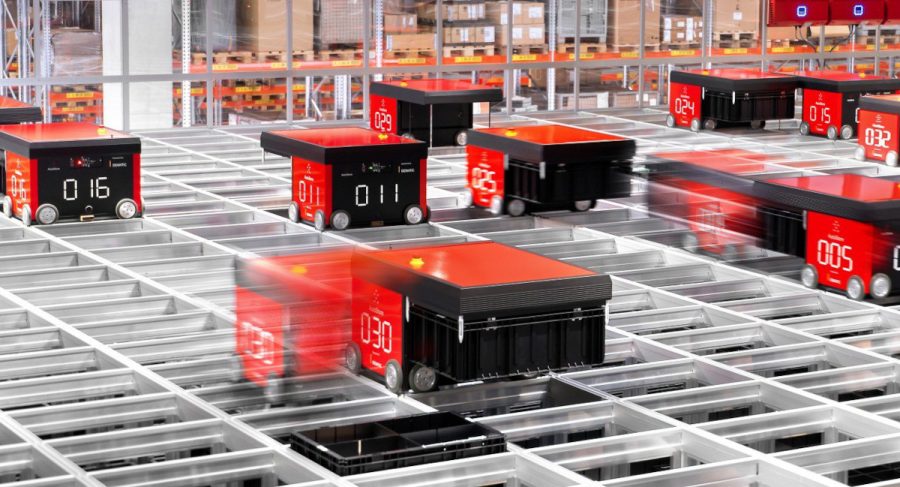
Roboty usprawniają magazynowanie małych ładunków – Case Study
Spójna koncepcja magazynowania z użyciem przenośników, robotów i wózków widłowych może pozwolić zwiększyć gęstość składowania i wydajność kompletacji nawet kilkukrotnie. Przekonano się o tym w ramach kompleksowego wdrożenie w zakładzie Siemens w Chemnitz.
Zakład Siemens w Chemnitz ma długą tradycję projektowania i produkcji maszyn i komponentów. Zakres działalności przedsiębiorstwa obejmuje m.in. inżynierię aplikacji, logistykę materiałową czy montaż wyposażenia elektrycznego oraz inspekcję i wstępny rozruch urządzeń. Wytwarzane są tu zarówno rozdzielnice do obrabiarek, jak i elementy potrzebne w inżynierii ogólnej i mechanicznej. W skali roku w zakładzie prowadzone są projekty, do wykonania których wykorzystuje się niemal 1,3 mln pozycji materiałowych. W efekcie w ciągu 12 miesięcy w Chemnitz powstaje w sumie 46 000 rozdzielnic, podzespołów specjalnych i komponentów elektronicznych dostarczanych następnie klientom na całym świecie.
Wyzwanie
W związku z rosnącym popytem na usługi i produkty firmy magazyn w Chemnitz musiał obsłużyć wolumen ładunków i materiałów większy niż kiedykolwiek wcześniej. Pomimo rozbudowy magazynu paletowego i zewnętrznego, po brzegi wypełniona była przestrzeń przeznaczona na podzespoły niewielkich rozmiarów. Dotychczasowy magazyn kontenerów SLC/KLT z małymi częściami okazał się niewystarczający do zaspokojenia rosnących potrzeb. Celem projektu modernizacyjnego było poprawienie efektywności obsługi małych ładunków, optymalizacja wykorzystania miejsc paletowych i zwiększenie wydajności procesu składowania i transportu wewnętrznego.
Zastosowane rozwiązanie
Pierwszym krokiem do stworzenia systemu intralogistycznego, który sprostałby wymaganiom firmy Siemens, było zebranie szczegółowych danych na temat funkcjonowania magazynu. Informacje te stały się bazą do stworzenia przez dostawcę wielu wariantów projektu. Zostały one następnie ocenione i porównane za pomocą kluczowych wskaźników wydajności pod kątem wymaganej przepustowości i dostępnej powierzchni magazynowej. W toku dyskusji z klientem spośród projektów wyłoniono te najlepiej rokujące – tak, by ostatecznie wybrać jeden, dopracować go i wdrożyć. Wybór padł na rozwiązanie, w którym funkcjonują jednocześnie:
- automatyzacja magazynu małych części w oparciu o technologię AutoStore® firmy Dematic,
- dostarczone przez firmę STILL przenośniki,
- system regałów paletowych na 12 tys. miejsc obsługiwany przez sterowane ręcznie wózki wysokiego składowania STILL FM-X.
– Współpracując z doradcami intralogistycznymi STILL, zdefiniowaliśmy wymagania dotyczące magazynowania i transportu w naszym obiekcie w oparciu o analizę struktury artykułów i zamówień. Pozwoliło nam to przeprojektować przepływy materiałów pod kątem maksymalizacji pojemności magazynu oraz wydajności obsługi ładunków – mówi Carsten Sambo, Head of Inbound Logistics w Siemens i menadżer projektu wdrożenia ze strony klienta. W zmodernizowanym magazynie przepływ towarów rozpoczyna się od przyjęcia ładunków na jeden z dwóch sposobów. Spaletyzowane towary są transportowane na regały magazynowe z użyciem sterowanych ręcznie wózków wysokiego składowania STILL FM-X. Kartony z małymi komponentami trafiają natomiast na przenośniki i windy oraz – za ich pośrednictwem – do pracowników odpowiedzialnych za rozpakowanie paczek, sprawdzenie ich zawartości i umieszczenie komponentów w kontenerach BIN kompatybilnych z systemem AutoStore®. Za sprawą przenośników kontenery trafiają następnie do automatycznego magazynu – gotowe do wysłania, gdy tylko produkcja zgłosi odpowiednie zapotrzebowanie. By dodatkowo usprawnić pracę systemu, zaprogramowano funkcję prognozowania zapotrzebowania następnego dnia. Elementy, które mogą okazać się przydatne, są pobierane i przenoszone przez roboty podczas nocnej zmiany z najniższych poziomów systemu AutoStore® w górny, „wierzchni” obszar jego samonośnej siatki.
Efekt wdrożenia
Wdrożony w Siemens system AutoStore® jest w stanie pomieścić do 45 000 pojemników SLC z ponad 24 000 typami materiałów. W porównaniu ze stosowanym dotychczas systemem ręcznym na tej samej powierzchni można składować nawet czterokrotnie więcej towarów. Z 30 do 75 pozycji na godzinę wzrosła także wydajność kompletacji. Rozwiązanie spełnia cele sformułowane dla projektu przez Siemens.– Dzięki nowemu magazynowi jesteśmy dobrze przygotowani na przyszłość. Konieczność skalowalności rozwiązania uwzględniliśmy już na etapie planowania – relacjonuje Carsten Sambo. – Wdrożona koncepcja pozwoliła w pełni osiągnąć założone cele w zakresie zwiększenia pojemności magazynu, efektywności kompletacji zamówień oraz poprawy wydajności operacji magazynowych w ogóle – podsumowuje.