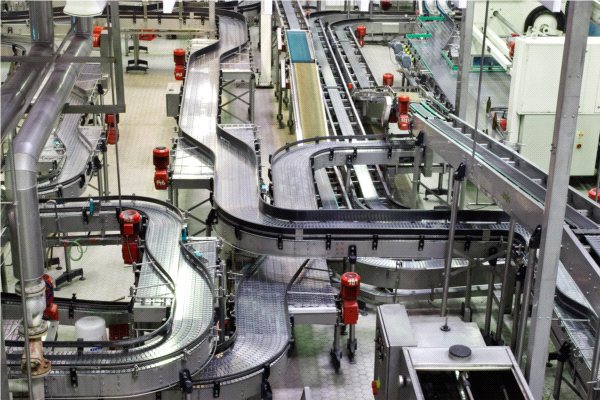
Zagrożenia Lean Manufacturing
Lean Manufacturing, koncepcja, filozofia, zestaw praktycznych narzędzi czy technik zarządzania produkcją, które przewróciły świat zarządzania do góry nogami.Termin „Lean” został po raz pierwszy użyty i wymyślony przez naukowców z Massachussets Institute of...
Termin „Lean” został po raz pierwszy użyty i wymyślony przez naukowców z Massachussets Institute of Technology. W 1991 roku opublikowali oni słynny światowy bestseller „The Machine That Changed the World” (maszyna, która zmieniła świat), książkę, którą czyta się jak kryminał, a w której to porównali parametry nakładów i wyników w przedsiębiorstwach japońskich, amerykańskich i europejskich. Za lidera uznali Toyotę – producenta japońskich samochodów. W ocenie nie chodziło tylko i wyłącznie o suche i bezduszne wskaźniki ekonomiczne. Toyota była zarządzana w oparciu o odmienne, bardziej skuteczne w praktyce metody zarządzania w stosunku do tych używanych przez amerykańską czy europejską konkurencję. Wyróżniała się także na tle przedsiębiorstw japońskich. System Produkcyjny Toyoty, a w zasadzie szczupła produkcja, czyli zastosowanie unikatowego podejścia do procesu produkcyjnego, był czymś, co wzbudzało fanatyczną zazdrość, podziw i chęć naśladownictwa.
W zasadzie to już w latach 80-tych po raz pierwszy Toyota przyciągnęła uwagę świata. Jednak do czasu opublikowania książki Lean Thinking mało kto wiedział, na czym polega System Produkcyjny Toyoty. Było jednak jasne, że Japończycy produkują samochody szybciej, bardziej niezawodnie, po konkurencyjnych kosztach, co było nie lada wyzwaniem biorąc pod uwagę wysokie płace japońskich robotników. Po lekturze Lean Thinking stało się jasne, że chodzi o sposób projektowania i wytwarzania, który charakteryzował się niewiarygodną spójnością procesu i produktu. To także sposób radzenia sobie z problemami, mówienia o nich i rozwiązywania ich w możliwie najkrótszym czasie. Toyota za każdym razem, kiedy ujawniała jakąś wyraźną słabość i wydawało się, że jest wystawiona na ciosy konkurencji, w cudowny sposób usuwała problem i dzięki temu wzmacniała się jeszcze bardziej.
Pięta achillesowa
Fundamentem lean jest metoda Just in Time (ang. dokładnie na czas), która jest masowo wykorzystywana w przedsiębiorstwach japońskich, europejskich i amerykańskich. Dzisiaj to standard branży motoryzacyjnej, ale nie tylko. Lean da się zastosować w każdej organizacji, nawet w skostniałych i bezdusznych urzędach. Przeanalizujmy krok po kroku reżim pracy, jaki funduje ta metoda producentom i dostawcom uczestniczącym w łańcuchu dostaw.
Just in Time tylko pozornie wydaje się prostą, szybką i łatwą metodą do wdrożenia. W rzeczywistości jest to bardzo skomplikowana koncepcja bez gwarancji sukcesu.
Just in Time ma m.in. na celu wyeliminowanie lub minimalizację poziomu zapasów i magazynów. Co to oznacza w praktyce? Przecież gdzieś czy u kogoś te zapasy muszą być składowane. Trzeba mieć materiały do produkcji (w końcu z czegoś trzeba produkować). Według JIT materiały znajdują się w magazynach dostawców i są dostarczane dokładnie na czas, wtedy kiedy są potrzebne, nieważne czy do gniazda, na strefę przyjęć czy na linię produkcyjną. Na czas oznacza w taki sposób, aby nie zakłócić przepływu produkcyjnego. Warunkiem koniecznym perfekcyjnego działania takiego modelu biznesowego jest współpraca z wiarygodnymi dostawcami. Konieczne staje się utrzymywanie z nimi silnych relacji, są oni bowiem bardzo ważnym elementem łańcucha dostaw. Cena jest ważna, ale nie jest jedynym kryterium podlegającym ocenie.
