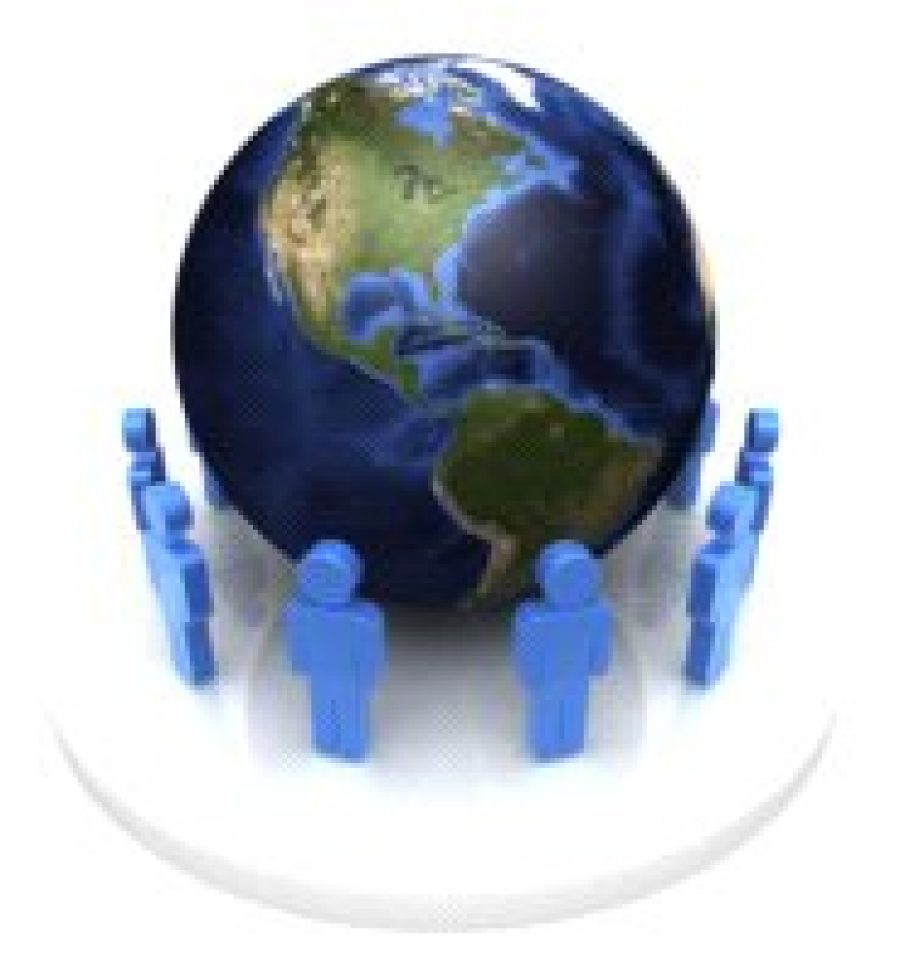
Wykorzystywanie systemu GS1 oraz etykiet dystrybucyjnych w łańcuchu dostaw
O tym jak ważne jest przyśpieszenie i zautomatyzowanie czynności przyjęcia dostaw zewnętrznych oraz wydania (sprzedaży) towaru, zdano sobie sprawę już w roku 1932, kiedy to mała grupa studentów pod kierownictwem Wallach Flint’a wzięła udział w ambitnym projekcie
O tym jak ważne jest przyśpieszenie i zautomatyzowanie czynności przyjęcia dostaw zewnętrznych oraz wydania (sprzedaży) towaru, zdano sobie sprawę już w roku 1932, kiedy to mała grupa studentów pod kierownictwem Wallach Flint’a wzięła udział w ambitnym projekcie automatyzacji punktów kasowych w supermarketach na Uniwersytecie Harwardzkim. Założeniem projektu było użycie karty perforowanej przez klienta, która później przekazywana do kontrolera, była umieszczana w czytniku. System automatycznie dostarczał produkt z magazynu do kasjera, rachunek był drukowany, a stan magazynu uaktualniany. Jednak dopiero siedemnaście lat po prototypowym rozwiązaniu zaproponowanym przez Wallach Flint’a, Norman Woodland i Bernard Silver, złożyli wniosek patentowy zatytułowany „Urządzenia i metody klasyfikacji”. Wynalazcy określili swój wynalazek, jako „sztuka klasyfikacji przedmiotów za pomocą identyfikacji wzorów” [1].
