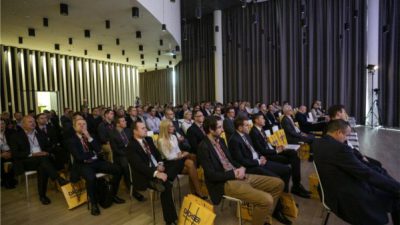
MANUFACTURING SUMMIT 2014
To był dzień wielu zaskoczeń. Konferencja Manufacturing Summit 2014, która odbyła się 6 listopada 2014 roku w hotelu Sound Garden w Warszawie, zaskoczyła organizatorów dużą ilością gości, gości ciekawą tematyką wystąpień, a wszystkich zgromadzonych klimatem sprzyjającym nawiązywaniu nowych kontaktów, poszerzaniu wiedzy i poszukiwaniu sposobów na poprawę efektywności firm produkcyjnych.
Wydarzenie, które było skierowane do dyrektorów i menedżerów firm produkcyjnych, specjalistów do spraw ciągłego doskonalenia, specjalistów utrzymania ruchu oraz menedżerów logistyki, zostało zorganizowane przez Wydawnictwo Eurologistics i czasopismo Logistyka Produkcji. Wydawca, Adam Błuś, powitał zebranych gości, przedstawiając koncepcję wydarzenia i zapowiadając szereg atrakcji zaplanowanych na nadchodzące godziny.
Pracownicy robią sobie dobrze
Konferencję dobrze jest rozpocząć od wyjątkowo trudnego tematu. Dlatego też jako pierwsza wkroczyła na scenę Weronika Piela-Janków, kierownik ds. Lean i Obsługi Serwisowej Obiektu w firmie Flextronics International Poland, która podczas obszernego wystąpienia chciała przekonać zgromadzinych, iż dzięki odpowiedniej motywacji pracownicy zakładów produkcyjnych mogą naprawdę aktywnie zaangażować się w proces rozwoju miejsca pracy.
Flextronics International Poland działa w Tczewie od 2000 roku i jest przedstawicielstwem koncernu, który na całym świecie ma ponad 200 tys. pracowników. Flextronics zajmuje się produkcją kontraktową m.in. dla czołowych firm z branży elektronicznej, zaś klienci zakładu w Tczewie mogą skorzystać z całego pakietu rozwiązań „door to door” – prócz produkcji w ofercie jest także projektowanie, dystrybucja i serwis.
W Tczewie działają dwa budynki, pierwszy w nich to hala mechaniczna, gdzie dokonywana jest m.in. obróbka plastyczna metalu i zadania montażowe, zaś w hali elektronicznej realizowane są m.in. zadania związane z produkcją elektroniki. Weronika Piela-Janków kieruje działem Lean, który realizuje szereg działań, mających na celu ciągłe doskonalenie i usprawnianie realizowanych procesów.
Zainteresowanie gości konferencji wzbudziła zwłaszcza prezentacja programu sugestii pracowniczych. Program motywacyjny 3 P (Pomysł, Punkty, Pieniądze) został zainicjowany w 2008 roku na hali mechanicznej, rok później został skopiowany na halę elektroniczną. Firma aktywnie zachęca pracowników do składania swoich pomysłów usprawnień i nagradza za nie punktami, zamienianymi następnie na nagrody finansowe. Prelegentka podkreśliła przy okazji, iż nie zgadza się ze spotykaną często opinią, iż pieniądze na dłuższą metę nie są skutecznym źródłem motywacji. Podczas prelekcji wyświetlane było kilka filmów, na których sami pracownicy potwierdzali, że gratyfikacje finansowe są dla nich ważne, choć liczy się również to, iż zgłaszając pomysły usprawnień ułatwiają sobie pracę.
Flextronics zachęca nie tylko do zgłaszania gotowych pomysłów, ale również wskazywania problemów na stanowisku pracy, których rozwiązanie poprawi produktywność. Prelegentka zwróciła uwagę, iż w przypadku pomysłów, które nie mogą być zrealizowane, bardzo ważne jest wyjaśnienie pracownikowi powodów decyzji odmownej. Informacja zwrotna pozwoli na utrzymanie zaangażowania pracownika i jego chęci samorozwoju.