Aby skutecznie realizować koncepcję szczupłej produkcji, należy bardzo rygorystycznie podchodzić do kontroli jakości materiałów na wejściu
Jeżeli analizuje się zagrożenia wynikające z lean manufacturing, to dostawcy są prawdziwą pietą achillesową. Dlatego proces weryfikacji dostawców doczekał się procedur zawartych w takich standardach jak Odette czy MMOG/LE.
Problem z dostawcami może być monumentalny. Wie o tym Toyota, która traktuje swoich dostawców jak członków wielkiej rodziny – zupełnie inaczej niż przedsiębiorstwa amerykańskie. Drobne przerwy w dostawie materiałów tylko od jednego dostawcy w krótkim czasie mogą doprowadzić do wstrzymania produkcji. Podobnie problemy z błędnymi dostawami, niską jakością dostarczanych materiałów czy też nieterminowością dostaw są poważnymi zagrożeniami dla ciągłości produkcji.
Najbardziej znanym z historii przykładem „wpadki” związanej z dostawcami jest General Motors. Amerykański gigant został sparaliżowany przez siedemnastodniowy strajk dostawcy i nie miał wdrożonego planu awaryjnego na taką sytuację. Strajk doprowadził do kompletnego paraliżu całej firmy, ale nie tylko. Zatrzymanie linii produkcyjnych doprowadziło do wstrzymania dostaw od innych kooperantów i dostawców, którzy ponieśli kolosalne straty. Według szacunków General Motors stracił od 600 do 800 milionów dolarów zysku. Musiał tymczasowo zamknąć 2/3 swoich zakładów produkcyjnych, ale nadal ponosił koszty stałe. Po zakończeniu strajku dostawca pod silną presją GM miał przyśpieszyć produkcję. Tak się stało, ale kosztem jakości dostarczanych elementów, co nie odbyło się bez zwiększonego poziomu awaryjności i w konsekwencji kolejnych problemów GM.
Aby ustrzec się przed tego typu zakłóceniami, producenci działający w modelu Just in Time wdrażają plan awaryjny, który ma ich zabezpieczyć przed strajkami, powodziami, pożarami, złymi warunkami atmosferycznymi, korkami na drodze, wypadkami oraz innymi problemami.
Wewnętrzne zagrożenia
Zagrożenia z lean manufacturing to nie tylko i wyłącznie zagrożenia zewnętrzne. To także zagrożenia wewnętrzne. Źródłem zakłóceń zaburzającym przepływ może być sama organizacja. Menedżerowie fabryki muszą nauczyć się zarządzać i takimi zagrożeniami. Należy znaleźć odpowiedź na proste pytanie: co się stanie w przypadku kiedy awarii ulegnie maszyna w gnieździe produkcyjnym? Przecież zakład nie ma magazynów, nie ma gdzie składować materiałów, które jadą do fabryki lub są właśnie przyjmowane. Jeżeli maszyny nie zostaną szybko naprawione lub nie wstrzyma się dostaw materiałów, linie ulegną zakorkowaniu, drogi transportowe, strefy dostaw będą „zawalone”. Firma musi nauczyć się zarządzać taką sytuacją.
Warunkiem osiągnięcia sukcesu z wdrożenia lean manufacturing jest inwestycja w wiedzę, która fundamentalnie zmieni sposób myślenia, prowadząc od przedsiębiorstwa tradycyjnego do szczupłego
Organizacja powinna mieć również wewnętrzne procedury w sytuacji, gdy nie przyjdzie do pracy większa liczba pracowników, będzie dłuższa przerwa w dostawie energii elektrycznej itd., czyli na wypadek zagrożenia płynności produkcji.
Stosowanie lean manufacturing wymaga umiejętności skutecznego działania w warunkach gwałtownego wzrostu popytu. Praktykując Just in Time trudno jest zaspokoić większe zapotrzebowanie na materiały przy błyskawicznym wzroście potrzeb konsumentów.
