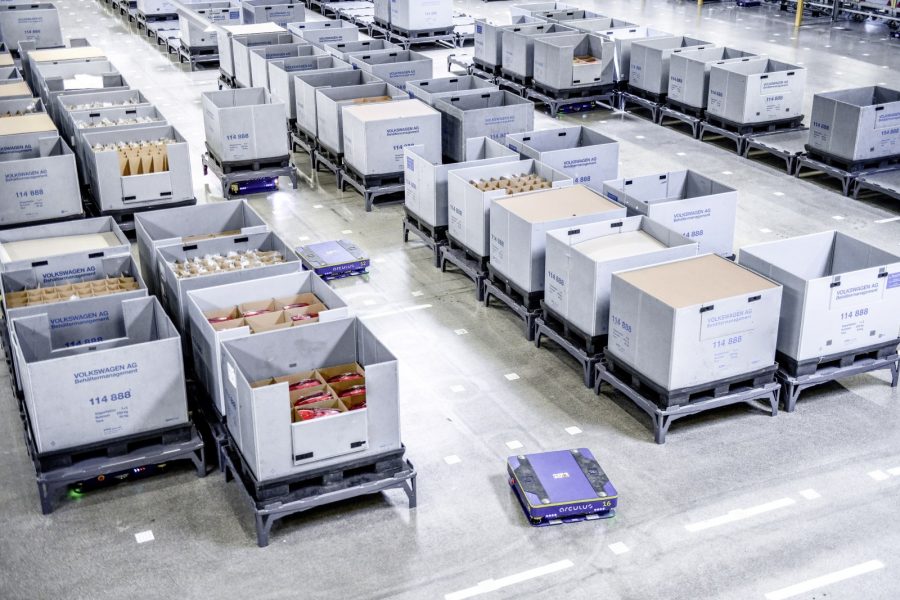
Supermarket 2.0 w przemyśle motoryzacyjnym
W fabrykach Audi od wielu już lat używa się automatycznie sterowanych pojazdów (AGV). Pomagają one w tzw. supermarketach – obszarach logistycznych działających w myśl koncepcji Przemysł 4.0 , z których pracownicy, w odpowiedniej kolejności, pobierają podzespoły do produkcji.
Teraz niemiecki producent niejako odwraca tę zasadę kolejności i wdraża projekt Supermarket 2.0. W nim to towar trafia bezpośrednio do pracownika, a nie na odwrót. Wszystko to jest możliwe dzięki innowacyjnemu oprogramowaniu sterującemu, opracowanemu przez ekspertów Audi we współpracy z technologicznym start-up’em „arculus”.
Towar do osoby
Po raz pierwszy w logistyce produkcji seryjnej w branży motoryzacyjnej, wdrożona zostaje zasada „towar-do-osoby” członek zarządu Audi AG ds. produkcji Peter Kössler mówi: – Supermarket 2.0 i Audi Fleet Manager to niezwykle ważne etapy w tworzeniu przyszłościowej, inteligentnej logistyki. Oprogramowanie pozwala na używanie w przyszłości różnych pojazdów AGV na tym samym obszarze
Kiedyś, zgodnie z zasadą pobierania podzespołów „osoba-po-towar”, pracownicy podczas komisjonowania towarów pokonywali duże odległości, tracąc przy tym czas. Projekt Supermarket 2.0 po raz pierwszy na szerszą skalę umożliwia zastosowanie zasady „towar-do-osoby”. Pojazdy AGV podjeżdżają pod kontenery z niezbędnymi komponentami i transportują je w odpowiedniej kolejności do stałego stanowiska komisjonowania. Na stanowisku tym natomiast, pracownik logistyki rozdziela odpowiednie podzespoły na odpowiednie miejsca linii produkcyjnej. Sterujące tym procesem centralne oprogramowanie nosi nazwę Audi Fleet Manager. Zmiana zasad dostarczania spowodowała, że teraz regały magazynowe zajmują mniej miejsca i w ten sposób Audi w przyszłości będzie w stanie zredukować przestrzeń magazynową o około 25 procent.
