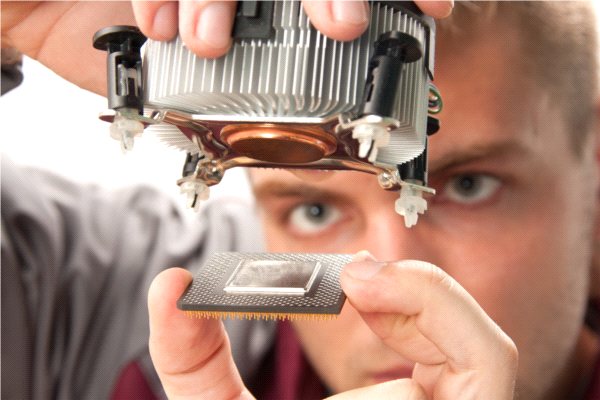
Skrócony cykl życia produktu
Chyba najbardziej dramatycznym wyzwaniem wobec producentów dóbr masowej konsumpcji stał się wymóg produkcji małych partii różnorodnych wyrobów dopaso-wanych do indywidualnych gustów i potrzeb klientów.Działania przedsiębiorstw w konkurencyjnym otoczeniu są uwarunkowane...
Działania przedsiębiorstw w konkurencyjnym otoczeniu są uwarunkowane pojawiającymi się wokół różnorakimi ograniczeniami i wymuszeniami. Umiejętność radzenia sobie z oddziałującymi na przedsiębiorstwo czynnikami zewnętrznymi decyduje o jego przetrwaniu na rynku. Za jeden z najistotniejszych czynników, które obecnie kształtują obraz rynku, należy uznać ogromną różnorodność produktów oraz „szum informacyjny” wywołany niespotykanym wcześniej natężeniem aktywności reklamowej.
Kolejnym czynnikiem decydującym o obliczu dzisiejszego rynku jest rewolucja technologiczna. Jej owocami są nowe elektroniczne kanały dystrybucji i komunikacji, które umożliwiły bezpośredni kontakt z oddalonym klientem, a co za tym idzie, spowodowały globalizację konkurencji.
Odpowiedzią na nowe warunki stał się marketing relacyjny, który umieszcza potrzeby klienta w centrum zainteresowania przedsiębiorstwa. Nowe podejście zakłada konieczność budowania indywidualnych, trwałych kontaktów pomiędzy producentem, dostawcą a klientem. Komunikacja, produkcja i dystrybucja coraz częściej zaczyna mieć charakter indywidualny, ukierunkowany i dopasowany do potrzeb klientów.
Nowe podejście zakłada konieczność budowania indywidualnych, trwałych kontaktów pomiędzy producentem, dostawcą a klientem
Ta elastyczność wcześniej w przedsiębiorstwie produkcyjnym nie występowała, ponieważ tradycyjnie najważniejsza była zazwyczaj produkcja podstawowa, głównie dlatego, że często prezes był poprzednio szefem wydziału produkcyjnego. Czasem najważniejsza była funkcja projektowania, ze względu na fakt, że naczelny był konstruktorem. Postulat podporządkowania struktur i funkcji celom strategicznym był jedynie hasłem, ponieważ i tak bez tego przedsiębiorstwa radziły sobie nieźle w warunkach niezbyt ostrej konkurencji i niewysokich wymagań rynku.
Nowe wymagania i komplikacje
Widoczna od połowy lat 80-tych koncentracja na kliencie i jego potrzebach doprowadziła do wzrostu znaczenia jakości zasobów ludzkich producenta. To już nie mogli być robotnicy bez kwalifikacji, przyuczeni do wykonywania powtarzalnych prostych czynności, pracujący „na ilość” w systemie akordowym.
