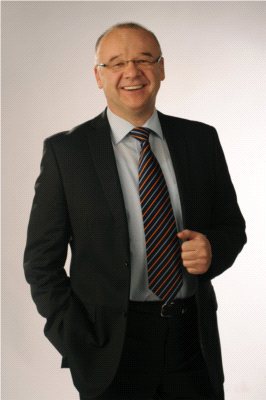
Systemy dla nanotechnologii
Z Andreasem Glenzem prezesem firmy PREVAC rozmawia Przemysław Ozga.Jakie sektory korzystają z państwa specjalistycznych produktów?
Naszymi odbiorcami są głównie instytuty naukowe, jednostki badawczo-rozwojowe, uniwersytety oraz politechniki, jak i szeroko pojęty...
Jakie sektory korzystają z państwa specjalistycznych produktów?
Naszymi odbiorcami są głównie instytuty naukowe, jednostki badawczo-rozwojowe, uniwersytety oraz politechniki, jak i szeroko pojęty przemysł. Aparatura konstruowana przez naszą firmę jest wykorzystywana do rozwoju nanotechnologii, która jest nauką o materiałach zajmującą się budowaniem struktur na poziomie pojedynczych atomów i cząsteczek. Nanotechnologie są wykorzystywane m.in. w medycynie, farmacji, elektronice, motoryzacji, przemyśle spożywczym, włókienniczym, odzieżowym, meblarskim, budownictwie i wielu innych dziedzinach. Dzięki naszej aparaturze powstają nowe materiały, m.in. gatunki stali, stopów lekkich, klejów, lakierów, światłowodów, katalizatorów, powierzchni uszlachetniających do produkcji narzędzi obróbczych, optyki, warstw termo-reflektujących, nowoczesnych ubrań na bazie membran, półprzewodników używanych w mikro- i nanoelektronice oraz medycynie, np. materiałów do produkcji sztucznych zastawek serca, implantów, stentów itp. Na naszej aparaturze testowane są m.in. spektrometry montowane w rakietach kosmicznych przeznaczonych do analiz składów atmosfer na nowo badanych planetach. Ostatnia ciekawostka dotyczy pierwszego polskiego satelity nauko-badawczego LEM.
Cały czas wybiegamy w przyszłość, często wiemy, jak będą wyglądać nowe technologie, np. nowa generacja samochodów będzie oparta na produktach, które powstają dzięki naszej aparaturze. Ale motoryzacja to tylko jeden z przykładów. Praktycznie wszystkie branże przemysłowe korzystają z badań, które są przeprowadzane przy użyciu naszej aparatury. Tak powstają np. impregnaty do bawełny czy nowa generacja bardzo twardych lakierów na bazie nanorurek.
Czy korzystają państwo ze stałych dostawców komponentów zasilających linie produkcyjne?
Mając na uwadze znaczenie niezawodności wyrobu oraz wagę zapewnienia ciągłej zdolności do spełnienia wymagań klienta musimy dążyć do kształtowania wzajemnie korzystnych relacji z naszymi dostawcami. W tym celu dokonujemy bieżącej oraz okresowej kwalifikacji dostawców, tym samym możemy stwierdzić, iż prowadzimy stałą współpracę z dostawcami zapewniającymi optymalną relację pomiędzy jakością, ceną oraz terminem dostawy. Przyjmując za podstawę wymagania normy ISO 9001 opracowaliśmy system oceny dostawców obejmujący szeroki zakres kryteriów kwalifikacji, wśród których do najważniejszych zaliczamy atrakcyjność cenową, wyniki oceny ilościowej i jakościowej realizowanych dostaw, jak również dotrzymanie przez dostawcę zadeklarowanego terminu realizacji. Weryfikujemy również wdrożenie przez dostawcę systemu zarządzania jakością. Dzięki tak sformułowanym kryteriom oceny współpracujemy z firmami wiodącymi w danej branży. Co więcej, wieloletnia współpraca owocuje korzystniejszymi warunkami realizacji naszych zamówień. Zakupy u stałych sprawdzonych dostawców to czynnik mający istotny wpływ zarówno na proces produkcyjny, jak i szybki czas reakcji serwisowej na zgłoszenia klientów. Tak sformułowana polityka zakupów pozwala nam na utrzymanie wizerunku rzetelnego partnera w oczach naszych klientów.
