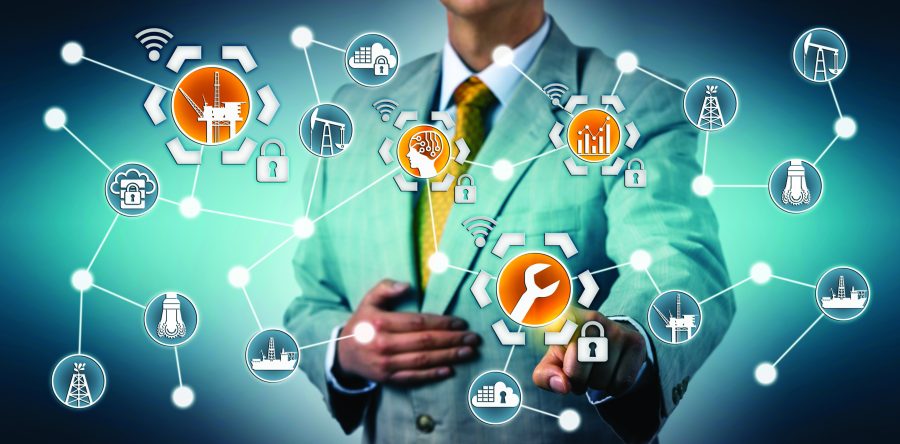
UR coraz bliżej predykcji
Czy możliwe jest ciągłe monitorowanie stanu maszyn pod względem najczęstszych usterek z powodu uderzeń, zmęczenia podzespołów bądź tarcia? Czy da się z wyprzedzeniem w określonym terminie przewidywać i planować prace konserwacyjne, zanim wystąpią poważne uszkodzenia lub awarie powodujące przestoje produkcji?
Takie pytania zadaje sobie wielu przedsiębiorców, którzy w swoich fabrykach i zakładach produkcyjnych chcą stosować rozwiązania i systemy Przemysłu 4.0. Odpowiedź? Tak – wystarczy wdrożyć predykcyjny system monitoringu, ochrony i konserwacji maszyn.
Możliwość zapobiegania nieoczekiwanym awariom sprzętu oraz optymalnego planowania napraw to główny cel konserwacji predykcyjnej, która jest coraz częściej doceniana i stosowana przez zakłady przemysłowe. Konserwacja predykcyjna różni się od profilaktycznej, ponieważ opiera się na faktycznym stanie sprzętu, a nie na przeciętnych lub oczekiwanych statystykach pozwalających przewidzieć, kiedy będzie ona wymagana.
Techniki konserwacji predykcyjnej mają za zadanie pomóc w określeniu stanu eksploatacyjnego maszyn w celu oszacowania, kiedy należy przeprowadzić konserwację. Działania te są oparte na szacowanych stanach degradacji określonych elementów urządzenia. – Pozwalają zapewnić zwiększone bezpieczeństwo instalacji, odpowiednią żywotność sprzętu, mniej wypadków, również tych z negatywnym wpływem na środowisko oraz zoptymalizowane gospodarowanie częściami zamiennymi – mówi Piotr Szopiński z ifm electronic. – Konserwacja predykcyjna pomaga również poprawić wydajność. Została również uznana za jeden ze sposobów wprowadzenia modelu zarządzania just-in-time w produkcji.
Przydatne monitorowanie online i offline
Konserwacja predykcyjna ocenia stan sprzętu poprzez okresowe (offline) lub bieżące (online) monitorowanie stanu sprzętu . Ostatecznym celem tego podejścia jest wykonanie konserwacji w zaplanowanym momencie, kiedy czynności te są najbardziej opłacalne i zanim maszyny stracą wydajność w granicach wyznaczonego progu. Dzięki temu można zmniejszyć nieplanowane koszty przestojów z powodu awarii, które w zależności od branży, mogą sięgać nawet setek tysięcy złotych dziennie.