Wymóg produkcji małych partii wyrobów różnorodnych, dopasowanych do indywidualnych gustów i potrzeb, stał się chyba najbardziej dramatycznym wyzwaniem wobec producentów dóbr masowej konsumpcji. A to powodowało wzrost kosztów przestawiania maszyn i urządzeń oraz wymagało nowych rozwiązań w dziedzinie inżynierii przemysłowej i pokonania narastających komplikacji w planowaniu i sterowaniu produkcją. W związku z tym wzrosło jeszcze bardziej znaczenie uniwersalnego przygotowania robotników. Restrukturyzacja służąca pokonaniu opisanych problemów przebiegała w dwóch kierunkach: integracji funkcji projektowania, planowania, zaopatrzenia i wytwarzania oraz podziału pracy pomiędzy wyspecjalizowanych uczestników rozległych sieci kooperacyjnych.
W większym niż dotąd stopniu koncepcje i konstrukcje produktów musiały uwzględniać ograniczenia narzucane przez organizację produkcji, wzrosło znaczenie unifikacji. Rozpowszechniła się technologia grupowa polegająca na tym, że małe partie podobnych wyrobów grupuje się razem, aby poddawać obróbce produkcyjnej jednorazowo większą ich ilość.
Skracanie czasu realizacji zamówień w połączeniu ze stałym naciskiem na redukcję kosztów doprowadziło do upowszechnienia nowej strategii produkcyjnej: „szczupłej produkcji”. Zastosowanie kanbanu oraz „ciągnące” sterowanie procesem stało się współczesnym standardem przemysłowym w większości sektorów wytwarzających w sposób nieciągły różnorodne produkty.
Śmiało można stwierdzić, że pierwszy etap narodzin współczesnych strategii produkcyjnych doprowadził do głębokich zmian w obszarze systemów sterowania produkcją. Zarządzanie przez jakość, integracja procesów i funkcji, produkcja wsadowa i kanban oraz zdecentralizowane zarządzanie procesami należą dziś do kluczowych warunków sukcesu w warunkach konkurencyjnej gospodarki.
Od końca lat 90-tych byliśmy świadkami następnych zmian, które doprowadziły do narodzin nowego pojmowania elastyczności jako zdolności adaptacji nie tylko do dużych, lecz także do małych zmian dotyczących produktu. Technologia grupowa stosowana do szerokiego asortymentu mało różniących się elementów jest obecnie najbardziej „pożądanym tematem” organizacji produkcji.
Zrównoważone strategie produktowo-rynkowe polegają na wprowadzaniu produktów na rynek w ściśle określonym momencie
Rosnące wymagania w zakresie złożoności produktów wyznaczają drugi kierunek zmian. Wyroby i usługi o wielkim stopniu złożoności są wytwarzane w procesach obejmujących wiele etapów. Jeśli asortyment takich złożonych produktów ma być szeroki, sterowanie kanbanem przestaje być najlepszym rozwiązaniem. Obecnie poszukuje się rozwiązań hybrydowych, czyli optymalnej mieszaniny sterowania „ciągnącego” i „tłoczącego” (pull and push).
Rosnąca złożoność produktów, w szczególności kompletowanych wyrobów i usług, rodzi także potrzebę poszukiwania rozwiązań strukturalnych. Wymóg oszczędności nakazuje, aby elementy były wytwarzane przez wyspecjalizowane zakłady mające niekiedy siedziby w różnych zakątkach globu. Telekomunikacja i elektroniczna transmisja danych umożliwiają szybką komunikację i integrację rozproszonych dostawców, ale powstaje pytanie, w jaki sposób sterować taką produkcją i globalną logistyką, aby zapewnić najbardziej optymalne, wyrównane obciążenie zdolności produkcyjnych, synchronizację dostaw i optymalne wielkości partii? Już samo kompletowanie (montaż) urasta do rangi osobnego zagadnienia, pojawiają się więc nowe rodzaje systemów logistycznych z pośrednimi centrami dystrybucji.
Koniec czy początek drogi?