Pomysł kodowania zaproponowany w latach czterdziestych i obecnie funkcjonujący, jako kod kreskowy jest najpopularniejszą formą automatycznej identyfikacji towarów, materiałów, półfabrykatów, wyrobów oraz dokumentów. W dzisiejszych czasach nie sposób sobie wyobrazić sprzedaży, głównie detalicznej bez użycia kodów kreskowych, które z dnia na dzień zyskują coraz większa liczbę użytkowników w innych sektorach gospodarki. Prawie każdy wyprodukowany produkt opatrzony jest dziś kodem. Spotyka się go również na dokumentach, kopertach, dowodach rejestracyjnych, dowodach tożsamości, książkach a nawet opublikowanych drukach muzycznych. Kody kreskowe odgrywają bardzo istotną rolę przy automatyzacji procesów przyjęcia, przesunięć oraz wydań magazynowych, znacznie skracając czas potrzebny na rejestrację przyjęcia bądź wydania z magazynu, jednocześnie minimalizując ilość pomyłek.
Globalizacja i dynamika w rozwoju prowadzenia działalności gospodarczej „bez granic”, spowodowały gwałtowny wzrost znaczenia oraz funkcjonalności łańcucha dostaw, przyczyniły się do utworzenia nowych kanałów dystrybucji, zmiany we wzorcach popytu jak i rosnące oczekiwania klientów wobec świadczonych usług. Dążenie przez producentów oraz handlowców do przyśpieszenia dostawy towaru klientowi finalnemu, przy jednoczesnym zachowaniu jak najwyższej jakości (minimalizacja pomyłek w wydaniach, ograniczenie obsługi posprzedażowej), nadały decydujące znaczenie technologii informatycznej w procesach gospodarczych, a tym samym większe znaczenie zaczęto przypisywać kodom kreskowych, które od początku ubiegłego stulecia przeszły dużą zmianę.
Z biegiem czasu, użytkownicy najprostszych kodów kreskowych, które pozwoliły zautomatyzować handel detaliczny i hurtowy zaczęli odczuwać ograniczenia wynikające z ich budowy oraz ilości informacji, które w sobie zawierały. Powszechnie używana symbolika do znakowania opakowań jednostkowych i zbiorczych, kod EAN-13 (European Article Numbering – Europejski Kod Towarowy), odczytywany w punktach kasowych, pozwala jedynie na identyfikację towaru. W systemie EAN oprócz podstawowych kodów EAN-8 (7 cyfr danych i 1 cyfra kontrolna; umieszczany na opakowaniach jednostkowych, na których nie może się zmieścić kod EAN-13) i EAN-13 (zawiera 12 cyfr danych i jedną cyfrę kontrolną; umieszczany na opakowaniach jednostkowych oraz na jednostkowych opakowaniach transportowych typu karton) wykorzystywany jest także kod EAN-128 (umieszczany na zbiorczych opakowaniach transportowych typu paleta, skrzyniopaleta, półpaleta – DHP, itp.), który umożliwia zawarcie w numerze kodowym dodatkowych informacji (data produkcji, termin ważności, adres, numer serii, itp.) Poważnym problemem przy użytkowaniu kodu kreskowego, zgodnego z EAN jest fakt, że w momencie jego zatarcia, zagięcia, zamoczenia itp. odczyt danych poprzez system skanowania jest niemożliwy, a identyfikacja towaru następuje poprzez manualne wprowadzenie kodu do systemu przez użytkowania. Pociąga to za sobą zarówno straty czasowe, jak i finansowe.
W związku z wyżej wymienionymi ograniczeniami i problemami, dręczącymi rozwiązanie EAN-8 i EAN-13, powstał standard GS-128 (dawniej UCC/EAN-128, EAN 128), który ułatwił krajową oraz międzynarodową wymianę informacji jak i komunikację pomiędzy wszystkimi parterami w łańcuchu logistycznym, począwszy od dostawców surowców i półproduktów, przez producentów, dystrybutorów, hurtowników, detalistów a skończywszy na odbiorcach końcowych i konsumentach. Podstawowym atutem tej symboliki są tzw. Identyfikatory Zastosowania GS1. W nowoczesnej gospodarce występuje potrzeba nie tylko automatycznej identyfikacji dóbr, co umożliwiają symboliki EAN/UPC, ale również przedstawienia w postaci symboli kodu kreskowego informacji dotyczących np. daty trwałości, numeru serii produkcyjnej, miar handlowych i logistycznych, numerów lokalizacyjnych, relacji usługowych i innych informacji biznesowych. Służą temu właśnie standardowe Identyfikatory Zastosowania tzw. IZ. IŻ są to prefiksy, które jednoznacznie definiują znaczenie i format występujących po nich pól danych. Obejmujący wiele branż standard, poprzez wprowadzenie unikatowej etykiety dystrybucyjnej, pozwala na wykorzystanie informacji zawartych w kodzie GS1-128 w każdym zakątku świata bez konieczności wcześniejszego kontaktowania się ze sobą kontrahentów w celu uzgodnienia formatów danych, ułatwia identyfikację produktów, jednostek wysyłkowych, jednostek sprzedażowych oraz usprawnia procesy biznesowe.
