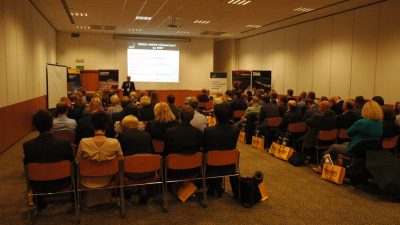
Relacja z konferencji Focus Factory 2015
Logistyka Produkcji wspólnie z MPM Productivity Management 23 czerwca 2015 zaprosiły menedżerów sektora produkcji na unikatową konferencję. Focus Factory miał pokazać zainteresowanym jak duże błędy popełniane są w firmach produkcyjnych, jak poważne są konsekwencje nieprzemyślanych decyzji – ale i co robić, gdy wszystko poszło nie tak, jak należy. Ponad setka zgłoszeń upewniła organizatorów, ze pomysł na tak nietypowy program nie był chybiony.
Imprezę otworzyli Adam Błuś z Wydawnictwa Eurologistics, Zbigniew Sobkiewicz z MPM Productivity Management, oraz Witold Zygmunt z Logistyki Produkcji. Po powitaniu gości przestawiono genezę projektu oraz zachęcono do wyrażania swoich uwag na temat wygłaszanych prelekcji.
Zaskoczyć problemy
O Sales&Operational Planning, trudnej, ale bardzo skutecznej praktyce, pozwalającej zarządzać procesami produkcji i magazynowania w warunkach zmiennego popytu mówili Zbigniew Sobkiewicz oraz Krzysztof Spring z firmy Rotom. Rotom zajmuje się dostarczaniem produktów do przechowywania oraz transportu towarów. W ofercie znajdują się przede wszystkim palety, pojemniki oraz inne nośniki służące do transportu.
Biznes paletowy wiąże się z wieloma wyzwaniami. Jednym z głównych problemów jest sinienie palet, co wiąże się z szybką utratą ich wartości, zaś konserwacja wyrobów jest kosztowna. Należało zatem znaleźć sposób na takiej planowanie produkcji, aby uniknąć zalegania zapasów w magazynie, a zarazem być w stanie odpowiedzieć na zmienne zapotrzebowania klientów.
Kolejne poważne kłopoty sprawiała współpraca z kooperantami. Długie kontrakty i ograniczone możliwości w pozyskiwaniu drewna stawiały dostawców w silnej pozycji. Głównym wyzwaniem było sprostanie sezonowym zmianom zapotrzebowania klientów. W listopadzie popyt niemal przekraczał zdolności produkcyjne i sytuacja stawała się krytyczna.
Jak można wyjść z tej trudnej sytuacji i zaskoczyć problemy, aby problemy nie zaskoczyły nas? Sales&Operational Planning jest rozwiązaniem, ale wyzwaniem okazuje się jego skuteczne wdrożenie. Proces ten wymaga bezwarunkowego wsparcia ze strony zarządu i najlepiej jest, gdy prowadzi go osoba zajmująca czołowe stanowisko. W przeciwnym wypadku wdrożenie rozmywa się, brakuje dbałości o szczegóły, a nawet jeśli początkowo widać efekty, S&OP potrafi obumrzeć.
W Rotomie udało się jednak wyjść z trudnej sytuacji, czego dowodem były zaprezentowane dane na temat aktualnego stanu zapasów. Najważniejszą lekcją, którą poznali uczestnicy konferencji, był jasny komunikat: do sukcesu S&OP niezbędne jest bezwzględne zaufanie wszystkich członków organizacji.
W gąszczu SKU
Dariusz Dudek z Nordglass oraz Bogusz Dworak z MPM Productivity Management przedstawili studium przypadku dotyczące trudności z planowaniem w fabryce znanego dostawcy szyb samochodowych. Nordglass, oferujący szyby czołowe do samochodów osobowych, działa głównie na rynku aftermarket, przez co planowanie produkcji i zapewnienie dostępności wyrobów staje się koszmarem. A klienci zawsze chcą, aby szyba już na nich czekała w serwisie.
