiększenia wartości dodanej tych rozwiązań.
Czym różnią się rozwiązania?
W ostatnich latach zaawansowane rozwiązania dla predyktywnego utrzymania ruchu zostały rozwinięte i zaadaptowane w takich branżach jak wydobywcza, obsługa turbin wiatrowych czy przemysł kosmiczny. Wykorzystują one dane z różnych źródeł i wykorzystują analityczne techniki modelowania w celu generowania prognoz.
Bazując na danych departamentu energii USA, implementacja programów predyktywnego utrzymania ruchu w tej branży zaowocowała 10-krotnym zwrotem inwestycji. Zanotowano spadek wydatków na utrzymanie ruchu o 25-30 proc, liczba awarii zmniejszyła się o 70-75 proc, przestoje skróciły się o 35 do 45 proc, zaś produkcja wzrosła o 20 do 25 proc.
Case study
1. Branża naftowa
Wysokie koszty, krytyczne znaczenie dla gospodarki oraz trudny dostęp do surowców sprawia, że branża naftowa stała się idealnym polem do adaptacji rozwiązań predyktywnego utrzymania ruchu. W razie wystąpienia nieprzewidzianych awarii, konsekwencje ekonomiczne, ekologiczne oraz zagrożenie bezpieczeństwa mogą być ogromne. Wydajne zarządzanie maszynami, przy zapewnieniu bezpiecznej i stałej produkcji, to kluczowy czynnik. Tym samym w branży tej opracowano pierwsze rozwiązania informatyczne, przekazujące dokładne dane.
2. Farmy wiatrowe
Predyktywne utrzymanie ruchu dało znakomite efekty przy monitoringu pracy farm wiatrowych. Odległa lokalizacja i trudny dostęp po turbin wiatrowych w połączeniu z trudnymi warunkami pogodowymi w których one pracują, skutkowały wysokimi kosztami operacyjnymi i utrzymania. W ciągu kilka lat sięgają one poziomu 20 proc. kosztu wyprodukowania turbiny. Jeden z operatorów stwierdził, iż stosując system predyktywnego utrzymania ruchu jest w stanie obniżyć całkowite koszty operacyjne o 250 tys. dolarów. Inny po zaimplementowaniu systemu odkrył, że jedna z turbin generuje o wiele mniej mocy. Udało się dotrzeć do przyczyny ten sytuacji – niechcący nałożono na nią ograniczenie wydajności. Rozwiązując ten problem zdołano dodatkowo powiększyć zyski.
Jak skorzysta na tym produkcja?
Najlepsze praktyki, wypracowane w innych sektorach, dadzą sie przenieść na grunt zakładów produkcyjnych. Produkcja ma pod wieloma względami podobną charakterystykę: jest kapitałochłonna, wywiera duży nacisk na redukcję przestojów i kosztów, zaś zatrzymanie procesów może mieć katastrofalne skutki. Sektor ten zmaga się też z dodatkowymi trudnościami. Środki trwałe muszą zapewnić coraz większy zwrot z dokonanych inwestycji, zaczyna też brakować doświadczonych pracowników.
Adaptacja rozwiązań predyktywnego utrzymania ruchu staje się zatem atrakcyjna dla producentów. Pozwalają one na eliminację niepotrzebnych procesów serwisowych, redukcję kosztów wymiany komponentów, skrócenie nieplanowanych przestojów i wydłużenie cyklu życia maszyn. Kombinacja tych zalet pozwala poprawić produktywność i zyski, zaś efekty doceni zarówno zarząd jak i pracownicy UR.
Metodologia ta jest jednak wciąż często pomijana w firmach produkcyjnych. Jakie są tego przyczyny? Na przeszkodzie do szerokiego wdrożenia predyktywnego utrzymania ruchu stoją dwie podstawowe bariery, typowe dla środowiska produkcyjnego: kłopoty z przygotowaniu funkcjonalnych rozwiązań możliwych do zaadaptowania w produkcji oraz niska gotowość sektora produkcyjnego na takie wdrożenia.
Co stoi na drodze do zmiany?
Pierwsza z tych barier wiąże się z wieloma technicznymi wyzwaniami. W większości fabryk pracuje bardzo zróżnicowana gama maszyn. Wiele z nich ma krytyczne znacznie dla utrzymania ciągłości produkcji. Tymczasem, w branży farm wiatrowych, jako krytyczne urządzenia traktowane są tylko turbiny co znacznie ułatwia zadania UR. Często też w fabrykach pracują podobne maszyny ale różnych producentów, wymagające innego sposoby pomiaru ich stanu. Rozwiązania predyktywne muszą być zatem możliwe do zaadaptowania w środowisku charakteryzującym się dużą heterogenicznością zasobów, z czym muszą zmierzyć się dostawcy rozwiązań.
Podobna sytuacja ma miejsce jeśli chodzi funkcjonowanie tej metodologii w wysoce dynamicznym środowisku, jakim są zakłady produkcyjne. Wysoki proces interakcji międzyludzkiej, duża ilość obrabianych materiałów oraz często zmieniające się produkty końcowe to kolejny trudny do rozwiązania problem.
Natomiast jeżeli chodzi gotowość sektora produkcji na wdrożenia rozwiązań predyktywnego utrzymania ruchu, wskazać można kilka powodów jej niskiego poziomu. Nowoczesne maszyny generują coraz większą ilość danych dzięki wbudowanym czujnikom. Dodatkowo pojawiają się nowe standardy gromadzenia informacji, jak MT Connect. Tym samym komplikuje się kwestia zebrania i syntezy niezbędnych dla skutecznego działania PUR informacji.
Brakuje ponadto zaufania personelu działów utrzymania ruchu do tej metody. Z jednej strony niepewność budzi jej realna skuteczność, z drugiej – jeśli PUR będzie się sprawdzać, pracownicy zaczną obawiać się o swoje posady. Konieczność zakupu oprogramowania napotyka z kolei opór zarządów, niechętnych inwestycjom zwracającym się w długim okresie czasu.
Według jednego z pytanych inżynierów UR to właśnie opór kulturowy sprawia największe trudności w rozwoju tej metody. Lecz zdaniem autorów raportu, wskazane przykłady i oczywiste zalety sugerują, że jej szerokie stosowanie w sektorze produkcyjnym jest tylko kwestią czasu.