Większość kontroli predykcyjnych wykonuje się podczas pracy urządzenia, minimalizując w ten sposób zakłócenie normalnego działania systemu. Aby ocenić stan sprzętu, wykorzystuje się tu nieinwazyjne technologie testowe, takie jak np. analiza wibracji, pomiary poziomu dźwięku lub ciśnienia i jakości oleju. Do tego niezbędne są m.in. właściwe czujniki.
Systemy monitorowania stanu
służą do opartej na stanie rzeczywistym konserwacji maszyn
i instalacji. Dostępny na rynku asortyment produktów obejmuje m.in. systemy
monitorowania wibracji, jakości oleju, a także zużycia sprężonego powietrza i wody. Pomagają
one odnaleźć uszkodzenia we właściwym czasie i zapobiegają kosztownym
uszkodzeniom wynikowym.
Nie tylko drgania
Czujniki drgań wykrywają uszkodzenie łożysk i kół zębatych elementów tocznych lub niewyważenie napędów i obracających się części maszyny. Wśród najnowocześniejszych produktów do monitorowania drgań znajdują się m.in. transmitery i czujniki drgań, akcelerometry oraz monitory kontrolne. Transmitery oraz czujniki drgań wykrywają uszkodzenia łożysk tocznych oraz niewyważenie napędów i wirujących elementów urządzeń. Akcelerometry, w połączeniu z elektroniką diagnostyczną, służą do kompleksowego monitorowania drgań w dużych napędach.
Z kolei systemy monitorowania jakości oleju pomagają we wczesnym wykrywaniu wody i cząstek ściernych w cieczach hydraulicznych i smarach, aby zapobiec zakłóceniom pracy lub uszkodzeniom agregatów hydraulicznych, pomp, zaworów, cylindrów i maszyn. Specjalne monitory cząstek są w stanie weryfikować stopień czystości i ewentualny poziom zanieczyszczenia olejów, olejów hydraulicznych oraz cieczy chłodząco-smarujących. Natomiast czujniki do pomiaru wilgotności oleju mogą mierzyć wilgotność względną w oleju. Produkty te przyczyniają się tym samym do zapewnienia optymalnego utrzymania ruchu w oparciu o stan rzeczywisty.
Media też można kontrolować
Kolejnym aspektem wpływającym na skuteczność predictive maintenance jest monitorowanie stanu rzeczywistego mediów. Posłużyć temu mogą np. nowoczesne przepływomierze do sprężonego powietrza. Są one wykorzystywane do zastosowań przemysłowych, do argonu, dwutlenku węgla oraz azotu. Posiadają duży zakres pomiarów do 17500 Nm³/h oraz krótki czas i dużą czułość reakcji. Wskazują ilość przepływu objętościowego, ilość całkowitą i temperaturę oraz ciśnienie. Parametryzacja odbywa się tu bezpośrednio za pomocą przycisków na czujniku. Ponadto czujniki mogą być parametryzowane również przez IO-Link, np. za pomocą interfejsu USB.
Natomiast do pomiaru stanu i przepływu wody służą przepływomierze magnetyczno-indukcyjne lub ultradźwiękowe. Rejestrują one trzy parametry procesowe: wielkość przepływu, ilość zużywaną oraz temperaturę medium. Są często stosowane w obiegach chłodzenia, np. w hutach, w przemyśle motoryzacyjnym lub w produkcji szkła. W zastosowaniach w gospodarce wodnej oraz w urządzeniach przemysłowych czujniki są stosowane do pomiaru zużycia wody.
Skuteczność
Gwarancją skuteczności procesu jest między innymi bezproblemowa integracja powiązana bezpośrednio z systemami przemysłowego ethernetu. Do obsługi alarmów automatycznych służą proste wskaźniki, działające w czasie rzeczywistym. Jednocześnie pozostaje możliwość przechwytywania do zaawansowanej analizy surowych sygnałów i nie ma potrzeby stosowania szaf sterowniczych czy skomplikowanego okablowania. Skuteczne monitorowanie stanu prostych maszyn w sieci jest zapewnione dzięki zwiększonym możliwościom IO-Link i dostępności łatwych sposobów łączenia.