Z reguły o strategii produkcyjnej zwykło się mówić, że to taka organizacja zasobów, która czyni z produkcji narzędzie do jak najlepszej realizacji strategii korporacyjnej. W klasycznym ujęciu strategię tę można sprowadzić do odpowiedzi na pytanie o spodziewaną zmienność sposobu produkcji (technologii) oraz odpowiedzi na pięć pytań na temat organizacji zasobów dotyczących: lokalizacji zakładu (zakładów), dynamiki inwestycji w zakłady i środki produkcji w różnych horyzontach czasowych, systemu podziału pracy, mechanizacji procesów i operacji, rozplanowania środków produkcji w zakładach (warsztatach).
W dobie globalizacji i rosnącej swobody przepływu zasobów odpowiedź na pięć w/w pytań staje się coraz łatwiejsza, ponieważ inwestorzy mają większą „swobodę manewru”, niż mieli wcześniej. Pojawiły się natomiast problemy strategiczne związane z niektórymi technologiami tzw. high-tech, do których można zaliczyć takie dziedziny, jak biotechnologia (projektowanie oraz przemysłowe wytwarzanie i przebudowa bardzo złożonych makrocząsteczek), sposoby precyzyjnej obróbki i montażu (np. nanotechnologia, montaż powierzchniowy), inżynieria złożonych materiałów (np. kompozytów, odlewów ze stopów), inżynieria systemów i technologie informacyjne. Za najbardziej zaawansowane obecnie uznaje się technologie kosmiczne i lotnicze.
Obecnie część klientów nie może już albo nie chce ponosić kosztów wyścigu technologicznego
Zastosowanie technologii informacyjnych przyczyniło się do podważenia podstawowej zasady biznesowej ugruntowanej na doświadczeniach, według której konkurowanie jest rywalizacją wartości dostarczanych na rynek w postaci produktów (wyrobów i usług), co osiąga się obecnie poprzez zrównoważone strategie produktowo-rynkowe, które polegają na wprowadzaniu nowych produktów na rynek w ściśle określonym momencie: gdy produkty dotychczasowe kończą najlepszy okres swego cyklu „życia”. Inwestycje w opracowanie nowych produktów „mają czas”, aby się zwrócić, a źródłem ich finansowania są głównie zyski z początkowego wysoce przychodowego okresu sprzedaży dotychczasowych produktów.
Wyścig technologiczny wspierany dynamicznie rozwijającym się sektorem technologii informatycznych stał się wyścigiem standardów przemysłowych, a nie produktów. Stało się tak, mimo że światowy biznes już wcześniej odczuł boleśnie, że nie tędy droga (np. zwycięstwo standardu VHS dowiodło, iż to nie technologia wygrywa i nie standard przemysłowy, choćby najlepszy).
Zdecydowanie szybciej zmieniają się uwarunkowania dla całej działalności biznesowej, a szczególnie produkcyjnej, ponieważ odstęp czasu pomiędzy kolejnymi standardami staje się coraz krótszy i jest znacznie krótszy niż cykl użytkowania produktu. Producenci nie mieliby więc szans na uzyskanie zwrotu z inwestycji w nowe standardy przy normalnej eksploatacji produktów przez użytkowników, zastosowali w związku z tym politykę wymuszającą na klientach przedwczesną wymianę sprzętu i oprogramowania. Klienci płacili za wyścig swoich dostawców bez gwarancji uzyskania równoważnych korzyści, a użytkownicy produktów przeznaczonych dla przedsiębiorstw zaczęli w końcu płacić także za niedopasowanie różnych standardów (integrację).
Obecnie część klientów nie może już albo nie chce ponosić kosztów wyścigu technologicznego przynoszącego zbyt często pozorne korzyści. Bezrobocie, które ogarnia wysoko kwalifikowane kadry, to koszty historycznego błędu, które mają wymiar społeczny po raz pierwszy w dziejach świata. Można się spodziewać, że ta nadzwyczajna sytuacja zrodzi nowe strategie korporacyjne i produkcyjne.
