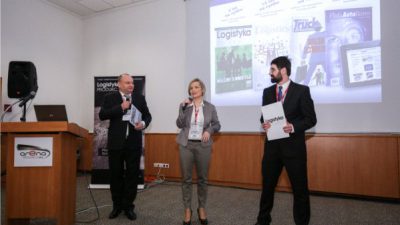
ARENA PRODUKCJI 2015
Ponad 150 menedżerów i specjalistów produkcji uznało, że warto poszerzać praktyczną wiedzę na temat nowoczesnych i innowacyjnych metod zarządzania produkcją. Źródłem cennych informacji z tej dziedziny była dla nich Arena Produkcji – wyjątkowa konferencja, która odbyła się 16 kwietnia 2015 w hotelu Novetel Airport Warszawa.
Zorganizowane przez czasopismo Logistyka Produkcji oraz Wydawnictwo Eurologistics wydarzenie miało za zadanie zaprezentować najnowsze, praktyczne metody doskonalenia produkcji, wskazać źródła marnotrawstwa a także zastanowić się nad tym, w jakim kierunku będą się rozwijać fabryki. Za sukces konferencji oprócz sesji wykładowych odpowiadały indywidualne rozmowy prowadzone przez gości konferencji, ekspertów i partnerów. Podczas zorganizowanej sesji crowdsurcingowej – a także tradycyjnie przy okazji spontanicznych spotkań w przerwach imprezy – nawiązano szereg cennych kontaktów, wymieniono wiele uwag, doświadczeń oraz wyciągano wspólnie wnioski.
Przyszłość jest inteligentna
Po otwarciu konferencji przez organizatorów, pierwsze wystąpienie poprowadził Janusz Pieklik z Business Global Consulting. Ekspert w zakresie systemów klasy ERP, zarządzania produkcją, Lean Manufacturing i Lean Logistics tym razem postanowił przyjrzeć się temu, jak będzie zmieniał się świat produkcji w najbliższych latach, jakie trendy zyskają decydujące znaczenie oraz na kim warto się wzorować – Chciałbym przenieść Państwa do przyszłości a potem sprowadzić na ziemię – oświadczył prelegent.
Wystąpienie rozpoczęło kontrowersyjne pytanie – czy warto wydawać pieniądze na innowacje? Prowadzący pokazał jakie niewielki procent dochodów na rozwój i badania wydaje Apple, najbardziej innowacyjna firma świata według raportu Booz&Co. Gościom zaprezentowano kilka najbardziej innowacyjnych produktów, które do niedawna znajdowały się tylko w sferze marzeń – jak procesor neuronowy, Toyota Mirai napędzana wodorem, biofarmaceutyki czy też dostępne już od kilku lat elektryczne samochody Tesla. Niewątpliwą rewolucją staje się drukowanie 3D, które z miana ciekawostki przechodzi do roli technologii realnie użytecznej dla firm produkcyjnych, Janusz Pieklik przypomniał, jak duże znaczenie wciąż mają dla fabryk zasoby ludzkie, ale podkreślił gwałtowny rozwój robotyzacji.
Skąd zatem wychodzą najlepsze pomysły na innowacje? Zdaniem prelegenta, na pewno nie od osób które mają za sobą najbardziej cenione uczelnie dla menedżerów. „Jeśli tylko to możliwe, unikaj zatrudniania absolwentów zarządzania. Programy MBA nie uczą jak tworzyć przedsiębiorstwa” – powiedział Elon Musk, założyciel Tesli i PayPala. Innowacyjność firm zabijają menedżerowie, mający tylko zdolności wykonawcze, a świat rozwija się dzięki szaleńcom, jak Thomas Edison, Henry Ford czy Stebe Jobs. Na potwierdzenie tej tezy prowadzący przedstawił drzewa konfliktu występujące w przedsiębiorstwach.
Jak więc będzie wyglądać Produkcja IQ? Dominująca stanie się rola systemów informatycznych i automatyki, rozwinie się sztuczna inteligencja. Ogromne znacznie zyskają precyzyjne dane z fabryk. W związku z tym już teraz trzeba kompletnie zmienić podejście do zarządzania danymi, trzeba przestać ignorować ich obecność i wpisywać co się chce i kiedy się chce – a to obecnie plaga w fabrykach. Dzięki temu systemy będą mogły nie tylko gromadzić dane, ale tez podejmować decyzje.
Efektywność energetyczna nie jest opcją
Po spojrzeniu w przyszłość, wróciliśmy do problemu spotykanego na co dzień. Marcin Wieruszewski z Centrum Energetyki i Techniki zwrócił uwagę gości konferencji na rosnące wydatki na energię elektryczną i media. Przedstawił jednocześnie kilka metod, pozwalających na poprawę efektywności energetycznej firm produkcyjnych.