– Dzięki projektowi Supermarket 2.0 i dzięki oprogramowaniu Audi Fleet Manager, wkroczyliśmy w niezwykle ważny etap rozwoju inteligentnej logistyki przyszłości – mówi Peter Kössler. Duża różnorodność części i podzespołów oraz potrzeba poprawnego ich sekwencjonowania sprawia, że produkcja samochodów jest wyzwaniem dla scentralizowanego sterowania pojazdami automatycznymi AGV. Opracowany przez Audi we własnym zakresie Supermarket 2.0, jest wykorzystywany w procesie seryjnej produkcji w głównej fabryce czterech pierścieni w Ingolstadt. Obecnie oprogramowanie steruje jednocześnie ośmioma zautomatyzowanymi pojazdami AGV, a do końca roku liczba ta wzrośnie do 32.
Dostosować się do rożnych AGV
Równocześnie, eksperci Audi AG oraz FAW-Volkswagen Automotive Company Ltd. z Foshan w Chinach, stworzyli podobny Supermarket 2.0. System ten został uruchomiony na początku 2020 roku w fabryce FAW-VW, która produkuje Audi A3, Audi Q2L, Audi Q2L e-tron oraz inne modele Grupy Volkswagen z przeznaczeniem na rynek chiński. Tamtejsze rozwiązanie bazowało jednak na systemie AGV lokalnego producenta i zostało dostosowane do specyficznych wymagań projektu Supermarket 2.0 oraz produkcji motoryzacyjnej.
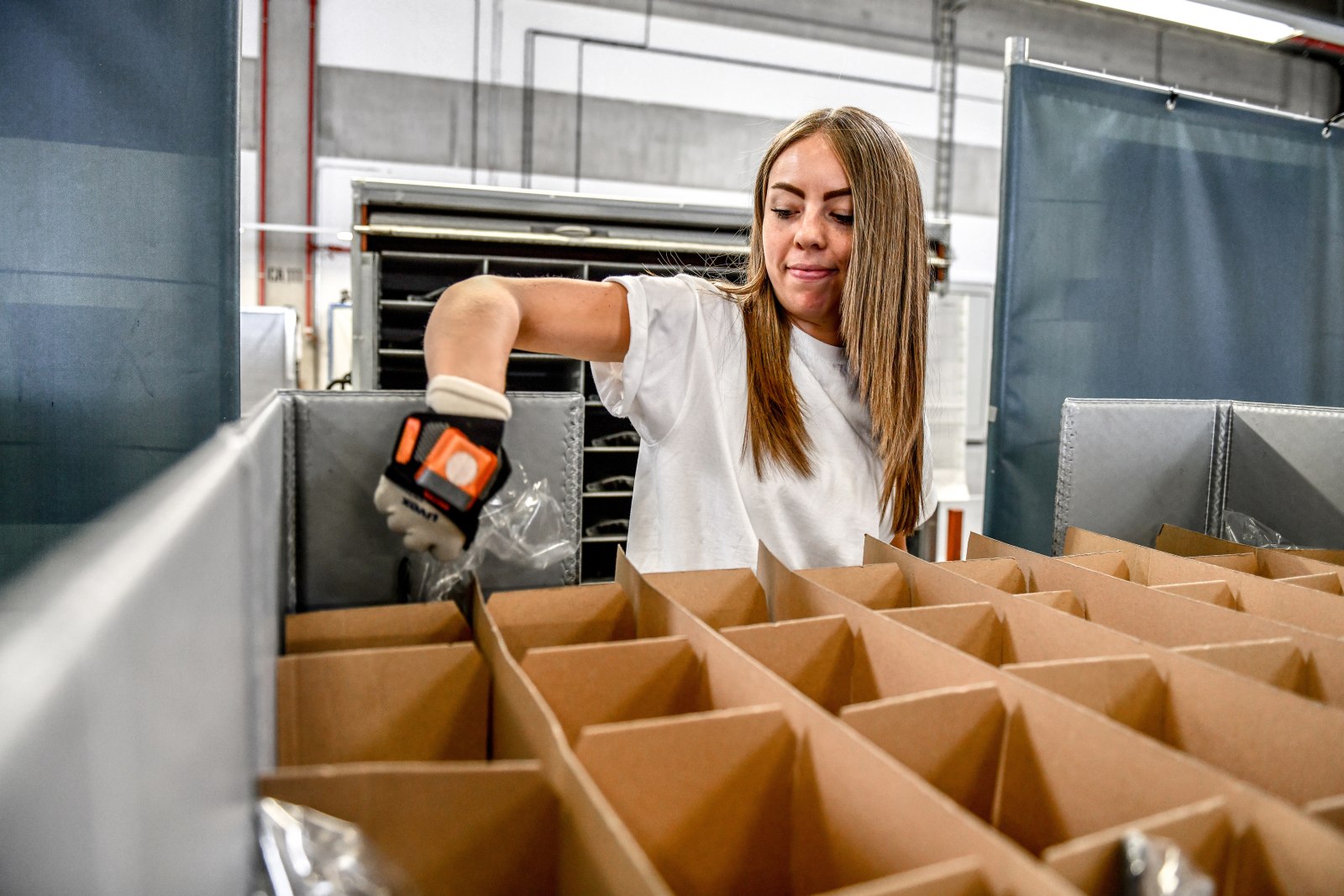
Audi, już w roku 2015, jako pierwszy na świecie producent z branży motoryzacyjnej, na małą skalę przetestowało zasadę „towar-do-osoby”. Pojazdy AGV pomagały pracownikom odbierać instrukcje obsługi pojazdów. AGV używane obecnie w Supermarkecie 2.0 w Ingolstadt, mogą