W postaci kodu GS-128 może być przedstawiony kod SSCC (Serial Shipping Container Code) – Seryjny Numer Jednostki Wysyłkowej, który jest standardowym numerem identyfikacyjnym, stosowanym do identyfikacji jednostek transportowych (palet, skrzyń itp.). Numer seryjny jest nadawany tylko raz, w momencie formowania danej jednostki logistycznej. Etykieta dystrybucyjna zaopatrzona w ten kod, umożliwia indywidualne śledzenie przemieszczanych jednostek transportowych, dzięki połączeniu ruchu jednostki (załadunek, transport, wyładunek) i przepływu związanych z nimi informacji. Stosowanie kodu SSCC daje możliwość wdrożenia wielu różnych operacji na bazie jednostki transportowej np.: przeładunek, automatyczne przyjmowanie towaru, automatyczne skanowanie i wydawanie towaru itp. i może być stosowany przez wszystkich partnerów uczestniczących w łańcuchu dostaw. Seryjne numery jednostek transportowych, które są nadane przez nadawców przesyłek, można wykorzystywać we własnych systemach kontroli wewnętrznej i dystrybucji. Podobnie jak w przypadku pozostałych sposobów kodowania SSCC poprzez swoją unikatowość zapewnia jednoznaczną identyfikację jednostek transportowych, co umożliwia dostarczenie klientowi bieżących informacji o przepływie towarów
Problem ze stosowaniem kodów EAN oraz GS-128, ( np. w przypadku GS-128 w związku z zastosowaniem tak zwanych Identyfikatorów Zastosowania), wynika z ich wielkości umożliwiającej kodowanie różnorodnych zestawów danych, bardzo często jest zbyt duży z punktu widzenia stosowania go w niektórych sektorach (elektronika, telekomunikacja, farmacja, diagnostyka). Wielkość etykiety jest, ograniczeniem w stosowaniu kodu GS-128 w przypadku małych opakowań i małych produktów (elementy elektroniczne, telekomunikacyjne, fiolki, blistry z tabletkami, tubki z maściami itp.) a także tych o nieregularnych kształtach (świeże produkty rolne sprzedawane na sztuki, paczkowane artykuły spożywcze wędliny, mięsa, sery).
Rozwiązaniem powyższego problemu jest nowa dwuwymiarowa symbolika kodowa GS1 Data Matrix. Kody kreskowe drukowane są w postaci symboli kwadratowych lub prostokątnych. Symbol umożliwia zakodowanie znacznie większej ilości informacji niż przy użyciu kodów EAN oraz GS-128, wymagając do tego dużo mniejszej powierzchni. Mimo niewątpliwych zalet GS1 Data Matrix, należy pamiętać, że odczyt takiego kodu może być dokonany jedynie przez skanery obrazu dwuwymiarowego lub systemy wizyjne. Wiąże się także z większymi kosztami wprowadzenia tego typu kodowania, niż w przypadku kodów jednowymiarowych np. GS-128. Dodatkową niedogodnością jest małe rozpowszechnienie urządzeń skanujących, co ogranicza użyteczność tego standardu do ograniczonej grupy odbiorców.
Pomimo wyższych kosztów wdrożenia kodowania z zastosowaniem GS1 Data Matrix warto wspomnieć o zaletach tego systemu:
– system umożliwia umieszczenie kodów bardzo małej powierzchni
– kod może zawierać znaki specjalne np.: nawiasy, ukośniki, przecinki oraz pozostałe
znaki alfanumeryczne
– w kodzie można zawrzeć 1,5 kilobajta informacji w tym dane o producencie, dacie
produkcji, dacie ważności, numer serii, partię w produkcji itp.
