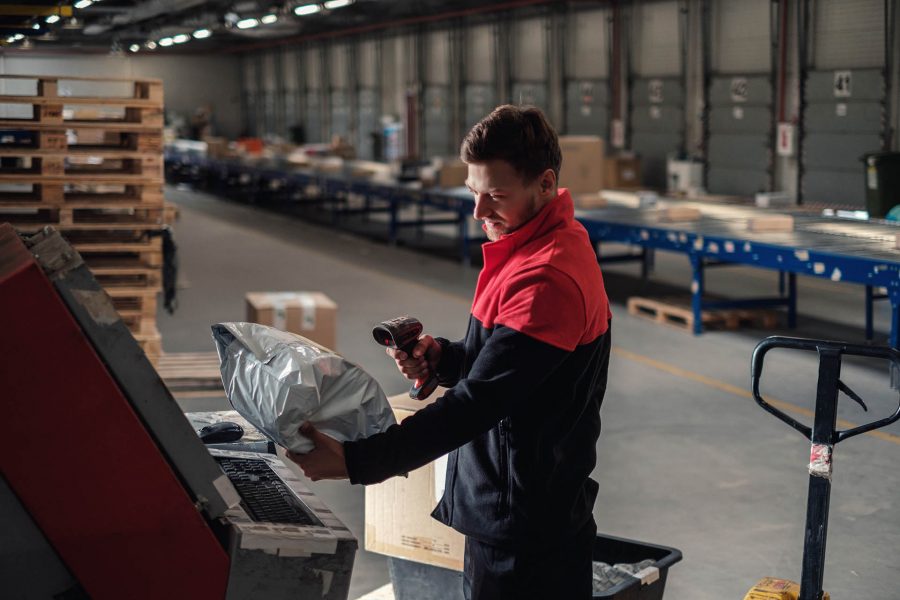
Top 5 najczęstszych problemów w procesach magazynowych
Każda firma chcąc poprawić swoją pozycję na rynku musi cały czas dążyć do osiągnięcia przewagi konkurencyjnej. Bardzo często cel ten jest realizowany poprzez optymalizację procesów, które przekładają się na redukcję kosztów. W projektach generujących oszczędności wiele przedsiębiorstw zwraca się z prośbą o wsparcie do firm konsultingowych, które posiadają szeroką wiedzę specjalistyczną oraz odpowiednie kwalifikacje w zarządzaniu pracami projektowymi.
Na podstawie doświadczeń jednej z nich – firmy SMART Project, będącej liderem na rynku doradczym w Polsce, postaram się omówić 5 najczęstszych problemów w procesach magazynowych. Przedstawione w niniejszym artykule wnioski są wypadkową wieloletnich praktyk i dziesiątek z powodzeniem zrealizowanych projektów usprawnieniowych w największych zakładach w Polsce.
Zanim jednak przejdę do meritum, chciałbym na chwilę pochylić się nad rolą magazynów we współczesnym biznesie. Zadania stawiane przed nimi już od dawna znacznie wykraczają poza tradycyjną ich funkcję, czyli składowanie towarów. Rynek konsumenta wymusza na magazynach transformację w kierunku coraz większej elastyczności w zakresie wykonywanych procesów (np. dodatkowych usług konfekcjonowania, etykietowania, przeładunków) oraz czasu realizacji dostaw (dostawy ekspresowe, nocne czy też weekendowe). Istotny wpływ na sytuację może mieć także wybuch epidemii koronawirusa.
„Magazyny czeka rewolucja w obliczu pandemii. Wzrosną oczekiwania ku temu by było ich więcej, bliżej rynków zbytu. Już nie optymalne zapasy bezpieczeństwa, a efektywna praca na magazynie i sprawne dostawy do klientów zyskają na ważności.” – uważa Joanna Górna, kierownik projektów w SMART Project. Zgodnie z tą opinią efektywność procesów, a więc eliminacja najczęstszych problemów w procesach magazynowych może być źródłem przewagi konkurencyjnej.
Aby wyeliminować owe problemy, osoby zarządzające magazynami muszą postawić sobie pytanie w jaki sposób redukować marnotrawstwa w procesach, a także które z tych problemów generują najwięcej strat. Zgodnie z zasadą Pareto – jedną z podstawowych technik definiowania problemów – 80% skutków jest powodowanych przez 20% przyczyn. Oznacza to, że wpływ zaledwie kilku najistotniejszych z nich znacznie przewyższa wpływ wszystkich pozostałych, co czyni etap identyfikacji niemal kluczowym. Chociaż charakterystyka każdego magazynu jest unikatowa i zagrożenia tam występujące również mogą być różne, warto zwrócić uwagę na te najpowszechniejsze i już na samym początku zastanowić się czy i w jakim zakresie problem ten dotyka naszego magazynu. Mam nadzieję, że ranking 5 najczęstszych problemów magazynowych przygotowany z ekspertami ze SMART Project okaże się w tym pomocny.