Nordglass posiada centralę w Polsce, u nas skupiona jest również produkcja (dwa zakłady), ale obsługiwane są wszystkie rynki europejskie, rozpoczyna się także ekspansja poza nasz kontynent. Sama oferta na polski rynek to ponad 2200 SKU, strategia Make to Stock zakłada pełną dostępność od ręki – i w przypadku popularnych modeli samochodów udaje się ją realizować, zaś w przypadku mniej popularnych modeli szyby dostarczane są do serwisu w ciągu 24 godzin.
Jak jednak zarządzać i planować produkcję w sytuacji, gdy znajduje się w niej 3000 SKU? Ogromna ilość modeli samochodów skłoniła Nordglass do sięgnięcia po kategoryzację ABC. Jednak okazało się, że nie zmieniło to znacząco sytuacji – zazwyczaj do kategorii A trafia niewielka ilości wyrobów, tymczasem zakwalifikowano do niej ponad 700 SKU.
Problem nie został rozwiązany w ten sposób, ale kategoryzacja ABC pomogła podczas wdrożenia S&OP. Podjęto wówczas decyzję o alokowaniu ograniczonych zdolności, budowaniu zapasów i zarządzaniu ograniczeniami produkcyjnymi pod sezonowy popyt. Z kolei w procesie prognozowania skupiono się na kategorii A. Przygotowano harmonogram produkcji zamrożony na 7 dni, lecz jego szczegóły przekazywano na produkcję raz na dzień, co skróciło lead time i dało większą kontrolę nad WIP. Upór, pracowitość i odwaga sprawiły, że Nordglass uporał się z problemami i notuje świetne wyniki dostępności wyrobów.
Czy zaufać dostawcom?
Tomasz Sokołowski z MPM Productivity Management dla odmiany pojawił się samotnie i pochylił się nad zagadnieniem udziału dostawców w uzupełnianiu zapasów metodami nieopartymi na MRP. Idea brzmi kusząco, ale prelegent zastanawiał się, czy takie uproszczenie łańcucha dostaw w praktyce ma szanse na sukces.
Goście konferencji przyznali, że narzekania na problemy związane z zaopatrzeniem produkcji pojawiają się także w ich firmach, Brak zapasów do produkcji skłania do przeniesienia odpowiedzialności za ich uzupełnienia na dostawcę. Trzeba jednak zastanowić się, czy taka decyzja uwolni nas całkowicie od zarządzania tym procesem, a zarazem rozwiąże problem.
Pan Tomasz zaznaczył, że mówiąc o udziale dostawców w uzupełnianiu zapasu nie można abstrahować od wewnętrznych zasad obrotu materiałowego w przedsiębiorstwie. Wskazane zostały metody uzupełniania zapasów nieoparte na MRP i powody ich stosowania. Najważniejszą rolę gra tu możliwość obniżki kosztów oraz uwolnienia się od części zadań administracyjnych. Metody to stosowane są najczęściej do drobnych elementów złącznych, elektrycznych, klejów, olejów czy farb.
Nie brak jednak i wad tych metod, jak konieczność regularnego raportowania zużycia materiałów, konieczność zaangażowania osób z produkcji do czynności związanych z zakupami czy trudne wdrożenie przy wielu SKU. Aby włączyć w ten proces dostawców, niezbędne jest posiadanie z nimi partnerskich relacji oraz ustalenie jasnych warunków współpracy.
Pułapka za pułapką
O pięknej katastrofie mówili Konrad Grondek z MPM Productivity Management oraz Przemysław Bartniak. Pan Przemysław pracuje w firmie z branży meblarskiej, związanej z szeroko pojętą edukacją i wyposażającą placówki edukacyjne w elementy wystroju pomieszczeń oraz placów zabaw, materiały wykorzystywane przy edukacji umysłowej i ruchowej jak i materiały multimedialne.
Nie mogliśmy poznać nazwy firmy, ale dowiedzieliśmy się, jak działa jak zakład produkcyjny i przekonać się, jakie braki organizacyjne kryją się w jego zakamarkach. Konieczność reorganizacji była kluczowa i w celu zoptymalizowania zadań zdecydowano się na wykorzystanie narzędzia Werbel-Bufor-Linia szeroko znanej metody zarządzania – Teorii Ograniczeń.
I tutaj zaczęła się seria pułapek, o których nie wspomina sie w książkach, a które stanowią drogę do katastrofy. Związane są one z koniecznością ciągłego gaszenia pożarów na produkcji co powoduje chaos w harmonogramie, koniecznością pilnowania miksu czy terminowym zamawianiem materiałów do bufora na właściwym etapie. Największą pułapką jest jednak to, że Werbel-Bufor-Lina w żaden sposób nie przewiduje sezonowości produkcji.