Optymalizacja efektywności to nie tylko kwestia prostego rachunku ekonomicznego. Dyrektywa Parlamentu Europejskiego z 2012 roku zakłada 17% wzrost efektywności energetycznej do roku 2020. To i tak niższa wartość niż ta przewidziana w pakiecie klimatyczno-energetycznym 20/20/20, lecz skutkiem tych przepisów są nieuniknione dalsze wzrosty cen prądu.
Prelegent przedstawił przykładową fakturę za prąd oraz jej składowe. Zwrócił uwagę zwłaszcza na znaczącą pozycję, jaką stanowi opłata, a w istocie kara za moc bierną przesyłaną do zakładu. Czynnik ten można wyeliminować dzięki prostym działaniom, jak montaż baterii kondensatorów. Kolejnym sposobem na oszczędności jest wprowadzenie dokładnych pomiarów zużycia mocy i analiza wyników. Przestawione przykłady pokazały, jak można w ten sposób odnotować nieprawidłowości w pracy maszyn, nieprzestrzeganie procedur przez pracowników czy też skorelować plan taryfowy i godziny pracy zakładu. Inne wykresy pozwoli przekonać się, jak na zużycie prądu wpływa tempo podawania surowców do obrabiarki oraz stan narzędzi.
Prowadzący omówił tez kwestię jakości energii i wpływające na nią czynniki, metody pomiarów oraz korzyści, wynikając z analiz krótkotrwałych jak też ciągłej kontroli parametrów.
Nadzór zamiast decyzji
Temat inteligentnej produkcji rozpoczął a także zakończył pierwszy blok wykładowy. Krzysztof Fiegler z firmy UIBS Teamwork Sp. z o.o. zaprezentował IPOSystem – innowacyjny system zarządzania produkcją. Korzyści wynikające z jego stosowania można było poznać na podstawie wdrożenia przeprowadzonego w Andrychowskiej Fabryce Maszyn Defum SA.
Czy charakteryzuje się inteligenta fabryka? Zdaniem prelegenta posiada ona możliwość produkcji pojedynczych produktów pod indywidualne potrzeby klienta, zdolność szybkiej i automatycznej adaptacji do ciągłych zmian, wysoką efektywność wykorzystania zasobów, zapasów i energii oraz możliwość łączenia ze sobą procesów realizowanych w różnych halach produkcyjnych, a nawet przedsiębiorstwach w inteligentne sieci, które same się optymalizują.
Wdrożony w AFM Defum IPOSystem pozwala na automatyczną aktualizację (w zaledwie kilka sekund) harmonogramu po każdym zdarzeniu na hali produkcyjnej i w obszarze wokół produkcyjnym oraz inteligentne i samodzielne sterowanie procesami. System przekazuje zlecenia dla pracowników za pomocą terminali, zlokalizowanych na hali produkcyjnej. Zlecenia, wygenerowane na podstawie harmonogramu, pozwalają na wykonanie przez pracownika tylko określonego zadania i tylko na danym stanowisku. Planiści zamiast podejmowania decyzji skupiają się na nadzorze systemu, który w miarę pojawiania się nowych zamówień zmienia harmonogram produkcji.
Jakie korzyści odnotowano w AFM defum po wdrożeniu? Średni wzrost wydajności pracy pracowników bezpośrednio produkcyjnych po pierwszym roku użytkowania systemu wyniósł 17%. Elastyczność wzrosła o ponad 100%, zapewniono terminowość dostaw i zyskano pełną i bieżącą informację o koszcie wytworzenia. Zysk w 2014 r. w stosunku do 2011 r. wzrósł o 733%.
Sporo o MRP
Robert Głos, praktyk z dużym doświadczeniem w zarządzaniu produkcją, omawiał nowoczesne metody zarządzania produkcją. Jak sam przyznał, można mieć wątpliwości co do nowoczesności modeli liczących sobie kilkadziesiąt lat. Jednak metody MRPII i tak są młodsze niż podwaliny filozofii Lean, wciąż uznawanej za innowacyjną.
Prelegent rozpoczął swoje wystąpienie od prezentacji ewolucji modelu MRP – od harmonogramowania dostaw materiałów pod wdrożenia systemów ERP. MRP to komputerowy system informacyjny, który harmonogramuje i zamawia zapas asortymentów, ze względu na popyt zależny. Program wykorzystuje główny harmonogram produkcji, BOM-y i rejestry stanów magazynowych jako swoje wejścia, zaś dane wyjściowe obejmują rozpoczęcie realizacji nowych zleceń i przeharmonogramowanie otwartych zleceń.