Firma przyznaje nagrody kwartalne i roczne, zaś ich wręczenie następuje w uroczystej atmosferze. W ciągu sześciu lat działania programu liczba zgłoszonych pomysłów wzrosła ponad 10-krotnie, co potwierdza popularność programu wśród prelegentów. Pani Weronika w dalszej części prelekcji mówiła o pozostałych aktywnościach Lean, jak konkursy dla grup z różnych obszarów, wewnętrzne warsztaty Kaizen i zewnętrzne warsztaty Kaizen prowadzone przez sensei z Japonii. Flextronics mocno angażuje się w działania Lean 2.0 i zaprasza inne firmy do wizyt w swoim zakładzie, jak też obserwuje najlepsze praktyki u innych.
Logistyka a kolarstwo
Po bardzo intensywnym wystąpienia przyszła pora na nieco luźniejszy temat. Beata Troczyńska i Elwira Gałczyńska z Geodis Polska przedstawiły film, prezentujący kulisy partnerstwa operatora logistycznego z największą polską imprezą sportową – Tour de Pologne. Nie zabrało okazji do zaprezentowania działalności firmy.
Geodis posiada w Polsce 5 lokalizacji 28 tys. m.kw. powierzchni magazynowej. W ofercie znajdują się transport drogowy, transport morski, control tower, dystrybucja produktów farmaceutycznych, logistyka kontraktowa i projekty ponadgabarytowe. Duża renoma pozwoliła firmie zyskać zaufanie organizatorów Tour de Pologne.
Doświadczenie z codziennej realizacji zadań dla klientów z pewnością pomogło podczas obsługi wyścigu kolarskiego, rozgrywanego na terenie całego kraju. Geodis przewoził sprzęt używany przez organizatorów podczas każdego z etapów, zaś możliwość towarzyszenia najlepszych kolarzom stanowiła duże przeżycie.
Czy produkcja w Polsce ma szansę się utrzymać?
Takie pytanie zadał zgromadzonym Krzysztof Wilkosz z firmy SKK SA. Pan Krzysztof od ponad 15 lat zajmuję się tematyką rozwiązań usprawniających procesy w obszarze produkcji i starał się przekonać, iż ucieczka fabryk na Daleki Wschód może zostać powstrzymana dzięki automatyzacji zakładów.
Takie aspekty, jak jakość, terminowość, optymalne koszty i wydajność są istotne dla producenta niezależnie od lokalizacji. – W moim przekonaniu każda firma, która idzie tylko drogą najniższych kosztów, nie dojdzie za daleko – podkreślił prelegent. Należy też patrzeć na otoczenie i pamiętać, że ten aspekt ciągle będzie się zmieniać, a rynek nieustannie będzie oceniać producenta.
SKK skupia się na czterech obszarach w dziedzinie automatyzacji: znakowaniu automatycznym i identyfikacji, oprogramowaniu do raportowania realizacji produkcji, oprogramowaniu do zbierania danych z maszyn – OEE, oraz oprogramowaniu dla logistyki materiałów i wyrobów na produkcji. – Przy automatyzacji nie chodzi nam o zmniejszanie zatrudnienia, ale o jak najlepsze wykorzystanie potencjału ludzi – zwrócił uwagę pan Krzysztof.
Prelegent przedstawił studia przypadków dotyczące wdrożeń znakowania automatycznego i raportowania produkcji. Zwrócił też uwagę na często pomijane aspekty, jak np. materiały naklejek, które muszą być odpowiednio trwałe, ale też w niektórych aplikacjach łatwe do usunięcia.
Operacja na dużą skalę
Marek Prószyński z formy GEFCO zaprezentował studium przypadku, przedstawiające w jaki sposób doświadczony operator logistyczny może realizować wymagania firmy produkcyjnej o globalnym zasięgu. Klient firmy posiadał kilkanaście zakładów produkcyjnych w Europie i należało zintegrować je z siecią logistyczną GEFCO oraz zoptymalizować proces. Projekt wykonywany był stopniowo, obsługa obejmowała kolejne zakłady.
Komponenty odbierane są od ponad 200 międzynarodowych dostawców, dostawy realizowane są do 19 fabryk w 8 krajach – pięć z nich znajduje się w Unii Europejskiej, pozostałe w Turcji, Maroko i Bostwanie. Wybrane wymagania klienta obejmowały konsolidację odbiorów od dostawców wspólnych dla kilku fabryk, optymalizację globalnych kosztów logistyki i dostawy Just-in-Time.