transportować materiały o masie do jednej tony i poruszać się z prędkością 1,5 m/sekundę, co gwarantuje bezpieczeństwo pracowników. Między innymi dzięki systemowi Supermarket 2.0, Audi zostało pionierem innowacji w Grupie Volkswagen. Stąd Grupa planuje wykorzystanie tego rozwiązania również w innych fabrykach Audi oraz na potrzeby innych marek Grupy.
Audi Fleet Manager w przyszłości oferował będzie jeszcze inne korzyści. Każdy producent pojazdów AGV używa własnego oprogramowania sterującego, co oznacza, że różne pojazdy nie mogą się ze sobą komunikować. By zapobiegać kolizjom, potrzebują oddzielnych, własnych szlaków komunikacyjnych. Jednak pojazdy różnych producentów dobrze się uzupełniają – każdy ma swoje zalety. W związku z tym, Audi szukało rozwiązania, w którym pojazdy te mogłyby jednocześnie pracować na tym samym obszarze. Supermarket 2.0 i jego centralne oprogramowanie w przyszłości rozwiążą ten problem.
Drony przyśpieszają dostawy
Pojazdy AGV i Supermarket 2.0 wspierają logistykę wewnętrzną, ale Audi sięgnęło po zaawansowane rozwiązania także w procesie dostaw samochodów dla klientów. W zakładzie w Neckarsulm, używa specjalnie opracowanego drona do lokalizowania pojazdów gotowych do wydania. Urządzenie porusza się nad placem parkingowym zupełnie autonomicznie. Dron wykorzystuje techniki GPS i RFID do identyfikacji i zapisu dokładnej pozycji wszystkich pojazdów nad którymi przeleciał, pomagając w ten sposób pracownikom Audi w precyzyjnym planowaniu wysyłek do klientów.