Następnie goście poznali zasady działania systemu MRP z zamkniętą pętla, przekazującego informacje zwrotne na wyższy poziom i umożliwiającego planowanie produkcji. Kolejną ewolucję stanowił MRP II, posiadający zintegrowane funkcje planowania finansowego, marketingu i sprzedaży, rozwoju nowych produktów, zakupów oraz produkcji,
Prowadzący sporo czasu poświęcił BOM-om, których poprawne zdefiniowanie sprawia wiele problemów. Zaprezentowany został przykład planowania zadania produkcyjnego, po którym podsumowano działanie MRP. Końcowa część wystąpienie poświęcona była określeniu poziomu zapasów, jednemu z głównych wejść do procesu MRP, oraz długości cyklu produkcji,
Dystrybucja na nowo
Reprezentacji firm planujących rozwój eksportu swoich produktów, podczas wystąpienia Wojciecha Ciosa z firmy Dachser dowiedzieli się, w jaki sposób wykorzystać współpracę z dużym operatorem logistycznym dla poprawy swojej konkurencyjności.
Prelegent na początku prezentacji podkreślił pozycję swojej firmy, lidera transportu drobnicowego, która w 2014 roku przewiozła ponad 35 mln ton towarów i ponad 73 miliony przesyłek. Zwrócił tez uwagę na to, że w latach 2003-2013 poziom polskiego eksportu wzrósł trzykrotnie. W dalszym jego rozwoju może pomóc wykorzystanie innowacyjnego modelu dystrybucji.
W modelu tradycyjnym producenci posiadają na zagranicznych rynkach swoich dystrybutorów. Jest to rozwiązanie dobre przy wejściu na nowe rynki, ale jego wadami są znaczne uzależnienie poziomu sprzedaży od działań dystrybutora a także brak bazy odbiorców finalnych. Rozwiązania dopasowane do potrzeb pozwalają na uniezależnienie się od dystrybutorów, zwiększenie marży i szybkości dostaw. Rosną za to koszty dystrybucji, należy utrzymywać wysokie zapasy, często negocjować stawki z firmami transportowymi i liczyć się ze słabym ubezpieczeniem.
Prelegent przedstawił nowy model dystrybucji, oferowany dzięki zintegrowanej europejskiej sieci drobnicowej Dachser. Goście mogli tez poznać zasady, jakimi należy się kierować przy wyborze operatora logistycznego.
Słoń kontra kameleon
Jolanta Udzicka reprezentowała firmę Streamsoft, dostawcę rozwiązań informatycznych dla firm produkcyjnych, ale podczas Areny Produkcji nie mówiła o IT. Zamiast tego postanowiła się skupić na porównaniu dwóch podejść do zarządzania, spotkanych podczas wielu lat współpracy z fabrykami w Polsce.
Prelegentka poprosiła na początku gości o odpowiedź na pytanie, po co przybyli na Arenę Produkcji. Możliwości było sporo, ale prowadząca wystąpienie miała nadzieję, że większość zgromadzonych wybrała tę najlepszą – bo chciałby tego mój klient. Każda firma musi bowiem zaspokajać potrzeby swoich klientów, nawet jeśli wiadomo o nich tylko tyle, że są zmienne.
Goście mogli się zastanowić nad tym, co mogą powiedzieć o swoich klientach. Dominującą kwestią jest zmienność ich zachowań. W tego typu sytuacji niezbędne jest prowadzenie procesu zarządzania tak, aby firma była jak najbardziej elastyczna i mogła reagować na zmiany sytuacji.
Słoń stanowi symbol niezmienności, ociężałości myślenia, reakcji lub podejmowania się zmian, ale pozornych, np. wdrażanie koncepcji i narzędzi nie wiadomo po co, czasem niepotrzebnych. Kameleon symbolizuje z kolei widoczne zmiany w działaniu, postawie, myśleniu, przyjmowanie tego co jest nam naprawdę potrzebne. Z pewnością wygodnie jest być słoniem, a rola kameleona jest bardzo trudna. Jednak tylko ona pozwala na adaptację produkcji do zmian, możliwą poprzez zmianę mentalności i podejścia, świadome wdrażanie metod organizacji i zarządzania oraz świadome wdrożenie technologii informatycznych.
Zaczynać i kończyć na standardach
Ronald Galusik z Bridgestone Poznań w swoim multimedialnym wystąpieniu mówił o działaniu programu Kaizen w fabryce, produkującej opony dla samochodów klasy premium. Poznańskie usprawnienia, inspirowane japońską filozofią zarządzania, dały znakomity efekt i zaowocowały sukcesem w prowadzonym przez koncern globalnym konkursie Kaizen.