W centrum działań znajduje są magazyn crossdockowy, wykonywane są w nim także dodatkowe operacje zlecone przez klienta. Transport realizowany jest głównie drogą lądową. W ramach rozwiązania zaoferowano dedykowany „Flow Pilot” czyli program pilotażowy w centrum przeładunkowym GEFCO, analizę danych od dostawców w oparciu o szereg parametrów, realizację operacyjnego planu transportowego, konsolidację dostaw w centrum przeładunkowym, śledzenie dostaw produktów i ciągłe usprawnianie procesu i redukcję kosztów. Skonsolidowanie zadań logistycznych, dotychczas realizowanych w poszczególnych krajach przez lokalnych operatorów, zapewniło obniżkę kosztów na poziomie dwucyfrowym.
Inteligentny system planistyczny
Innowacyjną ideę, jakim jest inteligentna fabryka, zaprezentował Krzysztof Fiegler, reprezentant firmy UIBS Teamwork Sp. z o.o. Wizja z przyszłości zaczyna stawać się rzeczywistością, także w Polsce, czego przykładem był innowacyjny system zarządzania produkcją w Andrychowskiej Fabryce Maszyn Defum SA.
Po raz kolejny goście konferencji postawieni zostali przed ważkim pytaniem – czy planiści są potrzebni? Prelegent zwrócił uwagę, że pomimo wsparcia ze strony różnego typu oprogramowania, nadal to planiści podejmują ostateczne decyzje w sprawie planu produkcyjnego. – Czasem są to decyzje spokojne, ale w przypadku sytuacji nagłych, stają się one nieraz nerwowe. Nie zawsze podejmowane są wówczas najlepsze decyzje – zauważył prowadzący.
Innowacyjny system Iposystem, wdrożony w 2012 roku w Andrychowskiej Fabryce Maszyn pozwolił na automatyczną aktualizację harmonogramu po każdym zdarzeniu na hali produkcyjnej i w obszarze wokół produkcyjnym. Powoduje to, iż system inteligentnie i samodzielnie steruje procesami oraz zasobami.
Zadania produkcyjne są przekazywane za pomocą terminali prac, który wydaje zlecenia dla pracowników. System jest tak skonstruowany, iż pracownicy nie mogą wykonywać innych czynności niż te, wynikające z opracowanego przez algorytm planu. Po wdrożeniu planiści skupiają się na nadzorowaniu systemu a nie podejmowaniu decyzji, zaś przeliczeniowy koszt roboczogodziny pracowników produkcji Andrychowskiej Fabryki Maszyn do końca bieżącego roku będzie mniejszy o 15-20%.
Simple is powerful
Drugi blok prelekcji rozpoczął specjalny gość konferencji – Amir Schragenheim, współzałożyciel Inherent Simplicity. Specjalista w dziedzinie Teorii Ograniczeń, współpracujący z Eli Goldrattem, zaprezentował sposób na usprawnienie łańcucha dostaw dzięki rozwiązaniu Pull dla dystrybucji.
Prelegent rozpoczął swoje wystąpienie od zaprezentowania typowego łańcucha dostaw i nieuniknionych problemów. Jego wydajność zawsze ograniczona jest przez takie symptomy jak brak zapasów, doprowadzający do spadku sprzedaży i obniżenia marży, lub tez nadmierne zapasy, generujące koszty i obniżające elastyczność reakcji na sytuację rynkową. Pan Amir zwrócił uwagę, że zgodnie z prawem Muprhy’ego, te problemy zawsze się nawarstwiają i pojawiają w najmniej odpowiednim momencie. Zresztą, sformułowanie prawo Muprhy’ego padło w trakcie prelekcji jeszcze niejednokrotnie.
Jak jednak ustalić optymalny stan zapasów? Powinny być one zaplanowane biorąc pod uwagę oczekiwaną sprzedaż, lecz prelegent zauważył, że na ścisłe określenie tego parametru pozwoli tylko szklana kula, raczej rzadko wykorzystywana przez menedżerów. Typowe problemy dotyczące prognoz to błędy narastające wraz z wydłużeniem okresu prognozy, otrzymywanie nieprzydatnych w praktyce danych jak średnia czy odchylenie standardowe czy nieprzewidywane wydarzenia. Braki magazynowe czy nadmierne zapasy nie zostaną w ten sposób wyeliminowane.