Doświadczenia pokazują, że znane wszystkim klasyczne metody doskonalenia procesów wymagają wielu lat, by osiągnąć zakładane efekty biznesowe, w dodatku wiele kosztują. Biorąc pod uwagę rosnącą dynamikę zmian w biznesie mamy już teraz do czynienia z sytuacją, że nasz proces/produkt zakończy prawdopodobnie „cykl życia”, zanim zdążymy udoskonalić go tak, by osiągnąć optymalne efekty.
Rozwój technologi IT umożliwia zastosowanie ciekawych rozwiązań bez potrzeby wykonywania kosztownych eksperymentów na „żywym procesie”. Rozwiązania takie mogą być krokiem milowym w doskonaleniu procesów biznesowych. Przy stosowaniu klasycznej metodyki doskonalenia procesu eksperymenty i testy na „żywym procesie” trwałyby miesiącami/latami i kosztowałyby setki tysięcy, a nawet miliony złotych. Co więcej, testy te tak naprawdę nie optymalizują procesu, a jedynie mniej lub bardziej go usprawniają. Bez wirtualnej interaktywnej symulacji trudno tak naprawdę poznać, jakie są rzeczywiste ograniczenia i rezerwy analizowanego procesu.
Studium przypadku – Sterowanie produkcją w Spółce Saint Gobain Velimat Polska w Gorlicach. Spółka Saint Gobain Velimat Polska należy do Grupy Saint Gobain, światowego lidera na rynku budowlanym, która produkuje i dystrybuuje materiały budowlane będące odpowiedzią na konieczność związaną z oszczędzaniem energii i ochroną środowiska. Należąc do grona 100 największych grup przemysłowych świata, Saint Gobain stale rozwija swoje technologiczne know-how, często we współpracy z najbardziej prestiżowymi uczelniami i laboratoriami badawczymi. Obszarem działalności Spółki Saint Gobain Velimat Polska w Gorlicach jest produkcja i sprzedaż tkanin i dzianin z włókna szklanego dla budownictwa. Firma dostarcza produkty dla różnych zastosowań, takich jak: izolacja akustyczna, pokrycia ścian zewnętrznych, siatki przeciw insektom, pokrycia dekoracyjne, wykańczanie powierzchni i wzmocnienie oraz osnowy dla pap asfaltowych i izolacji antykorozyjnej. Aby zapewnić wytwarzanie produktu o jak najwyższej jakości, podjęto decyzję o wdrożeniu zintegrowanego systemu SPC (ang. Statistical Process Control – Statystyczne Sterowanie Procesem), którego głównym zadaniem jest monitorowanie on-line parametrów procesu produkcyjnego. W centralnej bazie danych systemu, która została opracowana i zaimplementowana tak, aby uwzględniać specyficzne wymagania produkcyjne, gromadzone są dane o jakości procesu pochodzące z dwóch źródeł: z laboratorium oraz automatycznych mierników zainstalowanych na liniach produkcyjnych. Dzięki takiemu rozwiązaniu oraz odpowiedniemu sposobowi udostępnienia tych informacji osoby odpowiedzialne za jakość bezpośrednio na hali produkcyjnej widzą aktualne przebiegi kluczowych parametrów produktu na kartach kontrolnych Shewharta zaraz po wykonaniu pomiarów. Dodatkowo do systemu wprowadzone są informacje o parametrach procesu, co pozwala na śledzenie zależności pomiędzy jakością produktu a nastawami procesu na poziomie inżynierskim. Oprócz śledzenia on-line przebiegu procesu produkcyjnego i rutynowego raportowania system umożliwia wykonywanie zestawień dotyczących parametrów produkcji z dowolnego okresu i analiz ad-hoc, przez co pozwala lepiej poznać i zrozumieć zależności zachodzące w tym procesie, wpływające na jakość produktu.