Sprawdzony przemysłowy system IO-Link ułatwia włączanie technologii Przemysłu 4.0. bezpośrednio do własnej, istniejącej platformy sterowania klienta. Bez konieczności stosowania kosztownych dodatkowych sieci, bramek i udziału zespołów IT. Mastery wysyłają sygnały stanu do elementów sterujących oraz mogą wysyłać przetworzone i surowe sygnały dotyczące wibracji do systemów wyższego poziomu. Wszystko to w celu zaawansowanej analizy.
Wartość
Czy sprostanie wymaganiom pomiaru różnych wartości w jednej obudowie czujnika jest możliwe? Z pomocą tutaj przychodzi czujnik wibracji VVB z komunikacją IO-Link. Pozwala ona na pomiar i przetworzenie istotnych wskaźników, z punktu widzenia zabezpieczenia maszyny oraz udostępnienie ich za pomocą komunikacji IO-Link.
Możemy mierzyć prędkość skuteczną drgań v-RMS odpowiadającą za ogólny stopień zużycia maszyn, np. według zbioru norm ISO 10816. Dodatkowo pomiar wartości skutecznej przyspieszenia a-RMS pozwala na wykrycie niekorzystnego tarcia elementów maszyny. Wartość szczytowa a-Peak natomiast odpowiada za wykrycie różnego rodzaju udarów oraz innych uderzeń. Dodatkowo współczynnik szczytu – Crest Factor pozwala na wykrycie degradacji łożysk. Ostatnim ważnym wskaźnikiem jest temperatura, które może wystąpić w przypadku nieodpowiedniego smarowania łożysk lub powstania silnego tarcia.
W celu szczegółowej analizy lub analizy przyczyn w przypadku uszkodzenia, czujnik dostarcza również dane surowe zarejestrowanego przyspieszenia. Są one wysyłane na żądanie w postaci BLOB (Binary Large Object) i przesyłane przez IO-Link. System może rejestrować stan roboczy maszyny nawet co cztery sekundy i przesyłać dane do systemów wyższego poziomu przez kilkanaście minut.
Dostępność
Co rzeczywiście oznacza zastosowanie Przemysłu 4.0. w diagnostyce maszyn? – To odpowiednia informacja, przekazana w odpowiednim czasie, odpowiedniej osobie. W praktyce jest ona w sposób idealny obrazowana przez tak zwany wskaźnik zdrowia maszyn – Overall Equipment Effectivness. OEE to ocena efektywności wykorzystania maszyn przez producenta. W ujęciu procentowym pokazuje, ile maszyny wykonały z tego, co teoretycznie są w stanie wykonać. Poziom 100 procent oznacza, że produkujemy tylko dobre części oraz elementy. Najszybciej jak to jest możliwe i bez żadnych przestojów – mówi Krzysztof Smaga, Inżynier ds. Aplikacji w ifm electronic.
Na finalny wskaźnik OEE przekładają się trzy czynniki. Pierwszy to dostępność, która mierzy nieplanowane i planowane przestoje. Stuprocentowa dostępność oznacza, że urządzenie zawsze pracuje podczas czasu produkcyjnego. Drugi czynnik – wydajność. Ten pomiar mierzy cykle pracy i drobne przestoje, stuprocentowa wydajność komunikuje, że maszyna pracuje z maksymalną możliwą prędkością. Trzeci czynnik to jakość, gdy mierzona jest ilość odpadów oraz elementów, jakie wymagają optymalizacji. Stuprocentowa jakość sygnalizuje, że urządzenie produkuje wyłącznie dobre elementy. Pomnożenie tych trzech wartości procentowych da wynik w postaci wskaźnika OEE, który, typowy dla wartości większości fabryk, powinien oscylować w granicach 60-65 procent, lecz producenci klasy światowej osiągają tutaj rezultaty na pułapie 85 procent.