– położenie znaku oraz kontrast nie ma wpływu na możliwość oraz prawidłowość odczytu
– sposób zapisu danych powoduje, że utrata nawet 20% kodu zapewnia pełny jego
odczyt
– kod umożliwia jednoznaczną identyfikację, daje bezpieczeństwo produktu oraz
zabezpiecza przed fałszowaniem.
Używanie rozbudowanego systemu kodów GS1 Data Matrix na produktach, opakowaniach zbiorczych bądź etykietach dystrybucyjnych, jest ważne z punktu widzenia zachowania możliwości automatycznego śledzenia ruchów i pochodzenia produktów w całym łańcuchu dostaw. Daje każdemu podmiotowi w łańcuchu gwarancję autentyczności wprowadzanych do obrotu towarów. Wdrożenie systemu kodowania jest ważne dla tych branż (spożywcza, produkcja leków, produkcja sprzętu medycznego), dla których konieczne jest śledzenie ruchów produktów wraz z wszystkimi dodatkowymi informacjami takimi jak numer serii, data produkcji, data ważności itp. w całym łańcuchu dostaw (traceability). Stosowanie kodów umożliwia zidentyfikowanie źródła pochodzenia, tożsamość i charakterystykę produktu odebranego szybko i dokładnie, kiedykolwiek zajdzie taka potrzeba (zasada jednego kroku wstecz). Śledzenie, które umożliwia kodowanie pozwala też na zlokalizowanie produktu w oparciu o specyficzne kryteria (np.: numer serii produktu), gdziekolwiek produkt ten się znajduje w całym łańcuchu logistycznym. Z punktu widzenia firm jest to bardzo istotne, aby mieć możliwość zidentyfikowania oraz zlokalizowania w każdym momencie, miejsca w łańcuchu dostaw, w którym znajduje się ich produkt, w celu wycofania z rynku oraz sprzedaży (zasada jednego kroku w przód).
Zastanówmy się, więc jakie są zalety oraz co można uzyskać i co nam gwarantuje wprowadzając kodowanie w łańcuchu dostaw dla producenta, dystrybutora, operatora logistycznego, hurtownika i odbiorcy końcowego. Przyjmijmy do naszej analizy obrót na rynku karmą dla zwierząt. Niby mało istotny towar, biorąc pod uwagę jak ważne jest śledzenie ruchów produktu farmaceutycznego w procesie logistycznym, ale w związku z rozpowszechnianą ogólnoświatową świadomością jakości towaru, również i to co dajemy naszym pupilom jest objęte rygorami dostarczania produktu na rynek o najwyższej jakości, gdzie cały łańcuch dystrybucji jest kontrolowany pod względem zachowania odpowiednich warunków transportu, magazynowania, dystrybucji itp. Zacznijmy więc od tego, że producent jest również dystrybutorem towaru i udało się mu wprowadzić jeden ze standardów kodowania w swoich fabrykach, zunifikowaną etykietę dystrybucyjną oraz przekonać operatora logistycznego i głównych odbiorców do wprowadzenia w swoim systemie WMS możliwości odczytu kodów na etykiecie dystrybucyjnej naklejanej na jednostce transportowej. Przyjmijmy, że będzie to paleta. W pierwszej części etykiety znajduje się logo firmy, jej adres. W drugiej w części zawarte są istotne dane o towarze, a więc nr EAN 13 towaru, ilość na palecie, data przydatności do spożycia, międzynarodowy numer jednostki wysyłkowej (SSCC). Etykieta może zawierać bardziej szczegółowe informacje takie jak o seria produkcyjna, masa, wariant produkcyjny, wymiary gabarytowe itp. W trzecim polu powtórzone są wybrane informacje z pola drugiego, zapisane w postaci kodu kreskowego. Dana informacja jest poprzedzona dwu-, trzy- lub czterocyfrową liczbą (identyfikator zastosowania) w nawiasie okrągłym, która informuje system o rodzaju zakodowanej informacji oraz o formacie jej zapisu. Ten właśnie kod jest ważny z punktu widzenia gospodarki magazynowej. Nasza paleta z towarem została opatrzona zunifikowaną etykietą u producenta, załadowana i znajduje się w tranzycie (transport od producenta do magazynu). Dzięki skanowaniu etykiety dystrybucyjnej i wprowadzeniu danych do systemu producent wie, co zostało załadowane, jaka partia oraz ilość, dystrybutor natomiast oprócz tych informacji może określić, kiedy dany towar zostanie dostarczony do magazynu. W obu przypadkach zarówno producent jak i dystrybutor mają gwarancję prawidłowości danych. Automatyczne skanowanie, w porównaniu do manualnego uzupełniania danych przez użytkowników systemu opartego 2% błędem, daje gwarancję prawidłowości danych. Dystrybutor