Poznańska fabryka Bridgestone działa od 1998, zatrudnia ok. 1700 osób i zajmuje powierzchnię 26,4 ha. Zakład ma płaską strukturę organizacyjną, pozwalającą każdemu operatorowi na bezpośredni kontakt z najwyższymi przełożonymi. Sprzyja to rozwojowi programu Kaizen. Za jego koordynację odpowiada dział Inżynierii Przemysłowej. Usprawnienia może zgłaszać każdy pracownik, często są one efektem współpracy kilku osób z różnych poziomów organizacji. Zespołowe zgłoszenia są dodatkowo nagradzane.
Pomysły zbierane są standardowych arkuszach, poszczególne pozycje ułatwiają ocenę pomysłu przez komisję. Komisja przyznaje punkty, które są następnie przeliczane na premie finansowe. Dodatkowo, podczas spotkań z załogą, pracownikom prezentowane są zrealizowane Kaizeny, zaś publiczność wybiera swój ulubiony pomysł, nagradzany upominkami rzeczowymi. Premie przyznawane są tylko za zrealizowane Kaizeny, lecz zdarza się, że pomysły trafiają do archiwum i powraca się do nich po pewnym czasie, gdy spadną koszty wdrożenia lub znikną bariery technologiczne.
Wybierane są Kaizen Miesiąca i Kaizeny Roku, lecz rok temu pomysły zrealizowane w Poznaniu zyskały szczególne wyróżnienie. Cała ich seria wprowadziła lub doprowadziła do rewizji 14 standardów, dzięki czemu o 47% obniżono odpady opon surowych. Kaizen ten został zgłoszony do konkursu prowadzonego przez centralę firmy, wygrał europejski, a następnie globalny finał w Japonii!
Jak widać, także w Polsce można z powodzeniem realizować tę filozofię. Prowadzący prelekcję podkreślił jednak, że Kaizen należy promować, a nie narzucać.
Lean jest sexi
Dzięki Rafałowi Palonkowi z Kaizen Institute Poland, pozostaliśmy w tematyce metod zarządzania produkcją. Pan Rafał opowiadał o metodologii Gemba Kannri, także opierającej się na standaryzacji zarządzania. Prelegent na początku zwrócił uwagę na ogromną popularność jaką zyskały sobie pomysły na zarządzanie rodem z Japonii. – Wszyscy chcą być Lean, bo to jest sexi – oświadczył. Dodał jednak, że rzadko te działania są efektywne. W fabrykach Toyoty, stanowiących wzorzec Lean, nie widać aż tak dużego zaangażowania n.p. w czystość na hali, a pomimo tego ich procesy są skuteczniejsze.
Goście poznali genezę słowa Kaizen i postawę tej metody – ciągłe doskonalenie każdego dnia, przez każdego i wszędzie. Wielka kariera sprawiła, że Kaizen obecny jest już nie tylko na produkcji – obejmuje też działania usługowe, administracyjne i logistyczne. Do ciągłego doskonalenia może motywować teoretycznie negatywny czynnik, jakim jest lenistwo. Ważne jednak, aby być leniwym pozytywnie, czyli ułatwiać sobie życie. Oczywiście doskonalić należy się też po prostu dlatego, aby być konkurencyjnym i przetrwać na rynku.
Prowadzący przestawił następnie pojęcie Hoshin Kanri i działanie firmy zorientowanej na cele. W tego typu organizacji wszyscy powinni znać i rozumieć cele firmy oraz swój wpływ ich realizację czyli na sukces organizacji. Nieznajomość celów sprawia bowiem, ze pracownicy zaczynają zadawać pytania – a każde pytane to marnotrawstwo. Stopień realizacji celów powinien być również nieustannie monitorowany. Wdrożenie Hoshin Kanri wiąże się z kaskadyzacją celów. Dzięki temu łatwiej będzie zaangażować wszystkich pracowników oraz stworzyć kulturę przywództwa i odpowiedzialności.
Gemba oznacza z kolei obecność kadry kierowniczej na hali produkcyjnej – czyli tam, gdzie tworzona jest wartość. Pracownicy dzięki nieustannemu kontaktowi z przełożonymi są w stanie lepiej zaangażować się w proces ciągłego doskonalenia i mają świadomość wymagań klienta. Zmiana kultury organizacyjnej zachodzi wówczas znacznie łatwiej, rośnie wydajność i maleją koszty.