Z taśm produkcyjnych fabryki Audi w Neckarsulm zjeżdża dziennie wiele różnych modeli: Audi A4 Limousine, Audi A5 Cabriolet, Audi A6, Audi A7, Audi A8, a z zakładu w Böllinger Höfe dodatkowo Audi R8. Po wyjeździe z hali produkcyjnej, pracownicy parkują samochody w wyznaczonych miejscach fabrycznego placu parkingowego. Nabycie pewności, że każdy egzemplarz Audi znajdzie stąd drogę do nowego właściciela, wymaga precyzyjnego planowania – od etapu produkcji, aż po moment wysyłki z fabryki. Od niedawna, pracownicy fabryki w Neckasulm otrzymują w tym procesie „pomoc z góry”. Mają do swej dyspozycji drona, który ułatwia i usprawnia lokalizację samochodów na placu.
Złożona fabryka
Biorąc pod uwagę fakt, że w Neckarsulm produkowanych jest tak wiele różnych modeli, fabryka ta jest jedną z najbardziej złożonych w Grupie Volkswagen. To z kolei sprawia, że precyzyjne planowanie wysyłek jest szczególnie trudne. – Szybka lokalizacja pojazdów to jeszcze wyższa jakość procesu i kolejny krok na drodze do produkcji cyfrowej. Dron zapewnia wsparcie z zupełnie nowej perspektywy. Oczywiście naszymi doświadczeniami w tym obszarze podzielimy się z innymi fabrykami Audi oraz w ramach Grupy Volkswagen – wyjaśnia Steffen Conrad, kierownik projektu w zakresie zarządzania innowacjami w zakładzie Audi w Neckarsulm.
Podstawą tego rozwiązania jest technika, z której od dłuższego czasu korzysta Audi: chip RFID (ang: radio frequency identification – identyfikacja przy pomocy fal radiowych) wraz z towarzyszącym mu numerem identyfikacyjnym pojazdu, który każde Audi otrzymuje już w procesie montażu nadwozia. Specjalnie opracowany heksakopter (dron z