na podstawie danych wprowadzonych w systemie przez producenta może sprzedawać towar, który jeszcze nie dojechał do magazynu, jak również przeprowadzić analizę czy dostarczony towar pokryje sprzedaż. Zamówienie na dodatkową partię towaru, która jest potrzebna do pokrycia zapotrzebowania rynku może, więc zostać dokonana przez dystrybutora zanim jeszcze pierwsza partia dotrze na magazyn. Dla dystrybutora jest to bardzo istotne z punktu widzenia kosztów i zarządzania zapasami. Czas reakcji znacznie się skraca, co pozwala na posiadanie niższych zapasów w magazynie dystrybucyjnym, czyli mniej „zamrożonego pieniądza”. Znajdujemy się teraz w punkcie, gdzie paleta dociera na magazyn i tu idealnym rozwiązaniem, aczkolwiek kosztownym jest wymiana EDI pomiędzy systemami dystrybutora oraz operatora logistycznego, ale ponieważ operator logistyczny nie ma w tegorocznym budżecie kwoty kilkunastu tysięcy na wprowadzenie EDI, własnymi siłami pracowników z IT w systemie WMS wprowadził możliwość skanowania etykiety dystrybucyjnej producenta, przetwarzania danych z tej etykiety do własnego systemu WMS, archiwizowania tych danych oraz monitorowania ruchów. O informacje z etykiety dystrybucyjnej zaraz po jej zeskanowaniu uaktualniany jest automatycznie system WMS operatora. Operacja przyjęcia
i rejestracji towaru w systemie jest szybsza, ponieważ dane przekazywane są w sposób bezpośredni, natychmiastowy do komputera lub innego urządzenia przetwarzającego
i przechowującego dane. Do systemu WMS operatora magazynowego zostaje wprowadzona dokładnie taka sama paleta, jaka została załadowana u producenta. Podobnie jak i przy załadunku u producenta tak i przy rozładunku eliminowane jest prawdopodobieństwo popełnienia błędu, kiedy dane takie jak kod produktu, data przydatności numer serii itp. są wprowadzane manualnie do systemu przez użytkowników. Oprócz wyeliminowania błędu ludzkiego mamy ograniczenie zużycia papieru, optymalizację zarządzania zespołem oraz zagwarantowanie wysokiego współczynnika jakości obsługi klienta dla przyjęcia dostaw (dostawy przyjmowane są szybciej oraz bezbłędnie). Nasza paleta z suchą karmą dla psów, która pokaże się na wydaniu będzie zawierać taka same informacje jak przy przyjęciu. Pobierana do zlecenia paleta poprzez kodowanie oraz skanowanie danych z etykiet daje na 100% poprawność pobierania metodą FEFO. Kodowanie ułatwia pracę operatorowi wózka. Nie musi się on bowiem zastanawiać czy pobiera właściwy towar, ponieważ system nie pozwala użytkownikowi innego wyboru. Identyfikując dane z etykiety dystrybucyjnej i przekazując taką informację do dystrybutora, operator logistyczny daje pełne i poprawne dane dotyczące dystrybucji towaru, a przy konieczności wycofania towaru z rynku gwarancję poprawności danych dotyczących miejsca dostarczenia danej partii produkcji.
Wprowadzenie kodowania na etykiecie dystrybucyjnej jest bardzo pomocne dla przeprowadzania inwentaryzacji. Komisje spisowe nie przystępują już do inwentaryzacji z startą papierów zawierających arkusze spisowe, kalkulatorami, długopisami lecz jedynie z skanerem, którym skanują etykietę dystrybucyjną i nanoszą zliczoną ilość towaru z palety. Wyeliminowany zostaje dodatkowy arkusz (najczęściej w xls), gdzie osoby wprowadzają ręczenie dane z arkuszy spisowych, eliminowane są też błędy powstające w procesie przenoszenia informacji z arkuszy do pliku (każdy z nasz wie jak ciężko jest czasami rozczytać kolegę i jak bolą oczy przy wpatrywaniu się w monitor, na którym przez kilka ostatnich godzin przesuwają się kolumny, wiersze, dane i tak w kółko). Na postawie takiego arkusza, generowany jest raport różnic poinwentaryzacyjnych opatrzony błędem ludzkim. Zastosowanie do inwentaryzacji etykiety dystrybucyjnej daje nam gwarancję, że dane, wprowadzane przez komisje spisowe do systemu są poprawne. Bezpośrednie i automatyczne przekazywanie danych do systemu, przetwarzanie ich i na koniec wygenerowany z systemu raport rozbieżności, daje nam pewność poprawnie przeprowadzonego spisu. W konsekwencji inwentaryzacja dla niewielkiego 6000 stanu magazynowego trwa niecałe 8 godzin (włącznie z korektami i raportami), a nie dwa dni.