Receptą na problemy jest model uzupełniania, oparty na zasadach Teorii Ograniczeń. Prelegent przestawi jego podstawy, reguły kierujące ustalaniem bufora i określeniem momentu uzupełniania. Bufor to doskonałe narzędzie, pozwalające na wyeliminowanie problemów dotyczących dystrybucji, a do tego bardzo proste, w myśl zasady Simple is powerful. Podział bufora na strefy i ich kolorystyczne oznaczenie pozwala na utrzymywanie go na optymalnym poziomie. Prelegent podkreślił, że choć zazwyczaj strefa zielona oznacza, iż wszystko jest w porządku, wcale nie należy dążyć do ciągłego utrzymywania zapasów na takim poziomie – optymalna rozwiązania to balansowanie na mniej bezpiecznym pozomie zapasów.
Wyjść poza ograniczenia
Dariusz Kacperzyk, wiceprezes firmy EQ System Sp. z o.o., zwrócił uwagę na to, jak duże są ograniczenia systemu ERP w zakładzie produkcyjnym, realizującym szereg skomplikowanych procesów – Każdemu proponuję, aby przeszedł się po dziale produkcji i zobaczył, jak tak naprawdę jest on skomplikowana – stwierdził prelegent na początku wystąpienia.
Zaprezentowane zostały możliwości rozwiązań, stosowanych przez EQ System i ich przewaga nad prostszymi aplikacjami – Systemy ERP zaczęły być obudowywane innymi. Ja reprezentuję pogląd, aby dostarczać klientom takie rozwiązania, które realizują ich potrzeby dotyczące poszczególnych funkcjonalności – oświadczył prelegent.
Studia przypadków, oparte na wdrożeniach przeprowadzonych w firmach Sopp Industrie, Convert Paper i Strauss Cafe Poland pokazały jakie konkretne korzyści można osiągnąć, stosując zaawansowane oprogramowanie do harmonogramowania produkcji. Przestawione zostały też zasady przygotowywania harmonogramu procesów produkcyjnych i błędy, których należy unikać.
Ciągłość dostaw dla produkcji
Grzegorz Łukaszek, reprezentant firmy Dachser, zajął się kwestią zapewnienia ciągłości dostaw dla produkcji, z wykorzystaniem routing order. Operator logistyczny otrzymał zapytanie od klienta, poszukujące możliwości optymalizacji dostaw do fabryki pod Opolem.
Fabryka posiada 96 dostawców na terenie Europy, miesięczna liczba zleceń sięgała 600 a odbiory następują z 15 krajów na terenie Europy. Klient chciał scedować na operatora logistycznego wszystkie zadania związane ze zleceniami, był też niezadowolony z terminowości dostaw, liczby uszkodzeń i liczył na redukcję kosztów. Także dostawcy mieli problemy ze współpracy z dotychczasowym operatorem.
Klientowi zaoferowano obsługę poprzez centrum w Sosnowcu. Sieć oddziałów w Europie i koncepcja Eurohubów pozwoliła na realizację codziennych połączeń liniowych. Dachser zagwarantował duże bezpieczeństwo towarów, dzięki ciągłemu szkoleniu pracowników, konsekwentnemu stosowaniu środków zabezpieczenia ładunku, regularnym kontrolom wewnętrznym dotyczącym jakości załadunku oraz zastosowaniu kontenerów wymiennych (swap-body) ze sztywną zabudową i z podwójną podłogą. Kody kreskowe i monitoring dokumentują przebieg działań w całym łańcuchu dostaw, zaś klient ma możliwość śledzenia przesyłki.
Jak skorzystać na ToC
Paweł Schmidt z ToC Strategic Institute podpowiadał, jak skorzystać z rozwiązań Teorii Ograniczeń w dystrybucji. Zalety tej koncepcji przestawił wcześniej Amir Schragenheim: wzrost sprzedaży w punktach konsumpcji zazwyczaj o 10-30%, ograniczenie poziomu zapasów zazwyczaj o 50%, wzrost dostępności (zazwyczaj o połowę mniej braków) i zazwyczaj wielokrotna poprawa rotacji zapasów.
Jak jednak sprawdzić, co to oznacza dla mojej firmy? Z wykorzystaniem danych historycznych można zaprezentować jaki jest potencjał dwóch podstawowych założeń dystrybucji TOC: uzupełnianie zgodnie z realną konsumpcją i dynamiczne zarządzanie buforami. Prelegent przeprowadził trzy symulacje: dla dwóch sieci handlowych i dla producenta.