Państwa firma realizuje mieszany model projektowo-produkcyjny…
Rynek, w którym porusza się nasza firma, cechuje bardzo duża dynamika zmian technologicznych i wymagań klientów. Z uwagi na ogromny potencjał ludzki i maszynowy posiadany przez firmę jesteśmy w stanie realizować najbardziej nietypowe zamówienia naszych klientów w zakresie różnych technologii, ale też oferujemy pewną gamę produktów standardowych. Kombinacja wcześniej wymienionych przyczyn zmusza nas do ciągłego dopasowania i rozwoju naszych produktów oraz z jednej strony utrzymywania pewnych stanów magazynowych dla wybranych materiałów i produktów, z drugiej minimalizowania ich w celu zapobieżenia dezaktualizacji technologicznej.
Żeby sprostać tak zmiennym wymaganiom oraz postępowi technologicznemu balansujemy wykorzystując różne modele produkcji do różnych produktów. I tak wśród wykorzystywanych modeli produkcyjnych znajduje się model ETO, czyli projektowanie pod zamówienie, ATO, czyli montaż pod zamówienie oraz MTS, czyli produkcja na magazyn.
W tak złożonym środowisku produkcyjnym musimy korzystać z narzędzi informatycznych, ponieważ w przeciwnym wypadku zarządzanie tysiącami zleceń w bieżącej produkcji wymagałoby zatrudnienia sztabu planistów i ciągłego ręcznego aktualizowania harmonogramu produkcyjnego. Aby zarządzać tak złożonym modelem, wykorzystujemy moduł zaawansowanego planowania i harmonogramowania produkcji z ograniczeniami. Działa on obecnie w możliwie krótkim horyzoncie czasowym i obejmuje kilka najbliższych projektów. Docelowo harmonogramowanie z ograniczeniami ma objąć wszystkie projekty i produkty zamówione przez naszych klientów oraz udostępniać handlowcom funkcjonalność ATP i CTP na poziomie przygotowania oferty handlowej, w celu jak najbardziej realnego przedstawiania klientom prognozowanych czasów realizacji ich potencjalnych zamówień.
Jak wygląda u państwa proces harmonogramowania produkcji?
Proces harmonogramowania produkcji ściśle związany jest z kolejnością przyjmowania zamówień na nowe projekty. Kolejność ta przenosi się bezpośrednio na produkcję. Przyjmowane zamówienia w zdecydowanej większości to projekty innowacyjne, które wymagają przeprowadzenia skomplikowanego procesu projektowego. Handlowiec odpowiedzialny jest za pierwszy kontakt z klientem – to on przekłada oczekiwania klienta na ustalenie i przedstawienie jak najlepszej oferty cenowo-technicznej. Zamówienie następnie trafia do działu konstrukcyjnego, gdzie każde z wymagań klienta jest na nowo analizowane i konfrontowane z realnymi możliwościami produkcyjnymi. Proces ten jest bardzo praco- i czasochłonny, ponieważ wiele zagadnień wymaga konsultacji z klientem oraz „burzy mózgów” naszych specjalistów. Po zakończeniu prac projektowych powstały projekt przechodzi przez proces zatwierdzania, którego uwieńczeniem jest wejście na produkcję. Czynnikiem ograniczającym jest zdolność produkcyjna. W planowaniu pomaga nam system IFS, z którego otrzymujemy informację, jakie jest obciążenie poszczególnych gniazd produkcyjnych, jakie detale i w jakiej kolejności powinny być produkowane itp. Po wykonaniu potrzebnych podzespołów następuje montaż oraz testy całej aparatury. Wyjątkiem są standardowe komponenty, które nie wymagają prac projektowych. Podsumowując, głównymi czynnikami wpływającymi na harmonogram produkcji są data przyjęcia zamówienia, zdolność produkcyjna, praco- i czasochłonność projektowo-produkcyjna aparatury.