Miejsce 5: Niewystarczające wsparcie procesów przez system WMS
Tak jak trudno wyobrazić sobie nasze codzienne życie bez smartfona czy notebooka, tak samo funkcjonowanie magazynów bez systemów informatycznych wspomagających ich pracę wydaje się prawie niemożliwa. Spektrum rozwiązań technologicznych jest naprawdę szerokie: od systemów zapewniających podstawowe funkcje, np. zarządzanie lokalizacjami towarów w magazynie czy kontrolę stanów magazynowych, aż po zaawansowane systemy w pełni dostosowane do potrzeb procesowych, włączając w to możliwość integracji systemu z automatyką magazynową. Właściwie dobrane funkcje systemu WMS pozwalają ograniczyć, a czasem całkiem wyeliminować straty w procesie, takie jak: zbędne prace manualne, poszukiwanie i identyfikacja towaru czy dublowanie czynności. Problemem wielu firm jest jednak brak wiedzy o użytkowanych systemach. Często użyteczne funkcje są na wyciągnięcie ręki – pożądana funkcjonalność znajduje się już w pakiecie wykupionym u dostawcy systemu i wystarczy tylko ją aktywować albo możliwy jest jej zakup za stosunkowo niewielką kwotę.
W niektórych przypadkach – gdy aktualny system nie jest już rozwijany lub każda jego modyfikacja związana jest z wysokimi kosztami, wskazana może okazać się inwestycja w zupełnie nowe oprogramowanie. Koszt zakupu licencji i wdrożenia systemu jest bardzo zróżnicowany i waha się od 150 tyś. zł, do nawet 1,5 mln zł. Jest to jednak wydatek warty swojej ceny – przy przygotowaniu precyzyjnej specyfikacji dostosowanej do potrzeb naszego magazynu, inwestycja ta może w przyszłości w znacznym stopniu zwiększyć efektywność procesów magazynowych.
Miejsce 4: Brak standardów pracy w procesach
Standaryzacja pracy w magazynach zazwyczaj kojarzona jest z przygotowaniem instrukcji stanowiskowych. Mimo pozornej łatwości tego zadania, nawet w tym aspekcie zdarzają się zaniedbania, bo chociaż owe instrukcje powstają, to i tak rzadko są wykorzystywane w praktyce. W rzeczywistości problem jest znacznie bardziej złożony. Członek Zarządu SMART Project Wojciech Rokicki charakteryzuje go w następujący sposób: „Potrzebna jest zmiana priorytetów – po pierwsze planować, tworzyć jasne procesy, szkolić, upraszczać i doskonalić. Nie dać się zapędzić w kozi róg pracy operacyjnej i braku czasu na myślenie. Dotyczy to każdego obszaru, w tym również magazynów”. Trudno z tą opinią się nie zgodzić, bowiem dobrze przygotowany standard powinien nie tylko zostać poprzedzony wnikliwą analizą procesu, ale również cały czas weryfikowany i poprawiany, by finalnie stać się jak najbardziej przystępnym dla jego wykonawców. Ostatecznie to brak pełnego i właściwego zrozumienia zadań jest jednym z głównych powodów nieefektywności w procesach: dodatkowych wyjaśnień, poprawek czy obsługi reklamacji. Dodatkowo, świadomość usystematyzowania procesów zazwyczaj pozytywnie wpływa na motywację pracowników, gdyż nie mają oni wówczas poczucia wykonywania zbędnej pracy. Stworzenie przejrzystego i łatwego do przyswojenia standardu ma także niebagatelny wpływ przy wdrażaniu nowych pracowników, zwłaszcza w firmach o dużej rotacji osobowej lub zatrudniających pracowników sezonowych.
Miejsce 3: Brak lub nieodpowiedni dobór wskaźników magazynowych
Podstawowym narzędziem pracy każdego skutecznego menadżera powinien być odpowiedni zestaw wskaźników. Możliwość zarządzania przez cele, odpowiednie motywowanie, właściwe planowanie pracy oraz możliwość balansowania obciążeń pracowników to tylko niektóre z korzyści płynących z właściwego wykorzystania wskaźników magazynowych. Tymczasem, wielu kierowników nie zdaje sobie sprawy z potęgi tego prostego narzędzia. Problemem najczęściej jest jakość danych, które nie są zbierane i wykorzystywane we właściwy sposób, przez co przygotowanie stosownego raportu bywa mozolne i uciążliwe. Nawet, kiedy wyniki są monitorowane na bieżąco, to nierzadko pozostają tylko do wglądu wąskiego kierownictwa. Jak zatem powinien zostać opracowany użyteczny wskaźnik? Przede wszystkim powinien posiadać konkretny, mierzalny cel. Co więcej, jego wyniki powinny być regularnie prezentowane i omawiane z zespołem magazynowym, np. podczas codziennych kilkuminutowych odpraw zmianowych. Wskazane jest również, aby wartości wskaźników były skorelowane z systemem premiowym dla pracowników. Dalej, pozostaje nam już tylko bieżąca praca ze wskaźnikiem: wynik powyżej celu daje nam pewność, że proces przebiega poprawnie, w przeciwnym wypadku mamy natomiast możliwość natychmiastowej reakcji i ograniczenie negatywnych skutków przyszłości.