Porównanie rzeczywistych danych i wyników symulacji wykazało, w jaki sposób rozwiązania ToC pozwala uniknąć zaburzeń związanych z nieprzewidywalnymi sytuacjami, w jednym z przypadków całkowicie wyeliminowany sytuacje, w których pojawiały sie braki. Prelegent zachęcił gości konferencji do przeprowadzania symulacji na podstawie własnych danych.
Kanban w Lincoln Electric Bester
Trzeci blok wykładowy w znacznym stopniu poświęcony był zagadnieniom związanym z Lean Manufacturing. Rozpoczął go Piotr Cichoń, dyrektor logistyki na Polskę z Lincoln Electric Bester, który przedstawił jak udało mu się wykorzystać zasady szczupłej produkcji do uwolnienia zasobów magazynowych.
Bielawska fabryka Lincoln Electric, amerykańskiej firmy produkującej materiały i urządzenia spawalnicze, działa od 1946 roku. Gdy koncern przejął zakład w 2002, problemem była konieczność korzystania z zewnętrznych magazynów wyrobów gotowych. Powierzchnia magazynowa była potrzebna, gdyż w Bielawie znajduje się także centrum dystrybucyjne na Europę.
Piotr Cichoń podjął się tego wyzwania, pomimo iż wprowadzenie zmian w zakładzie działającym od kilkudziesięciu lat było znacznie trudniejsze niż w przypadku nowo projektowanej fabryki. Szansą na znalezienie nowych zasobów magazynowych było uwolnienie miejsca w magazynie materiałów. Surowce miały trafić na halę produkcyjną i być składowane w supermarketach, czyli pomóc w zadaniu miał Lean.
W pierwotnym układzie brakowało jednak miejsca na supermarkety. Niezbędne było dokonanie analizy obszarów produkcyjnych i przeniesienie niektórych maszyn. Tym samym pojawiło się miejsce na duży supermarket, zaś dodatkowe zostały postawione na poszczególnych wydziałach. Uwolnione zostało 900 miejsc paletowych dla wyrobów gotowych, zmniejszone zostało ponadto zatrudnienie w magazynie.
Zamówienia i dostawy realizowane są w systemie Kanban. Wykorzystanie własnych pojemników pozwala na realizowanie systemu także we współpracy z zewnętrznymi dostawcami. Niezwykle proste i skuteczne rozwiązanie, w którym poszczególne supermarkety są oznaczone różnymi kolorami, umiesczanymi także na pojemnikach, ułatwia proces dostaw. Działa również system nadwyżek, w przypadku braku miejsca w supermarkecie nadwyżki trafiają do pływającej lokalizacji a uzupełnianie marketu następuje w systemie Kanban.
System supermarketów skłonił oczywiście do realizacji transportu wewnętrznego metodą milk run. Prelegent pokazał w jaki sposób wybrał optymalną trasę pociągu i za pomocą schematu wskazał, jak udało się uprościć system dostarczania materiału. W podsumowaniu wystąpienia goście mogli się przekonać, jakie realny korzyści przyniosły wdrożenia.
Poszukiwanie marnotrawstwa
Goście zainteresowani wdrożeniem Lean Manufacturing w swoich fabrykach czekali również na wystąpienie Macieja Koca z Arjohuntleigh Polska Sp z o.o. Reprezentant zakładu działającego w podpoznańskich Komornikach mówił bowiem o procesie mapowania strumienia wartości, niezbędnym podczas działań mających na celu wyszczuplenie produkcji.
Należący do Getinge Group Arjohuntleigh produkuje wyroby dla branży medycznej, szczególnie dużą uwagę przykładając do rozwiązań dla pacjentów z ograniczoną mobilnością. W Komornikach powstaje pięć głównych grup – łóżka, materace, garmenty, podnośniki i kozetki. W 2009 roku w zakładzie rozpoczęto wdrażanie Lean Manufacturing, rok później ruszył system Kaizen.
Prelegent przedstawił trzy główne etapy mapowania strumienia wartości – tworzenie mapy stanu obecnego, mapy stanu przyszłego i planu wdrożenia. Pan Maciej zauważył, że w literaturze spotykane są jeszcze pojęcia mapy stanu idealnego, lecz w ramach wykonywanych analiz wraz z zespołem ograniczał się wyłącznie do dwóch wcześniej wspomnianych map.