Rzeczywistość
Wykorzystanie nowoczesnych czujników, co podkreślają eksperci, przełoży się zatem w prostej linii na minimalizację strat na polu dostępności, wydajności i jakości. Pojawi się możliwość zarządzania nieplanowanymi i planowanymi przestojami, skrócą się postoje, ograniczone zostaną wydłużone cykle, pozyskane będą także oszczędności w odrzutach startowych i produkcyjnych. Monitorowanie napędów, przekładni czy narzędzi w fabryce, czyli diagnostyka drganiowa – pozwolą na określenie konkretnych parametrów stanu łożyska, niewyważenia, uderzenia, niewłaściwego ustawienia, poluzowania czy tarcia. Do nietypowych wibracji diagnozowanych przez nowoczesne czujniki smart factory można zaliczyć również niewspółosiowość, luzy, degradację, kawitację, a w przypadku temperatury suchobieg, brak przepływu powietrza czy zapchanie filtrów.
– Dodatkowo oprócz diagnostyki drganiowej, która może być mierzona za pomocą specjalistycznych czujników, do serwerów zajmujących się monitoringiem maszyn w fabryce, trafiają dane dotyczące ciśnienia, temperatury, przepływów, powietrza, stanu napędu, oleju czy zużycia energii. Wszystkie te źródła danych o maszynie, skorelowane z innowacyjnością zastosowań i rozwiązań z palety Industry 4.0. to szansa nie tylko na nowoczesność, ale i oszczędności wynikające z optymalizacji produkcji zakładów przemysłowych z niemal każdego sektora oraz branży – podkreśla Aleksandra Banaś, prezes zarządu ifm electronic.
Uzupełnieniem systemowym są także komplementarne zastosowania z gamy Smartobserver, pozwalające na wykorzystanie narzędzi informujących o aktualnym stanie parku maszyn oraz ich podgląd w czasie rzeczywistym niezależnie od miejsca lokalizacji i przemieszczania się. Wartością dodaną są też pakiety aplikacyjne gotowe do instalacji dedykowanej dla danego zakładu fabrycznego czy integracja z systemami automatyzacji zleceń. Powierzenie przeprowadzenia audytu maszyn pozwoli określić krytyczne elementy i zoptymalizować całe procesy w długofalowej perspektywie.
Sprawdza się w praktyce
Specjaliści z ifm electronic wskazują na wiele wdrożeń, które przyniosły realne korzyści finansowe przedsiębiorstwom, w których były realizowane. Jednym z przykładów jest firma oponiarska, gdzie dzięki wprowadzeniu diagnostyki udało się zapobiec awarii przekładni mikserów, gdyż prace remontowe zostały zaplanowane zanim doszło do poważnych uszkodzeń maszyn. Dodatkowo kontrolowanie drgań przy różnych mieszankach stosowanych przy produkcji opon, pozwoliło im stwierdzić, jakiego rodzaju mieszanki najlepiej nadają się do produkcji i przy jakim obciążeniu powinny wówczas pracować maszyny.
Temat wibracji był również niezwykle istotny dla jednej z firm produkujących samochody. W lakierni jednego z zakładów została zaimplementowana diagnostyka wentylatorów. Dzięki niej, możliwe było uniknięcie awaryjnego wstrzymania ich pracy, co mogłoby doprowadzić do przerwy w procesie lakierowania karoserii. To z kolei mogłoby narazić przedsiębiorstwo na duże straty. W tym przypadku mógłby to być nawet koszt produkcji jednego samochodu na 10 minut. Specjaliści ifm są obecnie na etapie wdrażania kolejnego rozwiązania z obszaru predictive maintenance w innej firmie z branży automotive. W tym przypadku przy wytwarzaniu poszczególnych elementów silnika np. tłoków, bardzo ważne jest ich precyzyjne wykonanie. Do tego wykorzystuje się różne obrabiarki. Przestój jednej z nich doprowadziłby do tego, że cała produkcja tego jednego elementu byłaby wstrzymana. Jest to tym bardziej dotkliwe, że jego produkcja wymaga wykorzystania kilku maszyn.