Wprowadzenie Gemba Kanri w zakładzie oznacza, że wdrażane standardy muszą być zaakceptowane przez wszystkich – przede wszystkim kierownictwo. Nacisk stawiany jest na bazowanie na danych, błyskawiczną reakcję na problemy, wykorzystywanie ich do rozwoju organizacji a także eliminację tendencji do poszukiwania winnych. Prelegent przedstawił wiele przykładów standaryzacji i na koniec zachęcił wszystkich, aby byli pozytywnie leniwi.
Kolacja z lwem
Część wykładową zakończyło bez wątpienia najciekawsze wystąpienie. Zbigniew Sobkiewicz z MPM Productivity Management przedstawił zgromadzonym w przystępny sposób trudny problem, jaki stanowi wdrożenie w firmie procesu Sales & Operational Planning.
Zrozumienie zagadnienia ułatwiło opisanie go na przykładzie działań firmy z branży farmaceutycznej. Zapotrzebowanie na jej produkt – lek na grypę i przeziębienie – było mocno uzależnione od sezonu. Fabryka posiadała zbyt małą elastyczność, aby dopasować się do zmiennego zapotrzebowania i w niższym sezonie produkowano na zapas zgodnie z założonym planem. Jednak prelegent zaznaczył, iż w każdym planie pewna jest tylko jedna rzecz – że jest on obdarzony błędem.
Dodatkowa zmiana sytuacji rynkowej wymusiła na firmie rewizję planów. Z nowej prognozy wynikało, że pod koniec roku, przy największym zapotrzebowaniu, zabranie zapasów. Skorygowany plan produkcji zakładał zwiększenie produkcji aby wyrównać ten niedobór, lecz kosztem przekroczenia teoretycznie maksymalnej wydajności zakładu w okresie wiosennym. Okazało się, da się pracować z wydajnością powyżej maksimum, ale na krótką metę – pracownicy po kilku miesiącach zaczęli odchodzić z firmy i kłopoty tylko się pogłębiły.
Stosowanie Sales & Operational Planning stanowi sposób na wyjście w tego impasu. W ramach tego działania identyfikowane są procesy, określane problemy i proponowane rozwiązania. Kluczową sprawą jest wybór priorytetów oraz świadomość tego, że proces będzie długotrwały oraz wiąże się z wystąpieniem braku zapasów na pewnym etapie, lecz na dłuższą metę uzdrowi sytuację.
Prelegent podkreślił, że problemem nie jest plan, ale konsekwentne jego wdrożenie. Decyzje w ramach tego procesu mają zapadać na najwyższym szczeblu i muszą obejmować długi horyzont działań. Sama metodologia jest prosta – wystarczy kilka spotkań, jako narzędzia posłuży arkusz kalkulacyjny, a czasem nawet wystarczyć kartka papieru. Proces jest jednak trudny kulturowo, wymaga wspólnego języka różnych działów, wspólnego celu, zaufania i proaktywności. Niezbędny jest też lider, który zainicjuje wdrożenie, wychowa ludzi i doprowadzi do sytuacji, w której będzie można się już bez niego obejść.
Aktywni uczestnicy
Na zakończenie dnia organizatorzy przygotowali sesję crowdsourcingową. Dzięki spotkaniom z ekspertami związanymi z tematyką poruszaną podczas konferencji, była okazja do poszerzenia swojej wiedzy, podjęcia prób znalezienia rozwiązań problemów pojawiających się w codziennej pracy, jak też poznania dostępnych rozwiązań, które mogą zoptymalizować działania fabryki.
Dyskusja została jednak nawiązana już w trakcie wykładów – uczestnicy konferencji okazali się bardzo aktywni, włączali się w prelekcje a także przedstawiali swoje opinie. Również podczas przerw można było usłyszeć wiele rozmów między menedżerami z różnych firm, szybko znajdujących wspólny język. Niezwykle nas cieszył taki przebieg spotkania i dziękujemy Państwu za zaangażowanie i obecność.
Podziękowania za pomoc w organizacji konferencji kierujemy też do naszych partnerów: firm Dachser, Streamsoft, IPOSystem, Emtor, Yale, IBCS Poland, Honeywell, Amsort, Kaizen Institute, Profes, Dachser, Bridgestone Poznań, MPM Productivity Management, PIAP, Centrum Energetyki i Techniki oraz Mind Supporters.
Galeria zdjęć do artykułu
Pliki do pobrania
zarejestruj się by uzyskać bezpłatny dostęp do materiałów z konferencji. W ten sposób dbamy o polepszanie jakości naszych usług i dostarczanych do Ciebie materiałów. Rejestracja oznacza akceptację aktualnej polityki prywatności.