Kontrola dostaw
Aby skutecznie realizować koncepcję szczupłej produkcji, należy bardzo rygorystycznie podchodzić do kontroli jakości materiałów na wejściu. Nie chodzi tutaj o generowanie ton papierowych dokumentów, jak to funduje nam ISO, ale o realne, fizyczne, skuteczne działania. Permanentne audyty dostawców, kontrolę i nadzór nad wdrożeniami elementów dostarczanych przez kooperantów. Kontrola jakości w momencie dostawy materiałów to bardzo dobra praktyka biznesowa w świecie magazynów, jednak w świecie bez magazynów może być już za późno. Kontrola jakości na linii produkcyjnej powinna być zastąpiona samokontrolą, nawet kosztem zatrzymania linii produkcyjnej. Ma to na celu minimalizację liczby błędnie wyprodukowanych detali, zespołów, podzespołów, wyrobów gotowych. Musi to być element ciągłej edukacji. Przykładem mogą być Amerykanie analizowani w początkowym okresie transformacji przedsiębiorstw w kierunku lean. W jednej z firm na liniach produkcyjnych zainstalowano czerwone przyciski do zatrzymywania procesu produkcyjnego. W początkowym okresie wdrażania lean przyciski były wykorzystywane do zatrzymywania procesu, ale w celu generowania przerwy w pracy. Mentalność Japończyków jest nieco inna od europejskiej czy amerykańskiej, nie akceptują oni marnotrawienia czasu, dlatego wynaleźli m.in. metodę szybkich przezbrojeń SMED (ang. Single Minute Exchange of Die).
Drobne przerwy w dostawie materiałów tylko od jednego dostawcy w krótkim czasie mogą doprowadzić do wstrzymania produkcji
Podczas gdy cały świat wykorzystywał produkcje masową, ekonomię skali i potężne maszyny do produkcji części w dużych partiach i po najniższym koszcie, jak to tylko możliwe (oczywiście tym koszcie wykazywanym przez analityków na papierze czy tym zarejestrowanym w systemie klasy ERP), Toyota wbrew ekonomii postawiła na elastyczność procesu produkcyjnego. Japoński producent opracował zespołowy proces redukujący czas przezbrojenia maszyny w celu zwiększenia czasu przeznaczonego na produkcję i zmniejszenia, a nie zwiększenia – jak podpowiada świat ekonomii – partii produkcyjnej, zmniejszenia ilości zapasów, czasu przejścia (ang. Leadtime) oraz realnych kosztów produkcji.
Potrzeba zmiany mentalności
W Stanach Zjednoczonych wielokrotnie badano organizacje, które wdrożyły lean manufacturing. Pewien wątek przewijał się od lat. Warunkiem osiągnięcia sukcesu z wdrożenia lean manufacturing jest inwestycja w wiedzę, która fundamentalnie zmieni sposób myślenia, prowadząc od przedsiębiorstwa tradycyjnego do szczupłego. Trzeba stworzyć warunki do powstania organizacji samouczącej się, potrafiącej rozmawiać o problemach, dostarczając w możliwie krótkim czasie właściwych rozwiązań, nawet kosztem przerwania produkcji. Słabe zrozumienie lean prowadzi do nieuzasadnionych oczekiwań, które w rzeczywistości nie są spełniane, a w konsekwencji do niezadowolenia.
Zagrożenia wynikające z wdrożenia tej metody wynikają ze zmian mentalnościowych, które mogą kompletnie zaburzyć przepływ materiałów na hali produkcyjnej. Sposób myślenia należy zmienić ekonomistom, którzy na koszty produkcji patrzą jedynie przez pryzmat ekonomii skali. Mentalność trzeba zmienić dyrektorom produkcji, planistom i ustawiaczom odpowiedzialnym za przezbrojenie, które nie jest przerwą na kawę i nie musi trwać kilka godzin czy wręcz dni. Toyota udowodniła, że duże prasy można przezbrajać w czasie do dziesięciu minut. Produkcja w dużych partiach jest niebezpieczna i nieopłacalna. Jak jednak zachowa się szczupły system produkcyjny, kiedy dostanie decyzję o wyprodukowaniu czegoś w dużej partii?
Zagrożeń płynących z wdrażania lean manufacturing jest więcej. W niniejszym artykule zasygnalizowano zaledwie kilka. Jednak ile by ich nie było, nie ma na świece lepszej, bardziej skutecznej metody zarządzania produkcją. To jedyna metoda zarządzania na świecie, która została opracowana przez praktyków i sprawdzona w praktyce. O skuteczności jej świadczy fakt, że jest wdrożona lub wdrażana w bezpośredniej konkurencji Toyoty , w firmach z sektora motoryzacji. Poprawnie wdrożona i zarządzana generuje gigantyczne korzyści dla firm. Warto znać zagrożenia i najlepsze praktyki biznesowe. Pytanie czy wdrażać lean jest nieco spóźnione, o kilkanaście czy kilkadziesiąt lat, ale lepiej pytać późno niż wcale. Wielu krajowych producentów uważa, iż ich firmy są szczupłe, podczas gdy w rzeczywistości wcale tak nie jest. Wdrażają oni pojedyncze elementy lean manufacturing, takie jak 5S czy TPM. To jeszcze nie jest lean manufacturing, to zaledwie początek drogi.