Goście konferencji zostali przeprowadzeni przez poszczególne kroki tworzenia mapy stanu obecnego, pokazano zasady i mierniki wykorzystywane w procesie. Równie dokładnie omówione zostało tworzenie mapy stanu przyszłego, prelegent wskazał, jakie pytania należy sobie zadać podczas tego działania. Na koniec prelegent zdradził, jakie wyniki dało mapowanie strumienia wartości w jego zakładzie. VSM ułatwia identyfikację marnotrawstwa oraz braku zbalansowania czynności, stanowi podstawę do planowania usprawnień w procesie czy też pozwala skupić się na idealnym lub oczekiwanym kształcie procesu.
Ciężkie życie lidera
„Rozwiązania w zakresie zarządzania produkcją dla firm typowych, normalnie zakręconych, gotowych na każdą zmianę just-in-time, aby spełnić wymagania perfekcyjnych klientów” – oto temat prelekcji która zamykała część wykładową Manufacturing Summit 2014. Jej autor, Janusz Pieklik, nie chciał zdradzić co kryje enigmatyczny tytuł, pozostało zatem jedynie wysłuchać wystąpienia.
Doświadczony konsultant, specjalizujący się we wdrożeniu systemów systemów klasy ERP, zarządzania produkcją, lean manufacturing i lean logistics, natychmiast włączył do prelekcji publiczność, pytając uczestników konferencji jak wygląda u nich doskonalenie procesów produkcyjnych i słusznie przewidując, że wiele rzeczy idzie opornie.
Prelegent wskazał wiele przykładów firm, które z pozycji liderów rynkowych spadły z niebyt. Pokazał też jak daleka potrafi być teoria, zawarta w książkach, od codziennej praktyki polskich firm produkcyjnych. Problemy spotykane w codziennych działaniach wynikają z ograniczeń, nader często leżących poza samą fabryką.
Ale prelegent zwrócił też uwagę na europejskie badania, w których polskie firmy produkcyjne wypadają bardzo dobrze. Wskazane zostały szanse na ich rozwój, ale i zagrożenia. Przede wszystkim, polskie fabryki muszą uciekać od roli podwykonawców, nie gwarantuje ona bowiem dużych zysków ani możliwości rozwoju. Janusz Pieklik namawiał zgromadzonych menedżerów do przejęcia roli liderów, choć prezentując postaci kilku biznesowych wizjonerów przypominał, że wyjście przed szereg będzie początkowo wiązać się z dużym oporem ze strony otoczenia.
Zainteresowani rozwinięciem tematyki prezentowanej podczas prelekcji, syntezą i wyborem najlepszych elementów z kilku nowoczesnych metod zarządzania produkcją zostali zaproszeni na szkolenie 3D Zarządzania Produkcję, organizowane przez Logistykę Produkcji i prowadzone przez Janusza Pieklika.
Czas na podziękowania
Sesje wykładowe dobiegły końca, ale nie był to koniec dnia. Na scenę powrócili organizatorzy i rozlosowali upominki, ufundowane przez firmy DSR, BPSC i Geobike. Goście konferencji zainteresowani pogłębieniem wiedzy na temat wykorzystania Teorii Ograniczeń w dystrybucji pozostali na sali, aby wziąć udział w warsztacie, prowadzonym przez Amira Schragenheima i Pawła Schmidta. Jednocześnie rozpoczęły się sesje crowdsourcingowe i networkingowe. Przy stolikach tematycznych dostępni byli eksperci, zajmujący się tematyką nowoczesnych metod zarządzania produkcją, a także partnerzy konferencji, oferujący rozwiązania poprawiające efektywność firm produkcyjnych.
Manufacturing Summit 2014 przeszedł do historii. Pozostaną po nim miłe wspomnienia, szereg nowych znajomości i duża dawka wiedzy. Organizatorzy konferencji serdecznie dziękują za pomoc w organizacji partnerom imprezy: Dachser, Quantum Software, Gefco Polska, SKK, BPSC, Panattoni Europe, Geodis Polska, EQ System, P3 Logistic Park, IPO System, DSR, Geobike, Arjohuntleigh, Kaizen Institute, Profes, Flextronics, Lincoln Electric Bester, MPM Productivity Management, 4 Results.
Pełna foto-relacja dostępna jest na stronie Logistyka Produkcji
Galeria zdjęć do artykułu
Pliki do pobrania
zarejestruj się by uzyskać bezpłatny dostęp do materiałów z konferencji. W ten sposób dbamy o polepszanie jakości naszych usług i dostarczanych do Ciebie materiałów. Rejestracja oznacza akceptację aktualnej polityki prywatności.