Kod z etykiety dystrybucyjnej pozwala, więc nadzorować operatorowi ruch palety podczas wykonywanych wszystkich operacji magazynowych, kompletacji, dekompletacji, paletyzacji, etc. i przekazywanie do dystrybutora danych o statusie danej palety. Kod kreskowy stosowany w całym procesie magazynowym u operatora zastąpił częste ręczne wpisywanie lub sprawdzanie danych i ułatwił kontrolę nad systemem pracy i jego optymalnym zarządzaniem. Pozwala operatorowi na lepsze kontakty z klientem przez ułatwienie dostępu do właściwej i aktualnej informacji w znormalizowanej formie, co jest bardzo istotne z punktu świadczenia usług na satysfakcjonującym klienta poziomie. Wymagania klienta nawet, jeśli jest to dystrybutor karmy dla zwierząt są coraz większe, współczynnik jakości obsługi ciągle podnoszony, ponieważ przy dużej konkurencji na rynku oraz powszechnej globalizacji, zadawalający poziom 95% dla wskaźnika jakości obsługi klienta w całym łańcuchu dostaw jest już za niski.
Kodowanie w najprostszej postaci jest, więc najtańszą formą i najbardziej efektywną techniką wprowadzania danych do komputera. Wdrożenie kodowania wymaga inwestycji w: drukarki do etykiet kodów kreskowych, etykiet samoprzylepnych, kalki barwiącej do drukarki (ribon, daje on trwalszy druk niż korzystanie z papieru termicznego, na którym pozwala drukować większość drukarek), skanera do odczytu kodów kreskowych, oraz oprogramowanie drukujące etykiety i przetwarzające odczytane kody kreskowe. Stosowanie w wymianie biznesowej kodowania towarów, może przynieść usprawnienie operacji logistycznej, redukcję kosztów dokumentacji papierowej, skrócenie czasu składania oraz realizacji zamówień, zwiększenie dokładności i lepsze zarządzanie oraz kontrolę całego łańcucha dostaw. Firmy, którym udało się wdrożyć standardy kodowania na etykietach dystrybucyjnych, na opakowaniach jednostkowych, zbiorczych bądź transportowych, zauważają znaczne obniżenie kosztów, poprzez wykorzystywanie do komunikacji tego samego rozwiązania u wszystkich partnerów, przy zachowaniu swobody stosowania przez nich własnych wewnętrznych aplikacji oraz systemów, lepszą obsługę klienta, optymalne zarządzanie kapitałem ludzkim oraz zapasami, niższy stan zapasów i koszty pracy.
Kod kreskowy (oficjalnie istnieje około 250 standardów), czy będzie to najprostszy jednowymiarowy EAN czy najbardziej zaawansowany i kosztowny DataMatrix wypalany laserem na dowolnym elemencie, zadomowił się na stałe nie tylko w biznesie, ale także i naszym życiu codziennym. Jego forma, zawarte w nim dane czy treści, mają za zadanie sprawną identyfikacje oznakowanego produktu, przez co ułatwienie i przyspieszenie prowadzonego przez nas biznesu. Jego rozwój uzależniony jest już tylko od potrzeb, jakie przedstawi rynek. Powinniśmy mieć świadomość tego, iż ten drobny, niepozorny kawałek druku stoi u podstaw każdego łańcucha logistycznego, że bez niego ciężko by było wyobrazić sobie dzisiejszą gospodarkę ogólnoświatową i jakąkolwiek panowanie nad nią.
Jednego możemy być pewni, decydując się na prowadzanie działalności logistycznej, produkcyjnej czy handlowej będziemy musieli wybrać, lub choć otrzeć o któryś ze standardów kodów kreskowych, czy będzie to EAN/UPC, Codabar, ITF, Code 39, Code 128 itd.
[1] http://www.pwsk.pl/kody-kreskowe/historia-kodow-kreskowych/