sześcioma śmigłami) przelatuje po ustalonych trasach, na wysokości około dziesięciu metrów, nad placem na którym stoją przygotowane do wysyłki pojazdy i określa dokładne położenie zaparkowanych tam samochodów. Dron wykorzystuje czytnik RFID do odczytu numeru każdego pojazdu i zapisuje zidentyfikowaną pozycję GPS auta. Gdy tylko dron wyląduje, dane są automatycznie, przez Wi-Fi, przesyłane do bazy danych. Po zakończeniu procedury lotu wynik jest wyświetlany na cyfrowej mapie.
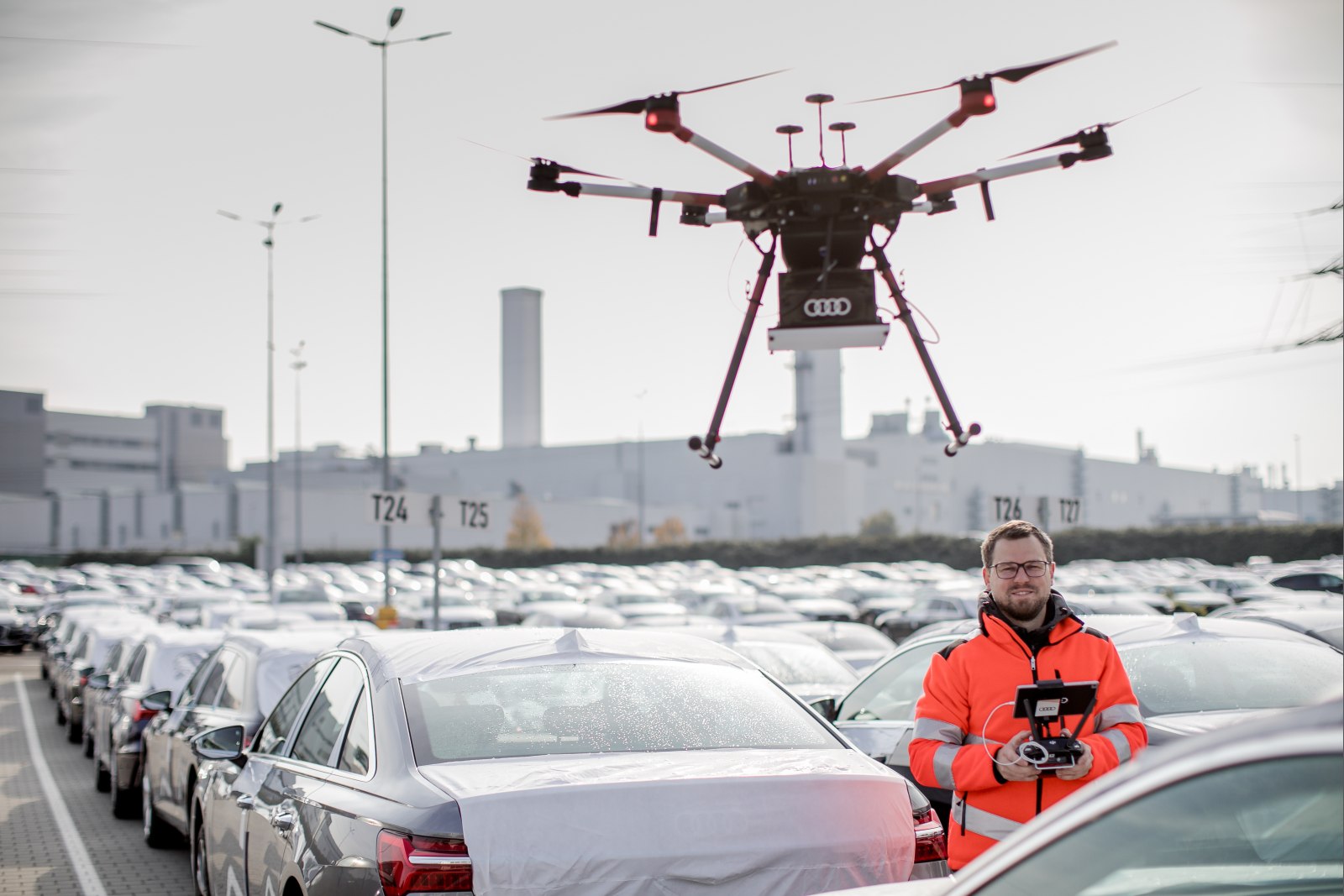
Na dobrą pogodę
Dron startuje, leci i ląduje autonomicznie. Przeszkolony odpowiednio pracownik Audi rozpoczyna, a następnie monitoruje cały lot na laptopie, albo na tablecie. W sytuacjach awaryjnych pracownik może oczywiście przełączyć się na ręczne sterowanie. Do obsługi tego przemysłowego drona zostało jak dotąd przeszkolonych czterech pracowników. Częścią szkolenia jest też uzyskanie profesjonalnej licencji obsługi latających dronów.
Przed każdym lotem dron automatycznie odczytuje prognozę pogody nad terenem zakładu w Neckarsulm. Jeśli wiatr jest zbyt silny lub porywisty albo zapowiadane są opady deszczu, dron nie wystartuje. Ponadto, oprogramowanie przed każdym lotem sprawdza poziom baterii drona i jej temperaturę. Jeśli coś nie mieści się w określonych parametrach bezpieczeństwa, dron pozostaje na ziemi.
Pilotażowy projekt został teraz skierowany do testów seryjnych, w ramach których eksperci z Neckarsulm będą gromadzić dalsze doświadczenia. Zapewne w przyszłości drony wykorzystywane będą do lokalizacji pojazdów również w innych fabrykach Audi.
Artykuł ukazał się w czasopiśmie Eurologistics nr 4/2020