Czy wymaga to elastycznej produkcji?
Taki model działania pociąga za sobą konieczność posiadania bardzo dobrze zorganizowanej grupy konstruktorów. Konsekwencją tak dużej różnorodności rozwiązań jest produkcja pod projekt. Przy produkcji prototypowej nie można w 100 procentach uniknąć poprawek. Wpływa to na wymaganie dużej elastyczności w każdym z działów, szczególnie w dziale produkcyjnym. W naszej firmie bardzo szybko trzeba reagować na bieżące potrzeby montażu. Brak jednego detalu bądź też jego poprawa blokuje cały proces montażowy, a co za tym idzie, uniemożliwia sprzedaż całego systemu.
Jak głęboko jest zautomatyzowana państwa produkcja? Czy posiadają państwo dział utrzymania ruchu lub osobę odpowiedzialną za gospodarowanie remontami?
Dbałość o jakość dostarczanych wyrobów zobligowała nas do opracowywania i wdrażania procedur umożliwiających prowadzenie procesów w sposób kontrolowany i bez nieuzasadnionych przestojów. Warunkiem koniecznym tym samym staje się wykorzystanie urządzeń zapewniających zachowanie reżimu technologicznego oraz wysokiej dokładności.
Park maszynowy umożliwia zarówno produkcję jednostkową, jak i produkcję seryjną na obrabiarkach sterowanych numerycznie, a także na maszynach konwencjonalnych. Sam proces obróbki mechanicznej jest wspomagany poprzez oprogramowanie CAD/CAM umożliwiające opracowanie procesu technologicznego obrabianego detalu.
Zaoferowanie klientowi końcowemu urządzeń i elementów spełniających bardzo wyrafinowane wymagania, jakie wiążą się z przeznaczeniem do pracy w warunkach ultra wysokiej próżni (UHV), jest możliwe m.in. poprzez wykorzystanie infrastruktury umożliwiającej obróbkę materiałów dedykowanych, w tym spawanie metodą TIG, spawanie mikro-plazmą elementów cienkościennych, lutowanie na gorąco, masowe gradowanie i polerowanie małych elementów za pomocą specjalnych urządzeń oraz mycie elementów za pomocą myjek ultradźwiękowych.
Postawienie na wykorzystanie maszyn renomowanych marek zaowocowało nie tylko zwiększeniem dokładności i wydajności, ale również zminimalizowaniem kosztów obsługi technicznej maszyn. Opracowany i wdrożony przez nas plan konserwacji maszyn umożliwił ograniczenie odpowiedzialności za utrzymanie ruchu do jednej osoby. Potwierdzeniem skutecznej realizacji zasad gospodarowania remontami jest fakt sporadycznie występujących usterek, do których usunięcia wzywany jest serwis fabryczny producenta maszyny.Oferując urządzenia przeznaczone często do nowatorskich eksperymentów jesteśmy wręcz zobowiązani do wykorzystywania nowoczesnych technologii i prac badawczych. Nie można tutaj nie poruszyć kwestii procesów testowania i kontroli jakości, podczas prowadzenia których wykorzystywany jest szeroki zakres sprzętu pomiarowego oraz własne urządzenia testowe. W celu skutecznej realizacji procesów pomiarowych w 2011 roku rozpoczęto proces wdrażania wymagań normy ISO 17025.
Jak wygląda u państwa optymalizacja zapasów magazynowych?