Wyciągnąć z tej pułapki może nas S&OP. W firmie Pana Przemka wdrożono zintegrowane planowanie MRPII, dzięki czemu zaczyna już działać prognozowanie Odbyły się pierwsze spotkania S&OP i powstaje plan MPS na produkcję i towary.
Królestwo, w którym źle się dzieje
Marek Repiński z MPM Productivity Management w kolejnym ciekawym wystąpieniu przestawił anty-przykład, czyli bajkę z życia wziętą. Bajka o nieudanym cięciu kosztów nie toczyła się w królestwie położonym za siedmioma lasami, ale w firmie produkcyjnej z branży automotive, w której podjęto decyzję o wdrożeniu projektu redukcji kosztów operacyjnych. Choć proces ten trwał już osiem miesięcy, wciąż nie było widać zakładanego efektu, czyli obniżki kosztów operacyjnych o 15%.
Prelegent opowiedział o strukturze królestwa, czyli o firmie, a w szczególności o magazynie, w którym zamierzano wprowadzić usprawnienia. Skupiono się zatem na wyodrębnieniu operacji generujących największe obciążenie. Analiza wskazała, iż największa ilość czasu poświęcana na procesy zaopatrzenia produkcji – czyli kompletację materiałów oraz transport na stanowiska. Zadania te zostały dokładnie rozpisane, goście dowiedzieli się, jak są one uwzględnione w systemach ERP i WMS i jak wygląda ich realizacja. Jeszcze bardziej dokładne poszukiwania przyczyn problemu wykazały, iż powtarza się konieczność oczekiwania w kolejce przy kasie (gdzie rejestrowane było wydanie materiału z magazynu na produkcję).
Kierownictwo firmy rozważało trzy opcje eliminacji tego problemu; zatrudnienie dodatkowego kasjera, co wprost kłóciło się z ideą obniżenie kosztów personalnych; wydawanie z pomocą skanerów, co także oznaczało wzrost kosztów; oraz eliminację kasy. To opcja wydawała się najrozsądniejsza, gdyż dokładna organizacja procesu nie miała znacznie dla jakości obsługi końcowego klienta, zaś działająca zasada FIFO i zmiany w ERP miały zapewnić automatyczną konsumpcję materiałów.
Na początku wszystko wyglądało dobrze, redukcja zatrudnienia wpłynęła na obniżkę kosztów. Bajka skończyła się jednak bardzo źle – wyeliminowanie kasjerów zakończyło się bałaganem na produkcji. Pojawiły się uszkodzenia materiału, kłopoty z ich identyfikacją, a nawet konieczność fizycznego liczenia materiałów przed zakupami. Zasada FIFO praktycznie przestała istnieć, co wymusiło korektę planu produkcyjnego. Na koniec prelegent zasugerował inne sposoby na przeprowadzenie procesu redukcji kosztów, dające szanse na realną poprawę sytuacji.
Nauka przywództwa
Gość specjalny konferencji, Egge Haak, na godzinę przed wystąpienie lądował dopiero w Warszawie. Na szczęście obyło się bez problemów komunikacyjnych i twórca symulatora The Fresh Connection mógł przedstawić swoje poglądy na to, jak należy skutecznie się uczyć i przekuwać wyniki tej nauki w efektywne zarządzanie organizacjami biznesowymi.
Na początku Pan Egge zaprezentował kilka ciekawych, ale i zatrważających statystyk. Na przykład 82% pracowników nie widzi żadnego powiązania między strategią firmy a swoimi codziennymi obowiązkami. Co więcej, 59% menedżerów w ogóle nie rozumie strategii przedsiębiorstwa. Nauka jest zatem niezbędna, aby osiągnąć sukces.
Tylko 10% naszej wiedzy pochodzi jednak ze szkoły. 20% uczymy się od naszych współpracowników, zaś 70% nabywamy podczas pracy. Jest to zatem najskuteczniejszy sposób nauki, ale potrafi być bolesny. Opiera się on bowiem na metodzie prób i błędów, które często są bardzo kosztowne. Nieraz też trudno jest powiązać związki przyczynowo skutkowe i wyciągnąć właściwe wnioski.