Miejsce 2: Błędy w kompletacji
Nie ulega wątpliwości, że kompletacja w zdecydowanej większości magazynów jest procesem kluczowym. Nie tylko angażuje najwięcej zasobów, ale również jest miejscem powstania wartości dodanej dla klienta – przygotowanie zamówionego towaru. Tutaj właśnie powstaje największe zagrożenie, z którym nieustannie zmagają się magazyny. Według dyrektora operacyjnego SMART Project Dominika Kowalczyka „Koszty wynikające z błędów kompletacji potrafią być bardzo wysokie, niejednokrotnie po wykryciu nieprawidłowości prowadzą do zaburzenia pracy nawet kilkuset osób. Najlepszym przykładem takiej sytuacji jest branża automotive, gdzie po kompletacji dostarczamy do linii produkcyjnych komponenty przypisane do właściwego pojazdu. W przypadku wystąpienia pomyłki niejednokrotnie zatrzymywany jest cały ciąg produkcyjny danego działu, np. linii montażowej.” Bardzo często, w celu uniknięcia następstw powstania błędu wykorzystuje się stanowiska kontroli jakości, od których nierzadko wymaga się dokładnego sprawdzenia nawet 100% skompletowanych zamówień. Mamy więc do czynienia z reakcją na skutek (wykrycie błędu), a nie na przyczynę (powstanie błędu), co pochłania dodatkowy czas, a zatem generuje dodatkowe koszty. Przyczyn powstawania błędów można wskazać co najmniej kilka: nadmierny pośpiech, brak odpowiedniego wsparcia systemowego czy wspólne składowanie towarów podobnych do siebie.
I choć ich eliminacja może wydawać się trudna, warto podjąć to wyzwanie. Systematyczna analiza specyfiki powstających błędów może doprowadzić nas do interesujących wniosków: być może pewien typ błędów zdarza się tylko w przypadku konkretnej grupy produktów, dotyczy pewnej grupy pracowników lub tylko określonego przedziału czasu (np. kumulacji zamówień). Tak sprecyzowany problem wyeliminować jest dużo łatwiej, skupiając uwagę kontroli jakości jedynie na tym obszarze. Dodatkowo według Dominika Kowalczyka „Poza budowaniem kultury pracy opartej na samokontroli, uświadamianiu pracowników o konsekwencjach błędu z pomocą przychodzi technika. Coraz częściej spotykamy nie tylko systemy wskazujące lokalizację pobrania oraz odłożenia komponentu ale również kontroli prawidłowości ruchów pracownika poprzez systemy wizyjne, RFID, czujniki ruchu.”
Miejsce 1: Nieoptymalne rozlokowanie towaru w magazynie
Pozostając w temacie kompletacji dochodzimy do numeru jeden w rankingu, a więc najczęściej pojawiającego się problemu magazynowego – nieoptymalnego rozlokowania towaru w magazynie, co w bezpośredni sposób wpływa na wydłużenie ścieżki kompletacji, a zatem powoduje spadek wydajności procesu. Sposób optymalnego rozlokowania poszczególnych asortymentów w znacznym stopniu uwarunkowany jest rotacją towarów. Brak kontroli tego współczynnika w prosty sposób prowadzi do chaosu w lokalizacjach magazynowych. Istotne znaczenie w tym aspekcie mają również nadmierne zapasy, zwłaszcza towarów, których sprzedaż już praktycznie wygasła. W niektórych prowadzonych przez nas projektach skala lokalizacji, z których nie odnotowano żadnego pobrania przez cały rok sięga nawet 40%. To jednak nie koniec, ponieważ rotacja w pozostałej części lokalizacji magazynowych również jest zróżnicowana. W tym miejscu z pomocą przychodzi metoda klasyfikacji ABC, zgodnie z którą aż 80% wszystkich pobrań dotyczyć będzie grupy 20% produktów (kategoria towarów A), kolejne 15% pobrań kolejnych 30% produktów (kategoria B), a ostatnie 5% pobrań wszystkich pozostałych produktów (kategoria C). Wykorzystanie tej wiedzy w praktyce, a więc wydzielenie stref w magazynie odpowiadającym kategoriom rotacji, pozwala zwiększyć wydajność kompletacji nawet o ponad 20%.
Przedstawiona powyżej klasyfikacja jest oczywiście zestawieniem w pełni subiektywnym. Z pewnością, każdy kogo praca bezpośrednio związana jest z magazynem bez problemu będzie w stanie wskazać przynajmniej kilka innych, w jego opinii znacznie częstszych i poważniejszych problemów niż wyżej wymienione. Rzeczywiście temat jest na tyle szeroki, że pewnie trudno byłoby go wyczerpać nawet w wielotomowej książce. Niewątpliwie jednak przedstawione przykłady są realnymi problemami, z którymi zmagają się współcześnie magazyny i świadomość tych zagrożeń powinna być atutem każdego kto kieruje pracą magazynu.