W obecnych czasach każdy dąży do tego, żeby mieć minimalny stan magazynowy. Tak jak większość firm staramy się produkować i kupować tylko te elementy, które są bezpośrednio potrzebne na montażu. Oczywiście pod uwagę należy brać specyfikę naszej produkcji – jest to produkcja jednostkowa. Stąd tylko niewielka część komponentów może być wyprodukowana wcześniej. Utrzymywanie wysokich stanów magazynowych jest bardzo wygodne z punktu widzenia montażu, jednak jest to rozwiązanie bardzo mało ekonomiczne. Pojęcie krótkoseryjnej produkcji na magazyn ogranicza się u nas do detali standardowych, które są używane w różnych systemach. Już wielokrotnie przekonaliśmy się, że zmiany konstrukcyjne postępują bardzo szybko i detale z magazynu nie mogą być wykorzystane w kolejnych projektach. Zmiany te mają swoje podłoże w ciągłym doskonaleniu naszych produktów. Każdy system musi być dopracowany w najmniejszym szczególe i jak tylko pojawia się nowy pomysł na udoskonalenie, bezzwłocznie wprowadzany jest w życie. Można oczywiście negować takie podejście, ale taka jest właśnie filozofia naszej firmy. Optymalnym jest, żeby większość detali była produkowana bezpośrednio pod dany projekt. Zgodnie z filozofią myślenia TOC staramy się skracać do minimum czas produkcji poszczególnych detali, a co za tym idzie, czas zakończenia całego projektu. Specyfika naszej produkcji pociąga za sobą pewne negatywne konsekwencje, jeżeli chodzi o politykę magazynową. W systemach oferowanych przez firmę PREVAC jest bardzo duża liczba wysoko specjalizowanych komponentów, które są produkowane przez firmy na całym świecie. Przy tego typu komponentach bardzo często terminy dostaw są bardzo długie, a więc chcąc zapewnić ciągłość produkcji i dotrzymanie terminów dostaw, trzeba je zamawiać z pewnym wyprzedzeniem, co pociąga za sobą niekorzystny efekt w postaci wysokich stanów magazynowych.
PREVAC korzysta z czterech obiektów magazynowych. Z jakiego wyposażenia korzystają ich pracownicy?
W firmie posiadamy kilka magazynów – montażowy, działu obróbki, działu elektroniki i IT oraz serwisowy. W każdym z nich magazynowane są materiały, półprodukty i produkty. Magazyny wyposażone są w liczne regały o różnej nośności – regały, na których przechowywane są lekkie komponenty, mają nośność od 150- 250 kg. Materiały, półprodukty i produkty przechowywane na magazynie np. działu obróbki cechują się większym ciężarem i wymagają kilkunastu regałów o nośności sięgającej rzędu 1200- 5000 kg. Każdy z magazynów posiada specjalnie wydzieloną powierzchnię na tzw. towary wielkogabarytowe, które przechowywane są na paletach i wymagają dodatkowej przestrzeni w przypadku konieczności ich mechanicznego przetransportowania. Towary znajdują swoje miejsce na magazynie zgodnie z ich wymaganiami (brak wilgoci, odpowiednia temperatura, brak wstrząsów itp.), gabarytami oraz podziałem na grupy ustalonym według numeracji nadawanej przez system. To właśnie posiadany przez nas system ERP integrujący pracę całej firmy wspomaga nadzorowanie i usprawnienie działań w zakresie gospodarki magazynowej. Nadawane numery są w szybki i łatwy sposób identyfikowane za pomocą czytników kodów kreskowych, w które wyposażony jest każdy z magazynów. Dysponujemy oczywiście wózkami widłowymi, paletowymi, jak i ręcznymi tak i podnośnikowymi. Nie korzystamy jednak z terminali radiowych.
Niedawno wdrożono u państwa system ERP – IFS, zastępując starszą wersję. Proszę opisać proces implementacji.