Te wszystkie czynniki skłoniły Egge Haaka do stworzenia The Fresh Connection – symulatora biznesowego, pozwalającego na eksperymentowanie w bezpiecznych warunkach i poznanie sieci zależności biznesowych. Uwzględnia on wszystkie rodzaje nauki – zajęcia klasowe są niezbędne, bowiem nie wszystkiego nauczą nas eksperymenty. Prelegent pokazał, jak działa idea „blended learning”, lawirująca między systemami nauki pchanej i wyciąganej, opartej na kontekście oraz na kompetencjach.
Nagrody dla mistrzów
Egge Haak przybył jednak do Warszawy nie tylko aby opowiedzieć o sposobach nauki. Wręczał on także nagrody dla triumfatorów polskiego finału The Fresh Connection – Open Competition. Zwycięska okazała się drużyna z PKN Orlen z Obszaru Zarządzania Łańcuchem Dostaw. W jej skład weszli Marta Jaroni, kierownik Biura Planowania Dystrybucji; Anna Kowalska, kierownik Biura Efektywności Realizacji Planu Operacyjnego; Robert Reńda, kierownik Biura Prognozowania i Analiz Rynkowych oraz Wojciech Bujak; dyrektor Biura Prognozowania i Analiz Rynkowych.
Zespół PKN Orlen nie tylko okazał się najlepszy w Polsce, ale też zanotował najwyższy ROI ze wszystkich ekip na świecie biorących udział w eliminacjach lokalnych. Reprezentanci Orlenu we wrześniu pojadą na światowy finał The Fresh Connection – Open Competition w Amsterdamie, dodatkową nagrodą dla nich jest seria warsztatów o wartości 60 000 zł.
TFC w praktyce
Ostatnia część konferencji miała na celu przybliżenie gościom symulatora The Fresh Connection w praktyce. Co więcej, dzięki głosowaniu brali oni udział w podejmowaniu decyzji biznesowych i mogli przekonać się, jak wpływają one na efekty.
Symulację poprowadził Zbigniew Sobkiewicz, a uczestnicy wydarzenia stali się członkami zarządu firmy „The Fresh Connection” – producenta soków owocowych. Znalazł się on w kiepskiej sytuacji, wskutek nieodpowiedniego poziomu zapasów, wysokich kosztów produkcji, sporej ilości obsolitów i budzącej zastrzeżenia postawie dostawców. Efektem było niezadowolenie klientów.
Przed rozpoczęciem symulacji, prowadzący przedstawił kilka ważnych cech, które należy uwzględnić w zarządzaniu przedsiębiorstwem z tej branży. Następnie rozpoczęła się symulacja, która odzwierciedlała proces naprawczy trwający pół roku. Zadaniem uczestników było uzyskanie maksymalnego ROI.
Goście konferencji podejmowali decyzje w obszarze zakupów, operacji, sprzedaży i zarządzania łańcuchem dostaw. Można było m.in. zwiększyć magazyn, usprawnić linie produkcyjne, wybrać dostawcę oferującego tańszy surowiec ale wymagający dłuższego transportu. Każdorazowo znane były koszty, ale i efekty poszczególnych zmian. Po serii procesów decyzyjnych program zaprezentował ich efekty. Czy ROI się poprawił? No cóż, powiedzmy tylko, że uczestnicy przekonali się, że ich decyzje jednak nie były optymalne.
Podziękowania
Na koniec pozostaje nam tylko podziękować uczestnikom za przybycie i zaangażowanie w ten nowatorski projekt. Dziękujemy również MPM Productivity Management oraz towarzyszącym im menedżerom firm produkcyjnych za przygotowanie niezwykle ciekawego programu i odwagę w mówieniu o niepowodzeniach biznesowych. Ukłony kierujemy ponadto w stronę partnerów wydarzenia – firm Dachser, NordGlass i Rotom.
Zdjęcia z konferencji można obejrzeć na stronie Logistyki Produkcji
Galeria zdjęć do artykułu
Pliki do pobrania
zarejestruj się by uzyskać bezpłatny dostęp do materiałów z konferencji. W ten sposób dbamy o polepszanie jakości naszych usług i dostarczanych do Ciebie materiałów. Rejestracja oznacza akceptację aktualnej polityki prywatności.