Decyzję podjęto już w roku 2009, rozpoczynając tym samym proces przygotowania firmy do wdrożenia nowego systemu. Firma przeżywała dynamiczny rozwój i wówczas używany system ERP przestał być wystarczającym narzędziem do pozyskiwania informacji niezbędnych do zarządzania firmą i nie wspierał obszarów projektowo-produkcyjnych. Wdrożenie przeprowadzono w niestandardowy sposób – posiadając zespół specjalistów o wysokich kompetencjach w zakresie IT, postawiliśmy sobie bardzo ambitny cel, aby wdrożyć system samodzielnie. Zainwestowaliśmy w ten projekt dużo czasu i pracy, gdyż zdawaliśmy sobie sprawę, jakie konsekwencje mogłyby wystąpić, gdyby wdrożenie było nieodpowiednio przygotowane. Samo wdrożenie natomiast było zaskakująco krótkie – trwało nieco ponad trzy miesiące. Wcześniej nikt nie chciał wierzyć, że nam się to uda. Uprzedzano nas, że wdrożenie systemu w tak dużym zakresie i w tak krótkim terminie to ogromne ryzyko. Na szczęście, obyło się bez większych przeszkód i niespodzianek, gdyż byliśmy świetnie przygotowani. Tu można mówić o kreatywności i silnym zaangażowaniu kadry.
Czy współpracują państwo z firmą transportową/logistyczną dystrybuującą produkty do ostatecznych odbiorców?
Tak, zlecamy transport produkowanych przez nas aparatur firmom spedycyjnym. Z uwagi na specyfikę produkowanych rzeczy, czyli aparatury naukowo-badawcze, które są czułe na wszelkiego rodzaju wstrząsy, drgania, mamy specyficzne wymagania względem firm transportowych. Robimy zatem wycenę konkretnego transportu u kilku firm spedycyjnych i wybieramy tę, która przedstawi nie tylko najlepszą ofertę cenową, ale również spełnia nasze wymagania odnośnie samochodów, m.in. zawieszenie pneumatyczne, zabudowa typu kontener, winda) oraz możliwie najkrótszy czas doręczenia. Zdarzają się sytuacje, gdzie istotna jest nawet trasa samego przewozu aparatury.
Każdy taki transport podlega również ubezpieczeniu. Wszystko po to, aby uzyskać jak najlepsze warunki i nie chodzi tu tylko o cenę, ale również o zakres, klauzule ubezpieczenia. Transport naszej aparatury to nie tylko transport drogowy, ale również transport lotniczy. Przy transportach towarów, które wychodzą poza obszar Unii Europejskiej, obsługę celną w państwie klienta zlecamy również spedytorowi. Jednym słowem obsługa w pełnym zakresie. Bardzo ważna jest przy wyborze spedytora kompleksowość świadczonych usług, ale również dotychczasowe doświadczenie czy relacje.
Czy korzystają państwo z outsourcingu w którejś z dziedzin państwa działalności?
Tak jak większość firm, korzystamy z outsourcingu. W naszej firmie współpraca z firmami zewnętrznymi sprowadza się głównie do kooperacji w zakresie produkcji detali potrzebnych do naszych projektów oraz wykonania specyficznych usług, takich jak pokrywanie detali specjalnymi powłokami, wycinanie elementów z blach, szycie namiotów oraz usługi stolarskie w zakresie wykonania opakowań. Nasz warsztat ma ograniczone zdolności produkcyjne, chociaż jesteśmy w stanie wyprodukować prawie wszystkie potrzebne detale. Chcąc zwiększyć ilość produkowanych systemów wspieramy się podwykonawcami. Podstawowa trudność we współpracy z naszą firmą to wysokie wymagania jakościowe, bardzo specyficzne materiały, z których są produkowane nasze detale, takie jak stal nierdzewna, tytan i molibden. Kolejną trudnością jest fakt, że elementy potrzebne do montażu aparatur bardzo często są małe gabarytowo, co jest dużym problemem dla firm zewnętrznych. Wbrew pozorom i ogólnej opinii, że każda firma szuka zleceń bardzo trudno jest znaleźć podwykonawcę w takim asortymencie.